Case Study: Harry Major Machine modern gantry improves plant uptime, recovery time
Figure 1: Harry Major Machine’s facilities include a 100,000-ft2 headquarters in Clinton Township, Michigan.
Harry Major Machine (HMM) provides industrial production solutions and services, specializing in the design and manufacture of automated parts handling systems, industrial parts washers, assembly machines and special machines.
Our facilities include a 100,000-ft2 headquarters in Clinton Township, Michigan, and a 30,000-ft2 plant in the United Kingdom (Figure 1). Our staff and expertise allows us to offer simultaneous engineering, system engineering and integration, equipment installation and mechanical and controls design (Figure 2).
We’ve worked with more than 100 gantry systems utilizing CNC-based systems, mostly for automotive machining manufacturing plants. We wanted to offer manufacturers a linear, PLC-based gantry system as a more cost-efficient and flexible alternative to CNC-based systems since most of our customer base is well-trained and comfortable with PLC systems, and the programming can be flexible for multitasking without major changes to the design of the overall length.
Through our partnership with Siemens, we were able to deliver a gantry system that expands motion-control possibilities and meets the growing requirements and specifications of manufacturers for common designs, modularity and easy-to-use programs in a variety of industries. The system fully integrates advanced Siemens PLC, HMI, servo drives, automation and control products for commonality, safety, diagnostics and seamless component-to-component communication.
Figure 2: Staff and expertise allows Harry Major Machine to offer simultaneous engineering, system engineering and integration, equipment installation and mechanical and controls design.
A needed lift
To keep pace with trends, not to mention competition, automakers, for example, must manage increasingly complex machining and assembly processes during powertrain production. Much of today’s manufacturing demands multipart systems, with equipment being commissioned for future parts. That type of flexibility needs to be designed into the system, while reducing the floor-space footprint of the machinery. Manufacturers in every industry need assembly lines that are more flexible to reduce production time, maintain high availability and keep lifecycle costs low.
Gantry systems are among the more significant solutions on the radar of industrial manufacturers, given its pivotal role in material handling, assembly, sorting, inspection, packaging and palletizing.
Also read: Harry Major Machine Debuts Cableless Gantry Technology for North America
Harry Major Machine provides a range of robotic gantry systems that use the productivity of computer numerical control (CNC)-based overhead gantry robots in an array of production environments. Most gantry systems are CNC-based in performing motion control functions. While these are known for precision and allow all motion functions of a gantry to be manipulated, they’re more expensive to purchase and require higher levels of support from an engineering and maintenance standpoint; parts also are costly.
We were certain a PLC-based gantry system would give manufacturers a viable alternative, as long as the whole package was desirable and cost-effective. The challenge was to ensure the new PLC-based gantry would:
- address real customer needs for unique performance specifications—from speed, uptime and cost requirements to individual plant layout specifications
- increase customer plant capacity, effect higher production value and reduce costs
- expand and enhance gantry control possibilities
- deliver immediate and long-term benefits to manufacturers across multiple industries.
We have just started to offer the PLC-based programs due to the development of faster PLCs. Previously, PLC base units couldn’t process quickly enough for gantry requirements. And due to our utilization of servo drives, there’s no tradeoff of precision with the PLC-based gantry system.
Our intent for the new gantry was to:
- provide a linear, xyz-type gantry that is PLC-based instead of CNC-based
- perform industrial material handling with greater flexibility at a lower cost
- offer a system that’s user-friendly, easy to maintain, able to multitask without major logic changes, deliver higher reliability and reduce resource consumption
- employ advanced hardware and software with more reliable integrated functions, such as rapid engineering efficiency, high performance, innovative design and integrated diagnostics, safety and security
- improve plant uptime, reduce downtime and afford faster recovery times
- offer multiple options that accommodate different lifting capacity requirements.
In the past, servo drives with PLC were too slow for industrial applications. The processor was too slow for transferring data to the drives and system; technology improvements over the past few years have overcome this and other processor issues required for gantry requirements.
As part of the initiative, we wanted to demonstrate real and applicable examples to customers through product demonstrations and at industry trade shows, because nothing compares to seeing a new solution in action.
We were expanding and improving our offerings, and we found that new technologies from Siemens would allow us to exceed our goal of providing a cost-effective and valuable solution for our customers. While developing the new unit on our floor, Siemens came to us with advanced and relevant technologies, including total integrated diagnostics and safety. We chose these and other new Siemens technologies, which helped us deliver dramatic improvements.
The Siemens engineering team came to us, visiting our facility several times with a team of engineers and technical-support personnel to review and suggest solutions that met our needs. Automation Consultant John Gibson, Business Development Consultant Melanie Spare and Account Manager Kevin Merlo led the Siemens team that reviewed our mechanical designs and, based on its findings, developed a bill of materials (BOM) with recommended components and then worked with us to integrate the new product lines.
In 2015, we introduced a new series of linear, PLC-based gantry systems for industrial material handling. The systems accommodate a more extensive range of applications, requirements and specifications than similar xyz gantry systems do. The HMM series includes five models—MGL-30, MGL-50, MGL-150, MGL-250 and MGL-500—with the model numbers representing each system’s lifting capacity in kilograms.
Technology leverage
All plants have unique requirements for system performance and application complexity. The Simatic S7-1516F CPU used in the gantry is part of the Siemens S7-1500 range of failsafe CPUs. Seamless integration of Simatic controllers in the common, totally integrated automation (TIA)-portal engineering framework allows for rapid software development and deployment, consistent data storage, the smart library concept and a uniform operating philosophy to simplify use of universal functions.
Fail-safe Simatic controllers are scalable in processing speed and performance characteristics, and they offer networking options across different communication standards. Integrated diagnostics with efficient fault analysis and fast troubleshooting cut commissioning times and minimize downtimes. Faults are uniformly indicated in engineering on the HMI, the Web server and controller display. The integration of communication from component to component is seamless.
Integrated safety was important. Fail-safe controllers enable the highest achievable level of integration with one controller and one communication system, as well as one engineering path for standard and fail-safe automation.
The PLC controls the gantry carriage by a network in a safe manner. The PLC, drives and motors talk back and forth in a seamless environment. Technology functions for metering and measuring tasks, closed-loop control and motion control also are integrated into all Simatic controllers.
Figure 3: Embedded diagnostics allow the servo motors, PLC, HMI and I/O devices to talk to one another.
The Simatic TP1500 HMI facilitates operator control and monitoring, as well as complex process management. The Simatic TP1500 HMI Comfort Panel offers a 15.4-in-wide screen, a high-resolution TFT display and touchscreen controls (Figure 3).
Interfaces support Profinet with an integrated switch, Ethernet for Profinet, Profibus/MPI and USB. An SD card slot is also included, and the TP1500 seamlessly integrates in the Siemens TIA portal via WinCC.
We found the Simatic 1500 controller with built-in motion control worked very well with the Sinamics S120 drive, which has a range of coordinated components and functions in a package of single-axis drives and coordinated drives, with vector or servo functionalities designed for motion control. Embedded diagnostics allow the servo motors, PLC, HMI and I/O devices to talk to one another. These characteristics and the system architecture and digital communication options allowed for implementation of the customized drive solutions we wanted for flexibility and increased productivity. Efficient engineering and quick commissioning result from advanced tools and simple wiring.
According to our engineering team, working with a single source for the PLC, HMI, servo drives and the operating and monitoring panel made the integration of communication from component to component very seamless. For example, real-time diagnostic information is accessible on system monitors without any additional programming (Figure 4).
Figure 4: Working with a single source for the PLC, HMI, servo drives and the operating and monitoring panel made the integration of communication from component to component seamless.
Figure 5: MGL series gantry systems are designed to deliver improved plant uptime by 25% and improve fault recovery times by 35%.
The Simatic MP277 Mobile Panel is a mobile HMI—a portable operator device ruggedized for industrial use. The Mobile Panel 277 features short commissioning times and large user memory, and it’s optimized for WinCC-based projects. The panel is operated with touchscreens and membrane keyboards, and it connects to Profibus, Profinet and Ethernet.
Technology platform
Operating elements allow direct access to distributed I/O. Safety functions are available on a mobile basis at any point of the machine. These include a button that stops the machine in critical situations. The panel has a high-resolution TFT display, 64K colors and 18 function keys with LED.
Also used in the gantry technology platform are modular, energy-efficient industrial control products—from safety integrated products to efficient control panel engineering, Profinet, I/O-Link and devices for switching, protection, monitoring, control, commanding and signaling.
The new Harry Major Machine MGL series gantry systems are designed to deliver improved plant uptime by 25% and improve fault recovery times by 35%, based on the number of trained PLC personnel versus the number of trained CNC personnel in a manufacturing plant, as well as their respective abilities (Figure 5).
The new gantry systems also are compatible with a variety of robot technologies, including automation systems and industrial parts washers we offer. The gantries have the ability to feed multiple machines, are capable of I or H arrangements and have a compact footprint. The general designs and even programming are the same; components may vary or change due to servo sizes and requirements.
Siemens assisted our engineering team from the design concept and prototype to design approval, and all the way through commissioning of the gantry. We both agreed from the start that the support team remain the same from both sides, from cradle to grave, so that lessons learned would have been captured completely. This also assured a quicker timeframe for completion. One major hurdle was setting the parameters of the servo drives. During commissioning, the Siemens technical support team was able to resolve those issues.
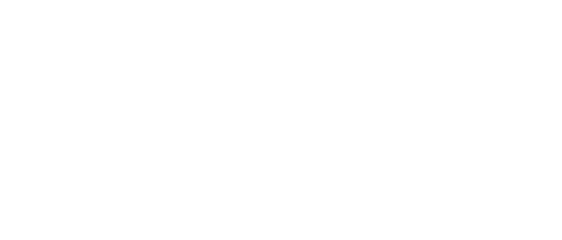
Leaders relevant to this article: