A growing number of potential new customers don't like that we use pneumatics to power some simple linear motion requirements. Simplicity is being pushed aside by users who don't want the air supply and maintenance hassles, and who aren't aware of the increasing comparable digital connectivity of many pneumatic devices. We'd prefer to keep it simple. Who's right?
—From September '10 Control Design
ANSWERS
Simple, Low-Maintenance
Even with advances in electric linear actuation, modern pneumatic systems still provide a simple, low-maintenance solution to linear-motion requirements. Basic components have decades of use in industry to support reliability numbers.
Modern upgrades in materials and interface components make incorporation into today's automation control systems simple. Newer materials and lubricants simplified installation and maintenance of pneumatic systems. Many of today's valves and actuators are permanently lubricated at the factory. Kink-resistant flexible tubing and push-to-connect fittings make installation and repairs a snap.
Today's pneumatic systems can use small, low-power solenoid valves that connect directly to the outputs of a PLC. Valve banks are also available that use several popular automation communication protocols. Reliable solid-state position sensors close the control loop with the PLC.
Pat Phillips, product engineer,
AutomationDirect, www.automationdirect.com
Electric Actuators Greener
The customer is right. It is more than the hassles of simply air supply and maintenance that push customers to electric actuator solutions. The more-subtle reason why customers push back on pneumatic devices has to do with environmentalism. Government policy and even politics force companies to limit or reduce air consumption and capacity.
The "going green" trend is growing roots and is here to stay, because air is expensive to use and air leaks are costly. Finally, there now is a reasonable ROI for companies when they reduce air consumption by switching to alternative electric actuator technologies. In addition, electric actuators offer much more flexibility, such as precise control of position and speed, advanced programmability, higher functionality that is consistent and repeatable, eliminating the need to constantly tweak the air flow.
Done right, the simplicity of an electric actuator is not much more difficult than a pneumatic device. What's more, the initial purchase price gap is closing as electric actuator solutions come down in price. Today, many of our machine-tool customers offer a pneumatic standard product as the lowest cost point, and an electric actuator option so the customer can choose.
Aaron Dietrich, product manager,
Tolomatic, www.tolomatic.com
The More Cost-Effective Choice
In general, pneumatics provides greater force density, meaning equipment size possibly can be smaller and lighter. Pneumatics can be more cost-effective. A good rule of thumb is that if two positions per axis of motion are required, then pneumatics is simpler and less expensive. When three or more positions per axis are required, then an electromechanical solution could be more suitable.
From an electrical connectivity standpoint, pneumatics can be just as easy to use/install, especially with components like modern fieldbus devices. Pneumatics also can be more suitable depending on the environment in which the machine will be used, because of the availability of intrinsically safe components. In washdown or corrosive environments, pneumatics can be mounted close to the location of the action, in places where electrical devices could not be used.
Pneumatics has been perceived in some circles to have a higher cost of ownership because of its use of compressed air. Modern best practices greatly reduce the operating costs associated with pneumatics. Correct sizing of components to the required tasks reduces unnecessarily high air consumption. Machine designers sometimes fall into the trap of repeating a previous design when those components are oversized for the application. Online calculators and configurators guide a designer to properly sized component selection.
Mounting components close to the actual tasks greatly reduces air line lengths. Optimal location of valving close to the actuators (sometimes even using cylinder/valve combinations) can reduce air volume required by up to 35%.
Using only as much pressure as needed for the task can reduce air consumption by 25%. This is achieved by pressure regulation of specific steps, such as lower pressure for the return stroke of an actuator—without compromising performance.
John Bridges, product marketing, Bosch Rexroth,
www.boschrexroth-us.com/brp
Understand Customer Needs
It's always important to understand customer needs. Typically, the customer concerns are influenced by many factors: cost, maintenance, performance, reliability, etc.
In many cases, the reason for concern about pneumatics has to do with the impression that air is more wasteful than electricity. In reality, a properly sized pneumatic system with field-mounted manifolds is very efficient and much more cost-effective than a similarly sized electro-mechanical actuator, motor and amplifier/controller.
In addition, the pneumatic system reduces overall cabinet space by being mounted outside the control cabinet and, with easy connectivity to EtherNet/IP, Profinet and other bus systems, is very easy to wire.
That being said, there are times when an electromechanical system is preferable. Our systems are designed for easy mechanical interchangeability between a pneumatic actuator and its electromechanical counterpart, matching mounting hardware, bolt hole patterns, and physical dimensions. This means that, for a given actuation, customers can select the best solutions for their needs, be it pneumatic, servo-pneumatic, stepper-driven, servo-driven, or even a direct-drive linear motor.
For more information, read "Selecting the Optimum Motion Control Solution for the Application" at www.controldesign.com/pneumatic.
Frank Latino, product manager,
Festo, www.festo.com
A Place for Pneumatics
Isn't it great when you both can be right? Pneumatics delivers simplicity, flexibility, durability and power to almost any application, including some that electrical systems can't handle. On the other hand, sometimes electronic control is the appropriate choice. New systems combine the ease of electronics with the simplicity of pneumatics. The choice really boils down to the specific application.
Pneumatic power is ideally suited for simple, continuous applications such as knife cutting or a diverting system on a conveyor. Electric actuator control is useful for low-force, precise applications like sequential positioning or pick-and-place.
Pneumatic systems are the clear choice for wet or hazardous environments. Electrical systems could have a higher spark hazard or risk of failure in these applications. Even if they can be used, they might require specialized certifications, driving up the cost.
Most equipment operates in settings where compressed air already is used. It is often simpler and less costly to use an existing power source. PLCs and fieldbus wiring make it easier to integrate pneumatics into sophisticated designs.
Concerns about maintenance are usually outdated. New air supply technologies solve most common issues with compressed air. Modern components reduce leakage. Improved lubricants operate across a wider temperature range and extend the life of actuators and valves, so they don't need to be serviced or replaced as often.
Randy DeForge, business development manager,
Bradlee Dittmer, product marketing manager,
Norgren, www.norgren.com/usa
Continue Reading
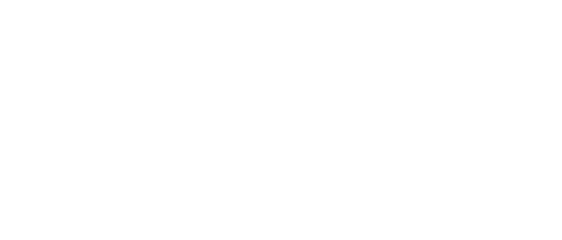
Leaders relevant to this article: