How do all-in-one automation platforms affect digitalization efforts?
As original equipment manufacturers’ and system integrators’ downstream customers are under increasing pressure to scale production to meet market demand while simultaneously increasing profitability, they are turning to data to methodically remove waste from their processes and therefore begin the transition into the Industrial Internet of Things (IIoT). This transition is driving demand for original equipment manufacturers (OEMs) to prepare machinery that not only meets current market performance metrics but provides cost-effective data harvesting without introducing cyber vulnerabilities. Original equipment manufacturers and system integrators (SIs) can competitively address data collection without compromising deterministic motion control or machine cybersecurity, all while avoiding hidden manufacturing costs.
The ubiquity of downstream customer data requests is fueled by the exponential acceleration of networking technology and the decreasing time for which manufacturing firms can capitalize on inflection points in the market. While data is created at the device or workpiece level, implementing a data-harvesting system can be achieved by a host of vendors—each selling product after product that is single-mindedly aimed at transferring performance insight from the point of collection to a central depository for analysis by either artificial-intelligence algorithms or experienced data-analytics professionals. Unfortunately, gathering data represents only a segment of the work needed to create sustainable results from the data gathered. When seeking production data to drive business decisions, OEMs and SIs should strive to create machines that accomplish these aims:
1. Consistently gather reliable and robust data without adversely affecting the current performance of the machine, as measured in production output or system precision. In other words, a data collection system should adhere to medical professional’s axiom of “doing no harm.”
2. Transport all data through the downstream customer’s facility without compromising cybersecurity. Akin with the understanding that when the security of one machine is diminished the security of all machines is threatened.
3. Integrate data collection practices while exceeding capital returns expected by downstream customers’ shareholders. As leading manufacturing firm’s performance has been built on success from the past, failing to exceed this precedent quickly invites both competition and leveraged buyouts alike.
By addressing all three of these goals, OEMs and SIs can not only properly serve the customer base but build a true competitive advantage when compared to their competitors and peers.
Reliable, accurate and robust data is absolutely imperative to reaping the benefits from a data-collection system. Time-synchronized data, which provides multiple perspectives of the manufacturing environment, allows downstream customers to establish a baseline of performance. A baseline, built on strong sample groups, can establish achievable improvement goals supported by production key performance indicators. These key performance indicators provide insight into a system’s long term performance trend, the trend itself allows firms to remove noise to translate root problems into tangible improvements. Such magnitudes of data, often required for establishing long-term trends, demand efficient network scaling to deliver data to areas of decision making without compromising the data’s credibility.
Often tacking on an additional system, machines may see a decrease in overall network performance, inadvertently widening the gap between the current state and the target goal. This is especially true when downstream customers are unsure of which data will be critical for future improvements and request multiple variables to be tracked at immense resolution.
With a greater expectation on the network infrastructure, without intentional topology selection, it should be no surprise when system refresh times are slowed due to the addition of data collection. Network segmentation and complementary globally open industrial protocols paired with data-ready hardware should be strongly considered before implementing data-collecting endeavors.
Network segmentation separates data traffic from safety and motion bandwidth. The act of doing this ensures that an overloaded subnetwork does not interference with the performance of other subnetworks on the system.
Allocating proper communication through complementary networks can also maintain jitter-free motion while simultaneously providing constant streams of manufacturing data. Data collection with larger packets run on slower, albeit microsecond-refresh-rate, networks while motion and safety control occur on truly deterministic protocols.
This can be achieved through leveraging both EtherCAT for high speed and EtherNET I/P for larger packet size communication. Data-ready hardware can be found in devices that are compatible with IO Link and controllers that remove middleware from system architecture by leveraging open platform communications unified architecture (OPC UA), message queuing telemetry transport (MQTT) and structure query language (SQL).
Cyber threats are increasing in both occurrence and severity, which increases the overall magnitude of risk for cyber security breaches within manufacturing facilities, according to IBM’s 2022 “X-Force Threat Intelligence Index”. This acceleration of risk is a function of industrial networks’ becoming ever-reaching and of artificial intelligence beginning to enter the cybersecurity space “McKinsey Technology Trends Outlook 2022”.
As the impact of cyber threats become cyber-physical, the ramifications of attacks extend beyond lost production to lost assets. Incorrectly implementing data-gathering practices exacerbates this trend by increasing opportunities for attacks, by openly linking operational-technology (OT) networks and information-technology (IT) networks, and also the severity of attacks, by increasing the intellectual property and trade secrets to the whims of attackers.
Edge computing, secure programmable-logic-controller (PLC) data transmission and network segmentation are all tools that can be used to simultaneously decrease the probability and severity of the cyber threats. Edge computing and PLC data transmission, without middleware, are methods where the IT network can be segmented from the OT network. By keeping data consolidated and managed within the OT system and keeping the OT system segmented from other facility networks, IT vulnerabilities cannot be transferred to OT consequences.
Network segmentation can take this one step further: In addition to helping manage data-traffic flow, the segmentation can be physical barriers from hackers jumping from an IT network into an OT network. This can all be completed without adding a superfluous network to the architecture. While many data-collection products can be quickly tacked on, they often add to the total number of networks within a facility. Increasing the total number of networks can increase the cost of designing and maintaining the entire system.
Data acquisition is not a small investment. Summing hardware cost, software licensing fees and hidden costs such as installation, maintenance and troubleshooting, it is only Darwinian logic that manufacturing firms weigh these costs against potential efficiency gains and the firm’s cost of capital.
Often single-purpose data-collecting products focus on helping firms to meet the return-on-investment (ROI) metrics by removing cost by solely focusing on data collection; of course, when these solutions fail to protect cybersecurity standards or preserve network efficiencies, integrators shoulder the burden. Often failure isn’t realized until OEM and SI downstream customers have completely committed to a solution during scaling.
As sustainability requires harmonization with adjacent systems in the facility, a holistic data-collection approach should be strongly considered. All-in-one or integrated automation ecosystems empower facilities with data collection while simultaneously improving cybersecurity through software and system updates. While the cost of implementing this across an entire facility appears daunting, scaling it is much more achievable.
All-in-one platforms can justify their existence with immediate success at a machine level by blending data, control, motion, safety, vision and robotics in one cell. Integrating these into a single integrated software environment allows programs to leverage simplified architecture for quicker development time through both two-dimensional and three-dimensional simulation.
These software environments also converge data, video, program structure and ladder logic creating a holistic perspective during playback, which can be time-synched and event-triggered to allow local and remote team members to diagnose issues without interrupting production.
As this occurs in the programming environment, implementing change can occur more quickly without an added license fee. As multiple machine cells comprise a manufacturing line, control of the line and then the facility can be scaled with subsequent capital projects, allowing firms to spread capital projects across multiple fiscal years while benefiting from compounding network benefits and hardware bundling economies of scale.
While a single-minded data-collection product is logical in an ideal world, modern automation systems do not exist in a vacuum. All-in-one platforms can achieve reliable data collection and maintain real-time network determinism and increase cybersecurity by simplifying automation so OEMs and SIs can focus on harvesting data to instill change.
Thomas Kuckhoff is product manager—controllers at Omron Automation. Contact him at [email protected].
Sponsored Recommendations
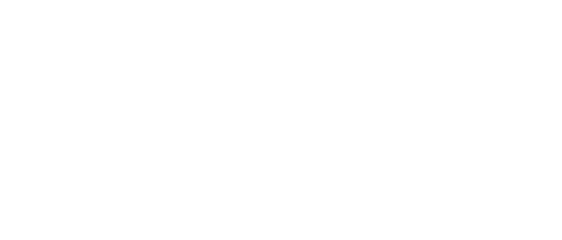
Leaders relevant to this article: