Warehouse and distribution-center automation requires dynamic solutions to accept, store and retrieve a wide variety of materials and products. As a leading producer of automated guided vehicles (AGVs), John Bean Technologies (JBT) understands that the fast pace of intralogistics requires highly adaptable technologies. “Our AGVs need to account for a certain level of unpredictability and reliably complete successful missions with the fewest manual touches possible,” says Vijay Chhabria, R&D manager at JBT. “Everything from the robustness of our design down to the individual components is crucial to ensure our AGVs function at the highest level despite challenging environmental factors. As a result, our product development is a constant evolution.”
JBT tailors AGVs to specific customer requirements using a flexible automation platform built on PC-based control. The broad AGV portfolio has several standard and custom vehicles, such as towing, unit load and forked AGVs, as well as the entry-level JayBoT line. The vehicles, which essentially function as mobile robots, are geared toward payloads from 2,000 to 10,000 lb (Figure 1).
Figure 1: JBT builds custom AGVs, typically to move pallets in the 2,000-to-10,000-lb range, for customers across industries. (Source: JBT)
They serve multiple vertical markets, including automotive, food and beverage, fast-moving consumer goods (FMCG), paper, hospitals, manufacturing and distribution. The company designs, manufactures, tests and services sophisticated systems for wide-ranging customers, and a culture of innovation is pervasive throughout all JBT divisions. With a global headquarters in Chicago, JBT is also a solutions provider to high-value segments of the food processing and air transportation industries.
One recent AGV evolution is the integration of 2D/3D camera technology by the automated systems team in Chalfont, Pennsylvania. This upgrade automates the identification of pallet fork pockets, product on pallets and space availability in racking at any height. This enables more efficient storage and retrieval processes, according to Mark Longacre, applications engineering manager at JBT. “Previous methods of doing this, such as with point lasers, were slow and cumbersome. This makes processes quicker and more reliable,” he says. “The cameras can even see through a certain amount of stretch wrap material to identify fork pockets, unlike a point laser, which would likely register the shrink wrap as a broken bottom board or object blocking the opening. The camera technology offers greater transparency, so the AGV successfully picks pallets a higher percentage of the time.”
Off-the-shelf components answer specific requirements
In addition to vehicle hardware, software capabilities are undergoing a transformation at JBT. The company’s AGV fleet management software, SGV Manager, maintains constant communication with ERP and other higher-level systems to optimize material movements and adjust priorities. Even the 2D/3D camera technology uses advanced algorithms to detect the pallet opening as well as the rack space volume or box packing volume. “The 3D camera is mounted on a drop-down actuator on the vehicle so that it can look for and verify the available volume,” Chhabria explains. These software capabilities are crucial for taking on the most demanding material handling tasks, such as storing and retrieving pallets up to 400 inches high in a 50,000-pallet-position warehouse.
By handling all automation logic in software, PC-based control has been a key design principle for JBT for years. About a decade ago, however, the company’s legacy machine controller, a CPU developed in-house by JBT engineers, became less able to keep up with the computational demands of constant AGV evolution. Developing proprietary hardware rather than buying it was common in the early days of AGVs out of necessity, according to Longacre. “JBT has been in the business since the early 1980s, and even 20 years ago, we made many components that we don’t now,” he says. “As AGVs become more mainstream, we can buy great components off the shelf more often.” When exploring different automation components, JBT engineers knew they needed a PC-based option that offered both a Windows environment and real-time control capabilities. Any new control platform would also need flexible programming options, including C++ in particular.
Automation without limits using PC-based control
After evaluating a number of solutions, the JBT team concluded in 2011 that Beckhoff Automation offered the most flexible, robust platform. TwinCAT automation software heavily influenced this decision, according to Chhabria. Integrated into Microsoft Visual Studio, TwinCAT 3 enables programming on standard PCs or even in the cloud via a web browser using the object-oriented extensions of IEC 61131-3, computer science languages, built-in function blocks and other options in the graphical editor. “TwinCAT allows us to run deterministic code at the required cycle times and supports C++ libraries. This is mandatory, since C++ is our main programming language. TwinCAT helps us sort out the user interface portion of the code,” he says. The real-time capabilities of TwinCAT were instrumental for reliable vehicle operation, especially in bustling warehouse environments. The software enables rapid decision making based on inputs from the 2D/3D cameras or commands sent from SGV Manager over Wi-Fi.
Figure 2: Beckhoff Embedded PCs provide scalable control hardware in multiple core levels for a variety of JBT vehicles. (Source: Beckhoff Automation)
PC-based machine controllers from Beckhoff are deployed for AGV control in the field (Figure 2). The standard controller for JBT AGVs is the DIN rail-mounted CX5130, which offers multi-core Intel Atom E3827 processors and 4 GB DDR3 RAM. For vehicles with more compact enclosure sizes, CP6706 “economy” Panel PCs conveniently combine a 7-inch touchscreen and a 3.5-inch motherboard with Intel Atom processors up to four cores for control and HMI (Figure 3). Most importantly, these solutions are scalable, adds Chhabria: “The Beckhoff CPUs are available in multiple performance levels and numbers of cores. If a complex application requires more processing power, we can replace the vehicle controller with another Beckhoff controller that will run the same TwinCAT software and Windows OS, so we know our application will be fully compatible.”
Figure 3: CP6706 Panel PCs combine HMI and vehicle controller capabilities in a compact form factor for AGVs with small enclosures. (Source: Beckhoff Automation)
A key factor in the transition to Beckhoff was the EtherCAT industrial Ethernet system. As the fastest fieldbus available, EtherCAT provides the data throughput necessary for real-time, deterministic networking and control. JBT uses a variety of EL series EtherCAT Terminals from Beckhoff. These I/O modules boast numerous off-the-shelf options, including 16-channel high-density form factors, integrated functional safety via TwinSAFE and, specifically, EL2522 Incremental Encoder Simulation terminals. The open EtherCAT system provides various gateways to communicate via CANopen, DeviceNet, EtherNet/IP or serial interfaces to specific components on the AGVs, such as navigation controllers, battery management systems or the 2D/3D cameras.
EtherCAT accelerates AGV evolution
The flexible, scalable Beckhoff platform has enabled continued evolution and customization of JBT AGVs. In addition, it has simplified engineering effort through the universal TwinCAT programming environment and the openness of EtherCAT (Figure 4). These advantages proved important when implementing the new camera technology. “EtherCAT establishes the 3D camera interface to the Beckhoff controller, usually using Ethernet over EtherCAT (EoE) and communicating via the TCP/IP protocol,” Chhabria says. “We can easily take a 3D image of any pallet and apply an algorithm to detect the pallet opening. Through fast, reliable communication, the Beckhoff controller receives the data and uses our algorithms for processing. The CPU then sends feedback to the actuators to properly pick up pallets and to correct for any irregularities in the pallet design or warehouse environment.”
Figure 4: Flexible PC-based control and EtherCAT technologies help JBT to continue evolving its AGV systems. (Source: JBT)
Since JBT transitioned to off-the-shelf Industrial PCs from Beckhoff in 2011, the company has built more than 2,000 AGVs based on the new platform with great success (Figure 5). This amounts to roughly 40% of all AGVs that JBT has made throughout four decades in business. “We consider Beckhoff technology to be very reliable compared to the alternatives. In addition, Beckhoff offers a solid support structure in North America, which helps us to support our own customers,” Longacre says. “We have the largest group of AGV experts in the world, and we serve the most demanding AGV applications. Beckhoff has proven to be a trusted and valued supplier, helping us deliver on our commitment to supply world-class AGV systems.”
Figure 5: JBT has built more than 2,000 AGVs based on the new platform with great success. (Source: JBT)
Joshua Douglas serves as marketing coordinator for John Bean Technologies. Contact him at [email protected].
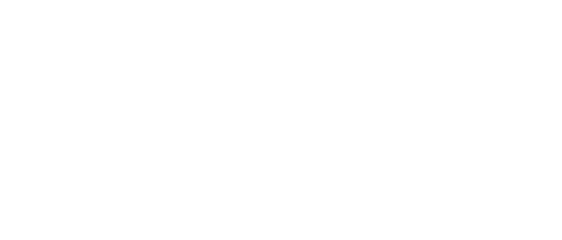
Leaders relevant to this article: