By Phil Burgert
[Read the second part of this article on the the use of touchscreens for discrete manufacturing operator interface applications. See Touchscreen Advantages-Part II]
The growing use of touchscreen-based human machine interfaces for discrete manufacturing is an indication of the advantages this type of interface provides when compared to traditional interfaces like keyboards and mechanical buttons.
Some of the advantages cited by the users and vendors of these technologies include increased flexibility, smaller space requirements, cost differentials, wiring reductions and reprogramming ease.
Good in Tough Situations
Properly selected touchscreen panels offer advantages for use in difficult environments. “Mice need to be clean for the optics to work; the old roller ball mice were even worse,” says Bob Meads, president and senior software engineer for Odessa, Fla.-based system integrator iQuest Inc.. “In a factory setting, dust and dirt from the process get into keyboards, which then can fail. “I’d hate to find that a key was stuck or not working when trying to enter a critical set point or operation step, and my process was adversely affected.”
In clean environments where a sophisticated interface is required, Mead says traditional interfaces are sometimes used, but “industrial panels certainly are called for where traditional PCs with fans and mechanical hard drives are likely to fail due to the environment,” he adds. “Environments with temperature extremes, liquid/fluid spray proximity, vibration and high airborne particulate counts are where panels are commonly deployed. Fans and hard drives just don’t hold up.”
His other considerations include proximity to the process and the workspace available. “Sometimes, there is no flat space for a monitor, keyboard, mouse and PC tower where the operator needs to be for efficient or even safe use,” adds Meads. “Since we can more easily deploy small touch panels for simple jobs, this makes panels the only choice.
Workers wearing protective gear or in a dirty environment could find it hard to use a mouse or pointing device. “However touch panels might not work for very dirty environments where the worker wears gloves or whose hands will be very dirty or greasy,” cautions Meads. “In these cases, some panels come with function buttons that respond to pressure rather than electronic sensitivity to allow gloved workers to operate the application.”
Clear Advantages
As demand for touchscreen operator interfaces for industrial machinery grows, the products offer technologies such as wireless mobile touchscreen panels and even safety-rated versions that include wireless e-stops, says Paul Ruland, S7-200 and Logo! product marketing manager in the automation and motion division of Siemens Energy & Automation.
A big advantage of touchscreens is space savings “to allow more devices and more data to be displayed in a smaller area compared to traditional hardwired pilot devices such as panel meters, gauges, annunciators and chart recorders,” says Ruland. “Touchscreens save manufacturing costs for machine OEMs by reducing the number of wired signals required to terminate, power and troubleshoot traditional panel devices. They also reduce the amount of additional I/O points on the controller for these devices.”
FINGERTIP CONTROL
Figure 1: Talon Manufacturing uses touchscreen panels for all-in-one control and display devices, as well as on simple HMI hardware.
Source: Beckhoff Automation
With a typical HMI application you’re doing either serial communications or some other bus communications to a PLC, whether it’s Ethernet or something else, says David Kaley, product marketing manager for HMI and networks at Omron Electronics. “When you’re using all those pushbuttons and meters, you’re actually wiring into I/O points on a PLC,” he reminds. “If you think about that, you’re adding cost to your PLC because need to have I/O points—analog and digital—dedicated to the controls on the panel.”
Operator interface software tools for touchscreens let engineers develop graphical screens without needing to develop hardwired computer-aided design drawings or wiring diagrams, says Ruland. “The graphical content displayed on touchscreens also can be more intuitive than traditional panel devices and be more easily customized with preferred labels and designs that help reduce training and maintenance costs,” he adds.
Interface Flexibility
Talon Manufacturing of Spring Park, Minn., uses two types of 12-in. display panels from Beckhoff Automation for all-in-one control and display on its bagging systems for microwave popcorn and other snack food. To complement the hardware, Talon used HMI software to design a high end, easy-to-use array of push buttons, menu screens and display graphics. The software also provides a visual representation of system monitoring.
“The advantage of the touchscreen is that you create a lot of flexibility,” says Dennis Hohn, president of Talon. “For a machine of this complexity you need multiple screens, engineering screens, and graph charts. Without a touchscreen, you’d need a huge display with buttons. It just shrinks the system and the space needed to run the machine and provides a lot more information.” The extreme flexibility of the touchscreen setup on the embedded PC includes the possibility of monitoring vision system images through the screen, adds Hohn.
“It gives you infinite capabilities,” he adds. “The screens are very reliable and robust. They are industrialized, and they are priced right. This solution really gives you technological advantages with ease of use.”
Talon’s machines are in 17 countries around the world and the touchscreen operator panel attached to an embedded PC allows for switching from one language to another, says Hohn.
As PC-based hardware prices decrease, more machine builders are adding multiple small panels to machines for more effective interfaces placed strategically around the machine, says Milo Grika, industrial PC product manager for Beckhoff Automation. “Not only are virtual buttons more customizable than their mechanical predecessors, the button layout can be easily changed later to improve flexibility and efficiency,” says Grika. “The low profile of on-screen buttons removes the potential of clothing, cables and other items from snagging or getting entangled on the physical button. Mechanical buttons often are more susceptible to environmental conditions as well as general wear and tear that can cause buttons to stick and have other possible reliability problems.” Real buttons added to a panel add cost, says Grika, noting that virtual software buttons can be created using software HMIs at a mere fraction of that cost.
Shaun Kneller, sales manager with B&R Industrial Automation, says it sometimes is difficult to explain why customers choose touchscreen, pushbuttons or keyboards. “Generally pushbuttons and membrane keyboards are fixed function,” says Kneller. “They have a particular purpose and that purpose doesn’t change. If you are building a machine with a lot of features, you’ll need a lot of buttons.”
An advantage of buttons certainly is that they always are available and they have a tactile feedback, says Kneller, noting that operators often are not looking at the screen or button when they press it. “They could be leaning into the machine and have their hands around the corner on the panel, pressing and operating the panel,” he says.
In a loud factory environment feeling a button is important to an operator, argues Kneller, whose customers sometimes need both traditional buttons and touchscreens. “They tell us they want that tactile feedback,” he says. “But they also want a touchscreen because it offers better and more valuable real estate.”
Ryan Gunderson, product marketing manager for PanelView at Rockwell Automation, says he would not recommend keeping those mechanical buttons just for tactile feel when an operator is not looking at what is happening on a machine. “If you are making blind touches, then you always have the chance of pushing the wrong thing,” he says. In those cases he said Rockwell’s customers use either touchscreens or portable tethered units.
Gunderson says touchscreens have the advantage over pushbuttons of offering more information. “In a discrete manufacturing environment with potentially more one-off products that require frequent setting changes, a touchscreen has the capability to offer more of a recipe,” says Gunderson.
Cost Effectiveness
Lawrence Liang, product manager for Advantech Industrial Automation Group, says his company’s ratio of touch to non-touch HMIs sold is 85% to 15%. “The key advantage of touchscreen monitors is that they act as both an input and output device with a graphical user interface,” he says.
Touchscreens have come down in price, says B&R’s Kneller. “That traditionally was the real advantage of membrane keyboards,” he says. “But now prices are much more competitive. A keyboard with 50 or 60 keys on it might even be as expensive as a panel.” Kneller notes it wasn’t long ago when industrial PCs with a touchscreen cost $10,000, but comparable devices now are $3,000 or less.
Omron’s Kaley agrees that key advantages of touchscreens include cost and panel space. While buttons and panel meters are relatively inexpensive, after adding a half dozen buttons and one or two panel meters to a project “you’ve reached the same price as a small HMI,” he says.
Rockwell’s Gunderson notes that touchscreen operator panels really have taken over much of what was handled with push buttons since the start of this decade. “Now touchscreen volume projections are three times that of graphical keypads moving forward,” he says of their use in discrete manufacturing.
Flexible Options
“A touchscreen’s biggest advantages are cost and flexibility,” says Gary Marchuk, member of the business development team at AutomationDirect. “Since touchscreen HMI products are software-based, the interface can change with the alterations of an operation or process. With some control systems remaining in place for years, changes in the process can be made easily.”
Flexibility is key, agrees Omron’s Kaley. “If you find that your initial vision might have been a little wrong, it’s real easy to change, or if you’ve had a mild product change, it’s very simple to make a changeover,” he says.
Screen proliferation provides more information to the operator, and newer touchscreens provide remote Internet access to information, or even email capability to notify maintenance personnel or engineers when faults occur, says Marchuk.
TACTILE TEXTILES
Figure 2: With touchscreen Ethernet-based controllers from BG Industrial Control employees switch to different stations and continue monitoring daily efficiency.
Source: AutomationDirect
BG Industrial Control, Placentia, Calif., uses touchscreens from AutomationDirect in a system it developed for real-time monitoring of employee efficiency and productivity in textile rental plants.
“It’s a simple application,” says Brian Greer, president of BG Industrial. “The complicated part is figuring out the logic and how to make that work to use the database and connectivity.” The work at five plants with a total of 160 touchscreens involves washing, ironing, folding and keeping track of textile uniform pieces as they travel through the plant. Touchscreens have been used in the plants for five years but they have been upgraded in the past two years.
“Managers can see the whole plant, what everybody’s doing, who is where, and their efficiency,” says Greer. “I have touchscreens at each individual workstation. Workers log in their employee number and the task they are going to perform and view the item’s name and the rate at which they are supposed to work. It shows them how they are doing during the course of the day. That’s all reported back on the main computer and it sends out production reports.”
The most important advantage of touchscreens over other types of control panels is versatility, says Greer. “I can send out actual strings or actual names. With an LED display you’re not going to get that. I can use variable screens and use it for maintenance or to send messages.”
Rick Tomfohrde, HMI business development manager with Pepperl+Fuchs, notes the ability of operators to directly see and touch machine visuals to activate desired functions as a chief advantage of touchscreens when compared to keyboards or mechanical buttons. “Any other style of input requires some back-and-forth hand-eye coordination by the operator,” says Tomfohrde. “While this might seem simple, and it often is, each cycle takes just a little more time and is just a bit more tedious and prone to error. Over time these incremental bits add up to reduced throughput and more operator errors.”
Marchuk notes that many machine OEMs now sell machines over the world, and touchscreens support multiple language options to provide one control solution regardless of location.
Mind the Disadvantages
The only disadvantage that iQuest’s Meads notes is that the screens do require cleaning. “This is far outweighed by the environmental problems and cleaning requirements with traditional interfaces,” he says. “Some say touchscreens don’t allow a robust interaction with the process. However, if the applications are designed with the touchscreen in mind, the application can enjoy all the benefits, without the drawbacks.”
Problems with touchscreens, however, could arise in certain applications where older, less-advanced technology is used. “For example, older cell- and grid-based technology could develop faulty cells on a touchscreen after repeated use or abuse of a single button on a screen,” says Siemens’ Ruland. “Some touchscreen designs aren’t usable when an operator is wearing gloves. However, newer touchscreens based on analog-resistive technology are pressure-sensitive and respond to any input device, including a gloved hand, finger or stylus.”
Importantly, disadvantages of touchscreens sometimes could involve safety issues, says Beckhoff’s Grika. “When it comes to an e-stop, nothing can replace a big, red, physical button; especially when e-stops are placed all around the machine,” he says.
While safety concerns can be addressed with physical interfaces such as e-stops, light curtains, dead-man switches and pressure mats, the majority of machine control can be accomplished using on-screen buttons, says Grika.
Grika adds that touchscreen space limitations could be a disadvantage, as well. “Software buttons on a screen can mean less space for other kinds of visualization,” he says. “However, minimizing screens or menu systems get around this.”
Replacing a touchscreen is generally much more complex than dropping in a new physical switch, says Grika, and “wear and tear is exacerbated by operators who use whatever is in hand to hit the buttons on the screen. Many touchscreens have to be replaced because of damage from a screwdriver used to activate on-screen buttons.” But Grika argues that new display technologies and quality improvements to panel designs for easier replacement of the glass screen all combine to make using software buttons more feasible in the long term.
“There really are very few disadvantages of a touchscreen,” agrees Rockwell’s Gunderson. “The only disadvantage I can see is an application that is a bit more extreme or messy that customers might not consider as touchscreen-appropriate. In reality, our touchscreens are all capable in those environments.”
Maybe so, says Advantech’s Liang, “but touchscreen panels will not function in very harsh environments with temperatures above 55 °C or below -10 °C. Brightness is not strong enough when used outdoors although sunlight-readable and transflective LCD technology have improved this.”
Touchscreen technology has become exceptionally reliable of late, says Tomfohrde. “However, surface wear, abrasion and accidental damage can and does occur,” he cautions. “To address these potential durability issues in the most extreme environments, some suppliers now offer hardened front surfaces or sacrificial overlay protective sheets.”
Phil Burgert is a freelance writer specializing in the technical trade media.
Continue Reading
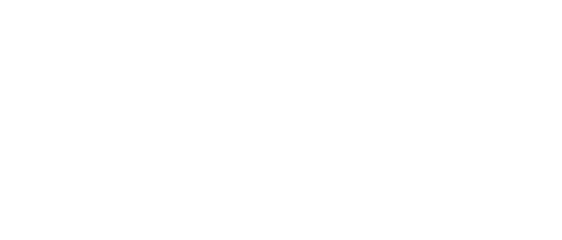
Leaders relevant to this article: