Electronic controls synchronize motion for Hagerty Steel & Aluminum
Synchronizing a process for highest productivity and quality output often requires precise electronic control of multiple motion axes simultaneously. This is difficult to do if each axis responds to control inputs differently, and yet they all have to produce the same relative motion.
Hagerty Steel & Aluminum is a metals service center. From its modest start in the late 1800s, Hagerty, Hunter & Company served flour mills, grain elevators and distilleries in the Peoria, Illinois, area. In 1906, the company's name became Hagerty Brothers, and in 1928 steel was added to the company's offerings. In 2000, the steel division of Hagerty Brothers was acquired by Liebovich Brothers, a subsidiary of Reliance Steel & Aluminum in Los Angeles. Hagerty is ISO 9001:2008 certified.
Figure 1: The Voss leveler is one stage in the Hagerty Steel & Aluminum cut-to-length line. Virtually all of the machine hardware was still useful, and only the motion control system needed to be retrofitted.
Consider a manufacturing line where a sheet of heavy gauge steel up to ½-in thick is being pulled off of a 25-ton coil, is flattened, and then is cut by a hydraulic shear to make sheet stock of a desired length. In the process employed by Hagerty, flattening the steel, which has a memory and initially wants to coil back up, involves passing the steel through a series of rollers—a flattener and a leveler—that bend the material back and forth, followed by pinch rolls that pull the metal tight and push it through the shear. Each stage does a different task and is powered by a different size electric motor. The flattener is driven by a 125-hp dc motor. The leveler is powered by a 300-hp dc motor, and the pinch rolls are powered by a 15-hp dc motor (Figure 1).
“A 15-hp motor can go from zero to full speed a lot quicker than a 300-hp motor,” says Thomas Boon, maintenance manager at Hagerty Steel & Aluminum. “And, unless one takes into account the different drive characteristics, it’s possible to have one of the motors trying to move quickly and one moving sluggishly such that the larger motor will push or pull the smaller one, which can cause it to trip off-line.”
When Hagerty started noticing roll marks on the material in the summer of 2008, it knew it had a problem, explained Boon.
Hagerty’s heavy-gauge, cut-to-length line had been upgraded three times over the past few years, but it wasn’t cutting sheets precisely. “One of our customers requested that we tighten our tolerance, and with the old system it was impossible,” says Boon. To fix the problem, our company, Advanced System Integration & Control (ASIC) of West Chester, Ohio, an integrator with years of experience in machine retrofits, was called in to upgrade the control system.
The upgrade started with the ASIC team getting a thorough understanding of the old machine and the process to be controlled. “There were prints available for the old machine, but they were a combination of drawings from several upgrades that had been done over the years,” explains Mike Hiett, software engineer, ASIC. “We found that the prints didn’t accurately portray the actual wiring that is spread across several control cabinets, so we spent a week tracing the wires and integrating two new dc drives and the motion controller with two existing PLCs and the existing third dc drive.” Then the ASIC team set about to employ a new control strategy for achieving more precise coordination and control of the various motors.
The team needed an electronic motion controller that was capable of performing complex multi-axis synchronization tasks, and, based on experience with an upgrade of another machine at the Hagerty plant, our ASIC engineers knew that an RMC motion controller from Delta Computer Systems could do the job.
The previous application that ASIC did for Hagerty using a Delta motion controller was also a cut-to-length line. It was simpler, in that the entire line is run from a single motor, so there weren’t problems with coordinating the motion of three motors. The motor in that case was a hydraulic motor. The output from the Delta motion controller was fed to a servo control hydraulic valve for controlling the motion. The same encoder that was used on the measuring roll for that line is used on the new Hagerty line to regulate the cut length.
The Delta RMC150 eight-axis motion controller has several built-in multi-axis gearing, camming and synchronization functions that enable multiple slave motion axes to produce tightly controlled motion in relation to that of a master axis.
So Hiett set up the Delta RMC150 multi-axis motion controller to control the three dc motors, each with its own PID control loop, and all of them as slaves to the master motion of a measuring roll. The measuring roll, which precisely tracks the length of the steel sheet being cut, was set up as a “virtual axis,” since the roll is not being driven by a motor, but is instead tracking the sheet length. The machine operator, through a PLC interface, specifies a cut length that translates to a command for the measuring roll to go to a specific position that’s a certain distance away. The motors, which are slaved to this virtual axis, are given velocity commands to drive the steel forward. There’s a rotary encoder on each motor that provides feedback to the motion controller, enabling the RMC to regulate the motor’s rpm and to make sure the motors are running together. At the same time, the RMC also performs open-loop control of a pneumatic brake on the supply roll spindle via a proportional valve in response to operator commands to hold tension on the material as it is fed into the machine (Figure 2).
Figure 2: Diagram shows machine axes controlled by the Delta RMC 150 motion controller. An encoder on each motor, which provides position/velocity feedback directly to the RMC150, is not shown in the diagram.
I’m the controls engineering manager of the ASIC engineering team, which includes four other controls engineers, including Hiett. We also have a service engineer who primarily does field service and startup work. I consider him to be a controls engineer. Our experience and expertise here is somewhat varied, making for a very good team. Our service engineer, Herb Prychodko, and I are very good with ac variable frequency drives, dc drives and coordinated drive systems. Hiett and Frank Gentry are experienced PLC programmers. The two younger engineers, Mike Bencsik and Evan Adamson, along with our owner, Jeff Nichols, are really good with servos and motion control. The vice president of sales/marketing is Chris Schieman, formerly of Rockwell Automation/Reliance Electric, and he’s quite experienced with drive systems applications after working in the steel industry for Reliance a number of years. In most cases, the engineer that designs a system also does the startup on-site where the customer has purchased it. Most users and some OEMs buy startup with the systems.
ASIC also has a full-service panel shop that’s certified to build and label panels to UL508A/cUL and UL698A. We build panels to customer designs, or ASIC can provide a turnkey solution from application engineering, panel design and programming to on-site startup assistance.
Tuning the system
“Tuning one motor drive with no load is not a hard thing to do,” explains ASIC’s Hiett. “But to get the three drives to move in a desired fashion independently of each other in synchronization required a lot of work.” The challenge involves decelerating to a stop so the cut length falls right in the distance window without having to reverse the motors, because moving backward really slows down the operation of the machine. During the initial testing stage, the unrolled material would blow past the setpoint and then reverse direction and pull past the cut length in the other direction in a never-ending oscillation. Part of the problem resulted from the fact that tuning this application presented some unique problems. “Typically, one turns the gains down if there’s an oscillation, but, in this case, the oscillations got worse when we did that,” says Hiett. With help from Delta Computer Systems’ engineers, and plot information obtained using Delta’s tuning tools, Hiett increased the proportional gains, and the system response got a lot better. Additional tuning to reduce rapid changes in velocity got the system to settle down quickly.
“During a phone and Internet collaboration session with the Delta engineer, we used Delta’s plotting tools to display the motion,” explains Hiett. “Then, we’d make adjustments to the control loop gains and then run another piece on the machine while Delta’s engineer watched the results over the Internet via a live connection.” The Delta engineer looked at the three real and one virtual axis and suggested tuning changes on each axis.
We would set a cut length of approximately 10 ft on the screen and initiate an indexing operation. The Delta software tool would then gather the data during the move. The data could then be transferred to Delta over the Internet. The Delta engineer would look at the shape of the curve and recommend a change in the gain value of one of the control loop parameters. Then we would back the material up and run it through again. We didn’t actually make cuts during the tuning because we didn’t want to waste a bunch of steel. I will say that we went from oscillations to an accurate index length very quickly, but it took another few hours to get the move time down to the quickest time possible while holding length accuracy.
Hiett also found the help index in Delta’s RMCTools software to be very useful. “Delta’s help information is the most useful that I’ve found among motion control vendors. For example, Delta’s website has sample programs on how to communicate between the product and just about any PLC currently being used in the industry, including several examples for the PLC that we were using on this project. The examples that I was able to download directly from the website easily saved me a full day of software development.”
Hagerty’s Boon also has been trained to program the Delta controller in the event that software maintenance is required. “I took the Delta RMC technical training in St. Louis, and I found programming the controller to be easy. I’m comfortable to make software changes when needed,” he says.
From a maintenance point of view, the software does make a big difference in the ease of making adjustments. Since we left the site, there have been a couple of instances where Hagerty ran a product with some different feature and additional tuning adjustments were needed to settle things down. That’s the result of tuning everything close to the edge in order to maximize production rates. Hagerty’s Boon has been trained with the software and understands it, so he has made the necessary adjustments each time and solved the problems after a brief phone conversation with ASIC.
With Hagerty’s controller upgrade, the production quality issues have now been resolved. Whereas the old machine was only able to produce steel sheets to within tolerances of approximately ¼-in, and out-of-tolerance material was wasted, the ASIC engineers were ultimately able to tune the machine to achieve the required dimension to within 1/1,000 of an inch, while getting the system to settle down quickly so ASIC’s customer can fire the shear more quickly and increase the production rate.
The changes were discussed and planned two years before the solution was actually implemented on this machine. The delay was primarily due to Hagerty’s upgrading the stacker and material handling system at the output end of the line.
Sponsored Recommendations
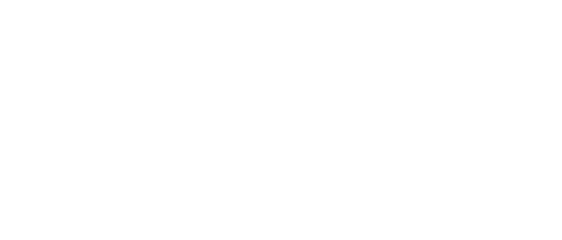
Leaders relevant to this article: