Busy warehouses and manufacturing facilities coupled with lingering labor shortages and supply-chain delays have resulted in the explosion of at least one major technical innovation—autonomous mobile robots (AMRs).
While earlier means of automating material-transport tasks have required infrastructure additions incapable of being moved without adjustments, AMRs can move freely yet safely on their own, transporting materials from one location to another with built-in sensors and 3D cameras ensuring they can stop or maneuver around anyone or anything in their paths.
As a result, it’s no surprise that the AMR market is growing at such a rapid pace. Recent statistics from ABI Research show global shipments seeing a 40% annual growth rate with global shipments expected to exceed 500,000 by 2030.
Many of those deploying these AMRs are still testing individual units, while others have already implemented dozens or even hundreds across their facilities worldwide, with an eye on cost savings, improved safety, better utilized employees and increased efficiency.
For those that haven’t yet jumped on the AMR bandwagon, not knowing how to get started and the fear of high costs and disruptions to their workflows are often sticking points. Follow these key points for a successful AMR deployment.
Start now
Engage with the right internal and external team for guidance. If you have seen the success other companies have had with AMRs and are considering deploying one or more for your facility, stop thinking about it and get started. The entire process is usually easier and faster than most think, with full integration often complete within weeks.
All facilities have different levels of internal expertise and resources to handle automation projects, so determine your knowledge level and appoint an internal champion to help lead the project along and help make employees comfortable with your automation strategy.
Start by working as a team to identify aspects of your operation that can benefit the most from AMRs and then “de-risk” your potential investment by bringing in some help from an AMR vendor or system integrator or both. The system integrator will come to your site to discuss your goals, provide a demo of possible mobile robots and various tasks they can accomplish and perform a site evaluation and risk assessment that includes evaluating your floor layout, typical traffic and best routes.
They will also test Wi-Fi coverage, evaluate how you use enterprise-resource-planning (ERP)/warehouse-management and manufacturing-execution-system (MES) solutions for integration with the robot’s fleet-management software. And they will determine how long the robots might need to operate in between battery charges.
Based on the initial applications you choose, they’ll also help to determine what types of top modules your mobile robots might need based on the application requirements, the weight of materials and integration requirements. Without top modules such as conveyors or lifts, carts and other mobile robotics equipment, autonomous mobile robots couldn’t do what they’re meant to do.
Start small
An AMR can scale for future needs. You don’t need to build everything in one day. If you are new to mobile robots, start small with a scalable and flexible AMR solution that allows you to learn with a smaller initial investment in both time and budget, but one that can be easily rolled out site-wide once you have proven it will work for your facility.
Learning with low-risk applications such as transporting finished goods to end of line or quality assurance or even removing trash will facilitate the process and set you up for future growth.
Metro Plastics, a supplier of custom plastic injection molded parts and tools based in Indianapolis, wanted an AMR to transport finished goods to quality assurance. Prior to using AMRs, workers would put the finished goods in boxes on a pallet at the end of each press unit and then wait for inspectors to make their way to the station, with folklifts moving through the facility to pick up the pallets when the goods were approved.
With as many as 20 jobs happening at a time, this meant that boxes and pallets would often stack up at each press unit as they waited for the inspector, often becoming a tripping hazard, especially during busy periods.
Figure 2: The Tinturaria Florisa plant in Brusque, Brazil, is using five high-payload robots to transport more than 200 tons of fabric per day, a 122% increase on what was manual achieved.
In its new facility, Metro Plastics set up AMRs to loop the production floor, stopping at each press for 30 seconds (Figure 1). This allows press operators to load finished products as soon as they fill a box and pass it on to the warehouse for quality inspection. That eliminated fork truck traffic and the accompanying clutter while making the production floor cleaner and safer.
Once you choose the initial task, as Metro Plastics did, work with the system integrator to review the application to determine the timeline of the project and how many robots you might need with what type of top modules to accomplish the task. The system integrator will also determine the distances and partners per hour needing to be moved, preferred paths and aisle widths for bi-directional traffic. They will also help train an operator to program the robot before helping to deploy the pilot project.
Starting by testing one or two mobile robots to perform these low-risk applications, even if you have enough tasks to occupy an entire fleet, helps to prepare your facility and your organization overall to more easily and quickly integrate more applications across facilities.
Strategically scale
Get help from more internal robot champions. If you are satisfied with your initial project, you might be ready to expand the use of AMRs within your facility or facilities. The versatility and flexibility of leading mobile robots enable you to add in multiple robots to do similar tasks as your pilot project, or even perform completely new tasks for different processes or production lines (Figure 2).
Before proceeding with a larger project, however, make sure to involve your human workforce in the project or at least help them to learn why you are automating so they accept more robots within the facilities. Automating the often dull, dirty and dangerous tasks with mobile robots allows employees who were previously performing the tasks to move on to more valuable work. Some of these employees could be trained to become directly involved in the AMR project as robot operators that help to program the robots and monitor them as needed. Some could be trained to service the robots if anything goes wrong.
In any case, they will learn to support the use of the robots working alongside them rather than be concerned about them taking over their jobs. While the uninitiated often believe the robots will come in and work nonstop without human intervention, that isn’t usually the case.
A successful deployment may start with one robot champion to help lead the way, but it will require multiple robot champions to make it all run smoothly.
Start now, start small and think big, working as a team to give your entire organization time and experience to prepare to move from single robots to dozens or even hundreds. These steps will help you reach your automation goals in the challenging business environment.
Matt Charles is sales director for the Midwest United States and Canada at Mobile Industrial Robots (MiR). Prior to joining MiR in 2019, Charles served as a key account manager for Kuka Robotics and a motion control and robotics sales engineer for Cross’s Automation Group. He earned a bachelor’s degree in mechanical engineering from Purdue University in 2007.Contact him at [email protected].
Sponsored Recommendations
Latest from Robotics
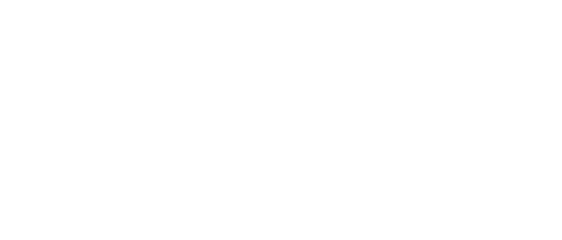
Leaders relevant to this article: