Unless your dear old granny made everything from scratch, the chances are good that the last pie you enjoyed had a crust that came from a machine made by Comtec Industries. Pies, pastries, tarts, cheesecakes, hors d'oeuvres and quiche all come with a formed pastry crust, and our machines form the crusts in commercial bakeries around the world.
We are a family-owned business that started out as a pneumatic fittings company more than 50 years ago. Somewhere along the line, my father was asked to assist with solving a problem related to pie crusts. He did, and my brother and I ended up in the business.
Our company has produced two main models of crust-forming machines since the 1960s. They're known to be strong, reliable and simple enough to maintain with a screwdriver and wrench. This is important because in the baking industry most maintenance people are responsible for many tasks. They're our jacks of all trades. Sophisticated electronics are not a typical skill set, and anyone designing machinery for bakeries needs to keep this in mind.
The previous-generation machines were largely standalone without a great deal of automation. This allowed Comtec to grow without building a worldwide cadre of support people.
Pie Crust: The Next Generation
As we began to plan for our next-generation machine, Comtec proceeded with two strategic thoughts. First, any new machine had to be easy to maintain. Our customers' core competency is producing culinary treats, not tweaking automation equipment. Further, machine setups, diagnostics and other important information gathering needed to be handled without adding dozens of field service people.
[pullquote]Our next-gen machine, Model 2900, is fully automated. It's hydraulically powered with a PLC, HMI panel and a number of sensors that measure temperature and pressure where the dies form the crust.
In addition, to meet our important objectives, we needed to think outside the box on topics such as machine diagnostics. It isn't enough to provide just a solidly running machine. Our customers' operating world calls for more extensive assistance, and we need to look at the whole operating environment.
A good example of what got us thinking about remote monitoring was a call several years ago from an anxious customer with a machine down. They reported their machine was taking more than two hours to warm up each morning instead of the usual four or five seconds. After several rounds of phone questions, the customer's maintenance person told us they had changed the oil that powers the hydraulic rams in the machine and replaced it with vegetable oil. Vegetable oil is what most of us would call cooking oil. Once this type of oil is heated, it congeals upon cooling, producing what looks like the solid grease that forms in the bottom of a frying pan.
Our machine uses a hydraulically driven die to press and hold the dough into its pan. To avoid any customer confusion, we designed our machine to use the most common form of hydraulic fluid available—the very standard ISO 32 that can be found in most auto parts stores. Apparently, we didn't communicate this strongly enough because adding cooking oil to the system is akin to using bacon fat in a high-performance racing engine.
Because the cooking oil solidified, each day the machine had to run long enough for the other parts to generate enough heat to turn this substance back into a liquid. It's a marvel that the machine survived.
It was these types of issues—ones that we simply couldn't anticipate—that told us we needed the means to monitor and log some of this information in the new-generation machine.
Costly Service
My brother Jim Reilly serves as Comtec's president. He also oversees the logistical details of taking care of machines in the field. "Our old line of machines are simple enough, we can trouble shoot them over the phone," Reilly says. "And, in a few rare instances for which onsite customer service was required, we would try to use a third-party service organization such as Hobart Service or other service providers in our industry to minimize travel costs. But even this strategy costs us $700-$1,600 every time we make a service call. Trips out of our Chicagoland headquarters cost double that, not to mention wear and tear on the person traveling and lost engineering time."
We invested some time to understand the potential trouble spots in the operation. Temperature and pressure histories in the machine are clues to locating trouble points. The combination of temperature and hydraulic pressure are important to ensure the pie crusts release from the molds. We accomplish this by applying an electric heater block between the machine and upper half of the die. This doesn't cook, proof or otherwise alter the crust; instead, it ensures the crust leaves our machine properly. Incorrect temperature especially results in a poorly formed product, manifesting itself in appearance issues. The consumer wants to see a perfectly formed pastry, not a broken-up pile of crust. In extreme cases, poor release can translate into jammed machines and lost production.
Control of Process Variables
In our environment, every recipe calls for a slightly different temperature. We monitor and build a history for both set point and actual temperature. Comparing the history allows us to determine if the customer is experiencing a regulation problem or an issue with one of two heating elements in the block. This can be a tricky situation for a customer in our industry.
We also measure the two most critical stages in the machine cycle and pull in historical time comparisons and build calculations along the way. "We log and compare hydraulic ram extension and retraction time," Reilly explains. "Because the extension cycle is made under pressure and the retraction is an energy-efficient, gravity-driven operation, changes in their relationship can indicate issues with the hydraulic pressures or with alignment."
Remote Possibilities
It was during an exploratory meeting on HMI devices with local automation distributor Standard Electric Supply (www.sescowi.com) that networking needs came under discussion. Standard Electric has extensive experience with communication schemes, so when the company realized we were developing plans to build machine environmental histories in the HMI, they encouraged us to check out the historical information storing capabilities of an eWon (www.ewon.us) solution. Further research on the eWon solution led us to a system for remotely accessing our machines via eWon's cloud service (Talk2M).
"Early on in our conversations, I realized the eWon 2005CD/4005CD was a nice match," says Jim Roth, sales engineer at Standard Electric. "It combines both remote VPN access with the Talk2M service and the ability to monitor and build histories with the I/O server and data logging features."
Secure Data Retrieval
Talk2M comprises connectivity services based on a hosted web application designed to connect users to their machines via the Internet. This hosted application acts as a broker and relays the communications originated by the users to their machines. Talk2M accepts connections from users as well as from their machines, so both parties can exchange data using tunneling technology.
"No incoming connections are made to the machines and customer network," explains Dominique Blanc, eWon's North American general manager. "Instead, the eWon industrial routers initiate the connection to the Talk2M server using either UDP or HTTPS, so we make it easy for IT people because no ports need to be enabled in their corporate firewall for incoming connections. The remote OEM specialist only can reach ‘his' devices—the PLC, HMI, drive, etc. —connected behind the eWon LAN side, and has no access to the rest of the factory network. Talk2M is designed to be minimally intrusive with the Open SSL/Open VPN protocol." Blanc adds that the information exchanged during the communication is encrypted (SSL 128 bits), so the data remains secure and only authenticated users can connect to the eWon units within the account.
"Each eWon industrial router connects exclusively to the Talk2M server," Blanc continues. "An authentication mechanism ensures that each eWon industrial router talks to the Talk2M server that has the same key. A similar mechanism ensures that each user can only communicate with his eWon units within his Talk2M account."
Blanc notes three steps for easy setup of remote access to machines:
- Create a free account using the eCatcher PC application, and manage users and eWon units within the Talk2M account.
- Configure the eWon unit to be registered in the account.
- Connect with one mouse click to the remote machine and get live support with the machine, including PLC, HMI, IP camera to support the end customer.
Food industry companies are particularly interested in securing their production to make sure nothing jeopardizes the quality of the product. Properly configured firewalls are the guardians that prevent non-authorized access to their network. It is difficult and time-consuming to change the firewall settings if the customer needs troubleshooting assistance.
With the eWon Internet router, the difference lies in the combined ability of eWon units and Talk2M service to easily set up a secure VPN tunnel between our support and the machine in the field. The IP address routing is in place, and we can reach the machine and perform needed support exactly as if we were standing by the machine. "The Talk2M service manages access control between users and the machines, and provides a unique time-stamp connection report that is key for this industry in order to keep track of any remote access to the machines," says Dominique Blanc, eWon's North American general manager.
Once it's running, the eWon unit can store historical information for later download and evaluation. "This is independent of the information we store inside the HMI panel," Reilly says. "Armed with this information, we can make the normal types of PLC changes, but we can do more. Fuses blown, temperatures, pressures and other variables are just as important as making programming changes on the fly. Again, this saves us travel expenses for easy issues."
The system also can schedule the connection time. Commercial bakeries run on tight schedules, so we need to know the best time for us to evaluate our machine's situation. The program lets the operator log the best time to access the machine into the HMI, with a note along the lines of "We end production today at 3:30 p.m." Once entered, this information is automatically sent back to Comtec to help us schedule our work load and improve the customer's machine uptime as a result.
"When it's necessary, we can add an Internet camera to the system to remotely watch the customer exercise the machine and evaluate the result," Reilly explains. "The capability is available, and helps us more quickly understand the customer's issue and shorten the resolution of most issues without expensive house calls."
Tasty Benefits
In a world where every second counts and efficiency is critical, we believe remote monitoring is a technology that finally has arrived. It helps us learn how our machines are applied and we can improve our machine to better fit customers' needs as a result of it. Our machines already have a reputation as long-lasting workhorses. But we can't just think about next year. Comtec has to look a long way down the pike. "Remote monitoring is not new, but the real breakthrough is how eWon technology makes it so easy to deploy and reach each machine in a customer's facility," Reilly says. "It answers IT compliance issues and machine control needs all at the same time."
In the baking business, downtime is expensive. With the Model 2900 operating at 3,600 crust pressings per hour, downtime could easily reach upwards of $7,000 per hour in lost revenue. With numbers like this, it's safe to say we will save our customers hundreds of thousands of dollars in lost production over the life of these machines. Moreover, the money we save our customers when we eliminate a field trip is just icing on the cake (no pun intended).
Continue Reading
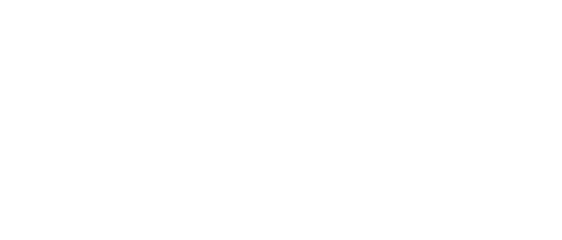
Leaders relevant to this article: