We farm out most of our repeat-design panel building work, but we often do the specials ourselves. It's been getting more crowded in many of these panels. Sometimes the simplest and shortest wiring arrangement means more heat generation around the controller and other sensitive components than might be wise. Any tips, best practices or software tools to share for optimal placement of components?
—From July '11 Control Design
Answers
Best Practices
Your problem contains two main issues for which we have best practices to suggest. For the first, which is that it's getting more crowded in many of the panels, the best practice is simply to put it all in a bigger box. That might sound callous or overly simplistic, but when it comes to panel building, like building a race engine, there is no substitute for cubic inches. If that is not possible, try using a deeper box with the same footprint, and mount components in multiple tiers. One trick is to have multiple mounting panels, on swing-out hinges, kind of like the pages of a book.
Another trick is to use two mounting panels, back-to-back in the center of the enclosure, with access from both the front and the rear, which essentially doubles the amount of component mounting space. If you can't go deeper, can you go taller? Or wider? The bottom line is, if you are adding more components, you need a larger box or you need to use the space in the existing box more effectively and efficiently.
Other space-saving tricks: Use encapsulated transformers and mount outside the cabinet (this also removes unwanted heat from within the cabinet); or omit the disconnect switch—the UL508A standard does not require one.
Larger boxes also have added thermal benefits, which addresses the heat issue. As a best practice here, if it isn't wise, don't do it. Again, somewhat simplistic, but without knowing the full story, we must assume this is a UL508A-listed industrial control panel application. That is a 40 °C standard, meaning the air surrounding the components cannot exceed those temperature limits at any time during full-load, steady-state operation, regardless of what the temperature outside the enclosure is.
There are numerous ways to control temperature around sensitive components. Make sure to adhere to the spacing recommended by the component manufacturer. In addition to keeping the control panel away from heat-generating objects, you'll need to keep heat-sensitive components as far away as possible from heat-generating components within the panel. Keep heat-generating devices together to make it easier to manage the heat.
Mounting heat-sensitive components in the lower portion of the cabinet will help to keep them cooler because heat will naturally rise to the top of the panel. You can mount components on the side wall of a panel if necessary to gain maximum air space/air circulation between heat-sensitive and heat-producing components, or even mount heat-sensitive components in a separate, isolated cabinet. Conversely, you can mount the heat-producing components (transformers, line reactors, VFDs, etc.) external to the panel. Raising components and mounting rails up from the mounting panel with standoffs is relatively inexpensive, and greatly improves air movement.
Provide cabinet vents if possible. If not, provide an air conditioner or other heat-mitigating device. Perform a heat calculation to determine the additional cooling (vent grills, fans, A/C unit, heat exchanger, etc.) needed to maintain internal panel temperature to within the components' maximum operating temperature range.
If using additional cooling, position components so as to not impede air flow or as little as possible to achieve maximum cooling efficiency.
Kenneth Wilson, Sr. Application Development Engineer,
Son Dinh, Industrial Control Panel Application Engineer,
Schneider Electric, www.schneider-electric.com
Err on the Cool Side
We focus very little on the physical placement of components; instead, we focus heavily on obeying minimum clearance specifications from the various component manufacturers. We also do a heat rejection analysis on every panel we build. If necessary, we mitigate the heat load with fans, air conditioners or heat exchangers. All of the major enclosure manufacturers have graphs and software tools to predict temperature rise, and these same tools will offer equipment to remove that heat.
In the heat rejection calculation, we use the maximum ambient temperature for the installation, the sum total of the heat rejection for every component, and the materials of construction for the enclosure, with stainless steel being among the worst for heat rejection. We verify that the temperature rise plus the maximum ambient temperature doesn't approach or exceed the maximum rating for the lowest-rated electrical component. If it does, we provide cooling. This analysis is quick, straightforward and easy to do. Important to remember: Electronics are happiest when they're cool, so err in that direction if the situation is marginal.
Jack Chopper, Chief Electrical Engineer,
Filamatic, www.filamatic.com
Power = Heat
Because enclosures can often be space-constrained and thermally challenging, there are a couple tips that we offer to our OEM and machine builder customers. First, we suggest that Power over Ethernet (PoE) should be considered. PoE offers power and data over the same Ethernet cable, eliminating the need for a power supply inside the enclosure as well as any related cabling. So you can reduce the amount of space you need and decrease the amount of heat produced. We see an increasing number of industrial devices coming online with PoE as manufacturers and end users are realizing significant benefits associated with this technology.
Reducing heat can be tricky, but a good rule of thumb is to choose devices with lower power consumption. Fewer watts usually mean less heat output. Choosing an energy-efficient product can pay off not only in the electric bill over time, but also in the reduction of heat inside an enclosure.
Sometimes there's just no avoiding the inevitable. If a PoE or energy-efficient model is not available or is price-prohibitive, you might have to go a more traditional route. Choosing products that are rated for extended temperature then becomes a must. Most industrial products will operate at up to 75 °C. Choose products that are temperature-screened for functionality before leaving the factory to ensure the highest possible reliability.
Unfortunately, lower-quality products operating at the higher end of the temperature spectrum usually don't fail catastrophically; instead they can intermittently send corrupt data. Troubleshooting this scenario is both time-consuming and costly.
Jim Toepper, Product Marketing Manager,
Moxa Americas, www.moxa.com
Hot Details
Heat generation seems to be a universal problem for panel builders. There are things you can do to alleviate this problem, though. For starters, look at what likely generates the most heat: the power supply. If you haven't already, consider using a new primary switch-mode power supply. These power supplies are much more efficient than linear supplies, thus creating much less heat. Additionally, they tend to be much smaller than linear power supplies, so you'll free up some panel space.
Look at components that generate heat. Although solid-state relays have a nearly infinite life span, they generate much more heat than their electromechanical equivalents, so you might want to avoid solid state if you currently use them.
Another option is to evaluate the way your components actually are wired. Most likely, they are wired via the traditional point-to-point method. Although this is most common and very inexpensive, it tends to create bulky cable runs that require wide wire duct trays. This takes up valuable panel space and begins to act as insulation within the panel, making it harder for heat to escape.
An option would be a "system cabling" approach. This method uses high-density cables that connect controllers to components. In addition to reducing wiring time, the high-density cables require much less space, therefore allowing smaller wire duct, and ultimately improving ventilation within the cabinet.
Those are some specific things you can look at when designing your panels. However, generally speaking, here is one great suggestion: Really do your research when you select products to use in your panel designs. The old adage, "If it ain't broke, don't fix it," may hold some truth, but new technology allows things that ain't broke to work better. Manufacturers always are working to improve their product designs. In turn, these products work much more efficiently than products did just five or 10 years ago. Usually, they consume much less power, and therefore dissipate much less heat. Often, panel builders simply specify what they are comfortable with and have used for years. Chances are there's a new version of that product that is much more efficient.
Jeremy Valentine,
Product Marketing Specialist,
Phoenix Contact,
www.phoenixcontact.com
Remove the I/O
The best-practice solution to eliminate overcrowding and many heat-generation problems inside a panel is to move components such as I/O and heat-sensitive devices to the outside. Even though the motor starters, which generate much of the heat, remain in the panel box, the sensitive components can be pulled and positioned in an area where there is less heat. Removing the I/O allows the size of the panel to be decreased and it allows you to distribute your I/O along your system, which in turn reduces engineering costs and aids in minimizing commissioning time.
The devices being pulled from the panel box need to be IP67-certified because components with the IP67 certification are rugged and manufactured with protection against the harsher environments outside the panel. This also allows more freedom in the placement of these components. An application we see is IP67 controllers that allow tabletop tools and fixtures not to need a panel but simply a steel plate with the IP67 controller, IP67 power supply, and IP67 I/O module placed on it. Up to 75% of the components that typically reside inside the panel then can be pulled out and be more flexible.
Some of the benefits of using IP67 components include decreasing the panel size, which saves hard wiring engineering time, and saving time typically devoted to testing the panel. Perhaps the greatest benefit to this approach is the ability to create generic control systems. The ability to extract these components out of the panel and use them in conjunction with one of several different open architectural industrial networks makes it possible to use the same configuration for many applications instead of having to set up a personalized control system for each application.
Mark Stremmel,
Business Development Manager,
Turck, www.turck-usa.com
Exhausting Heat
There are a variety of methods to exhaust heat from inside an enclosure. The issue centers on several factors, including the heat source, ambient conditions, component placement, and the amount of heat that needs to be removed.
For hazardous locations, temperature rise in the unit could be alleviated by several different methods, including using a certified purge/pressurization system, a hazardous-location air-conditioning systems, or an all-pneumatic vortex cooler. Each alternative has advantages and, in some cases, a disadvantage or two.
The tendency today in HMI/OIT solutions is a fanless design. These systems provide the user with a rugged, enclosed solution with great NEMA/IP ratings for dust and liquid ingress. The downside of that solution is limited methods to remove heat. Even with large display/touchscreen interfaces, the majority of the heat generated is from the back side of the unit, not the display. This means that all the heat is being stored in the enclosure. Convection and conduction are the only practical methods to remove heat.
In most cases, a conversation with your display or purge manufacturer is a great place to start.
Mike Mendicino,
Product Manager, Pepperl+Fuchs,
www.pepperl-fuchs.us
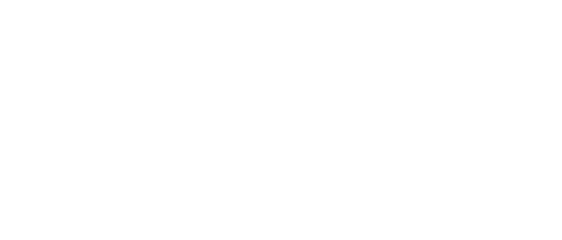
Leaders relevant to this article: