A Control Design reader writes: What are the effects of harmonics and electromagnetic interference (EMI) on the increased amount of industrial Ethernet found in manufacturing facilities?
ANSWERS
Grounding the shield and surge protection
First of all, let’s clarify that “Industrial Ethernet” is a blanket term covering Profinet, Ethernet/IP, Modbus TCP, EtherCAT and any other industrial fieldbus utilizing Ethernet as a physical layer.
Industrial Ethernet is inherently rather resistant to EMI, as the standard twisted-pair cable used for transmission cancels out most differential-mode noise between the conductors. Transformer coupling on the Ethernet card itself cancels out most common-mode noise, as well.
As you go up in speed from standard Ethernet (10 Megabits/second) to fast Ethernet (100 Mbps) and then to Gigabit Ethernet (1,000 Mbps), the construction and quality of the cables required goes from Cat. 3 to Cat. 5 to Cat. 5e, Cat. 6. Tighter twists, lower gauge wire and internal cable conductor spacers are some of the modifications.
Despite Ethernet’s inherent EMI resistance, when applied in an industrial environment with 480-Vac conductors and especially variable-frequency-drive (VFD) output cables in the mix, it can need some help.
Shielded twisted-pair cable is available in all categories, and this will keep out virtually all noise. However, it comes at a cost, about four times that of unshielded twisted pair (UTP). Additionally, the shielding increases the capacitance of the cable, which will serve as a low-pass filter and limit the maximum transfer speed, especially at long distances.
Grounding of the shield is necessary, so shielded eight-position-eight-contact (8P8C) connectors are needed for termination of shielded twisted pair (STP). Whether to ground one or both ends of the cable is a matter of debate. Analog (4-20 mA, 0-10 V) signal cable should be grounded at one end only, to prevent ground loops and 60-Hz hum. With digital signals, hum is not an issue; however, due to poor bonding techniques, ground-point differentials can exist between equipment residing in different cabinets. If your Ethernet cable shielding is the only thing bridging the differential voltage, bad things can happen. Therefore, many engineers, including me, recommend grounding the Ethernet shield at the “source” end only. For example, if you are connecting a PLC to a VFD in a remote cabinet using Profinet, install the shielded 8P8C connector on the PLC end only; a VFD to encoder link with EtherCAT would use the shielded connector on the VFD end, and so on.
Always follow the same wire routing rules for Ethernet as you would for any other serial fieldbus or analog signal. For example, keep parallel runs with power lines separated, in separate wireway and cross power lines at 90°.
Don’t overlook surge protection on the Ethernet cable runs. Outdoor runs between buildings, or to a silo, are obvious use cases, but consider surge protection for long inter-cabinet runs indoors if there is any arc welding or electrostatic powder coating going on nearby. Even high-speed roll goods converting in the paper and textile industries can generate an enormous amount of static electricity.
Finally, for the ultimate in EMI, surge, harmonic and lightning protection, fiberoptics is the gold standard. Fiberoptics offer complete protection for signals going to or from Class I, Div. 1 or other hazardous areas. No zener barriers are needed because there is no electricity present. For reference, most control signaling in pharmaceutical plants uses fiberoptic Ethernet, regardless of the fieldbus protocol riding on top.
To summarize, industrial Ethernet in all its flavors offers the best way to shuttle high-speed data throughout the plant. With a few careful installation considerations, including shielding, grounding, surge protection or fiberoptics, it will enable your plant to run efficiently and share production data with upper-level IT systems.
JOHN CLEMENT / field application engineer / Allied Electronics & Automation
Diagnose compromised signals and minimize interference
With manufacturing operations becoming heavily reliant on data exchange between control systems, smart sensors, data acquisition systems and myriad interconnected networking protocols, handling the speed and integrity of these signals becomes paramount.
What are the symptoms of a compromised signal?
- Erroneous signals from process sensors can trigger false alarms or inconsistent control.
- 0-10 Vdc analog signals are more susceptible than 4-20 mA signals.
- Watchdog systems detecting lost communication signals can trigger a shutdown.
- Low voltage PLC inputs can be triggered unexpectedly.
Harmonics and EMI must be managed through proper design, proper cables for the application, cable end connections, competent understanding and execution of shielding/grounding techniques by installation personnel.
What are techniques used to minimize interference?
- proper enclosure grounding
- ac line filters to help remove noise
- ac line reactors and filters for ac drive controllers
- snubber/suppression diodes used on inductive loads, such as solenoid valves and contactor coils.
Isolate cables from feedback signals, low-voltage instrumentation and process signals from any power wires that can cause harmonics. Separate these cables. If there is a point at which these signals can intersect, it is best to cross these cables at right angles. Proper shielded cables are a must.
Certainly, consult with a world-class cable manufacturer for the proper cables to match your application. With the variety of communication protocols, network speeds, distances the cables need to be run, it is likely the cable manufacturer will have exactly what you need and associated termination ends for your specific application.
WERNER LAMBERGER / technical support engineer / Automation24
Control the noise
Eliminating electromagnetic interference (EMI) is very important when keeping machines and plants trouble-free. Depending on the voltage of this noise, it can interfere with network communication, affect motor and drive performance, damage the control system or even cause a machine failure. Electrical noise can come from common electrical equipment, such as power supplies, generators or rectifiers or other devices. In intralogistics, for example, cardboard boxes running down a conveying system generate excessive static electricity, which creates EMI and interferes with the Ethernet network. This problem is made worse by the fact that it is very tough to resolve. Whether it causes small annoyances or creates considerable downtime, this environmental problem can easily become very expensive for end users.
The first step to reducing noise as much as possible is making sure the equipment is installed and wired properly. Did you isolate power cords properly, for example, separating high-voltage lines from standard 24-V lines? Otherwise, the noise from ac lines can interfere with dc lines. Is everything properly grounded? This is critical, for more reasons than this one. However, in some cases, it might not be possible to eliminate the noise completely, such as in the intralogistics example, so it is important to monitor and not to add to it.
Three-phase power measurement terminals can plug into standard I/O segments and provide critical information to the machine controller about power quality. These system-integrated I/O hardware solutions use the same programming software and network as the control system. Engineers should also look for reliable power supplies with low EMI and harmonics, which can eliminate issues in the electrical system before they can get to the machine. In addition, it is important to select components—I/O, controllers and sensors—that are designed to withstand any unpreventable EMI in the production environment.
SREE SWARNA GUTTA / I/O product manager / Beckhoff Automation
Stop transmission interruption
Harmonics and EMI can create electrical noise that can interrupt the transmission of an Ethernet network (Figure 1). These disturbances may degrade the performance of the Ethernet network or even stop it from functioning. It is highly recommended to avoid these types of interferences to the Ethernet network by using shielded cables and connect the shields at the end of the connections.
Figure 1: Drive technology and power-supply technology can help to minimize EMI emitted from inverters.
RUBIN ORTIZ / product manager for large inverters / Mitsubishi Electric Automation
Proper planning of medium and layout
The frequency and severity of harmonic and EMI issues are likely to decrease through mitigation techniques as industrial Ethernet continues to replace traditional fieldbus in manufacturing and process plants with the advent of IIoT and Industry 4.0. The increased speed and error recovery mechanisms that are possible with full duplex industrial Ethernet that has two twisted pairs are a key advantage over fieldbus. Ethernet can also take advantage of shielding and bonding techniques within control cabinets, and fiberoptic or wireless mediums in locations like welding cells or nearby large generators where EMC can’t be overcome with cable shielding or cable tray layout with power and communication cable separation. With proper planning of transmission medium type and physical layout, industrial Ethernet is quite capable of managing the potentially disruptive effects of harmonics and EMI.
STEVE FALES / director of marketing / ODVA
Avoid noisy components
With regard to how harmonics and EMI can affect industrial Ethernet, it's important to maintain proper shielding and grounding with industrial-rated Ethernet cables, as well as proper cable routing. This latter point means that you should avoid noisy items such as drives, servos, motors, welders and induction heaters. It's also a good practice to keep motor and high-power cables separated from Ethernet cables and follow all guidelines for grounding based on the protocols.
CARRIE LEE / product manager—controllers / Omron Automation Americas
Slow equipment degradation
The biggest EMI problem is the sporadic situations that slowly degrade the equipment and their components. Problems can be generated by EMI, like in electronic equipment, with failure of communication between devices of an equipment network and computers, alarms generated without explanation, action on relays, without logic or command, and burn down of components and electronic circuits.
The control of noise in automation systems is vital, because it may become a serious problem even for the best devices and hardware of data acquisition and action.
Fortunately, simple devices and techniques, such as the use of adequate grounding methods, shielding, twisted pair wires, media signal methods, differential filters and amplifiers may control the noise on most measurements.
DANIEL WEISS / Senior Product Manager / Newark
ALSO READ: Stop EMI from ruining your day and your system performance
Sponsored Recommendations
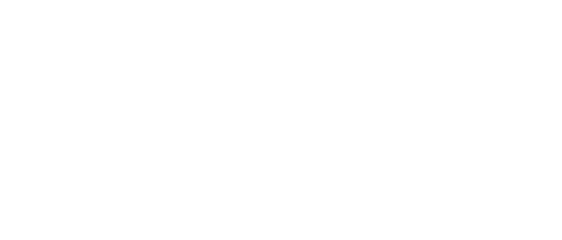
Leaders relevant to this article: