David A. Strobhar, PE, is one of the founders of the Center for Operator Performance, and principal human factors engineer at Beville Engineering in Dayton, Ohio. Contact him at [email protected].
I’ve heard many comments and discussions in the past few years regarding the color grey. Is that even a color? I’m not talking about the 50-shades-of variety. The use of a grey background on process graphics has become all the rage, or rage-inducing, depending upon with whom you are talking. Is background color on a display so powerful that it can, by itself, radically improve operator performance?
There are other elements of HMI design, so where do they fit in? If you rely on more than five decades of human performance research, I would argue that the order of importance for the elements of HMI design would be as follows, with background color the least important of them:
- content
- organization
- layout and formatting
- color coding
- symbols/shapes
- number and size of monitors
- background color.
Many people would likely have ordered this list the reverse of what I have. Their upside-down view of which elements are important in HMI design likely stems from a misperception of what HMI design is all about. People often think display design is fundamentally a visual issue. It’s not. HMI design is about information transfer: transfer of information from the process to the operator at the console. As such, the key concern needs to be how to transfer information, not visual representation of objects.
An easy way to think of this is storytelling, an analogy put forth by Don Norman, one of the pioneers in human factors. In telling a story, you’re trying to transfer some information. There are a variety of mediums for doing this—verbal, print, movie, play. While the medium can aid the transfer, it doesn’t in itself result in the transfer. The best prose, pictures or visual effects do not a great story make. Similarly, the best shapes, dynamos and color do not a great HMI make. Fundamentally, the success of the transfer depends upon the content.
This focus on content was emphasized in one of the first projects funded by the Center for Operator Performance, which is a collaboration of operating companies and DCS suppliers based at Wright State University in Dayton, Ohio. In conducting a project on color usage, Dr. Jennie Gallimore pointed out that, while poor color coding can hinder performance, it is proper content that is essential to performance. If the correct content is present, albeit with poor presentation, the task can likely still be performed. However, if the content is absent, task failure is almost guaranteed regardless of the presentation.
Many people would say that the content for the HMI is determined by the I/O of the process. It’s not. The I/O constrains the content, just as the events in your life constrain your biography. However, a biography that contained every event in your life presented with equal weight and detail would be both very long and very dull. Similarly, a good HMI design entails selection and organization of those I/O relevant to the tasks required. This selection and organization can and should be the longest part of the HMI design process. It not only is necessary to ensure good HMI design, it speeds the subsequent display design efforts and minimizes rework.
If done correctly, this process will yield a far more compact and efficient HMI than one designed in a stream of consciousness approach, simply drawing graphics starting from the beginning of the process to the end. Keep in mind a famous quote attributed to Abraham Lincoln, among others—“I am sorry to have written you such a long letter, but I didn’t have time to write you a short one.” Optimizing information transfer requires upfront thought and effort.
So should I just ask the users what information they need? While user input is essential, we often don’t know what we really need. Just because we know how to do something doesn’t mean we have analyzed how we do it and with what information. Most adult Americans can drive a car, but few have taken the time to determine the information processing and skill required to do it. Many a process plant operator has asked for an interface that replicates what they have, often because they know they are successful in using it. However, that can lead to either replicating a negative design or failing to produce a superior design.
For example, at one plant the operators wanted the hardwired firing panel for a boiler duplicated on screen, failing to realize that the panel did not have the necessary fuel flow and pressure controls needed to operate the firing panel. They failed to realize the need since those controls were relatively close on the hardwired panel. Once on an HMI, they would be on another screen. The operator would need two screens to perform the task rather than one. Obviously the operator knew how to perform the task; he just hadn’t analyzed what it actually took to accomplish it.
Once the information that is needed is known, it must be organized and structured. Hopefully in writing your autobiography—the transfer of information about your life—you would take the time to organize the events in some structure. While a chapter for each year would cover your life, it would likely be a poor way to transfer the information, just as a display for each piece of equipment is a poor HMI. Organization of the information into a hierarchy is a good approach for a variety of reasons. As you move down the hierarchy, greater detail is provided. The pinnacle of the hierarchy is those variables needed for an overall assessment of the process to maintain situation awareness—the big picture—and avoid tunnel vision. This pinnacle, the overview display, should reflect the hierarchy underneath it.
Now comes the point which most people think of as HMI design, the layout of the displays. Is that not simply a reflection of the equipment itself? No, that is a flaw called naïve realism. HMI design is about information transfer, and information is the reduction in uncertainty. Showing me the level in a vessel reduces my uncertainty about that level. Evaluation of any display or display element should entail an assessment of how it reduces uncertainty. Does showing all the trays in a tower reduce uncertainty? Not if I already knew how many trays were there. If it does reduce uncertainty, does the display element do so in the most efficient manner? This should be thought of in terms of bits/in2, the information transfer for a given area of the display. If you want to convey the status of a pump, then maximum information transfer will occur using a symbol sized just above the threshold for readability. Anything larger is less bits/in2: the same information divided by a larger area is worse information transfer.
Coding is a useful human-factors tool in that it enables more information to be transferred in a smaller space and in parallel with the other information, if it is done correctly. There are four major types of codes: color, shape, position and alphanumeric. The first two have the greatest use in HMI design. Color coding is simple in concept, each color used for coding has a unique—one and only one—meaning associated with it. If red means warning, then it cannot also mean “closed.” Since we humans are limited in our perceptual abilities, only about seven colors can be effectively utilized for coding. For shape coding, the goal is to transfer the information in as small and simple of a way as possible. A study by the U.S. Navy showed strong preference for symbols that looked just like the real aircraft, but performance was 70% better when simple triangles were utilized.
Of little importance is the number and size of the monitors the operator uses. This is due to the limitations of how we humans perceive our world. First, our conscious processing is limited to about seven chunks of information. So, even if each monitor could be processed as a chunk, which is unlikely, more than six monitors are likely to be unused. Second, the primary visual field for people is a 28-in diameter circle at normal viewing distance. Placing information outside that circle will exponentially reduce its usability. Adding more monitors will add little value. While many an operator has maintained that they do use all their monitors, it is surprising how often you will find the same display on multiple monitors.
Finally, the background color of the graphics needs to be set. What color? It doesn’t really matter, as long as the contrast ratio with the foreground colors is maintained. Operators have been told that grey background is best, yet grey includes everything from almost black to almost white. One plant switched only the background on their graphics from black to light grey. The cyan (light blue) process variables were almost unreadable. Grey, blue and tan are all viable background colors, as long as the contrast with the foreground colors is adequate.
Hopefully, if you’re in a conversation on HMI design, you’ll now be able to focus the discussion on the key elements. The key to effective HMI design is maximizing the transfer of information. This will require upfront effort to define that information and organize it. The result, though, will be better performance by the user and, hopefully, superior process performance, as well.
Main Image courtesy of Victor Habbick at FreeDigitalPhotos.net
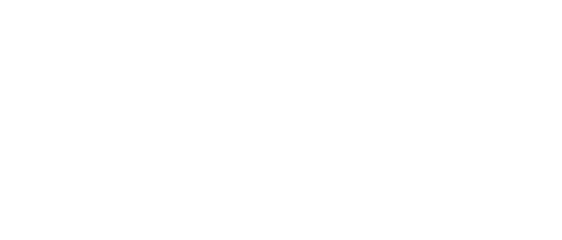
Leaders relevant to this article: