PLC-based system controls solar thermal installation in Mexican mining operation
Solar thermal is a highly effective method for large-scale energy production in geographies with high levels of direct sunlight. For industrial operations with significant heat consumption, solar thermal is often more cost-effective than fossil fuels, and it also results in lower carbon-dioxide emissions. Solar thermal is especially attractive in situations where land is plentiful and readily available.
At a remote mining facility in northern Mexico, heat accounts for an important amount of energy consumption at the plant. This is due in part to the heavy use of electrowinning, also known as electroextraction, a process used to obtain metals from ore. Electrowinning can require a tremendous amount of heat energy, and most copper mines using the electrowinning process rely on boilers to support this process. Because of the abundant access to land and nearly 3,000 sunshine hours available per year, solar thermal was an obvious choice for this site.
Jorgensen, a large-scale solar heating equipment and system provider, needed to develop a control system that not only maximized the solar heat production, but also efficiently managed and distributed heat to support a variety of processes.
From sun to process heat
Solar thermal plants generate process heat by harnessing heat from sunlight using flat plate collectors. Unlike photovoltaic (PV) systems that require semiconductors in arrays of solar cells to generate electric current, solar thermal plants use groupings of solar collectors to capture energy from the sun (Figure 1).
The solar energy is used to heat a fluid—in this case a mixture of water and glycol—circulated through the solar collectors. The heated fluid is then pumped to a heat exchanger, transferring the heat to plain water which is used for heat storage. The heated water in this storage tank is then distributed to various processes and heat consumers throughout the facility.
Forward-looking control
Jorgensen developed a control system specifically tailored for large-scale solar thermal plants. The S200 system controls the solar heat production, backup electric heat generation, and distribution to heat consumers throughout the facility. Consisting of a primary programmable logic controller (PLC), multiple remote input/output (I/O) units, and a human-machine interface (HMI), the system is highly flexible and reactive to the dynamic needs of the facility.
While programming for the electric backup and consumption systems is relatively straightforward, the solar thermal system introduces complexities due to its reliance on sunlight. The solar collectors are capable of heating the fluid to temperatures up to 95 °C; however the generated temperature for any project is based on the needs of the client and for optimizing the overall efficiency of the installation. Off-peak conditions, weather, and of course nighttime hours also need to be addressed.
For this reason, feedforward control principles are used to anticipate the system needs on cloudy days and optimize the output. For the solar thermal system, feedforward entails using the control logic to simulate conditions based on solar radiation, ambient temperature and the solar collector profile. Without utilizing these advanced calculations, the system would not react quickly enough to changing atmospheric and limited sunlight conditions.
Based on a history of proven performance and application advancements over the years, Jorgensen selected the AutomationDirect Productivity2000 micro-modular PLC, a powerful yet cost-effective solution that is equipped to handle the combination of feedback and feedforward controls (Figure 2).
Despite the advanced programming required for the application, the team found the free Productivity PLC development software platform intuitive and easy to use.
Night shift challenges: continuous operation for solar thermal
With mining operations running 24/7, the automation system faces the challenge of functioning continuously under widely varying conditions, even at night when the solar collectors are not generating heat. The electrowinning process requires the electrolyte be heated to 50 °C for metal extraction. To maintain a constant electrolyte temperature throughout the process, an automated consumption system is employed.
The consumption system supports not just the electrowinning process, but also the production of hot water for the copper cathode rinsing. Much like a typical commercial or consumer building, or even some cities, this method of district heating or “heat networks” is designed to distribute heated water to clients and processes throughout the site. At any given time, the number and volume of users can change dramatically.
As demand for heated water fluctuates, the consumption control system relies on a proportional-integral-derivative (PID) control feedback loop. The distribution manifold water differential pressure is the process variable, and the controlled output operates a series of pumps using variable-frequency drives (VFDs). More water users cause the pressure to drop, which requires the pumps to speed up. The opposite happens as there are fewer water users.
This arrangement allows the logic to closely regulate water differential pressure to the desired setpoint, because the controls responsively operate the pumps. In this case, the pump VFDs are advanced devices themselves, and a Modbus RTU serial connection is used for communication between the PLC and each VFD.
Monitoring critical systems
For any mining application, reliability is paramount, especially in harsh, dusty and remote environments. The Jorgensen S200 system incorporates data logging to support quick issue troubleshooting and alarm resolution. In addition, operators can monitor process status in the main control room using the AutomationDirect C-More 15-inch touchscreen HMI.
Designed for user-friendly operation, the touchscreen interface plays a crucial role in maintaining operational visibility. Users can tell at a glance how the system is running or if there are any alarms, and with the proper security credentials they can configure operational parameters.
DIY inventory check
During the design phase, challenges often emerge. For this solar thermal project, the global supply chain crisis created complications. A shortage of microchips led to extended delivery times on some components, and in this case one of the affected components was the remote I/O adapter. Rather than delay the solar thermal project, Jorgenson worked directly with AutomationDirect technical support during the development phase to find an alternative solution. The solution was to use a secondary PLC in a remote location for handling the remote I/O there, even though it was still controlled by the primary PLC.
One of the unique attributes of AutomationDirect is its consumer-facing website featuring transparent information about stocking levels. When Jorgenson identified the remote I/O delivery date as a risk, it was able to view real-time inventory levels on the website and select components that had the best availability for their project timeline. This resulted in swapping the remote I/O adapter with a second PLC that was affordable, was readily available and met the functional requirements and schedule needs.
AutomationDirect's support extends globally, facilitating ordering through the website without delays for quotes and proposals. This proved beneficial for Jorgensen, a global operator based in Denmark, but placing orders with delivery to Mexico. The AutomationDirect technical support team delivered a positive experience, highlighting the importance of collaboration and quick issue resolution in complex projects.
Flemming Jørgensen is the director at Jorgensen Thermal Solutions, operating in Denmark and Mexico. With more than two decades of solar energy experience, Flemming helps companies to use less energy through energy optimization and by generating economical, green and reliable thermal energy without burning fuel. He has a manufacturing engineering degree from the Technical University of Denmark.
Sponsored Recommendations
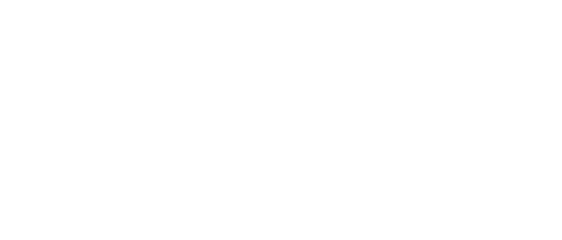
Leaders relevant to this article: