Programmable logic controllers automate brake-caliper assembly operations
Carlisle Brake & Friction (CBF) in Bloomington, Indiana, manufactures high-performance and severe-duty brake, clutch and transmission equipment for OEM and aftermarket customers in the mining, construction, military, agricultural, motorsports, industrial and aerospace markets.
Figure 1: The SA-10 bench assembles emergency brake calipers for Volvo and other large truck companies.
(Source: Dakswan Automation Systems)
Its products include hydraulic brake systems, transmission disks, clutch facings, brake rotors, torque converters, brake pads, hydraulic controls, master cylinders and similar products marketed under trade names such as Wellman Products Group, Carlisle Industrial Brake & Friction, Hawk Performance, Japan Power Brake and VelveTouch. CBF has 11 manufacturing facilities in the United States, United Kingdom, Italy, China and Japan. With more than 2,000 employees, CBF provides products to more than 100 original equipment manufacturers in 50 countries.
CBF had automated one brake caliper assembly bench at its plant in Bloomington, Indiana with a PLC. However, the installed PLC was unreliable with finicky outputs that didn’t always work, and CBF had trouble finding parts for it. CBF wanted to automate another assembly machine but didn’t want to use the same PLC, so it called upon us at Dakswan Automation Systems for help. We recommended replacing the existing PLC with an IDEC PLC, and automating the manual machine with another IDEC PLC.
Brake caliper assembly
Figure 2: The SAHR assembly bench handles more complex brake calipers than the SA-10.
(Source: Dakswan Automation Systems)
CBF assembles emergency or parking brakes for big truck manufacturers such as Volvo and Caterpillar. It uses a semi-automatic process where the operator is required to perform light assembly work.
The SA-10 assembly bench was already automated, but it needed a more reliable PLC (Figure 1). The previous PLC failed on a regular basis and wasn’t supported very well by the manufacturer.
The SA-10 bench consists of multiple stations to assemble an entire brake caliper system. The system first presses a magnet into the piston using a 600-lb pneumatic press. It applies a few O-rings, and then presses the piston into the cylinder using a 1,500-lb press. A pneumatic tool then tightens bolts in the caliper body.
The system loads springs on the piston, and a vision check by a Cognex camera confirms presence. When the part passes the inspection, it drops springs on the piston using a mechanical assembly actuated by pneumatic cylinders, and then applies and tightens the cap on the cylinder using an Acradyne torque tool.
Finally, it performs an air-leak test using a CTS air leak tester, and marks the part using a Telesis pin stamper.
The spring-applied, hydraulic-released (SAHR) caliper assembly bench assembles four different types of brake calipers—all essentially parking brakes for big trucks—following similar assembly operations (Figure 2). These operations are a little more complex because three of the caliper types have double cylinders instead of one, and the SAHR bench has a hydraulic testing unit, as well as an air leak tester, and two torque tools—Atlas Copco nut runners—to tighten the cylinder caps.
The SA-10 was previously controlled by another PLC, and the SAHR was a manual line that CBF wanted to automate.
PLC automation
Figure 3: A new PLC replaced the original on the SA-10 assembly bench.
(Source: Dakswan Automation Systems)
Replacing the existing PLC on the SA-10 line was a relatively simple matter. Dakswan installed an IDEC FT1A PLC, connected it to the existing 40 discrete I/O points and programmed the PLC to follow the existing control scheme (Figure 3).
Automation for the SAHR line was designed from scratch by Dakswan. The SAHR has 80 discrete I/O and four analog I/O, and, while the operations are similar to the SA-10, additional programming was required.
Figure 4: The two nut runners connect to the PLC via Modbus TCP.
(Source: Dakswan Automation Systems)
In the SAHR line, parts are put on a pallet. The pallet is on a rail so it can move from station to station. At the first station, the operator logs in and selects the type of part to be assembled. As with the SA-10, a magnet is pressed into the piston; sealant and O-rings are added; the piston is pressed into the cylinder; and springs are scanned by the camera and assembled into the caliper.
Because it assembles different parts, the SAHR has two Atlas Copco nut runners that are used to tighten the cap according to the part type. Both are connected to an IDEC FC6A PLC using Modbus TCP (Figure 4) to communicate data between the two controllers. After tightening, the part is moved to the pressure test zone, which does a low-pressure air-leak test using a CTS air-leak tester. Next is a high-pressure hydraulic test. Once the part passes these tests, it’s marked with a Schmidt pin stamper.
Machine operations
Before we built the SAHR bench, CBF used different machines for each part of the process, such as a press, a hydraulic tester and an air leak tester. There was no automated vision system quality check, no pin stamper to mark the part, no automatic torque tools and no logging of data. The whole process took more floor space as the machines were scattered.
CBF would carry parts in a cart from station to station. It was a manual and very inefficient way to build the calipers. We integrated all these different machines, as well as other machines which didn't exist in the manual process, into a single bench. This bench can produce four entirely different types of parts, and different variations of those parts. We built this new assembly machine from the ground up.
We started from the specifications of the parts to be produced and processes to be performed. Then we combined the common processes and divided the assembly bench into stations. We talked to operators about the processes and incorporated feedback from them to make the whole production process very operator friendly and less fatiguing.
Data and control
Figure 5: The HMI displays data from the PLC, allowing operators to visualize and follow the assembly process.
(Source: Dakswan Automation Systems)
On both assembly machines, the PLCs collect data from different devices, including torque tools, an air leak tester and a camera. The PLC collects data at each step of the process for quality-control purposes. CBF can trace back a lot of information from the part number and serial number on the part just by going through the logged data. This data is stored on an SD card so that it can be transferred to a PC in CSV format, allowing CBF to visualize the data using Microsoft Excel.
The IDEC HMI is an essential part of the control system (Figure 5). We used the HMI to visualize the whole process and to show assembly and test steps to the operator. The HMI also communicates with a barcode reader for an employee badge scan so the logged data can be associated with the operator on duty.
Operators can see the process flow on the screen, can see what steps have been done and can see what steps are yet to be completed. Some screens are password-protected so only a manager can see them, providing the required level of security.
Programming the IDEC PLCs was relatively easy. IDEC has a straightforward programming procedure, and Dakswan has built many machines using IDEC PLCs over the past few years. We are very familiar with the controller and related programming.
ALSO READ: New technology pushes machine smarts to the edgeÂ
Installation and operation
Dakswan engineers installed both systems, started them up and trained CBF operators. We did the SA10 first, and it took about a month for the complete project. The SAHR was a bigger project; it took two months.
Previously, brake calipers assembled on the SAHR machine were entirely built by hand. Now, the process is semiautomatic and well-integrated. On both machines, there’s less fatigue for the operator as a lot of the heavy lifting and moving of parts is now handled by the machines. The overall cycle time has been reduced significantly and build quality control has become much easier to monitor.
Dakswan is in the process of automating additional assembly machines.
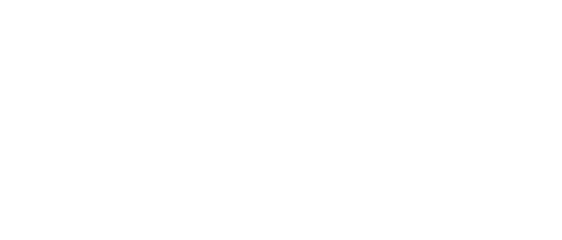
Leaders relevant to this article: