There typically are several motivations to use vision and robots for manufacturing. Labor savings, clearly, is one of them. While labor costs tend to stay the same or rise, they also recur every year. The cost of automation is declining and primarily is a one-time purchase. Because American manufacturing often is at a distinct disadvantage against overseas labor costs, typical ROI calculations for these labor-saving solutions are less than one year, while the length of a parts manufacturing program is typically five years.
Throughput is another issue. Manual operations often are upstream in a manufacturing line, so a manual operation that loads parts at the upstream station often controls the throughput of the line. This is amplified when the parts are large, sharp, or heavy. It may be that the line itself contains automation such as welding robots, but efficiency is controlled by the rate of entry of product into the line. Automating these throughput-controlling operation benefits the cost structure of the overall manufacturing operation. Manual operations also generate costly injuries, most of which could be avoided.
Vision Guided Robotic (VGR) solutions can solve these problems and provide more flexibility, allowing product changes to be handled with the same means for conveyance, e.g., racks, boxes, trays, conveyors, etc. When product changes are made, shutdown and a retooling aren’t required to manage new product geometries.
VGR Investigation
About a year ago, Dan Bickersteth, corporate manager for cycle time improvement and automation at Detroit-based American Axle and Manufacturing (AAM), took an assignment to champion his company's automation efforts. "We surveyed all our facilities and rank-ordered the automation opportunities," says Bickersteth. "Our objective was to establish a hit list that we could pursue that would maximize our capital resources allocated to automation."
During the same period, looking toward future needs, AAM selected robot partners and system integration partners. With the list in hand and the technical partners in place, Bickersteth set out to tackle the 2004 projects.
A machine vision initiative arose from of a need to reduce low-value-added work assignments such as axle shaft and pinion bin picking, pick/place operations, etc. "Our existing dunnage [parts container] does not provide any consistent part positioning," says Bickersteth. "However, I recognized that there are patterns to the unit loads."
In automated bin picking applications, products typically are randomly piled in the box or bin. (See sidebar below this story) This creates a challenge to find the parts, determine their orientation in 3-D space, and grasp them in spite of their varied resting positions.
Traditionally, these applications have offered the most promise for cost savings, but from a technical solution standpoint, have been the most elusive. However, with recent advances in machine vision technology, robotic end-effectors and 3-D calculation software, these solutions now are becoming more feasible.
Traditionally, both the axle shaft and the pinion picking operations were done manually. In the case of the axle shaft cell, AAM factory personnel handled an extremely large amount of material in a single shift. "We pursued this automation initiative not only for cost reduction, but also to eliminate an ergonomically demanding work assignment," says Bickersteth. "Automation also provides consistency. If the cycle time requirements are suitable for automation, we would see good results."
One of AAM's suppliers, Nachi Robotic Systems along with vision software solution developer Shafi Inc. suggested a VGR solution that might automate the manual bin-picking operation. Shafi specializes in turnkey solutions for vertical applications that involve robots and machine vision.
"Nachi is the first robot supplier to be involved with axle shaft and pinion picking operation at AAM," says Frank Seitz, of Nachi. "On this particular project, we supplied a six-axis robot that features a large working envelope and backward reach, a versatile feature that allows for quicker material handling."
The SH series robot selected is capable of handling payloads of 133-200 kg. "Our AX controller," adds Seitz, "is a high-performance, multitasking, PC-based controller. Programming is fast and flexible with additional options available through the teach pendant. It also features an internal manual/diagnostic function so that maintenance can be done remotely."
Build on What You Know
Automating the axle shaft and pinion bin picking operation is not AAM's first venture into applying machine vision. "We used machine vision in other areas, but with mixed results," says Bickersteth. "This was to be our first attempt with robot guidance, so I did my research. Shafi received very good feedback from its customers."
The only other outfit Bickersteth found that was pursuing these types of solutions was Braintech, a Vancouver, B.C.-based company "However, they are aligned with ABB, and it was our desire, in this case, to work with Fanuc, Motoman, and Nachi. The Shafi system's flexibility was proven when the axle shaft project was successfully integrated with both a Nachi SH133 robot and a Motoman HP165."
Shafi specified vision hardware and invited Cognex into the project. "The Shafi contribution to the project provides the "glue" that keeps vision and robots easy to use by providing enabling software that tightly integrates robots and vision," says Herb Wagner, Cognex's senior regional manager.
AAM provided Shafi with axle shafts and pinions to help them configure the system. Axle shafts are forged and then automatically packed into wire baskets at extreme temperatures at the forging facility. "Because of the conditions, there was no feasible solution to the packaging issue," says Bickersteth. "Or so it seemed."
Shafi started with an attempt at a single and multiple camera solutions. Bickersteth provided input as to how to structure the program to improve the success rate, for example, shrinking the search area, or establishing a recheck routine.
Next: Empty the Bin
After achieving some success with the machine vision system finding the parts in the container, they tackled the second problem: getting the parts out of the container. System integrator partner Auto/Con, Clinton Township, Mich., had previously worked with AAM making "significant contribution to our automation, manufacturing systems, and system integration needs," states Bickersteth. "For this project, Auto/Con developed an end-of-arm tool (EOAT) that integrated the camera and gripper into one unit. The tool was designed to provide a significant amount of compliance to maximize our success with removing the parts from the container."
As the integrator, Auto/Con, was tasked to make everything fit within the floor plan. Its other project tasks and responsibilities included the work envelope, capacity of the robot, the robot's EOAT--to manipulate the dunnage and parts--robot programming (excluding the vision system) and the wiring and piping of any pneumatic or electrical devices necessary for the system to operate.
"The Shafi-supplied and integrated vision system, with Shafi's own imaging program, was a critical element of the whole project," says Auto/Con Corp. president Ron Matheson. "Without a reliable vision system to make proper parts comparisons, the project would have failed."
With the gripper properly configured and the refined algorithm in place, the group achieved a successful solution.
Lessons Learned
"In addition to the technical problems solved by Auto/Con and Shafi," recalls Bickersteth, "we had to solve the equally difficult problem of convincing the 'customer.' To help them [plant operations and senior executive staff] understand the solution's scope, “we employed video and live demonstrations to successfully present the project."
Bickersteth believes there are three important points to take away this project. "First, machine vision provides the ability to solve previously 'unapproachable' technical problems. However," he argues, "vision cannot provide information that is absolute. Vision is not a silver bullet. We need to anticipate that it will not always hit the mark with absolute precision. The system must anticipate some degree of variation, but hard tooling is needed to account for anticipated variations."
That said, the second key point, says Bickersteth, is that he was fortunate to work with a competent integrator, able to design, deliver, and validate an EOAT that provided the second half of the solution.
"Third, the organization has to understand the assumptions associated with any project, especially those related to vision." Past vision-related projects," he continues, "were sold to senior management as 'bulletproof.' We knew that these types of projects might realize some nuisance faults."
These cells are being installed in areas where AAM has employees with enough available time to manage the automated material-handling systems with a minimum level of nuisance interruptions. "The benefits certainly outweigh the risks," he says, "but we had to identify, understand, and accept the risks before proceeding."
Training the operators isn't a big concern to AAM. "The Shafi system has very straightforward calibration routines," say Bickersteth. "We provide good training and on-floor signage to assist the operators. We also have onsite Fanuc and Nachi training cells that we use to instruct our operators."
Do What You Do Best
"Everyone has their own critical expertise in the project," reminds Matheson. "Usually, when a vision system fails, it's because the integrator couldn't figure out a way to compensate when the vision failed. When we began the axle shaft picking operation, Shafi rigged up a gripper that failed to work properly because the vision system had a hard time with depth judgement. In response, we made a gripper module that would compensate for that error and the bin picking was off and running."
Clearly, it's worked well. "VGR is no longer just a lab project," says Cognex's Wagner. "Done correctly, VGR provides manufacturers with the ability to meet their objectives for lower-cost, more flexible, reusable automation."
"But keep in mind," says Wagner, initially it's a cost consideration to put in vision-guided robotics. "In most manufacturing companies, labor is considered a fixed cost, while a vision-guided robotic system would generally be considered a capital expenditure."
AAM began installation of pinion-picking cell and expects to be online during February 2005. It also is in the capital-appropriation phase of pursuing its first axle-shaft cell installation.
The positions of the shafts are not repeatable and the bins that they are transported in are typically old, rusted and deformed. The shaft surface reflectivity characteristics. vary, and beyond the circular flange, there is no significant geometry to work with. When the shafts lie in a bin, the bin’s metal frame is also visible. A 2-D view of the parts reveals lines representing the shafts with no 3-D depth information. A robot gripper cannot go down straight down vertically when the parts are near the outer walls of the bin. An angled path approach must be considered.
Differential carriers are essentially half-spherical domes with a narrow metal spiked end. They are typically arranged in a 'bowl' upside down configuration or a 'cap' right-side-up configuration. An unpredictable pitch-roll tilt to these two resting configurations is an element of the problem to be solved. These parts arrange themselves on top of each other such that the overall stack configuration and the angle of the spiked end is highly variant. All of which makes it impossible to assign any repeatable characteristics to the position, height, or orientation of the bowls and caps. A 2-D view of the parts reveals a jumble of touching and partially overlapping parts.
These two types of parts have traditionally been handled manually by operators. They are lifted slowly with ergo-assist arms (to help overcome their weight), by manual operators who are careful by being slow, and who lift these objects out of bins and place them onto the most upstream position of American Axle's manufacturing lines.
Adil Shafi is president of Shafi Inc., a software solutions value-added custom software integrator of flexible factory automation. Learn more about the company at www.shafiinc.com.
Sponsored Recommendations
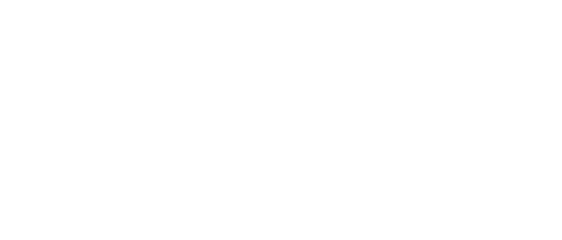
Leaders relevant to this article: