Simplify press maintenance and management through IIoT innovation
Four years ago, I joined Flodraulic, the controls contractor for Eagle Press & Equipment in Ontario. The organizations’ combined team wasn’t looking for a shift in press control architecture. Machines were working; warranty issues were resolved; and press customers were happy.
Flodraulic has extensive experience in the press industry, as well as in the steel, packaging, machine tool and chemical industries, designing and manufacturing fluid power systems combined with electronic control packages.
Figure 1: In the crown junction box, the Eagle Press and Flodraulic team was able to go from one to two days to build and wire the controls to only a few hours with significantly reduced troubleshooting.
Eagle Press & Equipment, located near Windsor, Ontario, is a manufacturer of industrial presses and stamping equipment. Since 1959, Eagle Press has been committed to extraordinary engineering, visionary design and standard-setting innovation. With constantly updated and inspired new technologies and products, Eagle Press is leading the charge in precision forming equipment. Eagle's product lines supply the automotive, appliance, aerospace, agricultural, HVAC, construction, mold, tool & die, acoustical material forming and insulating industries.
Figure 2: Incremental improvements in the crown junction box included adding junction blocks to reduce the number of cable passthrough holes in the box.
Figure 3: The hydraulic power unit control box located in the press pit utilized many cable passthroughs, field wirable connectors and complex terminal wiring practices.
Now that I’m controls technician at Eagle Press, I saw room for improvement in the press control architecture. Each junction box would take from a half-day to a day to build in the panel shop and then a half-day or more to wire and construct (Figure 1)."In the past, we had to wire every terminal in the junction box and had many sensor cable passthroughs," agrees Andy Ritchie, project manager at Eagle Press (Figure 2). Each press had four major junction boxes around the machine: at the operator station, up in the crown, on the ram and down in the pit with the hydraulic power unit (Figure 3).
In addition, every sensor cable was built custom with field-wirable connectors adding extra costs and increasing the probability of wiring errors in the build phase or failure in use for the end customer. For Eagle Press and Flodraulic, there were significant challenges from the junction boxes that had to be built to house the I/O. Terminal blocks, slice I/O, mounting, wiring, labeling and testing of each junction box added extra costs and troubleshooting time for wiring errors or loose wire connections. This increased commissioning time, decreased productivity time or both (Figure 4). All of these issues translated to increased operating costs to both the press builder and customers purchasing the press.
Figure 4: IO-Link slave I/O hubs were utilized in many places, such as the lubrication system, eliminating small junction boxes and reducing the time needed to commission or troubleshoot.
Figure 5: A linear position sensor utilizing IO-Link is used for position feedback to adjust the ram for shut height. A magnet travels along the sensor generating the position data which is communicated via IO-Link as thousands of an inch.
In addition to many inductive proximity sensors, Eagle used a number of measurement devices with analog signals to control and monitor pressure, flow, temperature and linear position on the press (Figure 5). "Measuring values like temperature on the bearings and bushings is important so we can predict a problem before it damages the press," says Ritchie (Figure 6). The traditional difficulties with analog signals were not foreign to the technicians and engineers at Eagle Press and Flodraulic, so special attention had to be paid to these parts of the control system to keep noise issues from interfering with the press performance.The team began looking for an I/O control solution that would:
-
reduce noise-related issues
-
allow full integration into the existing control architecture using EtherNet/IP
-
allow full integration into any future control architectures as directed by the market, such as Profinet, EtherCAT and CC-Link IE Field as examples
-
address and reduce the challenges coming from wiring and junction box construction
-
provide the customer with a simplified system for troubleshooting and fewer connection point failures to reduce downtime, increase productivity and improve overall equipment effectiveness (OEE).
The team committed to embrace new products and technologies to further the value of each new press and to continue researching incremental improvements on the presses. For many years, Eagle Press and Flodraulic based successful press control architecture on the utilization of IP20 slice I/O over EtherNet/IP in the junction boxes. At first, the team stayed with panel-mounted I/O in the junction boxes.
Figure 6: In the crown, IO-Link-capable temperature sensors (RTDs) monitor the status of the clutch oil, bearings and bushings temperatures. The data is communicated over a standard sensor cable and eliminates noise and wiring issues of traditional analog measurement.
We removed all of the holes in the panels with hardwired junction blocks mounted on the side of the cabinet. This way we had only a few passthroughs. But we realized it didn’t make sense to have these blocks on the panel, so we moved them out onto the press. The positive evolution of wiring solutions from individual wires to distributed junction blocks still had some of the limitations of the original design with direct wiring having many problems and requiring a decent amount of troubleshooting work.
Greg Heyd, control systems designer at Flodraulic, and I then proposed a new incremental control improvement to Ritchie, called IO-Link. "It was a big change for us in design, so we had to find the right project," says Ritchie. But the value that could come from reducing wiring time and simplifying troubleshooting was of interest to the team. IO-Link is an open standard supported by more than 120 component manufacturers to provide automation technology that is as easy to use in a factory as USB is easy to use with the PC. IO-Link was created to provide a simple platform for smart sensors to communicate with an automation controller. Not only does the sensor report its measurement or switching data but it can also communicate diagnostics and parameters.
Working in a point-to-point master/slave architecture similar to USB, a pressure sensor's parameters can be stored and re-downloaded upon replacement or configuration change. This makes the service and maintenance of the press dramatically easier for Eagle's customers, says Ritchie, "With IO-Link, if we get a service or warranty call, it is much easier to fix a cable or device on the press to get the machine running again," he says. Regarding the value of parameter storage, the press can even tell the customer if the wrong part number was installed.
With a wide variety of technologies available with IO-Link, Eagle Press was able to seamlessly integrate a multi-vendor solution that fits its needs and requirements. IO-Link pressure, level and temperature sensors are used in a wide variety of applications on the press—for example in the lube, clutch and bolster control to monitor hydraulic fluid level, pressure and temperature.
Additional sensors were used to provide scrap chute door control, counter balance control and hydraulic overload control. Shut height is precisely measured using an IO-Link linear position sensor from Balluff, which reports measurement values in its respective engineering units—thousandths of millimeters—over IO-Link with no need to calculate resolutions or scaling. "We were able to virtually eliminate analog on the machine by implementing IO-Link," says Ritchie.
Traditional I/O devices such as panel-mount motor starters and machine-mount I/O provided additional value in the electrical wiring of the machine (Figure 7). The motor starters are monitored and controlled by IO-Link. But we found an additional benefit in moving to IO-Link motor starters. We were able to eliminate more than half of the wiring of a traditional contactor and gain diagnostic information.
Figure 7: With EtherNet/IP IO-Link masters and IO-Link slave I/O hubs, Eagle was able to completely eliminate the junction box in the pit. In addition, it was able to improve troubleshooting with machine-mount I/O and smart-sensor diagnostics.
With machine-mount I/O from Balluff, “we've been able to eliminate a box on the crown, the ram box and the lube box in the pit," says Ritchie. And with the I/O hubs, we were able to get rid of fusing and breakers on the machine with the built-in short protection.
By utilizing IO-Link, Eagle has created significant improvements in maintenance for its end customers. Replacing a worn-out or damaged part is easy now with IO-Link automatically parameterizing the sensors. Pull it out of the box, bolt it on, connect it and its working. This is made possible with the Balluff IO-Link master's automatic parameter download feature ensuring error free re-calibration. This provides value to the customer maintenance team by reducing complexity of device setup and reducing downtime with hot-swapping of failed devices. Troubleshooting is made more effective with diagnostic visibility down to the individual I/O point.
This comes from a combination of machine-mount I/O providing easy-to-use diagnostics and dramatically reduced wiring on a scale greater than 60%. Troubleshooting in a traditional control architecture on the press has its challenges, emphasizes Ritchie. “Moving to IO-Link and eliminating the electrical cabinet in the ram was valuable,” he says (Figure 8). “There is oil everywhere. It's dripping down on you, and it is always difficult to troubleshoot in that space. Now, customers have to get up on a ladder much less frequently."
Figure 8: Moving to IO-Link and eliminating the electrical cabinet in the ram was valuable. There is oil everywhere, dripping down, and it can be difficult to troubleshoot in the space.
Production management can be improved by utilizing the diagnostics and data provided by the EtherNet/IP IO-Link masters and IO-Link slave devices (Figure 9). The machine can now report causes of downtime, part counts, idle time and which operator was on the machine for operator accountability.
Figure 9: By utilizing EtherNet/IP IO-Link masters in lieu of the crown junction box, troubleshooting and wiring become easier to work with. Bright LEDs, smart-sensor diagnostics and individual-port short-circuit protection make problem-solving take only a few minutes.
Figure 10: More than two dozen presses have been built and installed in North America with an IO-Link control architecture from Eagle Press and Flodraulic.
"More customers are looking for information from the equipment, such as analytics, Industry 4.0 and Industrial Internet of Things (IIoT) capabilities," says Mike Hebert, sales manager at Eagle Press. Even critical data, such as OEE and downtime, can now be reported easily from the press over Ethernet.Since the implementation of IO-Link for press control at Eagle, more than two dozen presses have been built and installed throughout North America (Figure 10). IO-Link cleaned up the look and created a consistent design of our machine. The IO-Link solution helped our machine be very modular for engineering, build, teardown and re-commissioning. "Since the presses have moved to the Balluff IO-Link solution, this change in architecture has resulted in a significant reduction in related field-service calls,” says Hebert.
IO-Link clearly provides a dramatic positive effect for manufacturers looking to increase production volumes and reduce downtime.
ALSO READ: Does distributed I/O architecture make sense?
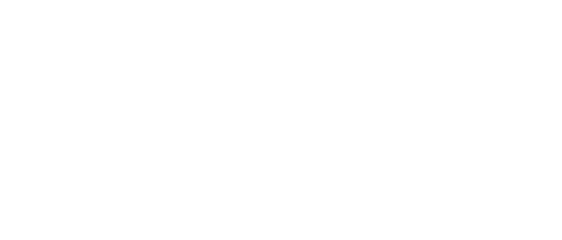
Leaders relevant to this article: