How machine designers can integrate thermal-protection technology to prevent solid-state relay and equipment failure
What do large industrial/commercial HVAC and refrigeration systems, heavy-duty transportation, assembly lines, medical equipment, energy and other manufacturing systems all have in common?
Motors. Big and expensive electrical motors that, if they overheat, can be damaged or even destroyed. Most large motor-driven machinery requires a system attached to the motor’s power supply that will sense overheating and turn off the motor to prevent this damage. In many cases, this device is an electrical relay that turns power on and off. There are two main types of these relays—electromechanical relays (EMRs) and solid-state relays (SSRs).
[javascriptSnippet ]
EMRs vs. SSRs
[pullquote]For more than 50 years, electromechanical relays were the go-to solution for managing load circuits.
However, in the past decade or so, solid-state relays have taken a great deal of the market share.
There are significant differences between EMRs and SSRs, especially in terms of life span.
EMRs are mechanically based and have moving parts, making them highly susceptible to magnetic noise, vibration, shock and other outside influences that can affect wear and lifecycle. In contrast, SSRs offer a durable, all-solid-state electronic construction with no moving parts to affect wear or accuracy, thereby offering predictable operation and
longer life. The average lifespan of electromechanical relays is in the range of hundreds of thousands of cycles compared to 5 million hours for three-phase solid-state relays. With such maintenance-free durability, SSRs often outlast the equipment in which they are installed.
In addition to a longer life span that provides greater reliability and replacement cost savings, SSRs provide faster switching than EMRs, making them adaptable to a wider range of high-power load applications. They operate silently, without the undesirable clicking sound emitted by EMRs, with low-input power-consumption and produce little electrical interference. Both shock- and vibration-resistant, SSRs can withstand harsh environments and continue to operate accurately and reliably, whereas EMRs need frequent replacement, making them very undesirable in harsh conditions.
SSRs excel over EMRs in other areas, as well. They are compatible with control systems, immune to magnetic noise, and are encapsulated to protect critical components. The solid-state design makes them position-insensitive and provides design engineers more flexibility to mount SSRs anywhere within an application—whether sideways or upside-down. SSRs can be installed in places where there is heavy vibration with no interference in performance, whereas mechanical-based EMRs are very sensitive to positioning, shock and vibration, thereby restricting design options.
With all the advantages that SSRs provide, it is understandable that they are more expensive than EMRs. This significant price-point disparity correlates to the life span of each relay type, as well.
Though simple in purpose, both device types provide critical functions; they must power down the electricity quickly enough to prevent component or load damage. For example, if the EMR or SSR fails to activate at the designated high set-point maximum, the motor it controls can continue to operate and overheat from a variety of influences. An electric motor can also overheat when it is forced to operate in a high-temperature environment, under constant overcurrent conditions or continuously without maintenance. Motor overheating can also be caused by mechanical failure of the application equipment itself or when a motor is started at an incorrect current value. In the latter case, the motor starts operation in a much warmer condition than the system’s originally assigned temperature.
About 90% of all electrical motor failures occur at the startup because of one or more of the following conditions:
-
high ambient temperature
-
high or low voltage supply
-
motor too small for the application
-
intermittent duty applications
-
high altitude.
Thermal management challenge
As SSRs generate heat when conducting current, there is a thermal-management component to their operation. Should overheating occur and damage an SSR, diagnosing and replacing the SSR can take time while the assembly line, machine or manufacturing system is down and out of service, running up even more costs.
To illustrate how an SSR operates, consider the product’s use in commercial-refrigeration applications in the building equipment market. In a refrigeration application, the SSR is responsible for turning the compressor on or off to keep the system’s operating temperature within a specified range. The input control circuit voltage might be 90-280 Vac with a required tripping temperature set at 95 °C. A buffer is engineered into the circuitry using a variety of components to ensure that the desired tripping action occurs as appropriate.
When the SSR turns on to conduct load current, it also generates internal heat. Failure to adequately protect the solid-state relay can cause damage to the relay or to the load.
To address this overheating challenge, SSR technology has been developed to integrate a thermostat into the SSR itself to ensure that the relay always operates in a safe or protected mode. The first SSR design of this type was developed specifically for use in a commercial refrigeration application. With some modifications, this SSR can also be used in wide variety of machines and industrial and manufacturing applications to provide similar system benefits. This design incorporates all the advantages of standard SSR technology. The temperature-sensing element is integrated directly into the SSR, so it triggers the SSR to cut off input circuit power at a specified temperature level. The SSR requires new layouts of the PC board and power section assembly.
The most important consideration is the SSR’s ambient operating temperature, which will allow for calculating the best derating for ampacity. In other words, engineers need to identify the maximum power rating, current rating or voltage rating for which the SSR is rated; then use less than those maximum ratings. This will prolong SSR life and prevent premature failures. Other points important in the selection process are the power the SSR dissipates and the heat sink used.
The automatic thermal protection is accomplished by means of the integrated thermostat embedded in the SSR (Figure 1). The thermostat senses the internal temperature of a mechanical interface with a metal plate where the internal power-switching device is mounted. If the heat exceeds the normal range, it sends a signal to the SSR to turn off the power. This built-in thermal protection completely prevents overheating conditions by providing a trip before equipment damage can occur.
Figure 1: The thermostat senses the internal temperature of a mechanical interface with a metal plate where the internal power-switching device is mounted.
In addition to preventing overheating, the integrated thermal protection function can troubleshoot design issues in the system. It can help to identify incorrect heat sinking capacity in the SSR or system, poor installation resulting in insufficient heat-sinking contact, heat-dissipation efficiency of the system, as well as other issues. This provides a valuable tool to the engineer responsible for the system’s operation.
The SSR with thermal protection can also be used in a range of heating control applications such as industrial ovens, HVAC/R, sterilization equipment, molding and extrusion machinery and welding equipment. Other uses include heavy-duty conveyor systems, such as those in construction, mining, packaging and material handling. Consider a conveyor-belt application where a motor could stick and cause overload and potential damage to the system. In this case, the SSR with integrated thermal protection would prevent overheating from occurring by shutting down the conveyor belt as soon as a pre-determined heat threshold was met within the SSR’s thermostat.
In injection molding applications where limited space can cause the temperature in the cabinet to rise, thermal protection prevents the SSR from overheating if the heat sinking is not adequate, thus avoiding costly repairs. For heating systems, the thermally protected SSR can help to shut down the heating element if there is a problem with the temperature controller that causes a temperature runaway, thereby protecting the entire system.
Despite being more expensive, solid-state relays offer many benefits over electromechanical relays:
- long life eliminates frequent component replacement
- fast switching for wider application use
- minimal electrical noise
- operation in harsh environments
- low-power consumption
- position insensitive for flexible mounting options.
ALSO READ: Mini-PLCs—more than just a smart relay
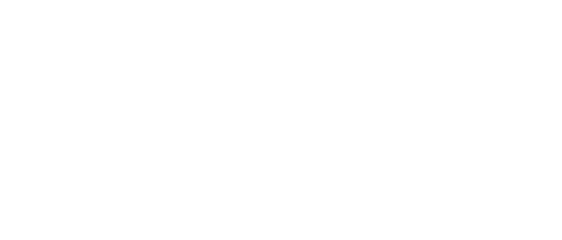
Leaders relevant to this article: