P. Hunter Vegas is senior project leader at industrial process control system integrator Avid Solutions, based in Winston-Salem, N.C. Vegas and his colleagues have engineered and installed many fieldbus systems in many different industries. He spent a great deal of time interviewing engineers and technicians in end user firms. This article is the result of that work
This is Part I of a two-part article. Part I discusses fieldbuses in general and outlines the true costs of field installations. "The Fieldbus Jungle — Part II" discusses advantages/disadvantages of individual fieldbus technologies.
There have been countless articles that tout substantial savings generated by fieldbus networks. Most claim greatly reduced wiring, marshalling panel and I/O space, reduced commissioning time, and extensive savings from putting control out in the field devices.
SEE ALSO:Â Trouble-Free Fieldbus Tips
These all are mostly true statements. However, when you consider the larger picture, those benefits and savings can be offset by other factors rarely mentioned. It is important that the automation professional considers all of the relevant factors before choosing a technology.
In this article the word "fieldbus" refers to digital networks in general. The scope of this discussion is limited to the instrument-level fieldbuses: Profibus-PA, Foundation fieldbus, AS-i and DeviceNet.
The Real Economics
Does fieldbus save wiring cost and reduce installation cost? It depends.
Fieldbuses replace multiple I/O cards and individual instrument wires with a single card and a single wire running to the area and then split off to the instruments. The amount of reduction is dependent on the fieldbus used, how it is installed, and the area electrical classification. On average, it is fair to say that fieldbuses will reduce wires and/or terminations by at least a factor of 4, and some fieldbuses can save a great deal more than that.
It is also true that there can be some engineering reduction because the marshalling panel sizes are reduced or eliminated and field junction boxes are no longer used. However, those savings are often offset — even overwhelmed — by other factors.
[pullquote]
Fieldbus I/O hardware is significantly more expensive than a standard I/O card, and the final hardware cost is at best break even. On average, the control hardware of a single, non-redundant AS-i port costs about the same as the DI and DO cards associated with 20-25 on/off valves with two limit switches each. Some vendors make dual-port cards, others single. These values are on a per-port basis. If you install fewer than 20-25 valves per port, the AS-i hardware likely will cost more on a per-instrument basis. An AS-i card also requires a power supply and might require power conditioners and repeaters.
A single, non-redundant, non-IS Foundation fieldbus (FF) network card with power supply costs about the same as the analog input I/O associated with 15 transmitters or valves. Most segments will not carry that many devices, so the Foundation fieldbus hardware actually costs more than standard analog I/O hardware for the same number of points.
Price comparisons with Profibus-PA are more difficult because the cost of the segment depends on how the DP/PA couplers and DP communication cards are implemented. However, in a typical installation, the cost of a single, non-redundant, non-IS channel of Profibus-PA is about the same as the I/O cards associated with 5-10 valves or transmitters. This puts the cost of Profibus-PA hardware on par with standard analog I/O.
Fieldbus wire is much more expensive than regular 4-20 mA wire. Although theoretically almost any shielded pair can be used, the specific fieldbus wire will allow maximum network lengths with minimum communication problems. Prices vary, but fieldbus wire is typically 3-5 times more expensive. That price difference can jump significantly if it includes the cost of special connectors, whip cords, etc., which are required in most fieldbus installations.
Fieldbus field devices are almost always more expensive than traditional I/O devices. The differential is shrinking, but still exists. Lead times can be longer as well.
Foundation fieldbus and Profibus-PA can eliminate field junction boxes, but they often replace them with some kind of segment coupler or block that must be installed in the field to allow the local devices to connect to the network. These blocks are vital because they usually protect the network from shorts in individual transmitters. The total cost of these segment blocks as well as the fittings, terminators, etc., can approach or eclipse the cost of the original junction box.
Fieldbuses eliminate engineering associated with junction boxes and marshalling panels, and replace it with the engineering of the network itself. This cost can be very significant, since it often requires knowing — within a few feet — where the devices are located before the facility even exists. As the process design changes and equipment is relocated, the network design must be re-checked. A 4-20 mA wiring scheme is very forgiving. It doesn't matter if the cable is 10 ft or 1,000 ft, it still will work. Few fieldbus installations allow changes of that magnitude without a revisit to the design.
Fieldbus installations often require additional software and/or software licenses that are not required for standard I/O. These costs can be very significant, especially if they are priced on a per-tag basis. This additional software often is overlooked during the initial cost evaluation phase.
Be wary of savings calculators provided by automation vendors. These calculations can make unrealistic installation assumptions and use labor and material costs very different from those of your plant. Take the time to do your own calculations.
Reduced Commissioning Time?
Can fieldbus reduce instrument commissioning time dramatically, as many claim? Yes. It also can make a startup a complete nightmare. You just don't hear much about the nightmares.
A 4-20 mA installation is pretty easy to troubleshoot. If the transmitter doesn't work, you ring out the wires with a cheap multimeter, find the swapped or broken wire, and go on your way.
Troubleshooting a fieldbus installation is rarely so straightforward. Until recently, there were few devices that could aid the network diagnostic process and the team was reduced to disconnecting segments and shooting them with oscilloscopes and meters to detect and correct errors. Recent introductions of network analysis devices make this process easier, but at added cost.
The key determinant between success and failure rests heavily on the technical capabilities of the project design team. Don't assign your fieldbus project to a team that has no experience with the technology. The team must ruthlessly evaluate the field devices to ensure they work as advertised. Plug-and-play devices often fail to live up to their name. The team also must ensure the network design is complete and correct. This is no small task and might require multiple visits if device locations change during project design and/or construction. Another key success factor is the capability of the electrical contractor installing the equipment. The wiring and terminations are much more sensitive, and installation requires a knowledgeable technician. If not, network startup can be a very long, painful process.
Reduced Lifecycle Costs?
It's said that fieldbuses reduce lifecycle costs by speeding troubleshooting, and their advanced diagnostics eliminate work requests to fix instruments that aren't actually broken. This claim rarely is backed up with real numbers.
A fieldbus makes a tremendous amount of diagnostic data available to a knowledgeable user. But even the most knowledgeable technicians often lack access to the programming levels of the distributed control system (DCS) required to use the information. When a 4-20 mA device fails, a technician armed with a loop drawing and a multimeter can usually identify and resolve the problem quickly. If the transmitter is at fault, he can replace it with any transmitter of similar range and material of construction.
Consider that same scenario for a fieldbus transmitter. If the control system does not provide integrated, direct access to the device, the technician needs a laptop or specialized fieldbus communicator to access the device. If it requires replacement, he needs an exact replacement, then has to get the transmitter communicating on the network, and download the configuration file for it. If the transmitter software revision is not the same, the system might not recognize the transmitter at all and could require an updated device file to be downloaded to the DCS. If the problem is network-related, it will require a highly skilled technician with a network analyzer to troubleshoot and isolate the problem. The net result is that a failed fieldbus device requires an elevated or engineering skill set to do the work that originally could be done by a reasonably trained technician. This costs the plant time and money.
The ability of advanced diagnostics of a fieldbus device to eliminate many maintenance requests must be considered carefully. The failure rate of field instrumentation is very low. When a device provides bad readings, the problem is rarely hardware-related and is usually associated with wiring, process fouling, or plugged sensors. Advanced diagnostics usually won't detect this type of failure nor will it reduce its frequency.
Another lifecycle cost issue is that fieldbuses introduce obsolescence into the field devices. A 4-20 mA transmitter from 20 years ago will function perfectly on a 4-20 mA control system today. Fieldbus devices undergo constant technical upgrade and improvement, and existing instruments and spare parts might not operate on the latest control networks.
More Process Info, Better Alarms
You'll hear that fieldbus provides much more process information and alarm features. This is absolutely true. It also can be a double-edged sword.
Fieldbus devices can provide hundreds of pieces of information beyond the single process variable value of a 4-20 mA transmitter. The volume of data can be overwhelming, and it has minimal value unless presented to the right person in a timely and meaningful way. Production operators generally receive far too many alarms as it is. Burying them with more alarms every time an instrument thinks it detects a problem can be counterproductive. Suppressing the alarms and logging them to a file that never is monitored is equally pointless. It takes time and money to engineer the HMI to effectively take advantage of the additional information. Add the per-tag software licensing costs, and the total price can be significant. Is that additional information worth the cost?
A large percentage of existing field devices have HART communications and can provide a great deal of additional process and diagnostic information. However, few companies actually take advantage of that information even today.
Increased Uptime and Reliability
Depending on the system the fieldbus installation is compared against, improvements in uptime and reliability are achievable. If you compare a new, carefully designed fieldbus installation against an aging, poorly documented and poorly maintained control system, there can be little doubt the fieldbus installation will be more reliable. If you draw that same comparison against a new, carefully designed traditional I/O installation, the difference will be minimal.
There are a number of issues to consider; single point of failure is one of them. A 4-20 mA transmitter has a single pair of wires leading to a single I/O card. Wire failure likely will impact only one transmitter. Card failure could take out a single channel or at worst all the channels on that card.
Wire failure on a fieldbus might take out the device or it could take out all the network devices. Card failure likely will take out the entire segment (or two if it is dual-port). Power supply failure also will take out the segment. Redundant fieldbus cards and/or power supplies are available, but costly. Segments can be made smaller to reduce exposure, but at a much higher installed cost.
If a new 4-20 mA transmitter is being added, it almost always can be added without impacting production. If a new fieldbus transmitter is added, the network often will require a complete download. This takes the segment offline as the information is transferred. Some processes accommodate this easily. Other systems don't shut down for weeks, months, or even years. An outage in this case might be difficult, if not impossible.
Outstanding in the Field
A system with control in the field devices is touted to be better than control in the DCS because it provides higher uptime, faster control and better response.
The logic is not convincing. Improved control response is based on extremely fast processes run on a laboratory simulation. It ignores the real-world effects of actuator speed and saturation limits. It also compares field-device control response to the control response of a typical DCS/fieldbus installation. A true analog response would be much faster than any fieldbus — regardless of the location of the control — if it runs directly to a DCS and will be even faster with a dedicated analog loop controller.
Perhaps the most important omission is that field device control has an unknown failure mode. Historically, most analog instruments fail in a small number of ways: downscale, upscale or, very occasionally, mid-scale. Fieldbus instruments have a larger number of failure modes, but their advanced diagnostics generally can indicate this.
However, if control is performed in the field devices and the fieldbus communication card goes down, now we have field devices that might — or might not — be operating. They might continue to feed reaction materials to an out-of-control process reactor, and there is no way to know.
Consider that there is a reason very few people employ this technology.
In the next issue of Industrial Networking, I'll take us through a look at the advantages and disadvantages of specific fieldbus systems.
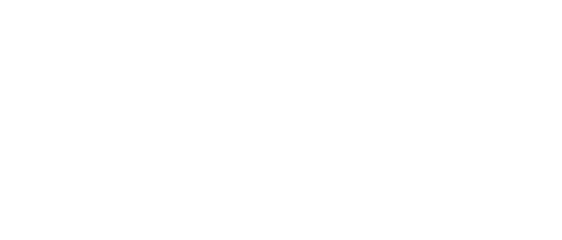
Leaders relevant to this article: