HMIs once served the sole purpose of interfacing at the machine level, with each application using its own software, which communicates between devices. Now, in some cases, the human-machine interface (HMI) is taking on a larger role, led by the need for more computing power and real-time analytics, as well as the introduction of Web-based software technologies into industrial manufacturing. This is creating a much more open environment, powering better remote access, data manipulation and edge computing from the HMI. Innovative HMI offerings from seven companies—Idec, ADISRA, Beijer Electronics, Omron Automation Americas, Phoenix Contact, Bosch Rexroth and Siemens—offer a variety of features, including Web-based technology, open platforms, high performance computing and advanced database analysis.
Two-way remote access
Idec’s HG series HMIs range from 4.3 to 15 inches and are configured using WindO/I-NV4 screen creation software, which Linda Htay, product marketing specialist for Idec, calls “simple and intuitive.” She says the HMIs are designed for all types of end users. Because the HMIs are suited for harsh conditions, the oil and gas industry is a main market for this product, including many others, such as packaging, medical equipment, wastewater treatment and traffic control and transportation.
Due to the pandemic, demands for HMIs that can withstand disinfecting and sanitizing equipment has risen, says Htay.
The HMIs are built to support a wide range of operating temperatures, from -20 °F to 60 °F for outdoor mounting. The screen also includes long-lasting LED lights, rated for 100,000 hours or more to minimize service needs. The liquid-crystal display (LCD) uses thin-film-transistor (TFT) technology, which makes the display brighter and sharper.
“The TFT technology provides certain benefits to improve HMI image quality,” Htay says. The TFT refreshes more quickly than a regular LCD display, she adds. The display is also readable in harsh or very bright lighting. “The brightness is the key feature to enable the HMI to be sunlight-readable,” Htay says.
The Idec HMI includes a built-in web server to facilitate remote monitoring and control with cybersecurity features (Figure 1). “The HMI web server is accessed using any device with a web browser, such as a smartphone, tablet or PC. Accessing the HMI using this method gives a user the same functionality, as if they were standing in front of the HMI on the factory floor,” Htay says.
Photo: IDEC_Control_Design_Innovative HMI-group 2021a.tif
Figure 1: The HMI HG series includes a built-in web server to facilitate remote monitoring and control.
It makes troubleshooting and system maintenance possible anytime from anywhere. Control limitations and the monitoring functions available to a remote user should be considered for proper cybersecurity of critical applications, notes Htay.
“The typical network configuration of HMIs with servers includes a local network with Ethernet communication and suitable industrial protocol. The HMI connects to controllers and to both local and remote web-browser terminals. The web browser on external networks accesses the HMI on the local network through the local network’s gateway/router and firewall, again following proper cybersecurity practices,” Htay says. “The user-account security function can give users multiple-level access to machines or equipment, based on their priority level.”
Two-way access to the HMIs via Wi-Fi Ethernet is provided through mobile apps for Android and iOS devices. “Users can download and upload programming, or they can delete data from the internal memory or an external memory device, such as a USB flash or microSD card,” Htay says. “Since the app can do it wirelessly, there’s no need to make sure the right cabling or program or software is available.”
Technicians can access the HMI of a PLC without even opening the cabinet. The app also includes features to limit the parameters that are being monitored and controlled. The HMI, using a file-transfer-protocol (FTP) function or mobile app or both, can read and write—copy or move—files to local memory, an external memory device or a cloud-based file, database or data storage platform. “This gives users even more options,” Htay says.
The mobile app also provides some data configuration. The logged data can be viewed in a trend graph, as well as attached to a text message or email and sent using templates configured for multiple recipients. Alarm logs, data logs, operation logos and screen shots can also be captured and sent this way, so, if errors occur, management is notified right away. “It helps the user to increase productivity and minimize downtime of the applications,” Htay says.
Comprehensive development environment
Marcia Gadbois, president and general manager of ADISRA, has seen a recent evolution in HMI development and equipment. “It used to be the HMI was just in the machine, and it did a very dedicated thing. Now it has evolved to not only do that, because that’s still a purpose that it serves, but it’s also offering machine builders the ability to transform their model by doing remote viewing and servicing of their machines remotely. It’s also now being put into headless devices, so it can do not only remote visualization, but the analytics, as well,” Gadbois says.
ADISRA’s software offering SmartView captures this next evolution of HMI software, she says. The connectivity between HMIs and sensors, PLCs and controllers, and all the sources of data and all the historical data, Gadbois says, gives the applications quicker access to that data in real time, and the system can perform anomaly detection to act on that data. “It should be able to not only do a decision tree, but analytics on the data that’s coming in in real time, and say there’s a problem based on casual analysis,” Gadbois says. “So, it’s reading it in real time and giving analytical suggestions based on the data and history.”
SmartView is an HMI, SCADA and IIoT development environment, and it also includes built-in redundancy (Figure 2). “It is allowing you built-in protection for downtime, so if something goes down, the other system picks up the load of continuing to analyze the data, and then, when the other HMI or edge device comes back online, it will sync it,” Gadbois says.
Figure 2: SmartView is an HMI, SCADA and IIoT development environment and can connect to proprietary drivers or with older communication options.
ADISRA is a big fan of OPC UA, she says, because of all the connectivity choices there, but SmartView can connect to proprietary drivers or with older communication options. “You have to work with the IT, as well as work with the proprietary, older protocols, as well as providing them a bridge to the new one,” Gadbois says.
SmartView extends HMI connectivity to all types of intelligent IIoT sensors, databases, historians, the cloud and other systems. “In classic automation architectures, there is a distinct site-centric HMI layer and a separate enterprise-centric analytic layer, so information and recommendations between the two must constantly be communicated, creating inefficiencies,” Gadbois says.
SmartView combines a comprehensive development environment for mobile, edge, dedicated hardware, personal computer and cloud environments into one platform.
SmartView is also SCADA-ready. “It has all the functionality for the SCADA market, as well as HMI,” Gadbois says. “It really is combining all that into one package.” With a small footprint, she says, it serves the IIoT market and many devices.
The HMI can reside with headless sensors or edge devices. “What it’s really doing there is it allows you to do remote visualization of the data coming in, but it is also helping you to understand what that data means as it’s coming in,” Gadbois says.
This HMI is applicable across many industries. As a company, Gadbois says, ADISRA has been focused largely on small to mid-sized manufacturers. The software has been used in oil and gas, water and wastewater and other industries. “Our focus is machine builders, the OEM market and small to mid-sized manufactures,” Gadbois says. For the small to mid-sized manufacturers, she thinks they are underserved by the current marketplace.
Software development à la carte
Jeff Hayes, product manager at Beijer Electronics, has also seen a move in HMI software development toward more connectivity and openness, and he also detailed how software has become the more valuable product for companies. “Hardware has become almost a commodity in HMIs,” Hayes says. “For the most part, for internal machines, HMI hardware is standard, so where companies spend their engineering resources and expenses is in software development.”
Beijer uses its own proprietary software, iX Developer, which is a GUI-like tool. At the company, the development group works closely with the support team and product managers to create custom products that customers are asking for in the field. Those products were shared internally for use with other customers, and Hayes says, that was the unofficial start to the Smart Engineering Resources (SMEs). Eventually, Beijer formally packaged the custom products and put them on a website for the public (Figure 3). These pieces of code for different applications are available, some for free and some for sale, to download and use with Beijer’s proprietary software. The project has grown since its inception, and Beijer actively creates the packages and publishes one or two per week. The package may include some how-to text on implementing the code, and Beijer’s customer-service department is available to help any user to implement new software.
Figure 3: Smart Engineering Resources began as custom products designed in the field for customers, now available to the public.
Adding PLC software to the HMI is a growing trend, Hayes says, which is supported by one of its SMEs. “Instead of having separate PLC and HMI hardware, you do it together in one machine in one HMI,” Hayes says. He uses smartphones as an analogy. “A smartphone used to be just a phone, and you had a separate MP3 player and separate GPS, and they’ve added everything together into one device. The same thing can be said with HMIs today. We’re doing a lot more with them,” he says.
A lot of HMIs use CODESYS, which is an open-source product. How to access and use that CODESYS software with a PLC is another example of a use of Smart Engineering Resources.
One of the latest resources available gives users more options to analyze data. “We gather an awful lot of data from the PLCs, and, so, what do we do with that data? What people want to do is they want to be able to make business decisions with that data,” Hayes says.
The information collected can be easily displayed on a dashboard. “We have integrated our software with Excel and Microsoft Power BI software, so we give you the data dump, and you can use whatever software to aggregate and parse the data and create dashboards from the data,” Hayes says.
The use of Smart Engineering Resources does require a novice-level knowledge of the software. “We try to make our software easy to use because it’s a graphical interface for the basics,” Hayes says. But underlying the graphical interface is the .net Microsoft framework, which uses C# (C-sharp) programming. “Most of the people that will use our product will have developed a pretty good understanding of C# and the programming involved with it,” Hayes says.
Integrated development environment
Data manipulation was on developers’ minds at Omron, when it created its Soft NA runtime software, says Clark Kromenaker, product manager of HMI, IPC, controllers and software for Omron Automation Americas. Kromenaker also points to other software development trends. “I think what I’ve seen change is a move toward an integrated development environment (IDE),” he says.
In a more traditional setup, the HMI and the PLC each had separate development programs, as well as all the individual devices in the application. When considering software updates, or firmware updates for the HMI itself or the PLC, it can be cumbersome to do all that, at least quickly, Kromenaker says.
“So, what a lot of developers are going to is what’s known as an integrated development environment, where one software tool, Sysmac Studio, has all those development environments in one software package, so they can program the PLC, the HMI, safety, motion, everything off one development environment,” Kromenaker says. Updates can be done once, and each device gets updated at the same time, he says.
In general, Kromenaker says, HMI screens are trending larger and higher resolution. “A lot of that follows consumer trends,” he says. The objects that are used in developing the HMI application are becoming more sophisticated. “Instead of push buttons and indicator lights and gauges, more advanced data manipulation tools can visualize data more effectively,” he says.
Soft NA was released in spring 2020. “It’s an emulator for another product that is hardware-based,” Kromenaker says. The Omron hardware-based HMI, called NA5, is a closed-loop system with computer components but not a full-blown computer. “The user can only do one thing with it, and that’s to run an HMI interface on it,” he says. “So, we developed an emulator that emulates all the functionality of that hardware version, NA5.” An industrial PC can run Soft NA and enterprise resource planning software or manufacturer enterprise software, along with controlling the machine itself through the Soft NA, Kromenaker says.
“The main driver for developing that was data manipulation,” he says. The reams of data coming off the factory line need a computer to manage all that data. “A PLC is great at running machines, but it does not do a very good job if you’re trying to manipulate data in a PLC,” Kromenaker says.
With Soft NA, users can also choose the computer power they want (Figure 4). “In the hardware version, NA5, you’re limited completely to what the design is of the product. With Soft NA, you could choose any type of processor, CPU, any amount of memory, hard drive size,” Kromenaker says.
Figure 4: With Soft NA, users can choose the computer power they want, and those that need high-performance can store and process large amounts of data.
Users of Soft NA need the high-performance computing power to process and store large amounts of data. “Almost every manufacturer is becoming more information-intensive, but, for this type of power, particularly in food and pharmaceutical, they are required to collect a lot of manufacturing data,” Kromenaker said. Data on raw materials and operators working at a machine can assist if problems occur and recalls are needed.
The automotive industry also has large data needs, Kromenaker says. Serialized components and conditions are monitored for trends; for instance, spikes in temperature are usually a sign of an issue. “Things like that help to have a continuously functioning operation, where you’re not surprised by downtime,” Kromenaker says. By monitoring trends, operators can know when service is needed before breakdowns and schedule that maintenance during holidays or breaks, or before it causes downtime.
Soft NA, as part of the Sysmac solution, was designed to interface as an HMI to Omron’s NJ and NX series of machine automation controllers, and applications that are developed on Soft NA will also run on NA5, so it’s portable between both the two platforms. “Machine builders using the NA5 can now add an option to upgrade to a Soft NA and IPC HMI, where other software can also be used to provide more functionality at the machine level,” Kromenaker says.
Universal web-based protocol
HMI software development is also moving away entirely from traditional runtime setups and instead using web-based protocols for easier communication. In a more traditional HMI setup, users create the visualization project at the HMI. “The visualization resides on the operator panel,” says Bjoern Falke, product manager for HMI/IPC for Phoenix Contact.
If that operator panel gets damaged and needs to be replaced, that’s at least a two-step process, Falke says. Users have to replace the damaged hardware, and find the visualization project associated with that station and download it to the unit. “If you do good housekeeping, and you keep these projects neatly organized, it shouldn’t be a problem, but it is a little more involved,” Falke says.
The Phoenix Contact BWP2000/WP4000 series HTML5 web panel is making that process easier. The web panel can talk to any web server for visualization of PLC data or any kind of visualization, configuration or diagnostic data hosted by a web server (Figure 5).
Figure 5: The BWP2000/WP4000 series HTML5 web panel can talk to any web server for visualization.
“The HMI projects no longer reside on the HTML5 web panel,” Falke says. “Because we are able to utilize the universal HTML5 protocol, we can talk to any kind of web service, so you’re no longer tied to any specific manufacturer.”
If the unit were ever to get damaged, users can replace the web panel, and all they need is the IP address of the web server. “That should hopefully be on the label of the unit, if you do good housekeeping,” Falke says. “So, you don’t have to chase down that HMI project anymore because that HMI project would reside on the web server.”
The web panels are the next step in the evolution of the HMI, he explains. “It’s definitely closer to IIoT because you are now more open. You are more universal, and the whole deployment is easier because the HMI now grabs the data that it needs to display from a centrally located web server,” Falke says.
A few years ago, Phoenix Contact launched a new series of PLCs with a built-in web server. This product was designed to work with that web-based device, but it also allows for compatibility with a much larger number of applications.
With HTML5, the web panel doesn’t need Ethernet IP, Profinet or Modbus TCP compatibility or any vendor-specific protocol to communicate. With no local HMI project to download, the panels are quicker to deploy in new machines and service if damaged. “You have the luxury of reduced downtime in your installation and quicker deployment,” Falke says.
Web-based systems are being used in many industries. The traditional sectors, Falke says, are automotive and material handling, but the web panel has also been used in oil and gas, agricultural and water monitoring applications.
On the edge
“HTML5 technology has existed for some time as a web technology for building web pages that we all use every day, but it has been slower to enter the industrial machine controls,” says Allen Tubbs, product manager at Bosch Rexroth. “The growth of technology outside of manufacturing has allowed us to pull those types of solutions into industrial manufacturing.”
With Bosch Rexroth’s runtime visualization software called WinStudio, Tubbs says, it made sense for the company to rethink its HMI strategy. Now, Bosch Rexroth will also offer WebIQ, its fully HTML5 based solution, as part of its ctrlX Automation platform. It’s been released as a prototype version, and the full version will be available to the public in April 2021. The WebIQ product is made by German-based company Smart HMI, and fits in the Rexroth’s open ctrlX architecture.
“Web servers allow the use of almost any device with a browser to view the application,” Tubbs says. “Also, HMI software is becoming more open to third-party solutions integration that allows for more implementation on the IT side.” Open-source and third-party software solutions that have not been focused on industrial manufacturing, are now bringing simple-to-implement solutions, such as edge databases, data visualization and SMS texting to the HMI.
Traditional HMI software designs have typically used what-you-see-is-what-you-get (WYSIWYG) editors, which allow users to drag interface objects onto a screen that will appear later as the runtime application. Similar tools are used by the web-design community in applications that help users to build web pages quickly, and WebIQ brings the WYSIWYG design tool to the HTML5 environment. “Traditional WYSIWYG editors do not typically have HTML5-type solutions. It has been an either/or choice until recently,” Tubbs says.
Many HMI applications have long been able to record, store and perform simple trend analyses on the data, but WebIQ allows for more sophisticated analysis tools, such as databases, integrated alongside the visualization piece (Figure 6).
Figure 6: The WebIQ, an HTML5-based solution, facilitates advanced query capabilities at the edge.
“Simply having the advanced query capability of a database at the edge is quite valuable in analyzing machine data. Traditional HMI software has had the ability to record data and even visualize it, but has not had the power of a true database,” Tubbs says. “As software technology grows, the HMI, as a user interface is progressively being pushed to be an edge-compute device as well.”
Perhaps always an edge device by definition, the HMI has not always had the IT communication and processing capability that machines have today and which allows for the use of HMIs as more than simple interfaces. “The merging of IT software into the OT space is allowing for more capabilities on the PCs that were typically only used for machine communication and operator interface. Now, data can be collected and analyzed at the machine with database and machine-learning tools,” Tubbs says.
Previously, with proprietary systems, users could run the HMI software but nothing else. “The hardware was pretty much designed around the software,” Tubbs says. “But now as software has become more independent from the hardware, now you can run the software on lots of different types of hardware and design the system such that you can add other functions into it.”
As a recent example, Tubbs says, the WebIQ software was integrated with an InfluxDB database into the same PC that’s running WebIQ. InfluxDB, an open-source time series database, stores the machine data. “Not only can we do visualization on the data like we could before, but I can use a query engine from InfluxDB to be able to pull insight out of that data and keep all that data right there on the edge without having to send it to a network database or a cloud database,” Tubbs says.
With the blending of web page functions, the application can be deployed simultaneously on many different hardware platforms. The software license structure can be modified to meet the specific application size.
“The cost of the system is based on the scale of functionality, and there are different types of functions that are unlockable along the way,” Tubbs says. “That’s a typical way of scaling HMIs in the past.”
However, the WebIQ software also provides another way to scale. “You have users that want to connect into the system from the top down, rather than from the machine up, so you can also scale based on how many clients need access at the same time,” Tubbs says.
ALSO READ: HMI software makes the user experience
From single machine to SCADA
Siemens has also embraced web-based technology with its new visualization software system, Simatic WinCC Unified. “The software runs on a variety of platforms, from proprietary panels to PCs, and users can interact with the machine directly from this platform or from a network-connected client, such as a smartphone or tablet,” says Ramey Miller, HMI product manager for the United States at Siemens. “It’s really breaking down a lot of barriers between functionality that would be typically pigeon-holed into an IPC or a PC terminal, where it would reside in a powerful system there. We’ve broken the barrier down of software functionalities and pulled those into a panel-built machine-level solution (Figure 7).” From a single machine on the facility floor, multiple isolated systems can share data and screens, and as the network grows, the WinCC Unified system will take users all the way to a SCADA system.
Figure 7: WinCC Unified visualization software’s open interface can take the power of an IPC and put it in a panel at the machine.
“The open communication is definitely a focus point right now because everybody wants to have remote access,” Miller says. “The backbone is developed with openness in mind to allow porting of information out.” The native drive technologies needed to communicate with other systems are all built into WinCC Unified.
The use of scalable vector graphics (SVGs) helps to make the transfer between devices quick and seamless. SVGs are a standard of graphics that can be resized without loss of image quality or resolution. With a bitmap or a .jpg file that’s imported into an HMI screen, if a user sized the project for a 7-inch screen and then tried to view that project on a 15-inch screen, the image would pixelate. SVGs can scale from any size and keep a clean, crisp image.
“It lends itself to be more flexible for all this remote connectivity that we’ve been building up. You’re not set to just the resolution of the operation terminal anymore,” Miller says.
WinCC Unified is built to integrate with Siemens Totally Integrated Automation Portal (TIA Portal), the encapsulating software that runs other Siemens products.
For instance, users can get tag information from a separate PLC very easily into the HMI within the same project because the two devices are already aware of each other. “They can easily relate and connect diagnostics information or alarm information,” Miller says.
The software also allows users to reuse elements across different hardware and projects, saving time and money to deploy to an unlimited number of panels and PC systems. “Having a panel and a PC runtime software package that can handle both types of solutions, the objects that you develop for configuring within a project can now do tasks between those two different platforms,” Miller says.
“You’re not going to have to redesign that entire graphical object and how it works. All of that is easily pushed and pulled back and forth between those two platforms,” says Miller.
From a graphical standpoint, objects are known and configured the same between the platforms, Miller says. “That’s part of the scalability. We can easily change our device type to any screen size of the panels, and it will reset that project to run on that different size panel,” he says.
WinCC Unified also works natively with web technologies such as HTML5 and others. “The software provides a wide range of industry-specific offerings, and it can be customized for user-specific applications with its open interfaces,” Miller says.
It also supports multiple communication protocols and can exchange data with other systems. “That makes it very flexible from a human-machine-interface aspect, to connect to devices that are not necessarily from Siemens,” he says. “The newer architecture that we’re seeing is remote access. People want to drill down the machine screens from anywhere in the facility, and you can do that with the web-based technology that it’s built on.”
Siemens is also looking at the future of HMIs and software integration, Miller says. “They may not be out on the factory floor yet, but we see future cases of augmented or virtual reality-type interfacing with our system,” he says. WinCC Unified is set up with the foundation to realize those advances in the near future.
Sponsored Recommendations
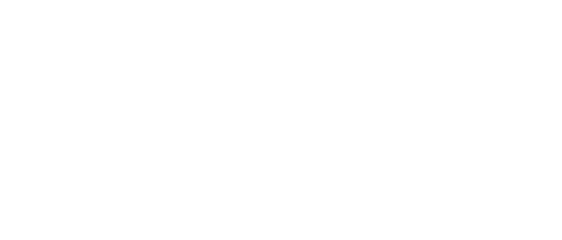
Leaders relevant to this article: