Many industrial machine builders have moved toward the use of push-in technology for terminating wires on a terminal block, as opposed to a more traditional spring cage or screw terminal. The newer technology does not require the many tools needed for older methods, so it’s usually more efficient and requires less user expertise. Three manufacturers, Phoenix Contact, Wago and Dinkle, discuss some of their terminal block push-in connections with options for space-sensitive and rugged applications, side-entry insertion, leg and cage clamp spring designs, and making the connection with unferruled wires.
To ferrule, or not to ferrule
The Phoenix Contact PTFIX series distribution terminal blocks use push-in connection technology, which provides a quicker way to terminate wires, says Will Morris of Allied Electronics & Automation, a distributor for Phoenix Contact. “You don’t have to use a screwdriver, so it really adds to your efficiency,” he says. “It’s a simple push-in wire terminal, instead of a spring case or a screw terminal, so it saves a lot of time.” Morris says push-in connections are up to 50% quicker than traditional methods, and they also help with fewer problems from terminations falling out.
A spring cage requires a tool to press open the terminal in order to insert a wire, and screw terminals require a screwdriver to open and close the terminal. “When you are terminating large amounts of wire, this can be very time consuming,” Morris says. “Push-in technology is a simple one-step process.”
The push-in connection can work with ferruled and unferruled wires. “Ferrules are used to crimp the end of the wire for more effective and quicker insertion and eliminating wire pull-outs,” Morris says. Unferruled wires do require an additional tool for installation with this terminal block.
The PTFIX series was designed for space-sensitive applications, where compact distribution is needed (Figure 1). “It’s generally a little bit smaller, so it can save space,” Morris says. “Transverse mounting capability allows high wire density and can save space up to 50%.”
Figure 1: Phoenix Contact PTFIX series distribution terminal blocks use push-in connection technology and were designed for space-sensitive applications.
The PTFIX 10 lineup offers a bump up in size and can handle larger wires than its smaller counterpart. “The footprint is a bit larger and can support up to six AWG wires per UL,” Morris says. American wire gauge (AWG) ranges from minimum of 26 to a maximum of 6 with solid wire. Morris says AWG 6 increases amperage and distance flexibility.
The terminal block’s mounting options add to its flexibility and space savings. Standard DIN rail mounting is available or direct mount. The DIN rail can also be mounted with a clip to mount vertically or horizontally. A 35-mm clip enables transverse mounting, or a 15-mm clip is available. “It gives you the flexibility to fit them wherever you need them in your cabinets,” Morris says.
This series of terminal blocks also offers an adhesive mount for placement on flat surfaces. “They have an adhesive on the back that can be peeled off, and they can place them wherever they need to go,” Morris says. “It’s not something you see very often, but it’s pretty handy.”
As an enhanced safety feature, different colors on the block can help users save time in installation or repairs. “Wires are always color-coded based on what their function is and this matches the terminal block to the wire, so it makes it a lot easier to know which wires go where,” Morris says.
Side-entry connection
Sometimes space constraints might push a user toward a screw connection, even if push-in is preferred, so Phoenix Contact also offers the PTV family of terminal blocks (Figure 2). “Side-entry connection allows wires to come directly into the terminal block, eliminating the need for extra space for bending wires into top-entry,” says Cory Myer, product marketing specialist for Industrial Cabinet Connectivity, which is Phoenix Contact’s group for DIN rail mounted terminal blocks.
Figure 2: PTV terminal blocks with side-entry on the push-in connection require less room for bending wires.
Myer further explained the push-in connection technology from Phoenix Contact. It uses a leg spring design to directly insert solid or ferruled wire without the use of tools. “If stranded wire is being used, you simply depress the orange pusher, insert the wire and release the pusher,” Myer says. “The same orange pusher is also used to remove any wire.” The leg spring design, he says, keeps the push-in force minimal, and the pull-out force is five times the International Electrotechnical Commission (IEC) required rating.
The direct, push-in insertion of the wire saves time and labor. With a solid or ferruled wire, the block can be terminated in one second or less, Myer says. “Even with stranded wires, it is extremely clear and simple to depress the pusher, and it still offers time savings over a common screw or spring cage block,” he says.
A spring connection is good for high-vibration environments or applications with wide changes in temperature. “A spring connection will automatically adjust and ensure the connection stays strong,” Myer says. “Spring connections allow for a very reliable connection, thanks to how a spring works.”
One of the benefits of a screw connection terminal block is that it uses a side-entry connection. “The wire comes directly out of the wire duct and into the terminal block, while the screw is on the top of the block. Because of this, there is no bending or manipulation of the wire required, which can be very helpful in tight situations,” Myer says. A screw block uses a regular screw to lower and raise a cage clamp that houses the wire, and, when tightened down, the cage clamp allows the cage to put pressure on the wire and hold it in place under stress. “When properly torqued, this principal allows our screw blocks to be extremely reliable in intense environments,” Myer says. With a screw connection, the wires come in the side, and the screw is on the top, while most push-in connections use top-entry, with the wire coming in the same spot where the screw would be on a screw connection. “That could be tough in some very space-sensitive applications,” Myer says.
Instead of the time-consuming screw connection, the PTV terminal blocks now also offer side-entry with the push-in connection. “It is wired up in the exact orientation as a screw block,” Myer says. For tight spaces screw connections and side-entry push-in connections require less room for bending wires. Control panel design, in general, is trending smaller and smaller, Myer says. “Cabinets are getting smaller, while systems are getting more intelligent, calling for products designed to maximize space,” he says. The PTV push-in terminal block is also a drop-in replacement for screw block terminals because of their similar side-entry design.
Typical push-in connections can also require rerouting wires or wire ducts to replace a screw connection block. “The wire must come out of the wire duct, bend upward and then back down into the terminal block. In space-sensitive applications, this can at times require more space to be designed in between the terminal block and the wire duct to allow for this maneuver,” Myer says. “With PTV, those modifications are not necessary.”
Rugged and pluggable
Wago offers machine builders a push-in solution for faster wiring with a cage clamp spring design (Figure 3). “It combines a compact design, high current carrying capacity with the additional benefits of intuitive lever operation,” says Rob Toenies, senior product manager, Newark, which distributes Wago products. The finger-operated lever makes it a tool-free solution and provides a secure connection when the lever closes the clamp. “The also clearly locks in position (open/close) with a tactile and audible click,” Toenies says.
Figure 3: The Wago 832 Series MCS Maxi 16 terminal block works with a cage clamp spring design.
The Wago 832 Series MCS Maxi 16 terminal block works for solid or ferruled conductors, sized up to 4 AWG with ratings up tot 85 A/600 V. The push-in cage clamp spring pressure connection technology makes the terminal block work in the most demanding applications. The connection is resistant to the negative influences of vibration, thermal cycling and corrosion. Toenies says the 832 series was developed for power electronic device applications in the robotics and factory engineering, energy, IT and 5G infrastructure, and EV charging industries, where they are looking for easy and reliable field-wired terminations. Food processing equipment, which requires frequent washdowns, is a good example of an application well-suited for these terminal blocks, he adds.
Vibration and temperature cycling allow for leak paths to occur, which can lead to moisture penetration and then corrosion. “Corrosion reduces current-carrying capacity and results in intermittent failure of the circuit. A corroding connector may cause its circuit to fail intermittently, causing downtime and maintenance expense,” Toenies says.
The pluggable solution works wire-to-board (a connector and a wire connecting to a connector on a printed circuit board (PCB)) and wire-to-wire (a connector and a wire connecting to another connector and wire). “Wago’s pluggable solution also offers the benefit of being able to terminate conductors either horizontally or vertically to the PCB,” Toenies says. Wire-to-board connections can be made from varying angles (0°, 90° and 180°) to the PCB. “Wire-to-wire connections are also in the scope, whether those are of a flying lead/free hanging nature, or mounted to a DIN rail or flat surface with an accessory mounting foot,” Toenies says. It can even be used as a panel feedthrough solution, he says, for passing power through an enclosure wall.
Unferruled wire solution
Dinkle also offers a terminal block connector for tool-free wire insertion with or without a ferrule. The push-in design PCB connector was developed for field operations where wires often need maintenance and operators don’t have the necessary equipment—a ferrule, crimper or the screws and lugs needed for traditional connections. Matt Hou, sales engineer at Dinkle, says some have automatic machines to ferrule wires on-site. Push-in type terminal blocks are being integrated throughout the industry, Hou says. The ferrule provides a strong insertion point, and push-in connectors typically require a strong force for insertion. “Ferruled wires are required right now to achieve that efficient wiring method,” Hou says. “With the push-in design PCB terminal blocks that is one of the limitations.”
It can also slow down maintenance without a ferruled wire or the tools to do that in the field. “The push-in type terminal block, it’s very efficient in the installation aspect, but during maintenance without a ferruled wire, it’s just really hard to insert the wire, if the wire does break,” Hou says.
“In the factory, everyone has a ferrule; everyone has the equipment,” he says. In the field, where the proper tools might not be available, a standard screw-in type terminal block could be a better choice than a push-in connection, or a terminal block like Dinkle’s 0229 series that can terminate unferruled wires (Figure 4). The installers also don’t need experience. “It definitely expands the ability to do the installation,” Hou says.
Figure 4: The Dinkle push-in design PCB connector 0229 series has a lever on both sides to open the cage, so users can insert wires directly without needing to ferrule wires.
The terminal block has a lever on both sides. “Pushing the lever opens the cage, so you can insert the wire directly without needing to ferrule the wires,” Hou says.
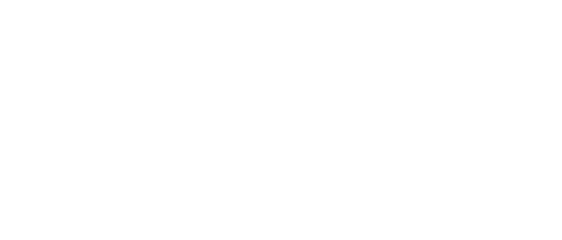
Leaders relevant to this article: