In anticipation of consumer preferences the following spring, a commercial greenhouse owner grows large quantities of those plants. The buyers want bigger flowers, better quality and more variety from their floral purchases (Figure 1). However, to remain profitable, the challenge is to grow a better quality product without increasing costs.
Bigger baskets
Figure 1: Buyers want bigger flowers, better quality and more variety from their floral purchases.
(Source: Control Dekk)
What’s your moisture?
Figure 2: By watering each hanging basket to its required moisture level, the plants are uniformly of better quality, leading to higher sales and less waste.
(Source: Control Dekk)
One way to improve quality is to add automation. This also can help to create a better product as consistency improves quality.
In this application, by watering each hanging basket to its required moisture level, the plants are uniformly of better quality, leading to higher sales and less waste (Figure 2). This also reduces production costs due to a more efficient process, which eliminates water waste. Simple monitoring of the process provides data for evaluating plant quality improvements.
Consistent product quality is important to ensure plants can be sold. This can be especially challenging when dealing with different varieties of flowers. Even identical baskets may not need the same amount of water due to differing conditions by location in a greenhouse. For instance, each basket may be exposed to different air flow, temperature and sunlight, which impacts moisture loss.
Examination of baskets grown using the timed watering method shows that there are often large weight differences between baskets. One test showed basket weights varying 3-6 lb each, indicating a huge difference in soil moisture. After installation of a control system, called Oasis automated watering system, the basket weights even out after just one pass (Figure 3).
Water weight
Figure 3: The Oasis system weighs each basket as it passes on a cable conveyor and feeds the information to the PLC, which adjusts the amount of watering.
(Source: Control Dekk)
Plant the seed to grow quality
Stress-free growing
Figure 4: Knowing each basket is going to be watered to exactly the same weight takes a lot of stress off the grower.
(Source: Control Dekk)
Control Dekk is a control engineering firm in Jenison, Michigan. I’ve spent decades designing irrigation systems that help commercial growers to improve their operations. In 2014, young entrepreneurial growers and Control Dekk partners Jared and Jordan Dekker wanted to find a better way to water their nursery’s 12,500 hanging plants. The Dekker brothers were seeking an innovative way to use automation technology to solve problems such as increasing costs and inconsistent product quality.
Knowing each basket is going to be watered to exactly the same weight takes a lot of stress off the grower (Figure 4). The grower has the peace of mind that all plants are intelligently watered. Demonstrating the importance of watering consistency has helped us open some eyes and close some sales. Some people have expressed an audible disbelief that inconsistent watering is happening in their greenhouses. It‘s been the same situation everywhere we went.
Introduction to a new market
Commence conveyor
Figure 5: When the grower determines that baskets need water, the conveyor is started.
(Source: Control Dekk)
Conventionally, many floral baskets are hung from pipes placed throughout the greenhouse. When the grower determines the baskets need water, a valve is activated, watering the entire line for a set time using incorporated drip lines. Other facilities have cable conveyors from which baskets are hung. When the grower determines that these baskets need water, the conveyor is started (Figure 5). As each basket passes a single watering station, a switch is activated that causes that basket to be watered for a set time.
The problems with these methods have been labor-intensive and inconsistent product quality due to over- or underwatering. I knew the solution was to design an intelligent, automated irrigation system that could customize watering for each basket based on its individual needs for greater, more consistent yields.
To break into a new market with a totally new product, the system needs to be at a cost level where people are willing to try it. Once they try the Oasis, they fully see its benefits and are willing to invest (Figure 6). To try something new, it requires some confidence in ROI, so the price point is important.
ROI proven
Figure 6: Once customers try the Oasis, they see its benefits and are willing to invest.
(Source: Control Dekk)
By choosing a Schneider Electric control package, I have components with plenty of capabilities at a reasonable price, creating high value that is worth the investment. Greenhouses operate on very tight budgets, so it’s important to bring value and demonstrate profitable results. Even growers with stationary basket lines have been eager to switch to cable conveyors because the new Oasis system would make the entire investment worthwhile.
Commitment to safety
To protect the entire system, the control design includes an emergency-stop button, a power disconnect and breakers from Schneider Electric. While not common in greenhouse applications, this level of safety and component protection reflects our commitment to providing a safe and high-performance product.
I feel strongly about the safety and protection of the Oasis devices and components. It has added a little cost to the system, but it’s the right decision to prevent damage and premature wear. Without it, I wouldn’t be comfortable standing behind its reliability.
Solution
In 2016, Control Dekk introduced the Oasis automated watering system, which measures and controls basket weight to precisely manage soil moisture and improve overall growing results for hanging baskets (Figure 7). We partnered with Schneider Electric to design a watering system that was reliable, simple to operate and cost-effective.
Introducing Oasis
Figure 7: The Oasis automated watering system measures and controls basket weight to precisely manage soil moisture and improve overall growing results for hanging baskets.
(Source: Control Dekk)
Once a grower sets the pre-determined weight desired for plant watering on a Magelis touchscreen, Altivar drives precisely move the cable conveyor lines full of hanging
baskets. When the baskets reach the Oasis module, a sensor measures each basket’s weight and reports it to the Modicon PLC, which opens a water valve for the time needed to achieve the grower’s target basket weight.
Logic as needed
Figure 8: A small and modular Modicon M221 Nano PLC controls the automated watering system and its multiple cable conveyor lines.
(Source: Control Dekk )
The Magelis HMI has an intuitive screen that requires little operator training. After watering, the HMI displays feedback that can help growers evaluate whether to make changes to the line. Vijeo DesignAir software replicates the Magelis screen on a mobile device, such as a smartphone or tablet, allowing growers to monitor and control the system remotely.
The cable conveyor lines are motor-driven using Altivar 12 variable frequency drives capable of operating on 120 Vac and can be adjusted using Modbus communication protocol.
A small and modular Modicon M221 Nano PLC controls the automated watering system (Figure 8). It has enough logic to control multiple conveyor lines in a greenhouse while taking minimal panel space. All control system components are housed in a nonmetallic enclosure that resists rust and protects against the greenhouse environment.
Having all that control in a small footprint is especially advantageous because greenhouse growers want to keep panels small to avoid blocking sunlight. I can add capabilities without increasing size by easily plugging in analog and digital modules to the PLC.
The Schneider Electric brand name has been beneficial to our sales efforts because customers’ maintenance technicians are comfortable with its products, service and support. Schneider Electric has been more of a partner than a supplier. Technicians spent a lot of time helping me figure out the software for Oasis, which saved a lot of time.
ALSO READ: Accurate fishing begins with lights-out manufacturing
Continue Reading
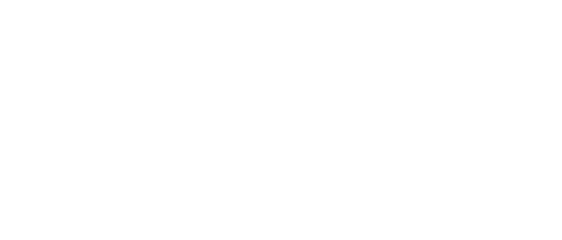
Leaders relevant to this article: