After working as a semiconductor process engineer, Hank Hogan hung up his cleanroom suit and now writes about process control and other technologies from Austin.
To be sure you hit a target, you have to see or somehow sense it. That truth lies behind the theory and practice of presence sensors, which are used to determine whether a box, bottle, piece of metal, or something else is there or not. Armed with that knowledge, a machine can then send a package where needed, shape a piece of metal as desired or take other action.
Sometimes this function is referred to as proximity sensing or object detection. "Typically what they mean by that is on-off type of sensors, sensors that turn on when a target is present and turn off when a target is removed," says Craig Brockman, marketing manager of presence sensing for Rockwell Automation.
The oldest type of presence sensing is a limit switch. If contact with an object is OK, then a limit switch can be an acceptable solution, explains Brockman. Advantages are low cost and simple operation, thanks to rocker arms that move to open or close a circuit. But limit switches are mechanical devices. Hence, they're prone to wear and misalignment, which can mean more maintenance.
What's more, a limit switch requires contact. This can be a no-no, since mechanical contact can mar a surface and make some sort of cleanup or post-processing necessary. For that reason, limit switches are not typically used for finished products, says Brockman. And there's been a general movement away from limit switch presence sensing, he adds.
Also Read: Presence Sensing: The Basics
Other approaches exploit noncontact techniques, using light, sound or changes in magnetic fields to pick up the presence or absence of an object. All of these techniques have the advantage of not touching the surface of the target, and so they can be used on finished and unfinished products alike. They also don't depend upon mechanical motion and so can be the basis for long-lived presence sensor.
In evaluating which of the different approaches is best, a key factor is the nature of the target. If it contains a ferrous metal, then an inductive presence sensor can work. In this method, a target entering a magnetic-field changes it, resulting in detection.
In contrast, a capacitive presence sensor can pick up a change in the electric field caused by any nearby object. It works in the same way some touchscreens detect when a finger is nearby but not in actual contact. In capacitive presence sensing, the target can be anything and doesn't have to be metallic.
Inductive sensors are inexpensive and widely used. They share a characteristic with capacitive sensors, one that helps determine whether or not they're suitable.
"How far away is the target from the sensor face?" asks Brockman. "If that's a relatively short range, less than 50 mm, then everything is still on the table. If it's longer than 50 mm, you can basically take off inductive or capacitive from that list."
For ranges beyond that, say from 2 cm out to 50 m, presence sensing comes down to light and sound. Both types of sensors generate a beam that interacts with an object in ways that can be detected, either by the beam being blocked or reflected back. Which type of presence sensor is best for a particular situation is determined by the target's attributes and such factors as its rate of movement.
Transparent liquids present problems for light-based presence sensors, since the probing beam easily travels through them. With little light absorbed or reflected, there's almost no change in the signal between the liquid being present or absent. Hence, for liquids, ultrasonic presence sensors that use high-frequency sound may be the best choice, although there are tube-mounted liquid-level-detection fiberoptic sensors, says Kristen Chonowski, product marketing manager at Omron Automation and Safety.
As for light-based presence sensors, they come in a variety of configurations, she adds. For instance, the light can arrive at and depart from the sensing area via fiberoptics. This offers the advantage of making the sensor head remote, thereby reducing the size of the presence sensor and potentially making it more robust in the face of harsh environmental conditions.
Another basic configuration choice has to do with location of the emitter and receiver with respect to the target. Light-based presence sensors can be through-beam, retro-reflective or diffuse. In the first and second cases, an object is present when a beam is broken, with a through-beam approach having the emitter on one side of the target and the detector on the other. In a retro-reflector, a reflector sends the beam back to the detector, which sits on the same side of the object as the emitter.
In contrast, a diffuse presence sensor detects the light coming back from the target itself. Consequently, this approach can be impacted by the orientation of the object, its speed of travel, and surface differences, with the latter a characteristic that can be exploited.
"Sometimes the difference between something being right-side-up or upside-down could be its color shade," says Chonowski. "If one side is much darker than the other, then, rather than recommending a color sensor, a standard diffuse reflective photo eye can be used."
Light-based techniques can work over long ranges, offering detection of objects that are meters or tens of meters away. Key to achieving the longest possible distance is the brightness of the source, with a more intense source yielding reliable presence sensing of more remote objects. That reach comes at a price, however.
"Lasers will give you the longer range, but they usually don't have the temperature range that LED versions have," says Tom Corbett, product manager of photoelectric sensing at Pepperl+Fuchs.
He adds that, no matter the light source, in general diffuse sensors have the most limited reach, with retro-reflectors offering more range. Through-beam techniques offer the longest range.
It's not only the source but also the environment that determines the range, particularly over time. Corbett notes that accumulating dust and dirt will diminish a light-based signal, with one possible eventual result being that the difference washes out between a target being present or not. Such a drop in the signal can be detected and the sensors then cleaned. If this happens too often or such routine maintenance is too difficult due to where the object detector is mounted on a machine, then a light-based presence sensor might not be the right choice. In these circumstances, an ultrasonic or inductive technique may be the answer.
Beyond the target and environment, it's vital to remember that a presence sensor is not there simply to detect an object. It also has to fit within whatever space is available and notify the larger system, a requirement that determines the final aspects of the configuration. Examples of what must be considered could involve how the presence sensor is wired, which could be to a PLC or to trigger a solenoid.
Summing up this aspect of a presence sensor, Corbett asks, "How is it going to interface with the rest of the machine?"
Sponsored Recommendations
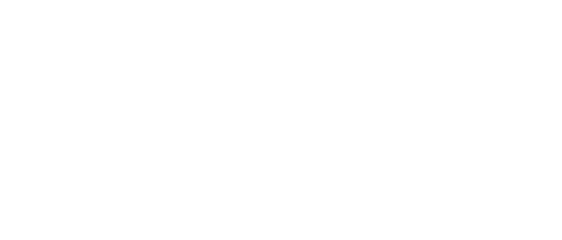
Leaders relevant to this article: