Paul Studebaker is chief editor of Sustainable Plant. He earned a master's degree in metallurgical engineering and gathered 12 years experience in manufacturing before becoming an award-winning writer and editor for publications including Control and Plant Services.
The University of Texas at Austin generates 100% of its electric power, steam and cooling for more than 150 buildings comprising 20 million square feet. Electricity, chilled water, steam, condensate recovery, water and sewer lines all run underground in truly redundant loop configurations through a network of tunnels throughout the campus. The university's 135 MW of combined heat and power operates with 88% fuel efficiency at 99.9998% reliability.
But it hasn't always been this way. "17 years ago, we were operating at 62% efficiency," said Juan Ontiveros, P.E., executive director of utilities and energy management for the university, speaking at the Power and Energy Management Industry Forum this week at the Automation Fair in Houston, presented by Rockwell Automation. The Austin campus and its power systems had grown organically since 1929. "Our controls were all pneumatic, and we were at capacity. We had to upgrade, but we couldn't shut down."
SEE ALSO: Two Avenues to Machine Efficiency and Sustainability
To add to the challenge, his department's budget left little room for investments. Money for improvements would have to be saved from operating costs by improving operational efficiencies and allowing staff to reduce by attrition. So they implemented digital controls in stages, starting with the boilers and power turbines. "We improved the maintenance process, standardized our systems and got a new Title V permit," Ontiveros said. The information provided by the new controls showed that the average efficiency was 62%, but some of the equipment was running at 80%. "Why don't all of them run at 80%?" he asked. "That became our first efficiency target."
The quest for efficiency gradually lead to new equipment, including a steam load controller, a load-shedding system for the electrical generator, and a modern tie-in controller to the grid. But major improvements came as the department was able to digitize the balance of plant (BOP) for remote monitoring and control. "BOP is very important when something goes wrong, so you can see it right away," Ontiveros said.
The department transitioned to Allen-Bradley PLCs for all BOP applications because of local support and their reliability in high-temperature and high-vibration environments. Standardizing made it easier to implement incremental improvements as funds become available. The latest major accomplishment was implementing a 100-MVA substation and an all-new power plant electrical system "without shutting down," Ontiveros said. "We did it all live."
The digital system supports optimization of the chilled water system, real-time power dispatch and, with new burner management systems, 100:1 turndown on the turbines and boilers. "We do all the tricks in terms of efficiency," Ontiveros said.
The systems' controls must have redundancy, independent process checks (to verify status of critical processes), the ability to gather and process data reliably even during work, and security. "We must be able to manage them in-house," Ontiveros said, "And they must have OPC."
"In combined heat and power applications, fuel efficiency is about 90%." FuelCell Energy's Ben Toby on the high efficiency and improving affordability of high-temperature fuel cells for power generation applications.
Since its peak about 17 years ago, fuel usage has dropped to 1976 levels despite more than doubling of the square footage. Energy savings like that don't happen by accident. "You have to take some risks," Ontiveros said. "It's easier to do nothing, but then you get nothing." Asked if he was able to invest some of that fuel savings in efficiency improvements, Ontiveros said, "The money we save on energy is outside our budget." All he gets for that is an annual, "Thank you very much." That's apparently enough.
Tyson Targets Energy Use
Tyson Foods is just getting started on a systematic approach to energy management. For the company that produces "one in five of every pound of protein in the United States," said Danny Hamilton, director, energy engineering, Tyson Foods, "Energy has started to become a definitive factor in the success of our operations."
The company has set the goal of 20% reduction in energy ― $84 million annually — over 10 years. Based on historical energy audits, it expects 10% to come from low-cost operational efficiencies and 10% from capital-based improvements.
{pb}
To find those opportunities, Tyson started at a single plant with a pilot implementation of a Rockwell Automation Industrial GreenPrint energy monitoring system and energy services. "We can't afford to monitor every possibility," Hamilton said, so Tyson selected the five major systems that, according to audits, consume 80% of the plant's energy: compressed air, cooking, refrigeration, steam and tempered water. Projects were limited to those that would pay back in less than two years.
All the information from the five systems was integrated with GreenPrint to feed its dashboards, and standards were established for each system based on production rates and historical information. Dashboard displays are coded green/yellow/red so anyone can see immediately how well they're doing, and can drill down as needed for real-time process information. "Very quickly, we are able to tell how we are operating against our standards."
Variance reports give details on cost, production and energy intensity, so "Unit operations managers know how much it's costing them to not perform," Hamilton said. "How much I consume is important, but I want to know how much I should be consuming."
The pilot identified major pain points in the compressed air and steam systems with paybacks of less than 12 months that reduced utility costs $300,000 per year. The system is going live at a second plant in December of this year, and Tyson is developing an enterprise-wide rollout.
Hamilton said energy managers need to clearly define their process and objectives, and to implement a continuous improvement process with continuous monitoring, real-time dashboards, feedback and opportunity tracking. He also said they should plan on some capital investment to get started: "We budgeted 20% of the annual energy spend to get this implementation."
Fuel Cells Becoming More Competitive
Another potential way to save energy while providing electricity and process or district heat is to install a commercial-scale fuel cell power plant, said Ben Toby, vice president, FuelCell Energy, Inc. High-temperature fuel cells have been used in commercial applications since 2003, and his company has installed more than 120 MW in commercial and industrial facilities around the world. "High-temperature cells run on natural or biogas at 1600 ⁰F, which allows reforming of methane and high efficiencies with lower CO2 emissions. In combined heat and power applications, fuel efficiency is about 90%."
The power plants aren't for everyone. They cost $7 to $12 million, so they generally must be financed by power purchase agreements (PPAs). Installed costs run 14 to 15 cents per kilowatt-hour with natural gas prices at $6 to $8/mmbtu, which makes them generally only attractive in states with high electricity costs and significant subsidies for using fuel cells.
Toby expects prices to fall to about 10 cents per kilowatt-hour as production volumes rise but even now, his company is finding takers among hospitals and companies such as Gill's Onions, which uses biogas from onion waste to feed fuel cells that provide a significant portion of the company's electrical power requirement. The fuel cells also can serve as back-up generators to sustain operations in the event of a grid outage.
The Power & Energy Management Forum also included a presentation on regulatory issues facing power- and energy-intensive industries by Diane Fischer, air quality control services leader, Black & Veatch, reported in yesterday's newsletter.
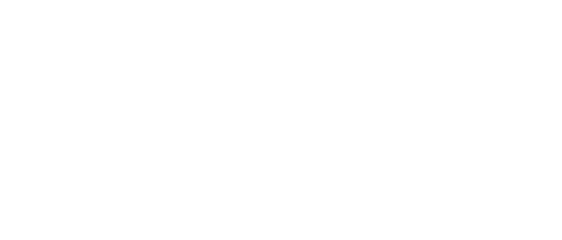
Leaders relevant to this article: