By Ed Barr, P&L Specialties
The grapes have been harvested and are ready to be processed. The winemakers stand ready to perform their magic on the fruit. To the untrained eye what happens next doesn't appear to amount to much. That, however, is not the case. Sorting those grapes to remove MOG (materials other than grapes)—those raisins, leaves, shot berries, spoiled fruit, bits of stem jacks, bugs (Figure 1)—is a crucial step. The sorting must be done before loading the grapes onto the conveyors that transport them to the fermenting step.
In many wineries, machine sorting has replaced hand sorting, which introduces another set of concerns. "If the sorting table shakes too rapidly or not fast enough, if its movement is uneven or if it starts and stops, the grapes can be damaged," explains Wes Snodgrass, P&L Specialties general manager. "They will not be sorted well, and either the process will be delayed while sorting is completed or MOG will find its way into the wine. None of those alternatives is good news to a winemaker who, in addition, might have to pay extra hours to a staff that's waiting around with nothing to do while a batch is re-sorted or for machinery to be fixed."
P&L is a California-based designer and manufacturer, integrator and supporter of customized winemaking, food processing and water-treatment machinery. Its grape processing equipment is widely used by wineries in the U.S. and Canada. In business since 1984, P&L has established a reputation for quality, value and unparalleled service. Its products include sorting tables, bin dumpers, destemmers, Le Trieur sorting tables, air knifes, receiving hoppers, catwalks, belt and screw conveyors, rotary screens and mixers. P&L also represents several high-quality, complementary, European pieces of equipment that can integrate with P&L's own systems. Its patented Le Trieur sorting machines (Figure 2) was recognized by Wine Business as one of the "Top 11 Products for the Small Winery."
All in the Movement
It is especially important to be able to smoothly control the motor while the speed of the machine is either increased or decreased, as the balancing force is less stable during changes in rpm.
When P&L set about replacing the variable frequency drives (VFDs) on its sorting tables and on Le Trieur, its short-term goal was to find an efficient solution to the challenge presented by one of its off- the-shelf units. "As the sales of these units increased, we began to face delivery lead time and serviceability issues with the original article controllers," explains Greg Nau, sales engineer. "We offer a comprehensive two-year warranty on our equipment and most electronic control manufacturers only provide 90 days to one year of warranty. We were essentially in the position of extending the manufacturers' warranty, so we demand solid performance and robust durability."
For P&L, keeping the big picture in mind is key. "We see our reputation for keeping our commitment to quality and performance as our No. 1 tenet to ongoing business," says Carl DeBenedetti, purchasing manager. "Our equipment is not the least expensive on the market, and our customers expect it to really deliver on long-term value and performance."
[pullquote]P&L has been using the Lenze-AC Tech stainless steel MC NEMA 4X drives on its sorting tables, several conveyors and Le Trieur, with good results. What exactly determines good results? "Lower failure rates, an excellent level of internal parameter programmability and smooth operation of the motors, especially during acceleration and deceleration," explains Snodgrass. "Plus, we really like the drive's look and performance. We use many of the programmable parameters to control variables such as speed, ramp up/ramp down time, minimum and maximum Hz settings, over-voltage and over-amperage protection."
This precisely addresses the concerns expressed by winery owners who've had poor experience with sorting machines that don't perform as smoothly as expected or have a high failure rate of electrical components due to the demanding environment of wineries. The main reason for failure is moisture entering the enclosure during washdown, creating steam when the unit is warm and thus causing a total electrical failure due to short circuit, says Snodgrass.
"The MC Series is a constant-horsepower, versatile drive that can be set up for simple applications requiring ramped start, ramped stop and speed control, all the way to demanding applications that require PID setpoint control and many other functions," states Lise Houston, regional sales manager at Lenze-AC Tech (www.lenze-actech.com). "Available in NEMA Type 1, 12, 4 and 4X stainless-steel enclosures, the MC Series consists of the MC1000 and MC3000 models. Most applications will use the MC1000 with a keypad that includes start, stop, up, down, forward/reverse, program/run, auto/manual and enter buttons. For non-reversing applications that require independent switching of start and stop from local to remote and speed control from auto to manual, the MC3000 series keypad replaces the forward/reverse button with local/remote."
Value for the Customer
Nau says customers value the quality and ruggedness of P&L's machines and appreciate the straightforward operation and ease of use. He stresses that this type of equipment is put to work intensely for a five-week harvest and then stored for the balance of the year, a tough duty on any piece of machinery.
"If our customers have problems or questions, the MC panels are very easy for our staff to troubleshoot," states Nau (Figure 3). "Occasionally customers accidentally enter the wrong parameter settings and change values that create operational issues. We also have some customers who would like to alter the ramp up or ramp down times or the min/max speeds, and being able to talk them through this procedure is a valuable tool."
Support Still Vital
"But at the end of the day, no matter how mechanized the winemaking process might be, there's still need for human intervention, and it's the same with motion control technology," laughs DeBenedetti, who says that part of the reason P&L chose the Lenze-AC Tech products is the support it gets from the distributor, Electrical Equipment (EEC), the Petaluma, Calif., supplier that builds P&L custom panels and is its primary vendor for electrical and electronic requirements.
"Our relationship is very important because we have to trust their knowledge of products and their ability to resolve issues," stresses DeBenedetti. "They understand the urgency of our business, and they never let us down."
DeBenedetti says P&L chose the MC largely because of prior good experience with the SCF, another VFD from Lenze-AC Tech, which P&L used in custom-built panels on other equipment lines it makes, and P&L had full confidence in the recommendation from EEC.
Ed Barr is president of P&L Specialties, Santa Rosa, Calif., and a licensed aircraft technician. When it comes to design, he says there is no compromise between elegance and functionality. "The aircraft industry is a wonderful world of form and function in the design," says Barr, former Boeing and United Airlines aircraft maintenance manager. "I really get the importance of machinery that functions properly, safely and to expectations, but I also have an eye for the beauty of design." Learn more about P&L Specialties at www.pnlspecialties.com.
Continue Reading
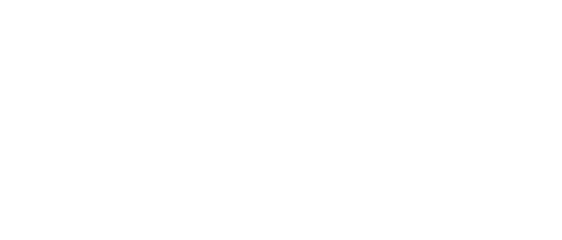
Leaders relevant to this article: