When we talk about making the aging electrical grid smarter or the factory of the future more efficient, what we’re really after are insights that can make our equipment and infrastructure smarter and more efficient. And to deliver these incredibly valuable insights, which will result in millions of dollars in savings, uptime or operational efficiency, we need data. Lots of it. We also need complex, computationally intensive algorithms that scour the data to find trends, patterns and anomalies (Figure 1).
Figure 1: In a world of smarter, hyperconnected devices and infrastructure, data is king.
While these algorithms and analysis routines are a very important piece of the IIoT puzzle, the best data scientists in the world cannot predict equipment failures without enormous amounts of data. And we’re not talking about just any kind of data either. Big Analog Data, a term trademarked by National Instruments, comes from dozens to thousands of sensors and devices spread across your assets, facility or entire fleet. It includes sensors measuring vibrations, pressure and flow; cameras performing thermal scanning and pattern matching; and motors being sent precise PWM waveforms to execute control algorithms (Figure 2).
It’s this type of data that offers the insights you need to unlock the full potential of smarter, connected industrial things, such as bearings that alert you 60 days before they fail or electrical grids that automatically direct power from dynamic, renewable sources to varying and widely distributed loads, all while maintaining perfect three-phase signals.
Figure 2: Big analog data comes from dozens to thousands of sensors and devices spread across your assets, facility or entire fleet.
And this Big Analog Data is big. While all IIoT data ends up digitized to beam across the binary superhighway, each measurement starts out in the physical, analog world, and a lot of digital bytes are required to represent even short and relatively inaccurate analog waveforms. So when channel count, signal duration or accuracy requirements go up, the result is terabytes of (digitized) analog data, sometimes even per hour. Then you add the rest of the data.
Yes, there’s more, including all the digital data from on/off signals and open/close sensors, as well as all the single-point temperature and proximity data. The insights you need to make your operations smarter or more efficient live within this collective set of data. And to extract those insights, you need to collect, manage and analyze the data (Figure 3).
Additionally, many companies deploying IIoT systems today are doing so in brownfield environments, where intelligent edge devices are installed on existing equipment. This means that the same edge devices extracting all that valuable sensor data must also interface with existing industrial infrastructure and the myriad protocols found in various industrial environments. This industrial information adds to the big data to deliver everything you need to extract valuable insight.
Figure 3: You must not only collect but also analyze and manage big analog data to extract insight.
First things first
All of this makes the ability to acquire data and integrate with existing devices a critical piece, if not the most critical piece, of IIoT systems. Storing all your data, protecting your data and analyzing your data are still important parts of the puzzle. But for any of that to matter, you have to acquire the data. So the question becomes, “How do you get the data in the first place?”
Also read: How time-sensitive networking enables the IIoT
Start by choosing an IIoT platform that has the inherent ability to connect to all of the sensors, devices and infrastructure found in IIoT applications. But for a more detailed answer to that question, consider the Industrial Internet Reference Architecture, a handy tool provided by the Industrial Internet Consortium (IIC). The IIC was founded in 2014 to bring together the organizations and technology necessary to accelerate the growth of the Industrial Internet. The IIC has more than 200 members, including small and large technology innovators, vertical market leaders, researchers, universities and even government organizations.
The IIC aims to accelerate the adoption of Industrial Internet systems because, to put it simply, designing and deploying IIoT systems is hard. They almost always require weaving together products from multiple vendors to create a complete system. Different vendors focus on different parts of the architecture, with some parts being more interoperable than others. Then you add the complexities of security, quality of service, bandwidth, data storage and intricate analytics, and sometimes it seems as though the promises of the IIoT aren’t worth the investment. But fear not. The IIC and its member companies are here to help.
You are not alone
One way the IIC helps system designers is through its testbeds, which are where the innovation and opportunities of the Industrial Internet—new technologies, new applications, new products, new services, new processes—can be initiated, thought through and rigorously tested to ascertain their usefulness and viability before coming to market. These controlled experimentation platforms are geared toward specific use cases and scenarios and generate reproducible architectures that end users can adopt and implement in industry.
The testbeds take the guesswork out of deploying high-value IIoT systems and deliver a blueprint that anyone can follow to put all the necessary components together for a complete end-to-end IIoT system. More than 15 IIC testbeds are in flight today, focusing on applications from smart grid and healthcare to smart factory and water management. Chances are, one of these testbeds covers your target use case.
Another helpful output of the IIC is the Industrial Internet Reference Architecture, which summarizes common elements of IIoT systems into three tiers: the edge tier, the platform tier and the enterprise tier. Everything starts at the edge tier, where you interface with the physical world to acquire the data that will deliver the insights that lead to the valuable benefits of safety, uptime, yield, and profitability (Figure 4).
Figure 4: Another helpful output of the Industrial Internet Consortium is the Industrial Internet Reference Architecture, which summarizes common elements of IIoT systems into three tiers: the edge tier, the platform tier and the enterprise tier.
In the edge tier, you use intelligent edge devices, or edge nodes, to interface with sensors, actuators and other devices and assets that are part of your IIoT network. You can place these edge nodes at each asset or, for lower channel-count applications, you may deploy one edge node for every few or several assets. Regardless, deployed systems almost always contain many edge nodes distributed across a wide area. You connect these devices in the edge tier to form the proximity network.
The edge tier interfaces with the platform tier through the access network, usually through a device called an edge gateway. You can implement the access network in many ways, such as a local intranet or an on-site cellular network. The platform tier serves as the connective tissue between the other tiers, hosting non-domain-specific services such as data queries and analytics, while the enterprise tier performs more domain-specific applications such as the decision making that might send control commands back down to the edge tier.
The service network connects services and applications across the platform and enterprise tiers and delivers the security, safety and quality of service requirements dictated by IIoT applications.
Edge node selection
When choosing a device for your edge node or edge gateway, consider the fundamental need to acquire data and interface with myriad sensors, actuators, devices, protocols, networks and control systems. The edge node must be rugged enough to be deployed into harsh industrial environments and perform reliably for long-term operation. It must also provide native support for any kind of sensor, from simple analog input such as 0–10 V or 4–20 mA to more complex measurements like IEPE vibration signals, high-resolution audio waveforms or infrared and thermal imaging signals from industrial cameras. The edge node should also support the most common industrial protocols such as OPC/UA, HART, Modbus, EtherCAT or EtherNet/IP. Many vendors offer products to meet these needs, but the requirements don’t end there.
The ideal edge node also delivers the ability to perform local processing, analysis and even control. Consider an application in which you are monitoring critical assets to detect and prevent failures. These failures could result in anything from expensive downtime to catastrophic explosions and loss of life. In one architecture, you deploy an edge node to acquire data, which you send up to the platform tier and enterprise tier for analysis, incurring the latency of the network.
[javascriptSnippet]
When the analysis determines that measurements are out of spec by a large margin, failure is imminent and you must take precautions. You send commands across the service network back down to the edge tier or to a supervisory control station, where an operator or automated device can stop the machine in question for servicing.
But the reality is that you may be too late. What if you had intelligent edge nodes that not only interface with any sensor on any bus but also contain enough processing power locally to perform advanced analysis and control? In this case, you can analyze measurements, compare them with thresholds and immediately implement the resulting control commands at the asset itself. Furthermore, this benefits the entire system by sending only necessary data or commands to other tiers in the system, which frees up storage and bandwidth across the enterprise and offloads the centralized and cloud-based analytics systems.
Conclusion
So when you set out to tackle the design and deployment of an Industrial IoT system, keep in mind that a key piece of the puzzle is choosing an edge node that can collect the data you need, because data is the prerequisite to insight. Also, remember that associations like the IIC are available to help you deploy an effective system from day one, with reference architectures to follow as a blueprint. This will ensure that your system delivers the insight you need to realize the promises of the Industrial Internet of Things.
Sponsored Recommendations
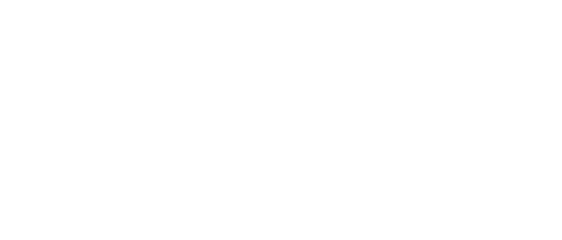
Leaders relevant to this article: