Mazak iSmart Factory leverages IIoT expertise
Mazak National Applications Engineer Neil Desrosiers, Manager of National Applications Engineering Paul Robinson and President Dan Janka explained how the machine builder envisions the future.
What are three key things that a machine builder, system integrator or manufacturer should know about your company?
Second, because we are in the business of manufacturing tools for manufacturers, we fully understand the constant need for refinement and competitive flexibility that drives our customers' expectations. Just as our own industry is dynamic and ever-changing, so are the diverse industries in which our customers compete. We constantly expand what we make, how quickly we make it and how much it can do, along with how and how well we can support our customers to achieve the fullest profitability for their businesses.
Third, we are a global company that thinks locally. We constantly strive to meet customers more than halfway, partnering with them to achieve more together. When we first established a North American headquarters and began importing Mazak equipment from Japan, we needed to ensure that our machine tool designs reflected the expectations and requirements of customers on this side of the planet. Accordingly, we began creating new designs, first as region-specific versions of Japanese models and eventually as original products entirely developed and manufactured in Florence, Kentucky.
What new technologies are driving your product development and why?
The increasing focus on small-batch, high-mix/low-volume part production leads to a parallel focus on equipment and processes that can stay ahead of constant changes in outcomes and throughput. As industries such as aerospace grow increasingly dependent on new and challenging workpiece materials to make parts that may take weeks of machining to produce, our Multi-Tasking technologies enable customers to set up a workpiece once, in a single machine, and take out a finished product. Our Hybrid Multi-Tasking machines combine conventional machining capabilities with advanced manufacturing technologies such as laser metal deposition, friction stir welding, hot wire deposition and software-driven multi-spindle synchronization for gear production.
How does the Industrial Internet of Things figure in your business strategy?
For advanced cybersecurity that protects our machines and the data on our factory network, we use the Mazak SmartBox, a revolutionary launch platform and highly secure open standard. This solution, which includes a Layer 3 managed switch, can connect multiple machine tools and other pieces of equipment with an industrialized version of the security protocol found in server rooms and other IT facilities. We use this scalable, end-to-end solution to connect all our manufacturing equipment, including machines, software and other devices, to our network and enable production data to flow freely to management systems via MTConnect.
The Mazak SmartBox also enables us to harvest and analyze production data from individual machines and manufacturing cells, including equipment from any manufacturer and of any age or type. This sophisticated digitalization gives our factory operations a fluent exchange of data under secured conditions that protect both our production information and our intellectual property. Although our customers may not operate facilities with as many pieces of equipment as our more-than-800,000-sq-ft manufacturing campus contains, they can implement the same technologies and achieve the same securely sourced data gathering and analytics.
How will machine automation and controls alter the way companies staff their operations in the future?
But experienced professionals with these skills are becoming hard to find. Through the attrition of Baby Boomer retirements and the industry's struggles to attract younger generations into its ranks—often because of false perceptions of working conditions and earning potential—Deloitte estimated that 2.4 million manufacturing jobs would remain open between 2018 and 2028, creating a potential economic impact of $2.5 trillion.
These facts and predictions have become a preoccupying problem for the industry. As employers grapple with these conditions and their ramifications, they have begun to understand the need for a three-pronged approach to counter it. First, they must train their current workforce to undertake greater responsibilities with cross-trained abilities that eliminate siloed approaches to production-line tasks. Second, they must make the work they offer more approachable for people with lesser skill levels, especially new hires with minimal experience. Third, they must find ways to accomplish more work with fewer people.
Training current workers to manage automated systems responds to the first part of this paradigm. Automation itself holds a critical key to the second and third parts. Unattended operations enable manufacturers to make parts around the clock and without human personnel present on site. Tool hives, pallet changers and other sophisticated options enable a single operator to manage multiple machines, all tied together with exceptional control technology. We build Mazatrol conversational programming directly into our CNCs, enabling operators to serve as programmers by answering straightforward questions about each part directly on the control to optimize cutting.
How is the development of software solutions impacting your requirements for hardware?
For example, we developed our Mazatrol SmoothAi CNC and its software from the ground up to support Multi-Tasking and enhance the machining process with artificial intelligence, machine learning and advanced data management. Its various software modules address specific conditions and functions with built-in and ever-growing expertise that otherwise would require additional monitoring capabilities or off-line programming additions.
Our AI technology detects any sign of spindle vibration and optimizes cutting conditions to offset its effects on workpiece quality, tool life and machine operating condition. Machine-learning displacement compensation through our Ai Thermal Shield stabilizes operating temperatures to prolong equipment life and enhance output results. Our Smooth CAM Ai software modules address the need to simulate machining operations and verify how actual production will proceed before committing to begin it.
At the same time that these and other software functions enable shops to extract every ounce of performance from our advanced machine tools, the hardware of our Mazatrol SmoothAi CNC incorporates ergonomic adjustments to make the large screen viewable for operators of all heights and present a multi-phasic view of critical machine data on one at-a-glance view. The CNC accepts an additional screen to show information from AI modules. At every turn, our hardware informs what our software must control and monitor, and our software enables shops to see and alter what their equipment does.
As engineering and IT continue their convergence, which one is and/or will be leading the direction of future automation and technology at your organization?
IT's role in manufacturing is vast and growing, as the Mazak iSmart Factory demonstrates, both as an everyday production platform and as a proven model of how our factory networking technologies can enhance manufacturing operations for our customers. The newest frontiers in enhanced machine-tool performance lie as much in IT as in machine-feature development. As the sophistication and power of AI and machine-learning implementations increase within our industry, IT has become a co-equal participant in the design process, helping to create machines that deliver the productive agility manufacturers want on their factory floors.
Looking into the future, how will technology change your company over the next five years?
At the same time that manufacturers collect, analyze and act upon increasing data streams, we are increasing our use of simulation technologies and augmented reality to anticipate production needs and offer newly effective training modalities. Our customers now can use our products to create digital twins of their actual machines so they can see and fine tune how their intended production processes will play out in terms of finished results. This means that when a job consists of a single part that requires weeks to create out of high-value materials—when failure truly is not an option—our technological capabilities enable our machines to help customers plan ahead to create parts correctly the first time and every time.
Along with machine technologies that enhance predictive analytics, we also use extended reality to make training and support easier and more effective. Virtual-reality technology enables us to train customers and service technicians on digitalized recreations of expensive equipment that suffer no real-world damage if a trainee makes a wrong choice. Through augmented reality, we can annotate a shared view of a customer's machine to provide procedural explanations, assist in troubleshooting or identify replacement parts, saving time for customers and for service technicians and delivering better results.
At the same time that predictive technologies and extended reality enhance our products and our service capabilities, we see increasing sophistication in the capabilities of our hardware. Today’s Mazaks not only perform subtractive machining at the highest levels of precision and productivity, but they can combine those processes with alternative manufacturing technologies in ways that advance Multi-Tasking beyond our original vision of Done In One.
Our Hybrid Multi-Tasking solutions add such capabilities as laser metal deposition, friction stir welding, Hot Wire Deposition and gear production to multi-axis machining. This technology applies to machines already installed in the field, not just new machines. Mazak MegaStir recently introduced an upgrade kit that customers can use to add friction stir welding to subtractive machines, broadening the reach of this groundbreaking technology.
Overall, the future of manufacturing both drives technology further and is itself driven by the technologies it serves. We see abundant opportunities for productive refinement and advancement of the tools we make and the industries they serve.
ALSO READ: Mazak debuts new technologies for CNC control, remote connectivity
Sponsored Recommendations
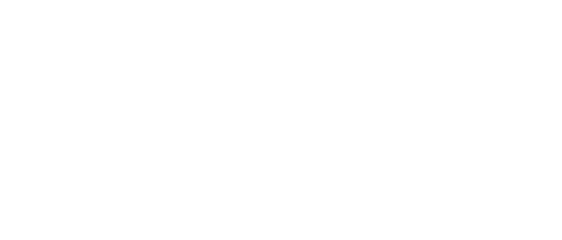
Leaders relevant to this article: