After working as a semiconductor process engineer, Hank Hogan hung up his cleanroom suit and now writes about process control and other technologies from Austin.
The same weekend the 2013 Super Bowl went dark due to a power outage, Russ Klisch, president of Lakefront Brewery, was hoping to avoid a somewhat similar fate. The Milwaukee-based craft brewer was installing a new filler, the machine that puts a beverage in a bottle.
Unlike the big game, Lakefront's switchover went off without a shutdown. This was, in part, due to the successful application of mechanical, electrical, control and software, or mechatronics, expertise. The new machine has proven effective, Klisch reports.
"Our uptime went from 80-90% to 99% runtime," he says. "We were running around 125 bottles a minute.
Now we're up to about 190 bottles a minute."
These results and how they were achieved illustrate some important points about mechatronics. Thanks to the greater integration of functions and more software, mechatronic systems are growing more complex. As a result, modeling is increasingly important. This greater upfront work can pay off in more capable systems and/or the completion of projects in less total time. But there are downsides to this approach, one being a need for greater modeling and software expertise. Such model-based design methods also take longer to produce hardware, and this lack of physical proof of progress can be seen as a disadvantage.
Better Bottling
In the case of beer bottling, the filling machine is important to more than the quantity of product produced. It has to be precise, ±1.5 ml. For a 12-oz bottle that translates to 0.4% accuracy. What's more, filling has to be done without dissolving oxygen in the beer, as too much of the gas makes for a flat and stale taste. The industry specification is that dissolved oxygen be below 100 parts per billion. There's also the need to ensure the safety of the beverage by preventing bacterial growth.
The new filler easily betters the oxygen content mark, according to Klisch. It's also more hygienic and accurate than the old machine.
Other improvements include a 50% or better reduction in the time it takes to change over from one product to another, which is an important benefit in the craft beer market. The new filler is more energy-efficient and more tightly integrated with other machines in the plant. Thus, when there is a problem, conveyors and other supporting equipment stop automatically.
The filler is a product of Waukesha, Wisconsin-based KHS USA, a machine builder with long experience in the beverage industry. Director of engineering Jeff Gilberg says the filler process involves pulling a vacuum on a bottle, purging it with carbon dioxide, filling it with a precise amount of the beverage, and finishing by injecting water. There are slight variations in the process between different types of beer.
Also Read: Mechatronics: Think Inside the Box
The new filler was smaller than others the company had built before, and it faced cost constraints while still needing to ensure product quality. That, in turn, demanded certain mechatronic performance specifications. "We had to make sure that the fit for the servo drives was proper, so we could have the right torque requirements for this small application and be cost-effective in doing it," Gilberg says.
Accomplishing this involved some simulation, using software from SolidWorks and PTC. KHS also used Rockwell Automation's motion analyzing and control logic simulation software, along with one of its programmable automaton controllers tightly synchronized with the same brand of servo drives and motors via an EtherNet/IP network.
The hardware provided motion control without a dedicated network, while the combination of simulation software allowed prediction of torque load to within 10%. Getting the simulation right was important, as having too small motors would keep the machine from working properly, while too large motors would be expensive and inefficient.
There are three servomotors on the machine that handle the motion. These motors are independent mechanically, but are synchronized electronically, so they appear to act as one, according to Gilberg. Valves and other functions on the machine are controlled using essentially the same logic and approach that bigger filling machines follow.
Since the successful rollout of the smaller filler, KHS has sold additional machines to several of the nearly 3,000 craft brewers in the U.S. One result has been dramatic increases in efficiency, with some end users getting as much product out in one shift as they previously did in two.
Growing Complexity
As this project shows, the software side of mechatronics is becoming more complex, something that Tony Lennon, industrial automation specialist with MathWorks, points out. The mathematical computing software company's platform for modeling and simulating dynamic systems is Simulink, which can help automate the chore of creating software. It does so by generating code from a model-based design.
This automated approach saves time and prevents errors, Lennon says. "In regard to code generation, Simulink can generate ANSI/ISO C code for microprocessors, IEC 61131 structured text for PLC systems and HDL for FPGAs."
That software situation could grow significantly more complex, thanks to the advent of cyber-physical systems. Such systems bridge the cyber and physical world, and they will have an effect on mechatronics.
"Similar to cyber-physical systems, mechatronics includes applications that continuously and dynamically interact with the environment through the coupling of distributed computational and physical components," says Ahmed Mahmoud, senior group manager for embedded systems marketing at National Instruments. He adds that cyber-physical systems combine elements of computation, communication and control. This combination of disciplines will become more important as machines and systems become more networked, which has implications for design tools. Mahmoud sees them as evolving to support cyber-physical systems, which, like mechatronics, demand multi-domain expertise.
Packing a Salad
Simulation model of a wind turbine combines electrical, mechanical and control disciplines in one design environment.
Thanks to the power of computers and the fidelity of simulations, an entire mechatronics solution sometimes can be tried out and verified before anything is actually built. A case in point comes from Pro Pack Systems. The Salinas, California-based company makes a variety of machines aimed at automating the secondary packaging process. Thus, Pro Pack's RoboLoader might take a closed, lettuce-filled, plastic tub and place it in a corrugated cardboard case, which would then be sealed and shipped to a retailer.
"The customer typically is packing the case by hand," Dave Zurlinden, president of Pro Pack, says of the company's target market. "We've automated that case packing."
According to Zurlinden, mechatronic components are used throughout the process. Empty cases that come into the machine arrive on a conveyor, and photosensitive circuits are used to gate this motion. Grippers hold a box steady, while tubs are packed in it. Servomotors drive mechanisms that correctly orient both the outside packaging and the tubs of produce.
Then there is a delta robot from Codian Robotics of Veenendaal, the Netherlands. Designed specifically for pick-and-place applications, the robot arm is capable of three-axes-of-freedom movement driven by servomotors. For lettuce in plastic tubs, no vision system is used, as that would add to the cost, Zurlinden says. Positioning to within 1/16th of an inch is required. Being off can lead to a crash, potentially opening up a tub, and sending lettuce everywhere.
The RoboLoader can handle 115 trays a minute, with the packaging machine typically running 20 hours a day, six days a week. The robot and the other elements have to do so in an environment suitable for produce. That translates to about 36 ºF and +90% relative humidity, and these cold and damp conditions dictate certain characteristics. "All the electronics enclosures need to be IP65 or better," Zurlinden says. "All the machine components need to be stainless steel or anodized aluminum.
A B&R Industrial Automation system runs the robot, with the entire control system developed and tested before the actual machine was built, says Karl Robrock. He's co-founder of San Francisco-based Automation Resources Group (www.automationresourcesgroup.com), which acts as a heavily engineering-oriented sales and distribution channel for B&R.
Pro Pack also had models of the physical machine, which the developers used for determining where obstacles to motion would be. The same models allowed path planning, so motion through physical space could be tested. Simulation allowed throughput, cycle time and process validation to be done before any hardware was complete.
"The entire process that runs on a servo drive is running in simulation in our environment, which is fun," Robrock says. "At the end of the day, that means Pro Pack can implement JIT [just-in-time] principles on new machine designs without affecting the quality of their product."
Mechatronic simulation and modeling are more complete and closer to reality than ever before, according to Derrick Stacey, solutions engineer at B&R. He says that B&R's Automation Studio is a tool that simulates control logic, and integrates with packages that mathematically model systems.
The ability to simulate with high fidelity is important because machine builders see an increase in customization requests, Stacey notes. As a result, systems are designed as modules that are added or dropped as needed, which requires that everything works together seamlessly.
The advent of modularity and simulation tools places certain demands on engineers and project management. In the old days, systems might be built serially, with the mechanical done first, followed by the electrical, controls, safety and software. "You really need to manage things in parallel," Stacey says of the new approach.
Make Things Easier
Inventor Kevin Maher tests GyroStim, a computer-controlled, multi-axis rotating chair that provides vestibular stimulation therapy for individuals with cerebral palsy, concussion, TBI, autism and other neurological conditions. This innovative device uses servomotors and drives and is the result of a mechatronics approach used throughout the development process.
Component vendors are taking steps to make such management easier on machine builders and system integrators. Alby King, applications engineer with Lenze Americas, points to his company's mechatronic modules for in-feed and dual-belt applications, which can be used for material handling and separation of products. The Lenze solution consists of a controller, inverters and motors. The functional components of the software are independent of the mechanical details, making it easier for users, who they can simply select the configuration best suited to their equipment.
Proper sizing of the drive is handled by the company's Drive Solution designer. King says, "This can rapidly perform in-depth analysis to easily size and choose between drives."
Models also can identify the impact of uncertain factors such as friction and elasticity. Such information along with other important data derived from models can simplify the setting control parameters and shorten the time needed to put a machine into operation, King notes.
Go For a Spin
UltraThera Technologies of Colorado Springs, Colorado, followed a different path to mechatronic success. The small company's GyroStim is designed for carefully controlled vestibular stimulation. This can help treat cerebral palsy, concussion, traumatic brain injury, autism and other neurological conditions. Subjecting patients to movement will help the inner ear and other parts of the vestibular system function more normally, thereby potentially restoring a sense of balance and other important capabilities necessary for daily life.
Before, such movement was a manual procedure. A doctor's instruction, for example, might be to place a patient in a swivel chair and spin them in both directions 150 times. However, securing a patient in a chair so that movement was safe could be difficult. In addition, such movement was manual and only along one axis, that of yaw. Being manual, the process was prone to a lack of control and repeatability. Also, the motion recipe could not be too complex, again because of the manual nature of the process. Automation and the design of a system addressed these issues by enabling safe, controlled, repeatable movement along the yaw and pitch axes.
The GyroStim is undergoing U.S. Food and Drug Administration evaluation for certification as a device suitable for treatment of neurological conditions, says UltraThera's president, Kevin Maher. It's also in use for pilot training and for research, with all of these different applications arising from the system's mechatronics. "So many new applications are possible because of the ability to provide precisely controlled motion to humans," Maher says.
A few years ago, Phoenix Contact faced a challenge. The industrial automation supplier used increasingly complex machinery to make its own products. Some of the manufacturing machines deployed had as many as seven PLCs, with some running the machine and others handling the interface with the rest of the production line. Dealing with that growing complexity loomed as a manufacturing issue.
"As we brought more of these highly technical machines in our facility, we realized we lacked the skills necessary to support these new machines," says Jerry Wise, technical training specialist. "So that's where we were lacking in our technician skills."
So the company developed a four-year, 8,000-hour training program aimed at producing technicians proficient in mechatronics, which required skill in mechanics, electronics, software and control. It did so in conjunction with the local educational system.
Several of the company's own technicians have been through the training. Results so far are positive, as can be seen in improvements to the process that include replacing a large linear drive on a particular assembly machine. Connected to a servomotor and encoder, the drive is responsible for all precision motion by the machine. Occasionally, the drive must be swapped out for repair, and that's when the training pays off.
"Before we had the mechatronics training, that operation took us approximately eight hours to complete. We noticed after the training we were able to do it in about half the time," says Keith Shumberger, mechatronics technician.
The time-savings and resulting line uptime improvement are attributable to the technicians’ increased expertise, Shumberger says. For instance, the time to configure and successfully start up the machine was cut due to greater knowledge about the sensors and how they interact with everything else.
Alby King, applications engineer with Lenze Americas, sees a need for such enriched education to be present beyond the technician level. "Engineering companies also need to work with area colleges to ensure applied engineering and mechatronics are part of four-year engineering curriculum beyond theoretical engineering," he says.
Genesis Engineered Solutions of Denver supplied the mechatronics expertise that went into the device. The challenge was to provide multi-axis motion with as few limits as possible, while maintaining safety, robustness, smoothness, quietness and cost-effectiveness, says Daniel Councilman, Genesis' engineered solutions manager.
Successfully meeting these requirements involved prototyping several servo drives. One of the reasons was that GyroStim uses a custom, PC-based drive control system, which had to be secure and flexible. The software also had to keep records such as speed, direction, acceleration and deceleration over time.
The need for flexibility and the lack of a predefined set of motions forced a decision about how to talk to the motion components, Councilman says. "In the end, we determined to use the most basic drive interface, as it gave us ultimate controls flexibility and allowed us to directly control the drive from the PC, while allowing the drive to provide precise, closed-loop control of the servos."
He adds, "We ended up using a simple Telnet session to send and receive data, thus keeping the interface simple and minimizing unnecessary overhead."
So the software takes the desired motion, decomposes it into the appropriate movement, and then builds a string from a lookup table. It then opens up a simple command window to the drive, something a person might use for basic operation. The command string is then sent to the drive, and the response is captured.
This approach allows changes to be made on the fly, with the system switching from a velocity to position mode, for instance, as needed. Precision is about a degree or so, according to Councilman.
This particular project followed a different path than is typical. Usually, Genesis does quite a bit of up-front planning, and performs simulations on the mechanical components and design. However, because of cost constraints, in this case, prototyping was done without mechanical modeling. The result was probably the same as would have happened if there had been the usual initial planning, but Councilman reports it did take longer to get there.
The Future
An intersection of technologies, mechatronics optimizes the tools required for easy and successful machine design by blending expertise in mechanical engineering, electronics, instrumentation, robotics, PLC computer systems and software-based engineering.
As for where mechatronics is headed, Nuzha Yakoob, Festo product manager, points to optimized mechanical design. She says the outcome can be systems with high-speed positioning, greater throughput, reduced energy consumption and a smaller carbon footprint.
Along these lines, Festo has kinematic solutions that operate off a single belt, making them light and compact, Yakoob says. She mentions another available lightweight solution: robots that can work alongside people in a collaborative production environment. Festo itself does not currently offer such robots, according to Yakoob.
Another trend benefiting from mechatronics involves the greater use by machine builders of multi-positioning systems. These allow products of various sizes to be handled on the same machine, an important plus on factory floors with limited space. Yakoob says achieving such a capability is only possible with a system that integrates mechanical and electrical components with feedback sensors, control electronics and software. "It can be programmed to adjust to different product sizes, so it provides that flexibility," she says.
An important mechatronic need and trend is educational in nature, indicates Mathworks' Lennon. "Experience with our customers shows that an important challenge is overcoming the silo effect," he explains. "Too often, development teams work in their own discipline, and they don't consider the impact of integration until the last stages of the development project, when prototype hardware and its software begin to come together."
Errors and mismatched requirements are easier to identify when system-level simulation is used, he says. That will be more straightforward with greater integration between CAD and high-fidelity, model-based design.
Finite element analysis methods can be used today to boost simulation accuracy. However, doing so can mean orders of magnitude increases in computation time, according to Lennon. That makes this approach too time-intensive to be routine. With greater computing power, though, that might no longer be the case, and system-level models would then benefit.
Kevin Craig, Marquette University mechanical engineering professor, echoes the idea that modeling of systems can prevent problems. Such modeling need not be overly involved and the simulations complex for an initial evaluation. "After all, he says, "if a system won't work in a simplified or an ideal case, it most likely won't work in a more realistic model or in a prototype."
Another value of a model is that it helps in understanding how a system works. It allows for such virtual changes as swapping out a drive of one size for another to see what happens. That, in turn, can allow engineers and others to gain insight into how to make changes to a machine in order to address specific problems.
The benefits of a model-based mechatronics approach are there, but so too are the old methods. These typically involve building a prototype and using that to verify a design, an approach that Craig says still has sway over machine builders. "Not only is this approach familiar, such methods also produce something tangible that can be used to judge an engineer's productivity and demonstrate a project's progress. So the real challenge in industry now is to get engineers to go from the design, build and test approach to this model-based, system design approach using physics and math." However, the situation could be changing, as industry responds to the increasing complexity of machines.
As Craig says, "The systems that we have are so multidisciplinary that there's really no other way to do this."
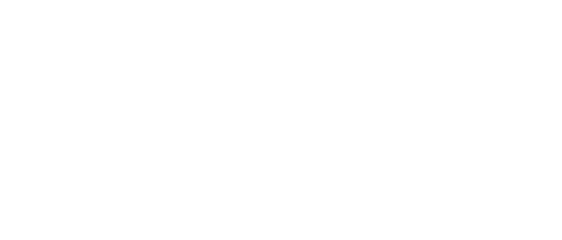
Leaders relevant to this article: