Romeo Engineering leverages PC-based control to improve manufacturing speed and accuracy
Kevin Oseguera is controls engineer at Romeo Engineering in Fort Worth, Texas. Contact him at 817/656-0048 or [email protected].
Any application, any time: Fort Worth, Texas-based engineering firm Romeo Engineering (REI) takes flexibility in manufacturing beyond the next level, developing and building sophisticated manufacturing equipment. With applications ranging from aerospace and automotive to electronics manufacturing and food processing, the company provides service and performance, while cutting manufacturing and assembly costs. Founded in 1987, REI maintains a knowledgeable staff of in-house mechanical, controls, and software engineering professionals.
“We believe that the REI principles of automation can be applied with great success across a broad spectrum of product manufacturing,” says Frank Romeo, REI president. “By utilizing standard automation components across all our systems, we provide solutions for nearly any application challenge, no matter how unique.” We have fully embraced this concept.
While our applications are rather diverse, our primary markets are waterjet cutting and special-purpose automation systems. REI manufactures waterjets year-round, providing an off-the- shelf cutting solution for industrial applications. The special-purpose automation side, however, tends to be more custom. REI can develop and build tailored solutions that are as small as a servo-powered screwdriver or as large as a full-scale pultrusion line.
PC-based CNC technology for any application
To best capitalize on our core market of CNC waterjet cutting, we design and manufacture a full range of ultra-high-pressure water and abrasive/water-cutting and cleaning equipment. This product offering combines waterjet intensifier pumps with specially designed machinery from REI, tailoring the latest in PC-based CNC cutting technology from Beckhoff Automation to match customer needs. We offer a series of precision cutting systems that make advanced waterjet technology available at a low cost. Our success in the market is largely due to the fact that REI waterjet systems are incredibly robust. To that point, many of our machines are still in service after 25 years.
Also read: Industrial Ethernet and multi-core technology
One of the more exciting applications for the PC-based automation technology and an offshoot of the CNC waterjet systems is a new, customer-specified CNC glue-application system for a manufacturer of windows in garage-door applications. Performing an important step to ensure weather resistance and product longevity, the CNC glue-applicator machine precisely applies a bead of hot glue around the edges of the frame in such a way that the operator can simply press the window into the frame to create a weather-tight seal.
As the needs of the company outgrew the previous glue-application system, the customer began to seek a faster, more efficient solution. The company approached us to create a custom machine that eliminates inefficiencies while increasing production throughput.
The old machine moved too slowly to keep up with the quickening pace of production. Instead of using CNC functionality and a gantry to move the nozzle, the previous machine required the company to place the workpiece on a table and the entire workspace moves around it. This method caused some pooling of the glue in the corners, wasting adhesive materials and costing the company money.
The glue that binds
When specifying components for this machine, we went through an extensive vetting process and found that Beckhoff provided the right price-to-performance ratio and met the required goals of the project. The motion control requirements for CNC systems are especially demanding, so designing a robust motion platform that was still cost-effective was paramount to the success of the project. Providing the foundation for the motion control is the Beckhoff TwinCAT 3 software platform that runs on a Beckhoff C6920 control-cabinet industrial PC (IPC) with an Intel Core i3 processor inside (Figure 1).
Figure 1: At the heart of the glue application system is an industrial PC, providing processing power and performance while reducing programming time and cost.
The compact C6920 is equipped with a 3½-in motherboard, and all PC connections are conveniently located at the front of the housing. Internal cooling fins and an exchangeable fan cartridge provide all the necessary cooling. A vast improvement over our previous systems, the Beckhoff IPC has proven to be excellent for our operations. The PC-based system provides significant benefits for us, both in programming and cost reductions.
The backbone for the control system is the TwinCAT 3 automation software platform from Beckhoff, offering a robust, flexible programming environment (Figure 2). We use TwinCAT 3 as our main control engineering platform. One of the biggest advantages that it brings to the table is that there are no licensing costs for the development environment. We pay the TwinCAT 3 runtime as part of the low cost of the controller, rather than paying for development license seats with other companies and still having to provide them a copy in the end. Over our previous software platform, we save around $2,000 with the Beckhoff system by not having to purchase development seats.
Figure 2: Software provides a platform for automation and motion control, enabling a vast array of programming languages to be used.
The integration with Microsoft Visual Studio in TwinCAT 3 and the flexibility to use a wide range of programming languages has been a boon for REI. Being in the Visual Studio IDE, I can program in a manner conducive to my software engineering background. Adapting a program, regardless of language, to an industrial machine is a simple process with the openness of TwinCAT 3, and the ability to use GitHub source control has been extremely valuable to our multi-discipline teams.
All of our projects reside in a private repository, and each team member can access the files and make changes. This is a vast improvement over previous methods of sharing files over a server with the associated risks of multiple people opening the same file concurrently and causing errors or accidently overwriting important changes.
A suite of Beckhoff servo motors and drives provides motion control for the CNC glue system. Specifically in this case, we chose to implement the Beckhoff AX5112 Digital compact servo drive because of its connectivity to a wide range of servo-motor types, such as rotary and linear. These drives also leverage EtherCAT communication, enabling highly dynamic motion and positioning tasks (Figure 3). Coupled to the AX-series drives are a pair of AM8053 servo motors featuring One Cable Technology (Figure 4); these streamline the necessary cabling by combining feedback and power signals into a single cable.
Figure 3: A look inside the control cabinet reveals a group of four digital compact servo drives, providing motion for the system in a compact footprint.
Figure 4: Coupled to the servo drives is a pair of servo motors, providing all the necessary motion for the CNC system.
The Beckhoff servo motors and drives represent the perfect solution for our application. Whether focusing on the fast EtherCAT communication or One Cable Technology, the Beckhoff solution enabled us to push the limits of CNC technology and offer a world-class machine to our customer.
Fast, reliable I/O that does not take up excessive space is also necessary for the manufacturing operations of the customer, and we leverage HD terminals from Beckhoff that provide 16 channels per I/O terminal, networked via EtherCAT. Providing programmable safety on the machine is a Beckhoff EL6900 TwinSAFE Logic terminal. The TwinSAFE Logic can establish 128 connections to other TwinSAFE devices such as EL1904 and EL2904 terminals used on the machine, which serve as safety inputs and outputs (Figure 5).
Multiple EL6900 are cascadable within a network, and these terminals feature certified safety function blocks, which are configured according to the requirements of the application. Safety functions such as emergency stop, safety door monitoring, or two-hand control can be selected and linked. In the application, we implemented several emergency stop buttons, with the possibility of adding safety mats in the future, all tied in through the TwinSAFE I/O modules creating the distributed safety system.
Figure 5: REI utilizes a series of I/O terminals for machine control and safety, which offer top-level performance in a compact form factor.
Figure 6: The Romeo Engineering customer-specified CNC glue application system applies glue at a blazing 1,200 in/min. Controls Engineer Kevin Oseguera oversees further testing.
Cost savings that stick
The EtherCAT-enabled machine is as fast and efficient as it is safe. With the integration of the PC- and EtherCAT-based control components, the high-speed machine can apply glue at around 1,200 in/min, four times faster than the old system (Figure 6). The CNC functions eliminate the glue pooling that occurred in the window-frame corners through precise programming that intelligently speeds up and slows down the machine on corners without stopping. Coupled with the upgraded speed, we provided twice the number of usable glue nozzles, effectively doubling the number of projects one machine can tackle simultaneously, and doubling throughput as a result.
The precision of the CNC motion allows the new machine to take on more projects at the same time, as a function of the speed and accuracy of the upgraded components. TwinCAT 3 really puts the Beckhoff system over the top here. An indispensable ability in the programming environment is that you can simulate the behavior of motors and other devices. None of our other vendors have been able to do that. Virtual machine design tools really help because I feel like the machine is right in front of me; it’s somewhat like having the machine already built before installing a single part.
This is extremely valuable to us. We can test and evaluate a machine before a single wire is connected. Testing and debugging can be done virtually, even remotely, reducing required programming time by up to a week and a half.
At REI we were able to reduce costs significantly by switching to Beckhoff controls technology. With the Beckhoff system, we were extremely pleased to reduce our budget by more than $7,300, savings we are then able to pass along to our customer.
We always strive to balance price and performance with our machines, and Beckhoff solutions allow us to do just that. Given the success of the implementation of PC-based control and EtherCAT into REI systems, we plan to continue extensively integrating these technologies moving forward.
Sponsored Recommendations
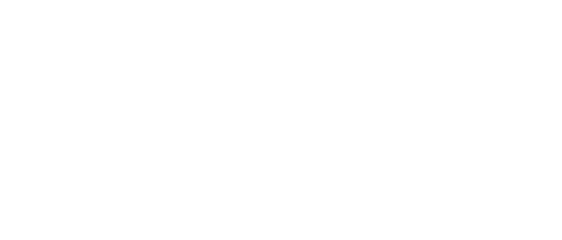
Leaders relevant to this article: