Case Study: A catalyst for smart manufacturing with Germany’s SmartFactory
Digitization is without question the major driving force that is turning our world inside out. The spaces around us are increasingly pervaded by smart and connected systems. What started with the Internet of people will end in an Internet of everything. The phenomenon known as the Internet of Things (IoT) will affect settings of all kinds—homes, cities, traffic, logistics, retail and medicine. And it will not stop at our factory gates.
McKinsey estimates the potential economic impact of IoT applications in 2025 is between $3.9 and $11.1 trillion, of which $1.2 to $3.7 trillion is allotted to IoT applications within the factory environment. Also known as Smart Manufacturing, or Industry 4.0 in Germany, the IoT is the technological driver for fully networked manufacturing ecosystems.
In a future where all “factory objects” will be integrated into networks, traditional control hierarchy will be replaced by a decentralized self-organization of products, field devices and machines. Production processes will become so flexible that even the smallest lot size can be produced cost-effectively and just in time to the customer’s individual demands.
Despite this huge potential, the introduction of IoT technologies in the rather traditional domain of manufacturing, where investment cycles are long and robustness of processes and technologies outweigh striving for innovation, will not happen abruptly. Too many questions have first to be answered. As IoT technologies penetrate ever deeper into our factories to the smallest piece of equipment, technology providers and factory planners are confronted with a variety of hurdles:
- how to assure interoperability, when connecting heterogeneous systems
- how to guarantee real-time behavior and predictability, when thousands of devices communicate at the same time
- how to prevent disruptors, or competitors, to take over control of highly networked production systems
- determining the benefit or return for investing in IoT technologies.
To compensate for technological uncertainty and financial risks, it requires adequate pilot environments, where smart manufacturing technologies and strategies can be implemented, evaluated and showcased for the first time. This is why almost every big IT or automation technology company has built its own smart manufacturing lab, where it can test and demonstrate proprietary solutions. But they are missing one important point: Smart manufacturing is a network paradigm affecting wide-ranging areas from automation to IT, from digital planning of a product to its recycling, and from smart sensors to the business applications.
There is no single-solution provider that can cover all of these aspects at once. So, for holistic solutions to emerge, there has to be a network of technology providers joining forces and competences to develop compatible solution blocks that fit the future requirements of technology users.
Collaboration model
The SmartFactoryKL in Kaiserslautern, Germany, is one of the places where holistic smart manufacturing solutions are developed jointly within a network of more than 40 companies and the research community (Figure 1). This includes large multinational enterprises such as Cisco, Huawei, IBM, SAP and Siemens, as well as small and medium-sized enterprises. Founded in 2005, the SmartFactoryKL association is recognized as the first vendor-independent factory lab for industrial IoT applications. An important element of its mission is to test innovative factory technology under realistic conditions and to move it as quickly as possible from the laboratory to the marketplace.
Figure 1: Holistic smart manufacturing solutions are developed jointly within a network of more than 40 small, medium and large companies and the research community.
A pragmatic approach is key for the collaboration within SmartFactoryKL. The association connects technology providers and users, regardless of competitive aspects. The group of technology providers divides into companies with and without overlapping business/competence areas. Technology providers with overlapping business/competence areas find a platform, where they can set vendor-independent standards and make proprietary technologies and business models ready for open ecosystems.
In contrast, technology providers with complementary business/competence areas benefit from networking opportunities arising by connecting different domains—for example, at the interface between classic automation technology and IT systems, such as big data applications or digitization of maintenance processes.
Also read: The manufacturing industry is on the verge of an evolution
Finally, the group of technology users represents manufacturing companies that want to prepare for the smart manufacturing era and learn how to introduce IoT technologies within their individual manufacturing setups. The network is complemented by research partners. Their role is to draw and continuously adapt the smart manufacturing vision and to coordinate the company collaboration. Joined together like puzzle pieces, the roles and competences of the individual SmartFactoryKL members contribute to the big picture of smart manufacturing.
Working groups
The network is organized into four working groups that lay the groundwork for the practical implementation of smart manufacturing solutions (Figure 2).
Figure 2: The network is organized into four working groups that lay the groundwork for the practical implementation of smart manufacturing solutions.
The first working group (AG-0 Visionary Applications) takes over a coordinating function. It coins the SmartFactoryKL vision, defines its road map and investigates the overall impact of IoT technologies and business models. The remaining three working groups focus on thematic aspects. The second working group (AG-1 Infrastructure) researches technical environments, in which production modules can be commissioned and operated in a flexible, efficient and safe manner. The third working group (AG-2 Digital Factory) is dedicated to IT-based methods and tools for planning and optimization of the product and production lifecycle. The last working group (AG-3 Automation) is concerned with modularization approaches for flexible and efficient automation.
Figure 3: In the first production line, developed in 2006, liquid soap is processed, colored, bottled and labeled according to the customer’s individual order. The technological focus is set on modular manufacturing concepts and smart product memory solutions.
The working groups meet on a regular basis to elaborate on common specifications and standards that suit the smart manufacturing idea. Many of their outcomes can directly be transferred into the development and operation of large-scale prototypes in order to deliver tangible proof and best practices, which is then reflected back again to the working groups. In this way, the involved partners learn how best to design and build next generation production systems and how to launch products that make smart manufacturing become reality.
Testbed activities
Figure 4: The second production line, developed in 2012, assembles small-scale consumer electronic products, such as flashlights. The system is based on smart product memory solutions, but also features a decentralized control architecture using cyberphysical systems.
Figure 5: The latest prototype, developed in 2014, is the highly modular, multi-vendor production line featuring plug-and-play module extension. It is a best practice example for recent SmartFactoryKL collaboration activities.
To fulfill its task as a vendor-independent test and demonstration lab, SmartFactoryKL possesses the capacities to plan, build and maintain complex, industrial production lines. Besides some small-scale demonstrators, three production lines were built to integrate, customize, test and demonstrate smart manufacturing solutions in a realistic setup.
In the first production line, developed in 2006, liquid soap is processed, colored, bottled and labeled according to the customer’s individual order (Figure 3). Here, the technological focus is set on modular manufacturing concepts and smart product memory solutions.
The second production line, developed in 2012, assembles small-scale consumer electronic products, such as flashlights (Figure 4). The system is based again on smart product memory solutions, but also features a decentralized control architecture using cyberphysical systems (CPSs).
The latest prototype, developed in 2014, is the highly modular, multi-vendor production line featuring plug-and-play module extension (Figure 5). It is a best practice example for recent SmartFactoryKL collaboration activities.
Modular, multi-vendor production line
One of the overarching objectives of SmartFactoryKL is to overcome vendor-specific, stand-alone solutions and create a solid base for cross-vendor solutions within manufacturing. Under this premise, a highly modular, multi-vendor production line has been realized in collaboration with 16 SmartFactoryKL partners, demonstrating the flexible networking of heterogeneous factory objects based on jointly set specifications. The activity is based on the understanding that the potentials of smart manufacturing can only be realized by vendor-independent specifications or standards.
Analogous to the development of the Web, universal protocols and information models are required to link smart factory objects and to make production processes comprehensible and accessible for the human worker. With the objective to create such specifications, a highly modular production line was designed within a network, where each partner took on the sponsorship for specific plant components and technologies in accordance with its core competence. This sponsorship concept has proven very successful.
As a result, participating technology providers delivered eight production modules that have been implemented in compliance with the predetermined SmartFactoryKL specifications. These specifications relate to the basic mechanical structure, as well as the power and communication supply of the production modules. Despite these specifications, the providers of production modules retain a high degree of freedom in design decisions, for example, concerning the selection and implementation of specific automation solutions (Figure 6).
Figure 6: The providers of production modules retain a high degree of freedom in design decisions, for example, concerning the selection and implementation of specific automation solutions.
Figure 7: Individual infrastructure boxes can be combined and operated across different vendors, while specific design and additional features can certainly differentiate from competitor's products.
This approach should facilitate the migration from traditional to next-generation control concepts. In addition, each production module is equipped with one dedicated manufacturing capability, such as storage, assembly, engraving or quality control, and may be operated individually or jointly with other production modules, provided they also comply with the SmartFactoryKL specification.
Thanks to this modular design, the plug-and-play paradigm can be brought into reality. The system can easily be extended with additional production modules or capabilities, depending on, for example, the order situation and customer requirements.
To combine production modules universally and with minimal configuration to an individual production process, a powerful and flexible infrastructure is needed. The infrastructure takes on major supply and management functions for the production modules. This includes the power supply, the data routing and the overarching control of the safety functions. Thus, the infrastructure is the connecting lifeline between the production modules that function otherwise completely autonomous.
Also the infrastructure itself must be designed modular and vendor-independent, to not lose flexibility gained in the design of the high-modular production line through laborious infrastructure planning.
To fulfill this requirement, four proprietary infrastructure boxes were developed as the first marketable products by the SmartFactoryKL partners. Here, the feature is that, the individual infrastructure boxes can be combined and operated across different vendors, while specific design and additional features can certainly differentiate from competitor's products (Figure 7).
For factory planners, this vendor-independent infrastructure concept will not only allow more flexibility during installation and configuration or reconfiguration of production processes, but also reduces the dependency on individual technology providers significantly (Figure 8).
Figure 8: The vendor-independent infrastructure concept allows more flexibility during installation and configuration or reconfiguration of production processes.
Another area of interest of in this collaboration relates to the closest possible linkage of automation and IT systems. This is led by the paradigm of synchronization of real and digital worlds for the purposes of transparency and computerized optimization, also know as the concept of the “digital factory.”
Information on the production modules and products to be manufactured should be available digitally and in real time. This will allow far more precise decision making and shorter feedback loops, both within a manufacturing enterprise and between enterprises. Based on available information, novel, data-based services can be developed and offered to the production environment, for example, in the field of remote diagnostics and maintenance. In close collaboration between automation technology and IT providers, the network has implemented and tested, among other, the following concepts:
- real-time digital dashboard coupled with big data applications
- seamless coupling of manufacturing engineering and operation by reusing documentation from the supply chain for shopfloor applications
- vertical integration of information and functionalities from ERP to the production modules
- dynamic, software-based certification methods for highly modular production lines.
Next stop: collaboration
SmartFactoryKL is a unique setting to prepare companies for the next generation of manufacturing. Offering technology providers and users a platform to exchange knowledge, learn from practical experience and ultimately set vendor-independent specifications, SmartFactoryKL acts as catalyst to bring smart manufacturing into reality.
[sidebar id=9]
An essential aspect of the SmartFactoryKL collaboration model is to implement and test smart manufacturing concepts in large-scale pilot setups under real industrial conditions. The implementation of the highly modular production line can be considered a best-practice example for multi-vendor collaboration. Here, key to success is the definition of common standards, which connect vendor-specific subsystems. This guarantees interoperability and enables companies to investigate the interaction of components and technologies within an open ecosystem.
The paradigm of smart manufacturing has awakened the vision of highly efficient, customer-driven factories that seamlessly connect to surrounding smart ecosystems. But, until then, numerous challenges lie ahead. Proving that smart manufacturing solutions are feasible from a technical perspective is only half the job.
One of the biggest problems today is the lack of technology acceptance and system interoperability. Widely accepted standards are a crucial requirement for the next industrial era, but they are far from easy to achieve. First, it requires a significant market demand driven by customers' needs; this is the market pull. Second, it needs a critical mass of companies, which collaborate and agree on common and marketable solutions; this is the technology push.
Of course, no technological revolution has ever been initiated in haste. More often, the upheavals took place respectively over a period of several decades in an evolutionary transition driven by technological advances and market demands. It is highly likely that the current movement toward smart manufacturing will have a similar evolutionary aspect lasting several decades. If we want to speed up these developments, it requires inter-organizational networks and test environments as a catalyst.
[sidebar id=1]
Continue Reading
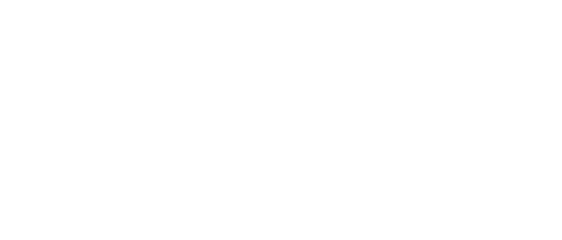
Leaders relevant to this article: