Recognizing their customers’ financial, operational and environmental advantages of energy efficiency, machine builders are responding with smarter, more efficient technologies, as well as advisory services.
“Just about every customer we talk to has some kind of green or sustainability program. They want to reduce energy, air and water usage,” says Mark Ruberg, director of corporate business collaboration at Pro Mach, a provider of automated packaging equipment (Figure 1).
Figure 1: Almost every Pro Mach customer wants to reduce air, power and water usage.
Source: Pro Mach
Air management is a particular concern. “There are a lot of air cylinders and air components on a machine for actuation and motion, and air is very expensive. Even with the most diligent maintenance programs, you still end up with leakage and waste,” remarks Ruberg (Figure 2). “It’s one of the reasons that servo machines are gaining in popularity. When servos need to move, they draw power. When they don’t need to move, they don’t draw power. Inherently it brings more energy savings, and it’s more efficient than compressed air, that’s for sure.”
Figure 2: Even with the most diligent maintenance programs, leakage and waste can be a problem. One big advantage is to build efficiency into the machine in the first place.
Source: Pro Mach
New solutions are on the horizon (Figure 3). “One of our Pro Mach divisions found a way to reduce water usage on a packaging machine’s processing by more than 50%, which reduces energy consumption,” says Ruberg. “It hasn’t been released to the market yet, but we’ve done some testing and it’s going through a patent process now.”
Figure 3: New solutions from Pro Mach are designed to reduce water usage, which reduces energy consumption.
Source: Pro Mach
Kleenline, a division of Pro Mach, is addressing the need to reduce the running cost of equipment that typically operates 24/7. “Many of our customers require high-efficiency motors and servos in their conveyor systems and machinery,” says Francis Maliski, manager of electrical and controls engineering at Kleenline. “We work with our vendors to identify motors and servos that meet the efficiency and sanitation requirements that are specific to the food, beverage and pharmaceutical processing industries.”
At Matrix Packaging Machinery, the spotlight is on air. “Some customers are already using most of the available air compressor capacity and are seeking to add more air-efficient machines whenever possible,” says Mike Krummey, electrical engineering manager at Matrix Packaging Machinery.
“More than 12 years ago, we introduced a new line of machines that uses 80% less air on average when compared to the machines we had been selling. This was accomplished through the use of an electrically operated horizontal sealing system instead of the more common pneumatic-actuated designs,” explains Krummey. “The machines are less costly to operate and the mean time between failures (MTBF) is longer compared to the pneumatic-actuated designs.”
New innovations are in the works. “A very small number of customers have asked for heat zones that will switch to a low heat temperature after long periods of inactivity. This will be an option available in the second half of 2015,” adds Krummey.
JLS Automation, a provider of case packing systems, is also innovating (Figure 4). “Many customers are concerned about the air consumption of vacuum generators, so we developed a highly efficient vacuum generator,” says Craig Hafner, vice president of technology at JLS Automation. “Tool-mounted compressed air vacuum generators use less power than blowers, especially due to their duty cycle of about 50% vs. 100% for a blower. Large blowers are inherently inefficient and have high line losses.”
Figure 4: JLS Automation strives to provide innovative case packing systems that use less power that are more efficient.
Source: JLS Automation
The company also relies on robotics, which provide good energy efficiencies by nature, says Craig Souser, CEO at JLS Automation (Figure 5). “Electric robots, especially high-speed pickers, are energy-friendly in that they take full advantage of the power conversion of ac/dc/ac to create an efficient energy transfer,” he explains. “An electric servo has high power density, and robots like ours are inherently built with reduced moving mass, so there is as minimal amount of kinetic energy used as possible.”
Figure 5: Robotics, especially high-speed pickers, provide good energy efficiencies by nature.
Source: JLS Automation
Independence days
“Energy efficiency can represent the single largest opportunity for a plant or corporation to lower the bottom line and increase profitability,” says Arun Sinha, engineer at Opto 22. “Plant personnel are typically not responsible or accountable for the energy spend. When a machine builder or OEM designs energy efficiency into the machine, it provides a financial benefit that the client may not have considered (Figure 6).”
Figure 6: Energy efficiency can represent the single largest opportunity for a plant or corporation to lower the bottom line and increase profitability. When a machine builder or OEM designs energy efficiency into the machine, it provides a financial benefit.
Source: Opto 22
No matter who is financially responsible for keeping energy costs under control, it can’t be done without everyone’s participation, says Danny Weiss, senior product manager at Newark element14. “All industrial components and devices must be considered as part of an automation system that can have a profound impact on energy consumption,” he says.
The benefits are wide-ranging. “Promoting energy-smart machine designs can help to achieve cost reductions in areas beyond the power bill,” says Aurelio Banda, president of Beckhoff Automation. “It has far-reaching effects on maintenance costs, as repairs may be made in lieu of replacement, and expensive unplanned downtime can be avoided.”
What’s great about energy-efficient designs is that, in many cases, they make the application more productive, says John Bridges, technical business manager at Aventics. “Higher pressures associated with oversized or less-than-optimal types of components reduce cycle times,” he explains (Figure 7). “Optimized system designs and components produce total cost of ownership savings by using less energy coupled with higher productivity.”
Figure 7: Energy-efficient designs often make the application more productive. Optimized system designs and components produce total cost of ownership savings by using less energy coupled with higher productivity.
Source: Aventics
Design considerations
“Energy efficiency begins in the design phase of a machine, for example, selecting electrically driven processes versus pneumatic or hydraulic,” says Corey Morton, director of technology solutions at B&R Industrial Automation. “The initial cost of selecting an electric solution may be higher, but in many cases the ROI can be extremely short from an energy savings perspective (Figure 8).”
Figure 8: Energy efficiency begins in the design phase of a machine, for example, selecting electrically driven processes versus pneumatic or hydraulic.
Source B&R Automation
Consider that, with a servo pump, the motor can be completely off until it actually needs to work, explains Ken Kerns, product specialist for low-voltage drives at Siemens. “By comparison, with a normal hydraulic type application, you’d have to continuously recirculate the hydraulic fluid to maintain the certain pressure,” he says.
“Proper sizing and selection of system components is another key to energy efficiency, from avoiding dead volumes and oversizing of components to having the correctly matched products for the application,” suggests Aventics’ Bridges. “We are seeing increased usage of online design tools, not just CAD, to simplify this task. Our online energy-consumption calculator defines how much air a machine uses. Our online product calculators help calculate loads and select optimal-sized components. Product configurators allow customized designs of the exact components needed. We also provide an online catalog and Scheme Editor circuit drawing software.”
Power transmission
“According to the U.S. Energy Information Administration (EIA), electric motors account for about half of the manufacturing sector's delivered electricity use,” says David Schrader, product manager at Fuji Electric of America.
“We as a standard use a high-efficient motor, but there are also NEMA premium efficient motors and super-premium-efficient motors,” says Rich Mintz, product manager for gear motors at Siemens. “We help machine builders understand the difference, why to use one over the other and their cost-benefit breaking point.”
The type of motor can make a big difference. “There are readily available energy-efficient induction motors, or permanent-magnet (PM) motors can be selected to provide even greater efficiency,” says B&R’s Morton. “The method used to drive the motors can be another good opportunity for efficiency. A very common example is using a variable frequency drive (VFD) on a rotary pump, as opposed to running a motor at full voltage.”
The use of adjustable-speed drives to optimize flow and improve productivity can be a huge energy saver, says John Malinowski, senior manager of industry affairs at Baldor Electric. “As more systems are designed using adjustable-speed drives, factories are able to connect the equipment using Ethernet and use process control to optimize process flow, gaining in productivity and reducing kWh per widget produced,” he explains.
“We provide a number of low-voltage-drive series options that eliminate inrush currents and compensate for voltage fluctuations, as well as provide for power factor correction in machine applied motors,” adds Fuji’s Schrader. “Use of our Frenic low-voltage ac drives, for example, can reduce power consumption by controlling motor speeds.”
Since motor efficiencies are nearing the limits of design, Baldor started to look at other components in the systems that add to losses, such as gearing. “A double reduction worm gearbox may be 50% efficient where a helical or helical/bevel gearbox could be 95% efficient,” says Malinowski. “This is a huge savings.”
How the gearbox is connected to the machine also makes a difference. “Are you using a direct drive where there are zero losses or are you using a belt that is 85% efficient?” asks Mintz. “Once you’ve maximized the motor and gearbox, look at the drive and whether there is software that can change the characteristics of the output to further improve motor performance. Slowing down and extending ramp times are also good places to start.”
New technologies lead to new approaches. “A typical cooling tower uses a two-speed motor operating a vertical flow fan connected to a right angle worm reducer,” says Malinowski. “Baldor has developed a direct-drive permanent-magnet motor that is a drop-in replacement for the gearbox. This operates from an adjustable-speed drive and controls the speed of the fan based on the temperature of the coolant.”
The fact is, the components are becoming pretty darn efficient, so you have to look at how they act together in the integrated system to gain more efficiency. “That’s starting to take place,” remarks Siemens’ Kerns.
Low-power modes
“New for us in the past couple of years is the ability to focus in on energy management from an operational vs. non-operational state,” says Phil Kaufman, energy technology manager at Rockwell Automation. “Our focus is helping machine builders to understand how to reduce their loads, put equipment into pause or sleep mode and have it back and ready to resume operation at predetermined periods of time such as after a lunch, break or changeover.”
Low power modes provide recurring value to end users. “It’s like when a laptop goes into sleep mode to save energy,” explains Mary Burgoon, market development manager at Rockwell Automation. “We’ve moved from using energy-efficient assets and hardware as part of the machine to make it run more efficiently to helping it operate more efficiently given how our customers will be running their lines, production schedules and energy peak demand charges.”
Rockwell Automation is helping machine builders to understand how much energy is being utilized during manufacturing vs. how much energy is used in total, adds Kaufman. “With these two KPIs, we can start to help end users to do what Dad always said: ‘Turn the light off when you leave the room,’” he explains. “Once more machine builders support low power states, the next competitive goal will be to offer the most efficient low power state, the deepest sleep and faster resume states.”
Siemens offers an ECO mode in some of its drives. “This monitors the magnetic flux within the motor, and, if the motor is not operating at its optimum load, the drive will reduce the magnetizing current, which helps save energy consumed by the drive itself,” says Siemens Kerns. “With hibernate mode, if the system goes into a non-operational state, the drive will go into a standby state and hibernate until it’s time to come back up.”
Another option is Profienergy from Profinet. “Smart shutdowns and smart startups can be programmed to occur periodically throughout the day or during a long shutdown, putting it into an idle mode and bringing it up ready to go at any given time,” adds Kerns.
Technology takes over
“On the drive side, for applications like a downhill conveyor where you need to maintain a certain torque or speed, the motor acts as a generator,” says Siemens Kerns. “Traditionally, there’s a braking module within the drive to manage the motor-generated energy by dissipating it in a large bank of resistors. Since you can’t just put that excess energy back into the drive, it’s usually wasted on resistors that get really hot. A more efficient solution uses regenerative technology with the drive, which consumes the excess energy in another area, whether it’s shared with another load that has a motor on it, which we call smart energy sharing, or it’s physically put back onto your line. Now we’re seeing technology advancement at the basic drive level to where you have some regenerative capability even in the lower-horsepower, general-purpose types of drives. In the past, that technology would have been cost prohibitive.”
“For certain applications, regenerative energy can be a large source of waste if dynamic breaking resistors are used to dissipate this energy,” explains B&R’s Morton. “Using active front end (AFE) technology, available with the ACOPOS multi-drive system, allows this excess energy to be returned to the ac mains. AFE technology also provides a low-harmonic solution and can regulate to unity power factor, both of which can reduce the demands on a facility’s power distribution system.”
End users would like to have machine builders report energy, although some may not see actionable value in the added overhead cost of adding power monitors to the machine, advises Rockwell Automation’s Kaufman. From an operational perspective, power is very important to the machine performance over time. Opto 22 offers a variety of products that allow machine builders to connect to, monitor and visualize their energy load, says Sinha.
“Simple parameters like voltage and current can indicate how the machine is performing against specifications and when it may be due for preventive maintenance,” explains Sinha. “One new trend is the concept of energy intensity, which is a measure of consumption vs. unit of output such as number of parts, gallons of product, weight.”
Some end users have found a system-integrated solution for power measurement and analysis, as well as condition monitoring, to be incredibly useful in increasing energy efficiency, says Beckhoff’s Banda.
Beckhoff offers energy-measurement solutions integrated into standard I/O terminals, leveraging the EtherCAT industrial Ethernet system. “With these tools, system-integrated energy-efficiency monitoring of machines, an overall factory or even power-generation infrastructure becomes possible. This high level of monitoring accuracy can also help to root out energy-related factors contributing to suboptimal production and reduced capital equipment health,” explains Banda.
“Energy-efficient machines with robust power monitoring have a direct tie to Industry 4.0 and the Industrial Internet of Things (IoT). This is because energy consumption is one of the critical production data that highly connected businesses need to share and manage across the enterprise,” adds Banda.
Sponsored Recommendations
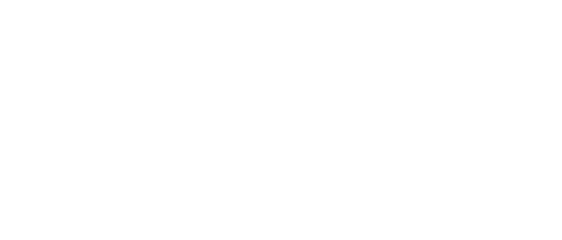
Leaders relevant to this article: