Since 2004, Signal.X Technologies in Northville, Michigan, has provided software and systems integration for complex end-of-line test systems and industrial automation. Controlling a production test system requires a multi-disciplinary team that brings together electrical, mechanical, hydraulic and controls knowledge. Done correctly, end-of-line test systems operate reliably day in and day out, while maintaining the level of flexibility needed to add new models, facilitate troubleshooting of components and provide the correct level of insight into the machine performance and health.
STAX platform
PLCs have traditionally been the primary solution to meet this requirement and are still the right choice for many machines. However, as these test systems become more complex, Signal.X has found that PLCs do not always satisfy the needs for high-speed data acquisition, signal processing and database interaction. In lieu of simply placing a PC next to a PLC on the production line, Signal.X created the STAX manufacturing test platform, built on the National Instruments CompactRIO hardware (Figure 1).
Figure 1: As test systems become more complex, PLCs do not always satisfy the needs for high-speed data acquisition, signal processing and database interaction.
(Source: Signal.X)
When we began deploying automation and control systems using NI hardware and LabVIEW, we wanted to create a configurable platform that was easily understood by a controls engineer who was used to working with PLCs but did not necessarily want to learn LabVIEW to modify how the machine worked. The result of that effort is the STAX platform.
At its core, the STAX platform turns NI hardware, specifically the CompactRIO, into a PLC, but with the power of LabVIEW to acquire and log high-speed data and communicate to devices. STAX contains a ladder-logic emulator that is used to program the behavior of the control system, with editing and monitoring tools very similar to a PLC (Figure 2).
Figure 2: The STAX logic editor includes a ladder-logic editor with editing and monitoring tools similar to a PLC.
(Source: Signal.X)
Hutchinson Antivibration Systems (www.hutchinson.com), which specializes in vibration control, fluid management and sealing technologies, located in Grand Rapids, Michigan, recently put the STAX platform to work on a test system that required automation, communication with a line PLC, sophisticated control and data acquisition. The STAX controller is testing active mass dampers as part of the assembly line to ensure the products are assembled correctly and meet customer requirements (Figure 3).
Figure 3: Active tuned mass modules are sophisticated components similar to a linear voice coil.
(Source: Signal.X and Ram Truck Engineering)
Destructive interference
The active mass dampers are called active tuned mass modules (ATMM) and are used to counteract unwanted vibration in automotive applications to improve customer perception and comfort. As emissions-reduction initiatives such as cylinder deactivation and engine downsizing become more commonplace, active mass dampers are critical to achieving noise, vibration and harshness (NVH) performance targets for customers.
Modern cars and trucks use a variety of closed-loop technology. An active suspension is one example. Level switches, air shocks and compressors are used to level a truck under load. Another example is engine cylinder deactivation technology. The engine will switch from eight-cylinder operation to four-cylinder operation to improve efficiency. A problem with this technology is that undesirable engine vibration can be felt through the floor and seats when only four cylinders are firing.
The 2019 Ram 1500 truck uses cylinder deactivation engines, the HEMI multi-displacement system, but uses ATMM to counteract the vibration, which makes the truck smoother. The ATMMs can be thought of as active shake weights. These solenoid-activated weights are mounted to the outside of the frame rails on both sides of the truck, near the front passenger area.
The ATMM technology is similar to noise-canceling technology, which is also used on the Ram. Sensors under the hood detect the engine vibrations, which activate the ATMMs, shaking them to create a vibration that is 180° out of phase of the undesirable vibration, canceling it. The vibration the ATMMs create is called destructive interference. The tuning of this interference varies, depending on the length of the truck frame.
These active mass dampers are sophisticated components resembling a linear voice coil. They are required to be 100% tested at the end of line. The test consists of controlling the command to the coil at various frequencies and measuring the response of the component through load cells to verify the correct forces are being generated. By utilizing high-speed measurement of the voltage, current and load to the part, the test system can accurately detect defective parts before they are shipped to the customer.
Advanced control
STAX implements a user-configurable, logic-based execution system that leverages multi-threaded embedded software development in LabVIEW. By utilizing a defined data space from each thread of the application, STAX creates a logic engine that makes decisions based on the state of the system, sets outputs and sends commands to each thread.
Hutchinson utilizes STAX to sequence the test, communicate to the line PLC, acquire data and analyze the data for pass/fail determination. Signal.X customized the STAX controller for this system to send a high-speed waveform to a power amplifier to drive the coil inside the damper, leveraging the power of the field programmable gate array (FPGA) in the CompactRIO.
STAX incorporates concepts that are familiar to ladder-logic programmers. STAX is configured to evaluate decisions based on inputs and command actions when a rung evaluates to a true condition. It can be structured to support various modes and evaluate actions in sequence or in parallel, accommodating continuous limit checks and sequence control in manual or automatic mode or as a global check.
This provides the customer with a sophisticated and flexible tool to serve testing needs while allowing an engineer with limited or no LabVIEW knowledge to configure the test system to future needs. However, the modularity of the architecture allows experienced developers to modify the threads of a custom application that provides data to the STAX logic engine. STAX systems can scale from a simple durability test application to controlling a refinery through this modularity.
Meanwhile, the STAX controller is also acquiring and analyzing the signatures from the test itself. The platform includes tools that help engineers to process, visualize and improve the pass/fail decision. STAX builds on Signal.X’s experience in metric-based decision making for manufacturing test systems. Hutchinson Antivibration Systems not only gets a pass/fail decision at the end of line, but can also archive the data using our Trove data collaboration server. Trove retrieves data from the tester and archives the data file, as well as enters metadata and test results in a SQL database.
The ability to view, mine and reprocess data from the test stand enables Hutchinson to understand its manufacturing process, adapt to changing requirements and improve the test system as the process matures (Figure 4).
Figure 4:The controller also acquires and analyzes vibration signatures from the test that can be viewed, mined or reprocessed.
(Source: Signal.X)
Historically, manufacturing plants have not been receptive to LabVIEW and National Instruments as part of the production process. Many plants believe maintenance of the systems requires LabVIEW experts. Asking a controls engineer who is an expert ladder-logic programmer to also learn LabVIEW is an unrealistic expectation in most plants. STAX enables controls engineers and technicians to maintain and manage sophisticated test systems using programming that is familiar and intuitive.
Hutchinson Antivibration Systems has leveraged the STAX platform successfully to implement a single test system that previously would have required either custom hardware or a combination of control, function generators and data acquisition. From controls engineers to NVH managers, this system can be monitored and maintained by Hutchinson Antivibration Systems personnel and is a reliable platform that can survive the demands of the plant floor for years to come.
ALSO READ Case Study: Vision guides high-speed robotic packaging
Latest from Control Software
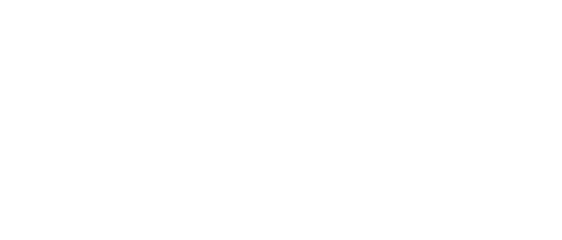
Leaders relevant to this article: