The general health of the programmable logic controller (PLC) market is a thing to behold.
According to Frost & Sullivan, the global PLC market has witnessed positive growth across all regions. The market, which experienced a strong decline in the early part of the decade, has bounced back strongly and is expected to reach $14.58 billion in 2018, up more than 40% from five years earlier. This growth includes the mature markets of North America and Europe, where uncertainty about economic standing had precipitated the earlier decline. Of particular interest is the Frost & Sullivan note that “the small and medium PLC segments will be instrumental for market development.” Those segments are the domain of traditional PLCs.
Much has been made in recent times about the impending demise of PLCs, expected to meet their end as the inexorable digital advance renders them obsolete with the advent of process automation controllers (PACs) and more advanced computer-based controls.
From the bottom up
Chris Elston, senior controls engineer at Fort Wayne, Indiana-based Yamaha Robotics, says that PLCs remain extremely relevant. “Probably 95% of machine builders still use PLCs as the controller of choice when they design a piece of machinery,” he says. “There really aren’t a lot of people out there who have switched over to something like PACs or PC-based control or anything of that nature.”
One of the reasons there hasn’t been an overwhelming rush to implement new control technology at the plant level is that many end users aren’t positioned to support it at the business end of things. “It can be boiled down to this: There’s a lot of skill set out there in the manufacturing industry, particularly with maintenance personnel or automation technicians, that is oriented to using ladder logic,” says Elston. “Most of them don’t understand a scripted language, so they are comfortable with working with PLCs. It’s a workforce issue at that level.”
Figure 1: End users’ familiarity with PLCs and their programming will drive continued use.
Source: Business Industrial Network
Don Fitchett, president of St. Louis, Missouri-based Business Industrial Network (BIN), underscores this point (Figure 1). “On the automation side, a lot of OEMs want to push ‘the end of the PLC’ idea; but it’s not going to be the end because the end users drive the market,” he says.
Fitchett compares the current situation to the vendors’ introduction of soft PLCs two decades ago. “When the industry came out with soft PLCs and pushed that approach, end users went out and bought any old computer instead of industrial computers. So when things collapsed, they pointed the finger at soft PLCs and went back to legacy PLCs,” he says. “Even though vendors still sell soft PLCs, they’re not pushed anymore because end users pushed back. A similar situation exists with the process automation controller and other new technologies for the entire plant. They’re not user-friendly for maintenance personnel.”
MORE: A look at PLCs, yesterday and today
The fact that manufacturers are finding the depth of the skilled labor pool a significant issue at this time only increases the impact of bottom-up resistance to switching out PLCs. “It’s really an issue of education, and also a generational one,” notes Elston. “Many machine builders are really cutting edge, but the issue with adoption is one of support after the fact. There is always a lag time between builders and users, and end users are typically reluctant to change control platforms. Maintenance personnel will even put PLCs back after they are switched out. They’ve been doing that for years because the PLC is something they have deep experience with and understand.”
Application breadth
“PLCs have been around for a long time,” explains Kevin Romer, product manager at Advantech America. “They work. They get the job done. There are a lot of people in the field that have familiarity with PLCs and know how to use them, so it’s not surprising that they are so broadly applied in industrial automation.”
Industry analysts at ARC Advisory Group and VDC Research estimate:
• 80% of PLCs are used in small applications (1 to 128 I/O points)
• 78% of PLC I/O is digital
• 80% of PLC application challenges are solved with a set of 20 ladder-logic instructions.
These statistics support what some have called an 80/20 rule: if 80% of applications incorporate simple digital and analog control, the boundaries of control applications are being pushed by a 20% minority. This ratio acts to preserve the viability of traditional PLCs.
“A lot of end users are less interested in PACs than PLCs because of the PLC’s simplicity,” says Romer. “They say that PACs and more advanced controllers are complicated. A PLC is simple. They know it and have a long history with it. From this perspective, they don’t see key advantages to changing out PLCs.”
Another reason for the resilience of PLCs is the robustness of the hardware, says Elston. “Almost anyone who has worked with something that has a hard drive in it has experienced some kind of failure with the drive,” he says. “Just remember the famous ‘blue screen of death.’ Those kinds of experiences don’t lead to comfort, whereas PLCs are extremely robust, resistant to environmental threats, such as vibration, and have set a standard in terms of interfacing. There’s a vast array of compatibility built into the neatly designed package.”
At a basic level, the simplicity/complexity paradigm can be used to determine where PLCs are likely to remain the choice in machine-building applications. Consider Yamaha. It isn’t known for big six-axis robots; it does a lot of single-axis robots that move products from point to point. They are relatively inexpensive—less than $2,000 for everything, including mechanical assembly—and provide a set of add-on instructions that a user can program in ladder logic.
“This setup does a couple of things,” says Elston. “If most of the industry has the capability to use or wants to use ladder logic, they can be intimidated when they see a robotic come to their floor that requires more exotic programming and so are reluctant to change. Our approach eliminates this.”
BIN’s Fitchett says the manufacturing industry will be the last to come around to networking all of their assets, and this will keep the PLC a major player in the sector (Figure 2).
Figure 2: The manufacturing industry will be the last to come around to networking all of their assets, and this will keep the PLC a major player in the sector.
Source: Business Industrial Network
“Things like strappers will be networked because they need data from other machines in the plant, for example, to know the size of the product coming down to be strapped,” he says. “But in small manufacturing, presses will be a stronghold for PLCs, because of the cost of upgrading and because the need to interface isn’t as high. A simple press with a cylinder going up and down doesn’t have the need to transfer data to other equipment.” Such applications will retain the legacy PLC, which lasts decades without the need for replacement.
Moreover, many companies have invested many man-hours and dollars in sending their personnel to schools and are much more comfortable in adding assets that can be programmed in a familiar environment. “Most of the time we see that comfort in ladder logic, in Allen-Bradley or Siemens or Omron, depending on what area of the country we are in,” says Elston.
Cost considerations
Michael Tiller, general superintendent with an engineering, construction and fabrication services company, says that PLCs continue to provide a combination of low cost and functionality that still makes them attractive choices for the end user. And heavy use in process applications often will drive acceptance and longevity in discrete manufacturing, as well. “There are some companies such as Triangle Research that have built a lot of functionality into legacy PLCs, enabling networking without a lot of programming skills,” he says.
Tiller cites his work with Oklahoma-based Chaparral Energy, a privately owned company that has grown to become a major energy player in the mid-continent region, with more than 1 billion barrels of oil equivalent and approximately 480 employees. Tiller designed solutions for a variety of Chaparral applications at its Ponca City, Oklahoma, facility. “They are going to stick with the PLC everywhere, including a couple of PLC-based edge devices that I’ve put in,” he says. The facility uses PLCs for applications ranging from process skids to tanks and tank arrays.
“One reason they chose the legacy PLC solution was because of cost advantages,” says Tiller. “Compared to more complicated solutions, it was a magnitude less expensive. They do the job. There’s no need for expensive software packages, and regular electricians can program them because there’s no high-level language involved.”
The low initial investment clearly provides strong support for the ongoing use of legacy PLCs. “Buying a legacy PLC will be at least one-third the cost of newer technology,” says BIN’s Fitchett. “It’s three times higher to buy a PAC than a PLC. For example, consider Allen-Bradley’s SLC 504 PLC. It can handle 95% of all industrial applications, and it’s around $3,000 versus up to $20,000 for a PAC.”
Advantech’s Romer says the people involved are key in application development. “It really depends on the person,” he notes. “If you’re targeting an electrical supply house or electricians, they won’t use anything but a PLC. If they’re involved in specification, PLCs will be specified in.”
Timeline projections
While there are compelling reasons the traditional PLC has remained so prevalent, change is inevitable, as technology such as cloud-based solutions and the Internet of Things (IoT) begin to move more prominently into the manufacturing ecosystem. “There is a convergence of price, functionality and power that is beginning to enable the IoT in the manufacturing sector,” says Tiller. “This is starting to be embraced, but there remains a real learning curve that average users of automation need to climb to be able to program this technology, to put systems together regardless of implementation scope and size.”
Beyond that, some reliability and stability issues linger from earlier experiences with computer-based controls—something that still contrasts to the long history of PLC performance. “People choose PACs or higher technology if they need really high speed or machines to communicate to each other. But even in highly regulated plants, such as nuclear power facilities, if the machine is stand-alone, there is less maintenance, less overhead, and higher reliability with PLCs,” comments BIN’s Fitchett. “There’s also a concern among end users about being more OEM-dependent with the newer technology.”
Elston notes that certain industries, such as medical-device manufacturers, will be early adopters of new technology because there are stringent mandated regulations to meet. At that point, PACs or computer-based control is a better choice, because of the need to interface databases with systems such as MES or ERP. In these cases, the PLC is problematic because it doesn’t easily lend itself to such integration.
“In five years we will see a significant market change due to cloud and IoT scenarios,” predicts Advantech’s Romer. “Security is a bit of a pushback, but those concerns should be overcome. I wish I could say the switchover from PLCs would be greater than half, but I think it will be less than that. In the end, it will be end customers requesting features that will drive the change.”
Both Tiller and Fitchett agreed with the five-year timeframe. But Romer concludes with a reminder of how resilient PLCs have proven: “`Ten years ago, they were supposed to be dead, but they’re still a force in the market.”
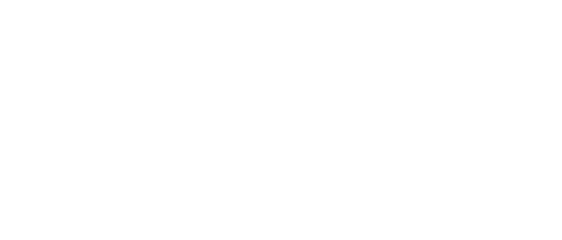
Leaders relevant to this article: