Located in Mt. Zion, Illinois, Green Valley Manufacturing has been making die and mold handling equipment for nearly 25 years. Die or mold carts don’t seem glamorous at first. Functionally, they are cousins to forklifts, but these carts specialize in moving awkwardly sized and sometimes very heavy dies or injection molds, some exceeding 100,000 lb, from one point to another with exceptional speed and stability. Client industries for Green Valley’s carts span from aerospace and automotive to medical and military. Practically every job is in some way a custom order.
A tier-one passenger vehicle parts manufacturer approached Green Valley in 2019 with a novel challenge. The client wanted a mold cart capable of lifting 70,000 lb. Moreover, because of the tight spaces in the manufacturing environment, they needed the cart built with four-wheel drive, four-wheel steering and an extremely precise four-cylinder lifting system. The client wanted Ackerman steering to increase tire traction, steering range and precision when executing turns. Essentially, the cart needed the ability to turn on a dime as well as crabwalk sideways by turning all of the wheels in the same lateral direction. The cart required four different steering modes—an impossibility with conventional mechanical linkage.
The application demanded combining simultaneous but different motion across the left and right. Ackerman steering requires geometry, trigonometry and calculus to determine each wheel’s angle, because it’s impossible to execute a turn with two wheels at the same angle. Doing such maneuvers with a typical PLC would be incredibly difficult, and so Green Valley found itself too limited by its existing programming environment and hardware.
[javascriptSnippet]
The role of the right controller
In order to meet the more demanding client requirements, Green Valley knew where to turn. The company partnered with John Henry Foster, a St. Louis-based firm that specializes in custom pneumatic and hydraulic systems. Having worked with Green Valley in the past, John Henry Foster devised a solution to the challenge of expanding Green Valley’s mold cart maneuverability required three sets of curves. The first mapped the relationship of wheel angles as they moved through their range of motion. The second conveyed the relationship between the wheel angle and wheel rotational speed. The third curve represented the speed throttling needed as steering angles increased. This last point was particularly valuable for Green Valley’s client.
John Henry Foster is a longstanding distributor for Delta Computer Systems motion controllers and had used Delta on previous projects with Green Valley. The company selected Delta’s RMC200, which it felt to be the best, most adaptable controller on the market, capable of both electric servo and hydraulic motion control and support for up to 32 control axes.
This particular Green Valley cart project used four hydraulic axes for steering and four axes of electric control for wheel speed. With most controller brands, this would require at least two four-axis controllers, with one controller addressing the hydraulic domain and another the electronic. However, because the Delta RMC200 is a 32-axis controller capable of supporting both hydraulic and electric motor controls, the wheel-steering and wheel-speed functions could be handled by a single control unit (Figure 1).
Figure 1: The cabinet contains the RMC200, complete with power supply, CPU, and I/O modules.
If one controller is managing the steering and a different platform is managing the wheel speed, they have to share that information back and forth and make sure that all the math is being done correctly. That adds complexity and can introduce issues. With the Delta application, though, we can take care of all the math and basically put all the motion inside one controller. That allowed Green Valley to focus on other aspects of the cart handled by the PLC.
The lifting system is comprised of four hydraulic cylinders with internal transducers. Each cylinder is separately controlled by the RMC200. This offers a tremendous benefit in adjusting for off-center loads. As Green Valley describes it, one might have 25,000 lb on one side of the table and only 3,000 lb on the other, but with continuous, microsecond-speed pressure detection, all four cylinders can lift and lower uniformly to within 0.05 inches of variance across all four corners. This motion control could have been done with a separate controller, but being able to run all 12 axes—wheel control plus lifting control—from the RMC200 yielded a simpler design with more efficient management and lower total parts cost.
None of Green Valley’s prior cart solutions offered this many axes of control, and the added steering complexity, along with the client’s specific demands, presented a new challenge. Armed with the advantage of using the RMC200, though, the John Henry Foster team made the two-hour trip from St. Louis to Mt. Zion, installed and configured the Delta controller in Green Valley’s cart, and drove home, all in the same day.
John Henry Foster sales representative and certified fluid power specialist Mark Certa notes, “Once we had it set up, Green Valley could go into Delta’s software and change that steering/speed relationship on the fly, like in two seconds, just by dragging points around on the curve.”
While vastly simplified on the surface, this ease of use is enabled by a lot of hard work on Delta’s part. The company spent many years refining its Windows-based RMCTools software, which encompasses a range of time-saving features and capabilities, including the Curve Tool.
In addition, Delta invests in creating the customizable source code necessary for its controllers to communicate with other devices. The controller manufacturer has amassed a considerable library of sample programs for its own as well as third parties’ controllers and accessories. Without this library, available for free to developers, RMC integrators may need to write their own code from scratch.
Despite these advantages, even Delta’s RMC setup still wasn’t quite plug-and-play simple (Figure 2). The controller code needed tweaking to the mold cart’s specific configuration. After building the cart from the ground up and handling all of its nonsteering programming, Green Valley still had to invest time in on-site development, testing and validation of the steering system. Green Valley engineers state the curves computed by John Henry Foster and Delta saved loads of time, but there was still a minimal phase of trial-and-error refinement. What was shown on the screen wasn’t always entirely what played out in real life, and so some adjustment was inevitable.
Figure 2: Technicians work on the RMC200 installation.
Trusting the track record
The automotive client’s successfully completed mold cart marked the third project in which Green Valley turned to John Henry Foster and Delta Computer Systems (Figure 3). Not long after the mold cart, though, Green Valley had another project that needed specialized two-wheel steering, which provided another application for Delta RMCs. Green Valley had five days to get the motion control configured. The company turned to Delta’s support department for assistance and had all the needed code in hand the next day.
Figure 3: The automotive client’s successfully completed mold cart marked the third project in which Green Valley turned to John Henry Foster and Delta Computer Systems.
John Henry Foster prioritizes several factors when selecting motion control solutions, including ease of use, feature depth, precise movement and steering, and exceptional end-user support. Because of these criteria and others, Delta remains among the few vendors Green Valley and John Henry Foster prefer as new challenges arise.
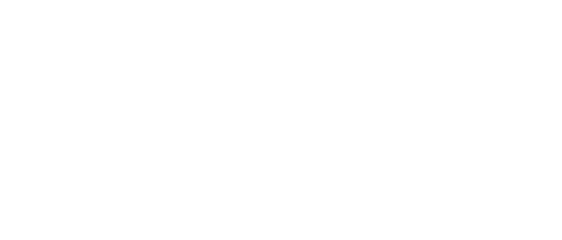
Leaders relevant to this article: