DMDII announces 6 research awards in digital manufacturing disciplines
Each project is managed by a lead organization that coordinates work among other organizations on the team.
The projects span several digital manufacturing disciplines, but each reflects the core mission of DMDII: propelling the field of American digital manufacturing and design forward.
“These project awards sponsor research that will change the way that manufacturers in all segments of the supply chain are able to engage in business,” said Dr. Greg Harris, DMDII’s program manager through the U.S. Army Aviation and Missile Research, Development, and Engineering Center. “The investment in cybersecurity research is particularly exciting, as the U.S. manufacturing sector lacks the compliance pathway and workforce development plan to comply with current standards. This award is part of DMDII’s commitment to moving American manufacturing beyond the 21st century.”
According to DMDII, the projects bring together teams with expertise in a variety of manufacturing disciplines and include major multinational corporations, small enterprises, government entities and university researchers.
Each project is managed by a lead organization that coordinates work among other organizations on the team. Facilitating connections among diverse project teams is a key aspect of the UI LABS approach.
Also read: IIoT implementation challenges and guidance
“This cohort of awardees shows what DMDII and UI LABS are all about: smart cross-sector collaboration that is going to enhance competitiveness for the entire industry,” said Dr. Dean Bartles, Chief Manufacturing Officer of UI LABS and Executive Director of DMDII. “Through these projects, we are lowering cost and access barriers to implementing digital manufacturing practices for small manufacturers across the country.”
DMDII’s six contract awards are as follows:
1. Integration of AVM iFAB Tools for Industrial Use
Lead Organization: Pennsylvania State University Applied Research Laboratory
Other Organizations on this Team: aPriori, Oshkosh Corporation, Parametric Technology Corporation (PTC)
Part of the U.S. Defense Department’s Defense Advanced Research Projects Agency (DARPA) Adaptive Vehicle Make (AVM) program, this project will develop tools and standards for advanced adaptive manufacturing of complex vehicles.
This project seeks to create “design assist tools”– tools that help manage data from design through manufacture and potentially service life –that will increase speed and efficiency and cut down costs. The tools will allow designers to analyze manufacturability and assemblability by creating a simulation that enables them to work on a virtual prototype, rather than a costly real-world one. Ultimately, the tools will be added to the Digital Manufacturing Commons, DMDII’s open-source online platform.
2. Elastic Cloud-Based Make
Lead Organization: GE Global Research
Other Organizations on this Team: Iowa State University, Northwestern University, Oregon State University, Pennsylvania State University Applied Research Laboratory, Quad City Manufacturing Laboratory, Rochester Institute of Technology, Rolls-Royce Corporation
Many SMEs lag behind larger manufacturers in adopting new technologies. A key challenge for these businesses is the adoption of information technology—particularly advanced modeling, simulation, and analysis (MS&A) tools, which is increasingly important to manufacturing competitiveness but can be cost-prohibitive for SMEs.
Through the Defense Advanced Research Projects Agency (DARPA) Adaptive Vehicle Make (AVM) Tool Integration project, the GE Global Research-led team will directly address these technical challenges by enabling SMEs to access the AVM MS&A tools via the Digital Manufacturing Commons.
3. Supply Chain MBE/TDP Improvement
Lead Organization: Rolls-Royce Corporation
Other Organizations on this Team: 3rd Dimension, Anark Corporation, ITI-Global (International TechneGroup Incorporated), Lockheed Martin, Microsoft, Purdue University
This project seeks to push Model-Based Enterprise (MBE) technologies forward by using MBE technology to streamline the design stage of the manufacturing process. This involves the use of intelligent 3D models to eliminate the need to translate to different formats, including 2D drawings, when transferring information between original equipment manufacturers (OEMs) and other companies within the supply chain.
Using MBE ties data related to tolerance, life of product, and other product specs to the 3D model during the design phase and allows it to be used for all stages of the process, eliminating issues of unclear or inaccurate drawings. The combination of the 3D model and accompanying information is referred to as the technical data package (TDP).
As a framework and best practices for MBE/TDP are standardized and disseminated more widely, they will become more useful and accessible to SMEs. As a greater percentage of the supply chain embraces MBE, the number of potential suppliers to the DoD and other major manufacturers will increase.
4. O3 – Operate, Orchestrate, and Originate
Lead Organization: STEP Tools, Inc.
Other Organizations on this Team: ITI-Global (International TechneGroup Incorporated), Mitutoyo America, System Insights
The O3 project will develop a web environment that will enable users to orchestrate machining and measurement processes from tablets and smart phones. Time and money are wasted when a machining program creates a part that does not conform to the design requirements of the customer. O3 will allow users to check machining programs for conformance from remote locations. When conformance is not met, the service will allow the process to be adjusted using apps.
The servers that will be used to host O3 tools will be located at DMDII, and the tools will be available to all manufacturers through the Digital Manufacturing Commons.
5. Advanced Variance Analysis & Make
Lead Organization: Rolls-Royce Corporation
Other Organizations on this Team: 3D Systems, Georgia Institute of Technology, Microsoft, National Center for Supercomputing Applications (NCSA), Penn State University Applied Research Laboratory, Southwest Research Institute (SwRI)
The Advanced Variance Analysis & Make project uses high-performance computing to demonstrate how data coming off of a machine relates to the part made by that machine. It will indicate whether an anomaly in the data is, in fact, related to an anomaly in performance and/or adherence to a design specification for the part.
The analyses will form the basis of a database of production anomalies available through the Digital Manufacturing Commons. Manufacturers will use the resulting data in real time to correct an anomaly if it will affect a part’s performance, or to ignore the data anomaly if there is no evidence of impact on the part’s capabilities, saving time and money during the manufacturing process.
6. Assessing, Remediating and Enhancing DFARS Cybersecurity Compliance in Factory Infrastructure
Lead Organization: Imprimis, Inc. (i2)
Other Organizations on this Team: SPIRE Manufacturing Solutions, Western Cyber Exchange
This project seeks to create, test and implement a uniform cybersecurity standard for DMDII, with the goal of improving cybersecurity and supply chain security across the manufacturing industry. It reflects feedback from DMDII’s large manufacturing partners who have expressed the need for improved supply chain management.
The project will review DoD cybersecurity standards for contractors, assess the costs, capabilities, and training manufacturers need to meet them, then develop a case study to aid manufacturers in meeting them. Ultimately, more manufacturers will be able to become DoD cybersecurity compliant, adding more potential contractors into the DoD and manufacturing pipeline.
[javascriptSnippet]
Sponsored Recommendations
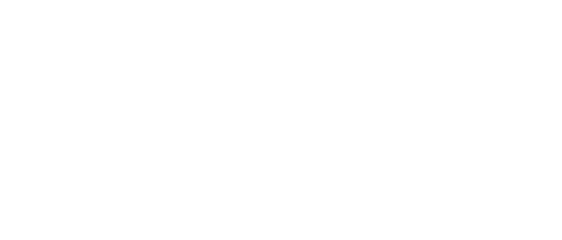
Leaders relevant to this article: