By Don Talend
As manufacturers aim to further increase the profitability of their operations and products, more demands are being placed on the motors that power their equipment. Efficiencies that enhance production speed as well as energy savings are top priorities.
Examples from plastic extruder and industrial compressor builders demonstrate how recent changes in motor design and their enclosures are meeting the demand for ever-higher efficiency.
The Move to AC
In recent years, John Clemens, manager of electrical engineering for Pawcatuck, Conn.-based Davis-Standard noticed that AC induction motors have increased in horsepower yet come down in price, making them much more competitive with DC motors. Davis-Standard is a diverse equipment manufacturer serving companies that make plastic sheeting, pipe, medical tubing and film in addition to rubber hoses and wire and cable (Figure 1).
CONVERTED BELIEVERS
Figure 1: Davis-Standard is converting from DC to AC motors in its machines.
Source: DAVIS-STANDARD
“Motor design has come a long way in reducing frame size, which has made AC motors much more applicable for higher-horsepower applications,” says Clemens, whose company is converting from DC to AC motors.
A competitive initial cost makes the choice a simple one for Clemens. “The price break used to be at 75–150 hp,” he adds. “If you went above that point, AC became very expensive. But over the past five to 10 years, that has changed and AC drive and motor combinations actually are the same price or lower than DC, even up to 500–600 hp.”
AC now offers a higher horsepower range at a price that is more competitive with DC. “Ten years ago, a 200-hp AC drive and motor might be $15,000, while 200-hp DC was $7,000,” continues Clemens. “Now, that 200 hp is about $7,000 on the AC side as well; that’s where they’ve really made a lot of progress.”
Extrusion is an application that requires a constant high torque and the AC motors with which Davis-Standard equips its extruders are well-suited to the task. “If everything’s set up right and the temperature profile is good, the extruder probably runs about 80% load because we typically oversize it to have that safety factor,” says Clemens. “And we do a lot of variable speed where we’re above 60 Hz.”
V*S Master from Baldor-Reliance is an inverter-duty AC motor that Davis-Standard uses for extruders that require less than 125 hp. According to Rich Schaefer, variable speed motor product manager with Dodge Reliance, the motor has a 1,000:1 torque ratio and standard 200% overload torque. The totally enclosed unit is particularly suited to the company’s PVC production, which uses wood flour that can potentially clog a motor, adds Clemens. This unit has a standard NEMA T-frame enclosure and doesn’t require a blower.
Above the 125-hp threshold, Davis-Standard specifies Baldor’s RPM AC motor, an even more robust inverter-duty unit, according to Schaefer. The standard overload torque is equivalent on the RPM AC unit and can be specified at 300% or 400% if necessary.
The Enclosureless Motor
According to Schaefer, a key feature of the RPM AC motor is a finned, square, laminated steel frame—the first finned frame configuration for an AC motor—designed to allow higher horsepower ratings in a smaller enclosure. The steel laminations that make up the stator are punched in a square shape instead of a round shape before the laminations are put in a press and bolted together. The result is an “enclosureless” motor that, unlike a motor with a cast-iron enclosure, does not trap heat and this design allows more horsepower in less area, points out Schaefer. This size economy, adds Clemens, allows Davis-Standard to fit the motors under its extruders.
The RPM AC motor is available in various ventilation configurations, including drip-proof forced ventilated (DPFV), which Davis-Standard mostly specifies. The DPFV configuration allows even smaller sizing of the motor enclosure. “When you force-ventilate the motor, that also allows the frame to be smaller,” notes Clemens. “By reducing the frame, you increase the mounting area around the extruder base, which allows you to mount other enclosures on that base.”
In March 2008, Dodge Reliance unveiled a new synchronous-rotor, permanent-magnet version of the RPM AC motor, which formerly had only an induction rotor, for more precise speed control with synchronous operation as opposed to slip-speed operation, says Schaefer. The salient pole permanent magnet version of the RPM AC that was unveiled has a rotor with protruding, salient, poles around which the windings are concentrated.
Schaefer points out that the new version of the motor will use neodymium-iron boron magnets designed to be an improvement in terms of resistance to demagnetization at high operating temperatures vs. the samarium cobalt magnets traditionally used in PM motors. More extensive mining of neodymium-iron boron magnets should close the price gap between PM motors that use these types of magnets and induction motors, claims Schaefer.
Cost-Reduction Emphasis
Energy savings is a major concern in industrial applications that require compressed air. Gavin Monn, president Americas for industrial compressor manufacturer CompAir, Piqua, Ohio, estimates that 70% of a compressor’s operating cost is devoted to electricity and fully 10% of energy consumed in manufacturing goes toward generating compressed air. CompAir provides compressors for industries and applications such as printing, automotive, medical, pharmaceutical, electronics, bulk handling and fabrication, many of which generate variable demand for compressed air.
The tricky task of matching rotary screw compressor demand output with actual system demand traditionally has been done with either modulation or load/unload controls, which aren’t very energy-efficient at part load, says Monn.
CompAir addressed this task with the SR (switched reluctance) Drive system from UK-based Emerson Motor Technologies division SR Drives, which is designed to operate the motor more efficiently across a wider speed range than a PM motor (Figure 2). It achieves this by generating torque via the magnetic attraction of a steel rotor to stator electromagnets. Mike Turner, SR Drives director of engineering, argues that this also is more efficient than the use of an inverter, which consumes significant energy by switching frequencies often.
EASY STREET
CompAir relies on switched reluctance to operate the motor more efficiently across a wider speed range than a PM motor.
Source: CompAir
The motor design also lends itself to energy efficiency. The motor is brushless and doesn’t use permanent magnets, a “squirrel cage” or windings. Turner points out that the SR motor actually was designed to be a variable-speed motor, in contrast to other motors that work with an inverter. He describes the motor as having the simplest design on the market with windings that don’t overlap, which makes them easier to wind and facilitates heat dissipation, and whose only moving parts are sealed, grease-lubricated ball bearings. “The motor works on the principle of magnetic attraction instead of repulsion, which gives it high-torque capabilities across its entire speed range along with a typical turndown capability of 15% of maximum speed,” says Turner, who also notes that, in lieu of permanent magnets, the motor uses insulated gate bi-polar transistors (IGBTs) that switch current through the windings that are coiled around laminated sheet steel poles designed to minimize eddy current losses. “Each pole is equipped with two IGBTs: one for the incoming power and one on the power leaving the windings,” says Turner. This design allows recovery of some of the power from the windings back into the capacitor bank, according to Monn.
Another important distinction of the SR Drive motor that Monn views as beneficial is that it runs on 650 Vdc. The drives convert the incoming AC power to DC and run the motor on the DC. “In contrast to variable-frequency drives that convert the power from AC to DC and then back to AC again and yield a roughly 1½% to 2% power loss each time, this system changes the power state only once, giving the system at least a 1½% to 2% advantage in energy efficiency,” he says.
REDUCED CONSUMPTION
If air demand drops to 50% of normal, CompAir’s compressor consumes only about 52% of its full load power.
Source: CompAir
Monn says the ability to control the speed of the motor in conjunction with compressed air demand allows CompAir customers to pay only for the amount of energy to produce the compressed air they need (Figure 3). For example, he argues, if air demand drops to 50% of normal, the compressor consumes only about 52% of its full load power. Modulation and load/unload controls on competitors’ compressors still consume about 85% of full load, allowing CompAir to provide its customers with a 30% energy savings, according to Monn.
Maintenance Advantages
Davis-Standard’s Clemens saw maintenance cost reduction as a major reason to get away from his DC motors and switch to the Baldor AC motors. “With the AC motor, you don’t have the maintenance issues of the old DC motors, replacing brushes and things like that. That’s really where the savings can be found,” he adds.
Monn’s experience has been similar. In addition to energy savings, he points out that the simple design of the SR Drives motor also provides the benefit of reduced maintenance compared with a typical PM motor. “The sealed grease-lubricated ball bearings do not require regreasing,” he says. “The first required maintenance is a bearing replacement at 32,000 hours of operation.” He also cites easier maintenance since the ball bearings are contained within bearing retainers. SR Drives also provides field replacement winding kits to replace the non-overlapping motor windings.
According to Monn, there is no peak current inrush during starting above and beyond normal full load amps, and this enhances the durability of the windings. “This operational aspect makes the windings operate at much-reduced temperatures and also allows starting and stopping of the motor as often as desired, compared with the normal AC motor start and stop limitations of six to 10 start-stops an hour,” he says.
Don Talend of Write Results, West Dundee, Ill, is a communications and publicity consultant specializing in the technical trade media.
Motor Mouth
Motor maintenance requirements are a big concern for users who need dependable machine uptime. Where’s energy consumption on your customers’ priority lists? Are they saying they want energy-efficient motors? Are they ready to pay the up-front premium? Comment at ControlDesign.com/motors.
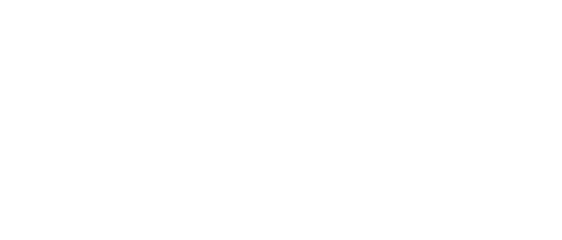
Leaders relevant to this article: