We need better accuracy now, so we're making a move to digital panel meters (DPMs) from our trusty analog panel meters. As we examine possibilities, it also looks like we could substantially reduce the number of different meters we use by using higher-end digital panel meters that offer optional expansion cards with a lot of extra functions, maybe to the point of needing fewer controllers. But it puts us in expertise areas where we haven't been before. Anyone care to share experiences about this possibility?
—From August'13 Control Design
SEE ALSO: Digital vs. Analog Panel Meter Choices
Answers
Think It All the Way Through
We build medium-sized ($1-5 million) wet-process machines for electroplating and similar wet-process operations. Our machines use numerous analog readouts and some process loop controls, and in past years we did use analog meters. We had a brief dalliance with DPMs, which lasted only a few years before we moved all of the analog readout functions, including process loop controls for temperature and such, into the PLC/HMI system on the machines.
We've relied on slip rings for many, many years to get essential signals from rotating segments of our equipment. Anyone who uses them in difficult, hot, dirty or less than perfect environmental settings struggles with maintenance and realibility. There's pressure for us to provide more data and more precise and reliable data from these points. This makes both operational and support issues a problem. There are wireless alternatives, but we haven't seen much evidence of them in tough, noisy environments. What do we need to know?
Send us your comments, suggestions or solutions for this problem.
Is it accuracy or significant digits and easier reading in the display that you need? If it is indeed accuracy, then that pretty much rules out any cheap DPMs. Look carefully at the specs for accuracy and at drift with respect to ambient temperature when making a DPM selection if accuracy is actually important to you. It is hard to beat those old mechanical Weston meters for accuracy over wide temperature range, year after year.
The high-end meters to which the questioner refers will be required if the goal is to reduce the number of different meter models used and if good accuracy is required. These meters are quite expensive and are also sometimes more accurate and more versatile than the $10 meters sold to the hobbyist market. If reducing the number of different models is important to the questioner, then I surmise that they must have quite a few meters to replace.
After about 10 meters, the total installed cost will in many cases be less to install a PLC with analog inputs, signal conditioning if necessary, and a nice HMI screen. In addition to replacing the analog meters, you get the following advantages for free:
- Control logic is already linked to the metered variables, so it is easy to write control programs based on those variables. There are no communications issues between "smart" meters or other analog input devices and the controller if the analog signals are brought right into the controller.
- Sophisticated alarm logic can be created. While some digital panel meters do have a simple alarm function, they lack the ability to mask the alarm at times when it is inappropriate for the alarm to be given, and no way to display whether an operator has acknowledged that alarm.
- Plaintext alarm messages can be generated, and the controller can even contact personnel through IM, e-mail, or cell phones in the event of alarms.
- Help scripts can be provided that are linked to specific alarm conditions.
- Adding datalogging is trivial.
- Calibration can be easier and in many cases can be automated.
- No hardware cost is involved to change the display style (bargraphs, rotating needles and direct numerical readouts all have their place in a good HMI), or to make the display color change prominently in the case of some alarms. Display sizes can be adjusted according to importance.
- Secure remote monitoring of the displayed values done via WiFi, Internet or cellular (and even alteration of setpoints or other process settings if permitted) from within the plant, or from the other side of the world, is possible with the correct choice of hardware and software options.
If those meters display the same process variables used by the control system, then there's an advantage to having the actual numbers come from the same source — only one calibration to do; no concern over the control system and the meter display disagreeing in the least significant digit; and immediate indication if the control system is no longer receiving the signal.
If the questioner's plant has a lot of analog meters, then to the extent that's a reflection of the age of the rest of their control system, it's a good bet they would see good payback from a complete control system upgrade instead of just swapping out the meters. Some outside expertise could be required, but the end result will be satisfactory for much longer than a patchwork approach. In some cases, better control and more user-friendly operator interface yield truly amazing gains in profitability when older systems are replaced.
Kim Ground,
sr. EE-controls,
Surface Finishing Technologies Div. of Technic
My Market Loves DPMs
The penetration and breadth of digital metering into the electrical distribution market has increased steadily and rapidly over the past few years. We're now at a point where it's desired to have metering down to the branch circuit level (15 through 100 A) in a lighting panelboard. The drivers for this vary from local/state legislation to the desire to become LEED-certified to simply wanting to understand the carbon footprint of a home or business.
There are many products and methods to achieve these results, including using expansion cards in digital metering infrastructure to address future needs such as Ethernet or relay inputs/outputs. While this can be a flexible method to approach branch-circuit-level monitoring, it might not always be the most cost-effective. Typically, these types of modular designs are more of an intermediate level meter, which require users to pay for the capability to have expandable functionality.
From a panelboard perspective, especially at a lighting panel level, the likelihood of needing these upgrades down the road is very slim. At this level, most users are looking to understand their energy consumption in order to make intelligent decisions on how to balance loads and bill their tenants appropriately. The key in this space is to provide what the customer needs as a "solution" that requires minimal amount of effort from an installation/implementation perspective. For example, with one of our main power and energy meters, a completely integrated solution is provided — the meter comes factory-installed into the panel complete with current transformers (CT) and wiring. This makes the installation process extremely clean and saves time — only requiring the contractors to terminate wiring as they would with any standard panelboard installation.
Taking the "solution" concept to the next level, enhancements are under development for our branch circuit monitoring (BCM) panels. With CTs already mounted and wired back to the main circuit board and integrally mounted into the panel for easy installation, the BCM panels also now include an integral cellular modem. This functionality allows for the transmission of energy data via cellular networks to the cloud and on to a web-based software platform, enabling customers to monitor the usage of a facility from a variety of devices. This alleviates the labor and capital expenditure of having to run wires all over a facility and the need to invest in servers and computers. It is the type of value-added solution that can be provided without requiring a significant amount of specialized expertise beyond what electrical contractors already are accustomed to in the installation process.
While it is easy to become overwhelmed with the amount of digital metering options available in the marketplace, there are solutions out there that are both cost-effective and skill-set friendly, and can help alleviate some of the major concerns around installation and implementation.
Lee Malmud,
product manager,
GE Industrial Solutions
It's Easier Now
In replacing analogs, which are signal powered, with digitals, one must consider the power requirement of the digitals as well as interface for serial communications, alarms, analog outputs and signal interface. And until last year, your choice was either modular DPMs or dedicated digitals for each function.
Well, not anymore. Due to advances in technology, now you can replace analogs directly with loop or ac/dc signal-powered digitals (not sensor powered yet) that have automatic, tricolor, bar-digital displays, detect when the signal fails, transmit the data serially, and require no maintenance or tapping on a stuck needle — all of it signal-powered just like two-wire analogs. And, if you want controlling outputs, then you supply the power to identical form and fit units. So, no matter what series you use, they all have the same firmware/hardware (other than mechanical). Once you know one, you'll know them all.
The rule of thumb for using signal/loop power technology is: if your signal can drive ~>10 mW, then use the latest technology that's HMI and MMI compatible.
Otto Fest,
president,
Otek
Accuracy Requires Digital
Analog meters, known largely for their "swing arm" capability, continue to serve our market very well. Think about, for instance, the gas gauge or oil pressure monitor in your car. It doesn't have to be 100% accurate — it just needs to be close — and as long as it's close, we can make decisions about when we need fuel based on what we see. Being plus or minus a gallon or two of gas is usually not a big deal until the gauge registers close to empty.
However, in today's environment, accuracy for process and machine control can be critical — and this is where a digital panel meter provides a more optimal solution. Digital panel meters typically measure to the tenths or hundreds of a unit. When measuring the flow through a pipeline, material levels in a tank or how heavy something is on a scale, digital meters can help maximize production efforts, as well as prevent costly mistakes.
For added control, many panel meters also offer plug-in option cards that provide management or communication features that relate to specific processes. Control outputs, for example, help to ensure that tanks are not over-filled or a dump truck is not overweight, while maximizing the space available. Communication capabilities allow the meter to be networked, so the process can be viewed and remotely managed.
In conclusion, while analog meters continue to serve the industry, digital panel meters provide a more integrated solution for today's demanding production requirements.
Jeff Thornton,
director of product management,
Red Lion Controls
Good Plan, Good Goals, But...
Good decision. The accuracy of a higher-end digital panel meter can be around ±0.03% of calibrated span, which is much better than the estimated readings and poor accuracy of an analog meter.
Reducing the number of meters you use is a good goal, but make sure you have digital displays everywhere your operators need to see critical process information. Standardizing on a high-end line of displays that supports 4-20 mA, 0-10 Vdc, thermocouple, RTD and other inputs, allows all of your meters to wire and program similarly. This speeds setup, programming and installation. Standardization also can make it less costly to have replacements on the shelf.
Make sure you consider how often you need different configurations, as it takes someone with the appropriate expertise to configure a meter with expansion cards. You'll also need to have meters and expansion modules in stock. If you don't want to carry a stock of expansion modules, you might as well order the meter that has the outputs and inputs you need for your specific application. In many plants, it makes sense simply to stock a meter populated with outputs. If, for example, the majority of your applications require two relays, but some need no relays, it's probably better to just stock a few two-relay meters than to stock both relay expansion cards and meters with no outputs.
A high-end meter family with a broad variety of I/O and extra features, such as alarming or math functions, can dramatically improve a process, and even eliminate other devices (i.e., temperature transmitters, loop isolators, data loggers, etc). Before making the decision to custom configure every meter using optional expansion parts, consider whether you are better off standardizing on a feature package rather than building every meter out of stocked modules.
Joe Ryan, product
marketing engineer,
Precision Digital
A Place for Analog
I feel that there is still a place for analog displays. Most analog controls were maybe accurate to around 5%, especially when the needle width was 3%. An analog system that used to be stable looks very unstable with three or four digits. Do you need 16-bit resolution with 65,535 counts? Analog is better for showing stability trends than digits. Now, with an HMI, you can show trends and multiple variables on a graphic. Say, on a tank, you can show level, temperature and pressure all in a compact space. Other digital advantages are networking, data logging and much better alarms: Hi, HiHi, Lo, LoLo, rate of change and setpoint-to-process variable deviation. A noisy process signal can be filtered in a variety of ways.
But, and there's always a "but," there's a learning curve for operators and maintenance. If you go the high performance route, such as RA's 5000 series, you will spend over $3,000 and a day just loading the programming software on each laptop. There are a whole range of options on the market now. Consider what you want and need.
Peter Koza,
instrumentation and controls engineer
AeroSoft USA
Digital. No Question
You should certainly go digital — all the way from the sensor. The future is digital. That is, no more analog 4-20 mA signal. Most transmitters today are digital — they have a microprocessor in them. Most panel meters (as well as chart recorders and control systems) are also digital, and based on a microprocessor. It doesn't make sense to use analog signals between them because, in the transmitter, you must convert from digital to analog, and in the panel meter (or system or recorder), you need to convert from analog to digital. In each conversion, accuracy is lost. There can also be a calibration mismatch between the transmitter and the panel meter (or system or recorder), so that when the transmitter output is 4.0 mA, then the reading is 0.5% or something else. Analog signals can also be distorted, such as limited, and this is very hard to detect.
Jonas Berge, director,
applied technology, Singapore,
Emerson Process Management
Not So Fast
Let's think about this a little deeper. It seems the original questioner actually still uses single-loop controllers, with displays individualized to the loop controlled. This is a pretty obsolete approach. Pretty much all of the process control industry has moved to the DCS realm now, with computer screens (usually called HMIs) replacing the old benchboard concept. This allows a much more systems-oriented approach to process visualization.
If you stay with digital panel meters, human factors engineering still shows the value of something like a bar graph indication, even with a smaller display, of the value to several significant digits. The human mind can process perception of change and rate of change much more easily looking at the size of a bar (or the position of a needle) than interpreting a rapidly-changing numerical display.
Jonas goes further, suggesting digital bus replacement for the 4-20 mA loop approach. I've been a proponent of this for about 15 years, but there is a learning curve associated with this jump in technology. I would suggest to the original questioner that it's a good thing to educate yourself on all of the options, including a shift to a DCS-style control system. In my experience, it's much easier to operate, maintain, and optimize the performance of a process plant with a DCS than with individual controllers.
John Petzen,
senior systems engineer,
GE Roanoke
Watch for the Weak Links
I think that it's important to remember that the digital meters are no better than the sending devices in the field. A 16-bit meter reading information from a 12-bit (or even an eight-bit) sensor or device doesn't give you much more accuracy. Just because the readout is digital doesn't necessarily make the information correct.
Randy Walker,
owner,
AttaBoy Automation
Time to Move Up
Actually, if your application is like one of the many infrastructure applications where you see 10-100 panel mechanical analog meters, you need to go to a controller and computer display — the PLC/PAC with SCADA display. Then, adding an additional analog meter display is often just adding rungs of logic to the PLC/PAC controller and using the SCADA GUI to add graphical representation. No more expensive analog meters. The meters in SCADA will never break; a meter on a computer screen is 100% reliable; driven by a PLC/PAC, it's 100% accurate; and it's zero cost besides your time to add logic to the PLC/PAC and cut-and-paste graphics into SCADA.
Doing it this way increases the entire system's reliability and safety. As with SCADA, you can view only the meter that needs viewing at that time. It can be automatically made bigger or highlighted during an alarm, and can be placed in the menuing system, etc.
When I still see control rooms, trains, power plants or process plants with all those analog mechanical meters, I don't know whether to laugh or cry.
Don Fichett,
president,
Business Industrial Network
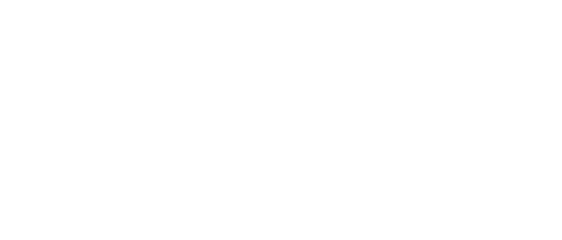
Leaders relevant to this article: