Matthew Bush, COO and co-founder of Hirebotics, a Franklin, Tennessee-based company that rents collaborative robots, will be giving a presentation on eliminating barriers to employee acceptance of robotic automation, as part of the Developing Your Workforce for an Automated Future session on April 6 from 9 am to 11 am at Automate 2017 in Chicago. Contact him at [email protected].
Are you thinking about introducing robotics into your factory? You can make the transition a smooth one and reduce the amount of anxiety felt by your existing human workers. First, why are you looking to add robots to the mix? That will determine how you need to approach introducing robots into your plant.
Plant managers add automation for a few different reasons:
- reduce headcount
- reduce costs/increase productivity
- increase quality
- fill vacancies that you can’t seem to find a human for
- increase global competitiveness
- create a safer work environment from either dangerous tasks or tasks that may cause repetitive motion injuries.
Of all the reasons listed, reducing headcount is probably the hardest to overcome with the existing workforce, and it’s the worst reason of all for deciding to get into robotics as it will drive a high level of anxiety among the workforce and make adoption a long uphill battle.
ALSO READ: Speeding up cobots, updating compliance & 3D factory simulation at Automate 2017
Even if the goal is to reduce current headcount, it is much better to approach that through natural attrition and focus your efforts on one of the other aspects of adding robotics. The first step in bringing automation into your factory, especially if this is your first introduction of robots into the mix, is to discuss with the employees why you are looking to bring in automation. Focus on the problem you are trying to solve with the robots and why you feel that robots are the correct solution. In discussions we’ve had with employees when introducing robots, we’ve always focused on the fact that no one would directly lose a job because we brought a robot into the factory to work. The focus is how we grow the company and ultimately the human workforce by finding new ways to do jobs that allows us to compete in the global market more efficiently.
Are you looking to increase productivity, reduce costs or improve quality? If so, how is the robot going to help to achieve that goal? Is it through consistent cycle times that robots can achieve or the fact that the robot does not get bored standing in front of the machine waiting for the cycle-complete alarm to sound and so can instantly respond and reduce the amount of time that the machine is sitting idle? Is the current job a very tedious or monotonous task, and so it becomes hard for a human worker to maintain a consistent pace due to either needing frequent breaks to reduce the occurrence of repetitive-motion injuries or boredom? Will the precision and repetitious nature of the robot allow you to make a higher-quality product by more closely following customer specifications?
In “The 5 Jobs Robots Will Take Last,” Shelly Palmer lists the four basic types of tasks that make up all jobs:
- manual repetitive (predictable)
- manual non-repetitive (not predictable)
- cognitive repetitive (predictable)
- cognitive non-repetitive (not predictable).
When introducing robots to the factory, we are looking to move the human employees from the manual-repetitive type of tasks, which are highly predictable and therefore easier to automate, to either the manual non-repetitive or the cognitive type of tasks as these are better suited to human operators, as well as harder to automate. It helps to have these discussions with the personnel who will be directly affected by the robots and get their input early and often in the process. Involving the employees in the project is a win-win for both the employee and the company. The employees will feel that their knowledge of the process and the issues that are preventing higher levels of productivity or quality are valued. And, because they are involved in how to make improvements, they will have a sense of ownership and will more easily accept turning their jobs over to a robot.
One area to focus on is filling positions when hiring humans is difficult. There are many reasons for this, including wage competitiveness, dull, dirty or dangerous work and a general lack of personnel in the area due to low unemployment. Manufacturing over the coming years faces a very big challenge finding enough employees to continue to meet demand due to the rapid retirement of baby boomers from the job force and the lack of interest in manufacturing by many that are entering the labor market for the first time. Couple this with a desire to bring manufacturing back to the United States, and you quickly have a labor shortage that will continue to grow. As you look around your company, where are places that you could use a robot to perform low-skilled, monotonous, dull work and free humans up to perform work that is better suited to them? Robot dexterity, vision and cognitive reasoning skills still lag greatly behind their human counterparts’, even though improvements are being made year after year.
Robots can be human, too
Now that you have had the talk with your employees and have gotten them involved in the planning phase of bringing in robots to the factory, what else can you do to help the human employees embrace their new robot counterparts? We have used a variety of techniques to help the humans and robots form a team and learn to work together such as humanizing the robot, giving the robot a voice and using collaborative robots to allow the humans and robots to work in closer proximity to each other.
Figure 1: Not all, but a lot of the robots that we have in the field sport employee badges.
When we deploy robots, one of the first things that we ask our customer is: "What is the robots name?" Often we get this weird look on the customer's face until we explain that, by referring to the robot by its given name, we are able to get employees to more rapidly accept the robot as a co-worker and not the guy who’s here to take my job. We then do our best to always refer to the robot by its name when we are talking to the team. As employees begin to reference the robot by name, they will quickly become attached. Many of our customers have held naming contests or will wait to see what name the employees come up with that are working around the robot. Some of the names we have seen are what you would expect for a robot, such as Johnny-Five or T-1000, but others have been unique, such as Manuel, which we had fun with as the robot is named after the infamous Manuel Noriega. Not all, but a lot of the robots that we have in the field sport employee badges (Figure 1). One side was our standard employee badge with the name of the robot and its ID in our system, as well as a QR code that is used by the customer to interact with the robot using a mobile app. The other side included an actual picture of Manuel Noriega. The employees loved it; they would make sure that was the side that was always displayed on the robot. For them, getting to refer to the robot this way made him part of the team, and they got to have fun with it, which made the robot a lot less scary.
We have seen customers that clothe their robots. For instance, I visited a company a few years ago that had a hair net on a Baxter robot from Rethink Robotics because everyone had to wear hair nets in the facility, regardless of the amount of actual hair on their heads, so that meant the robot had to wear one, too. The robot also had its own employee badge, as all employees had to wear a badge. This made the robot seem more like the rest of the employees and helped them to accept the robot as just another team member.
We once had a robot named Waldo, because you never knew where you would find Waldo when you came to work as it was a six-axis, collaborative robot from Universal Robots on wheels and so we would come in at night and teach him a new job and would often put him someplace new to work. One of the vendors actually bought him a red-and-white-striped shirt like the children’s character.
We’ve also had employees decorate robots for the holidays. So long as it did not cause a safety risk to the humans or a risk to the robot, we were OK with letting the team members have fun with the robots as they became an integral part of the team and the process.
One of the ways to help teams to accept the robot working with them is by giving the robot a voice. This can be accomplished in several different ways, by including pop-up messages on the robot graphical-user-interface (GUI) screen, by using an annunciator that can be programmed with different voice messages that the robot can activate and by allowing them to communicate with customers through a mobile app. These various ways have helped the human and robot to work more closely together as the robot is able to communicate what it needs to teammates so they can collaborate on achieving the best possible results. Have fun with these messages that either pop up on the screen or broadcast over the mobile app. For instance, we have a robot that says, “I need someone to clear the parts at the outbound conveyor,” which is clear and concise, but, when someone does help the robot, he responds by saying, “Thank you for your help. That part was starting to get heavy.” Now, what you can’t realize from the example is the part weighs about 6 ounces, so the statement has some sarcasm in it, but it helps the messaging between the robot and human to not come across as so sterile. It helps to break down barriers between the humans and the robots.
What we have found through deploying robots in our own facilities, as well as customer sites, is that the most critical aspect of eliminating barriers to employee acceptance of robots is ensuring the human employees that the robot is not there to steal their jobs. Talking to the employees early in the decision process about ways to use the new automation to increase productivity, reduce costs or increase quality will improve acceptance. If you can discover what jobs the employees hate doing and have the robot do those jobs, you will be a hero among the employees, and acceptance will almost be a certainty; talking to the employees is key. Once the automation is in-house, it is equally important to foster an environment where the humans begin to value the robots as fellow team members, that, just like any other worker in the facility, the robot is there to do a job. The great thing is, we can give the robots the most dull, dirty and dangerous jobs in the factory, and team members will never have to listen to them complain at break or lunch about how much the robot hates its job. Getting your human workforce to accept the new robot worker is not a given in most situations. But, through clear communication early in the process and involving the current employees in finding the jobs to give the new robot worker, you can knock down the barriers to acceptance and quickly gain the trust of your workforce while reaping the rewards of adding robotics to your factory.
Sponsored Recommendations
Latest from Robotics
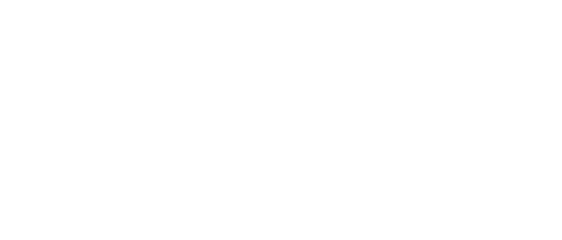
Leaders relevant to this article: