ANSWERS:
It’s Doable
Noise and environmental issues provide an opportunity for a positive, practical, and economical solution in many installations where hydraulic drives are used.
Hydraulic drives have become a very reliable and economical drive technology, but their extraordinary high power-to-weight ratio (power density) brings with it high noise levels. Environmental concerns from extensive use of petroleum oil as a medium also need to be addressed.
Noise from hydraulic drives comes from three sources: airborne, fluid-born and structure-born. Airborne noise can be attributed to vibrations in the drive reflected and amplified through mechanical structures, and from fluid-born noise transferring its energy or vibration into the adjacent air mass.
Fluid-borne noise is caused by the pumps used. Pulsations from pumps (gear, vane and piston type) transfer energy by way of vibrations and result in fluid-born noise that will cause mechanical elements to be excited.
In most cases the most cost-effective solution is to concentrate on the pump. Manufacturers of hydraulic pumps typically publish noise data (sound pressure dBA) for their pumps at a known drive speed, flow, and pressure. This sound data is typically collected and recorded in an anechoic chamber or room conforming to a DIN Norm 45 635, part 26.
Data from these tests in a controlled environment only measure the sound pressure from airborne noise emitted from the pump. While it is important to begin pump selection with relative noise data, differences of ±5 dBA can be seen based on the manufacturers’ tolerance, control settings, and the mounting of the pump. It would be equally important to note that one should gather similar data from the motor manufacturer.
OEMs can address noise reduction:
Inlet to pump:
-
Increase inlet diameter to pumps to a maximum oil velocity ≤ 0.5-1.0 m/s
-
Design inlet lines straight and short, avoid elbows, use full flow inlet valves
-
Terminate pump inlet line in oil tank ≥ 4 inlet line diameters below air/oil
Surface:
-
De-couple pump inlet by submersing the pump in the tank. This could be a fluid immersed motor/pump, but most often just is a submersible pump. This solution reduces air-born noise as well.
-
Use soft connections on pump inlet, hose, or expansion joint
-
Provide adequate tank volume and design (baffles) to dissipate entrained air in
The Oil
-
Avoid termination of any return lines near pump inlets
-
Provide for oil inlet head pressure to pump manufacturers’ recommendations
Pump Outlet, Service Lines, Return Lines:
-
Use hose on pump outlet, selected for fluid line velocities ≤ 4 m/s
-
Don’t use sharp bends on outlet lines to avoid reduction and distortion of wall
Cross section on pipe/tube
-
Secure outlet lines with clamps to ground noise to structure
-
Consider fluid line silencers (mufflers)
-
Limit return line oil velocities to ≤ 2 m/s
Structure-born noise reduction
-
Add flexible motor/ pump shock mounts with three degrees of freedom in shear rather than compression
-
Add a damping flange to replace the typical rigid bell housing or pump L-bracket with a kinematically matched pump motor coupling
-
Design and arrange fixing points of support where the reservoir and frame is most rigid and of substantial mass
-
Add additional high mass elements or gusset support areas
-
Remove/design to remove other mechanical sound bridges
These can include pressure, suction, and return lines that are rigid. Sometimes experimenting with adding a small section of hose can decrease noise transmission dramatically.
Environmental concerns prompted manufacturers to develop fluids that are both environmentally friendly and suitable for many modern hydraulic drives. Products categorized as HEES are prepared from rapeseed and soybean base chemicals. These are environmentally friendly and have measured success in hydraulic drives. Synthetic anti-wear hydraulic fluids, type HETG with better than petroleum properties, fire-resistance, and that are biodegradable have been employed with great success in many applications. —Andrew Binversie, Manager, Presses, Series, and Light, Bosch Rexroth.
Hydraulics Getting Better All the Time
Hydraulic power continually improves through increased power density; enhanced quality with solutions to noise and leakage issues; improved control; reduced emissions and environmental impact; increased electronics and computer control for operators; and application self-diagnostics for easier repair and preventative maintenance.
Noise is not the issue it once was. New piston-pump technology has reduced fluid-borne sound with a pre-compression or ripple chamber built into the pump’s rear cover. This ripple chamber pre-charges resident oil in the piston chamber and transitioning piston in tandem with overall outlet system pressure, thus decreasing output flow loss and rippling.
Additional pump sound sources such as cavitation and aeration can be controlled with in-line pulsation dampers and proper system design. Mechanically isolating system pressure components downstream from the pump can decrease noise greatly. Plant engineers also have the option of using enclosures tailored to the application.
Excessive strain on hydraulic lines because of a design that fails to allow for expansion and contraction, as well as improper clamping and spacing, might lead to vibration that causes noise and leakage. It is critical to allow for movement under load.
Using quality fittings and ensuring proper installation are the best ways to reduce leakage, potential noise, and future maintenance activities. Prying a poorly bent tube in place strains the joint and makes it prone to leakage. Also, a design that minimizes elbows and tees lowers leakage.
As system pressures continue to increase, component providers have improved design with straight thread ports, O-ring face seals, and elastomeric sealing to significantly reduce and often eliminate leakage in hydraulic systems.
Filtration systems and components present another potential source of hydraulic system leaks. A filter maintenance schedule should be set up and followed diligently.
Well-designed hydraulic systems provide high power and precise control; absorb pump, motor, valve and other system noise; cut hydraulic pulsation/shock; and reduce system component wear and tube/pipe connection leakage. The end result of an integrated system approach adds up to a much quieter and cleaner work environment. —Jim Hoenle, hydraulic system engineer, Parker Hannifin
The Controller Can Help
Two traditional environmental drawbacks to hydraulic power are noise and the potential for fluid leakage. Older hydraulic controls, using two-position open/closed (sometimes called "bang-bang") valves sometimes exhibit hydraulic shock when the valves are opened or closed.
The secret to reducing hydraulic shock and noise is to use proportional servo valves and an electro-hydraulic motion controller that smoothes out the motion. Metal-fabrication machine builders should look for closed-loop controllers that can smoothly transition from position control to pressure control. They also should look for controllers with automated, graphical motion-tuning tools to ensure the motion is as smooth as possible.
A potential environmental benefit to power motion systems that hydraulic power has over electric motors is the opportunity for lower power consumption. The pumps in hydraulic systems need to be sized only for average loads, while electric motors in electromechanical systems need to be sized to handle peak loads.
A key component in the system that enables the smoothing of power requirements is the accumulator. Accumulators, in addition to helping cushion shock in hydraulic systems, store energy for times when peak loads occur. —Bill Savela, PE, motion products manager, Delta Computer Systems
Mitigate Operator Noise Exposure
Most of the interest has come from parties concerned about plant noise to which their workers are subjected. In particular, automotive plants have seen an increase in heath costs related to noise issues and are looking to make their plants more ergonomic for their workers so that ear protection isn’t necessary. Many plant and machine specs are requiring 85 dBA maximum with no enclosures, as the enclosure often isn’t reinstalled after servicing.
Many pump system features have inherent costs involved as well, so before specifying a maximum noise level, a machine manufacturer or plant manager might consider what really is necessary before being shocked by the cost. Rexroth has built units that have operated at full flow and pressure at less than 65 dBA, but this involves extra costs. High efficiency and balanced electric motors, pulsation dampeners, creative design of the tank and supporting structure, high performance axial piston pumps – all are features that can be incorporated to reduce noise. —Dave Wenner, Product Manager, Power Unit and Industrial Manifolds, Bosch Rexroth Industrial Hydraulics
Ensure Good Design Practices
Airborne noise radiates from surfaces. It is important to ensure panels fit tightly to prevent any acoustic leakage. Gaps should be eliminated with proper seals.
Structure-borne hydraulic noise is transmitted into mounting structures and can be minimized with proper selection of vibration isolation devices such as pads and couplings.
Fluid-borne hydraulic noise is transmitted through the fluid to the surfaces of the hoses, tubes, and other components. Attenuation devices can be mounted in-line to reduce the magnitude of fluid-borne noises and properly designed vibration isolation also can be used to help achieve the desired noise reduction. Some new and innovative products also are on the market, such as tuned hose assemblies that can target specific running conditions to minimize noise.
Other good design practices that can help noise issues include avoiding flat panels and covers on components that can act like speaker surfaces to amplify noise. Damping and insulation materials also can provide effective results with proper selection and placement.
A low noise application is a team effort and requires good design, components, and assembly and maintenance practices. If any of these details fail, a low noise system cannot be achieved. —Lynn Soule, Marketing Communications Manager, Eaton Corp.
September’s Problem: |
We Need Custom Cable and Connector Assemblies
We often need custom cable and connector assemblies engineered specifically for our custom machine automation applications. We make these ourselves, but we’re now considering going outside to buy fully assembled cable and connector sets, some standard when we can, but many are truly custom. If we go outside for custom work, how do we find a good source that we can count on? What are the key workmanship and materials considerations?
Send us your comments, suggestions, or solutions for this problem. We’ll include it in the August 2007 issue, and post it on ControlDesign.com. Send visuals if you’d like—a sketch is fine. E-mail us at [email protected]. Please include your company, location and title in the response.
Have a problem you’d like to pose to the readers? Send it along, too.
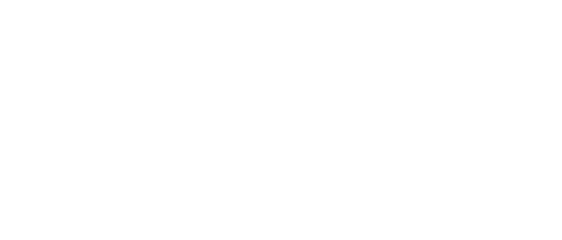
Leaders relevant to this article: