By Jim Romeo
When it comes to controller architecture, PLCs, PACs and PC-based controls are all players. However, CNC machining centers still play a viable role. Because machining varies by industry and application, so does the efficacy of controller. Many different permutations of control are integrated with machining for different applications.
So where is this element of control architecture heading? Opinions differ. Some believe there is a clear trend in integrating advanced control into CNC machining. While CNC may still be the dominant choice, the use of other controllers is becoming an increasingly visible consideration, often due to the need to integrate the machining center with other systems.
“CNC control of machine tools was, and still is, a breakthrough technology,” says Robert Page, and engineer with Milltronics, a machine builder in Waconia, Minn. “CNC makes it possible to cut angles, arcs and complex 3D shapes that were either impossible or difficult on manual machines tools. Many modern efficiencies are the direct result of CNC machine tool technology.” Page appreciates CNC’s extensive user interface, making the coordinated motion of several axes possible, but the only constant is change.
“The only trend clear to me is the growing use of PC-based devices,” says Page. “The growth of PC-based devices is a natural because in the past 10 years PCs have become vastly more powerful and capable, and also more reliable while their cost has been going down.”
Did He Just Say, “PC”?
PC-based controls are undoubtedly becoming more prevalent in the industry, says Kevin Bevan, president of GBI Cincinnati, a Tier 1 international distributor and the exclusive master distributor for Cincinnati Lamb’s high-end aerospace and transfer-line products.
“Back in the mid-’90s there was a strong push for more open architecture controls,” he says. “Customers felt that the standard control offerings were too closed and did not provide the end-user flexibility to customize the functionality as needed. Control builders tend to prefer a closed or more proprietary approach to the product they sell.”
Bevan contends that not much has changed since the mid-’90s. He feels that some companies have developed PC-based controls and have performed well in niche markets such as die/mold and medical, noting also that the term “PC-based” can be misleading. Ten years ago, the term made many wary that a standard PC may not be reliable enough. “With the changes that have taken place, today’s PCs are far more robust with extremely low failure rates,” adds Bevan.
GBI’s Revolution line uses computing technology in the development of its MTI CV control. This proprietary control architecture uses tool path algorithms that have a read speed of more that 50,000 blocks/sec and up to 50% cycle reduction, says Bevan. The result is a constant-velocity machining center that is fast, constant and without acceleration and deceleration, he claims. “With the leap in technology, we actually run on a dual kernel platform,” explains Bevan. “This means that the machine is being controlled by one platform that maximizes the efficiency in the cutting operation, while the secondary kernel performs all the PC functions in a Windows environment. The only time the two kernels communicate is in the loading of part programs.”
OUT WITH THE OLD
Figure 1: PLC/PC controls can be expanded by integrating CNC controls and then can replace the CNC functionality previously hard-coded in dedicated hardware.
Source: B&R INDUSTRIAL AUTOMATION
The Windows environment also is appealing to Russ Jacobsmeyer, chief technology officer for Sunnen, a vertical honing machine builder in St. Louis. He feels that the PC-based controls are easier to use and program, largely because many who use them are already familiar with a Windows environment. “This has been something we have had success with, or received constructive feedback from the market on,” says Jacobsmeyer. “The demand is global and in large and small shops. I believe productivity is driving the demand. In speaking with a customer we have in Germany when I was there in the fall, he had nothing but wonderful things to say about the operating system on our new PC-based equipment. He found it easy, intuitive, flexible, and ultimately most productive or efficient for him. We have also written our software to be easily translated into the local language of interest. I think this has been a plus for us.”
Softly, as in an Integration
Dario Doko, a sales engineer with B&R Industrial Automation also sees integration of traditional CNC with PLCs, PACs and PC-based controls as a definite trend. Doko attributes the trend to two factors: a better and easier CNC integration and a lower price for hardware, software and engineering.
From Doko’s vantage point, typical users are OEMs who would like to seamlessly integrate their standard machine control to the CNC feature (Figure 1).
“The standard PLC/PC controls can be expanded by integrating dedicated CNC controls in its software for easy CNC controls, data share between PLC and CNC components in a machine and future upgrades,” says Doko. “This way, a dedicated and expensive CNC controller is not required any more, but instead standard and well-known PLC/PC controls can be used.”
Doko explains that in the past CNC functionality was often hard-coded in a dedicated hardware. “We can extend the standard PLC runtime with a ‘soft’ CNC,” says Doko. “This means that the customer can use the same hardware for controlling, visualization, standard motion and CNC just by adding software components." But he explains that for some applications, standard dedicated controllers are still better. “The reason for that is not in the better technology they possess, but rather in well-developed software components that these dedicated CNC controllers historically have,” says Doko. “Over the time, this gap will be smaller and smaller. CNC on standard PLC/PC platform is a very young topic indeed.”
CNC machining centers might not be replaced in full by PLC- or PC-based architecture; however, the systems can no longer be disparate, according to Sloan Zupan, product manager at Mitsubishi Electric Automation. “Customers who use both CNC and PLC for different control applications have a desire to see the two platforms combined,” he says. “The ability to integrate sophisticated controller capability is valuable to customers who are looking for a competitive advantage in both performance and lowest total cost of ownership. Using a combined CNC/PLC platform means that different control types seamlessly integrate, and the costs associated with training and spare-parts inventory is significantly reduced because the rack, power supply, inputs and outputs and communication interfaces are common regardless of the controller type selected.” But Mitsubishi’s Zupan adds that it really depends on the customer’s application. “If the customer’s only application is machining and other control disciplines aren’t needed, then traditional CNCs are the best fit,” he says. “We are seeing that almost all applications require some other control. When more than one control discipline is needed, then theMitsubishi iQ platform is capable of combining CNC, PLC and the other required control disciplines.”
There’s No G in PLC
CNCs and PLCs are designed for different applications, and each control system is well-suited for specific types of applications, explains Paul Webster, CNC product manager at GE Fanuc. “There’s little overlap in usage between CNC- and PLC-based controls,” he says. “General-purpose motion control can often be accomplished by PC-based control systems and PLCs. However, the specific type of high-performance motion control that is required in a machining center requires increased sophistication and capabilities by the control engine, and it is these types of applications that CNCs are designed specifically to address. CNCs offer multi-axis interpolation and G-code capability among other functionality, which enables them to tackle the high-speed, high-complexity, multi-axis and multi-path control applications needed for today’s most complicated machining operations.”
G code has been around for a while as a standard programming method, but it hasn’t been static. As more features are required, new G code evolves to fill the gap. But according to Webster, G-code programming is very flexible—where PLCs and PACs typically require a hard-coded profile that doesn’t work well in machining centers. “Really, that is the point of a machining center and the CNC that controls it—the flexibility to quickly manufacture just about any part that will fit into the work envelope and the ease of switching between parts,” says Webster. “Speed and complexity are not a function of the G code, but of the control processing them. The faster the computer processes the code, the faster it can machine a part.”
MAKE A SPLASH
Figure 2: Some users have used PACs to provide rudimentary functionality, if it has the essentials for CNC tool compensation and interpolation built-in.
Source: BOSCH REXROTH
But arguments can be made for machining-center control with PACs. For simple x-y-z milling machines, some users have used PACs to provide rudimentary functionality, explains Karl Rapp, automation and machine tool branch manager with Bosch Rexroth. Rapp adds that, if the PAC has the essentials for CNC tool compensation and interpolation built-in, a typical NC program, consisting of potentially thousands of G-code lines per file, can be executed (Figure 2). "Large NC files are typically generated via CAD/CAM software using machine-specific post-processor programs," he explains.
Return to the CNC
Given the pressures to reduce manufacturing costs today, customers look for CNC equipment to provide them greater transparency to areas of lost productivity, says Jon Cruthers, manager for business development at Siemens Energy and Automation, and he sees this transparency being driven by customers that increasingly turn to overall equipment effectiveness (OEE) as a performance measurement.
“A basic OEE analysis includes measurement of machine utilization, machine availability, machine output and part quality,” says Cruthers. “By using the information available from a CNC system, customers look to automatically acquire, document and calculate OEE by monitoring productive time vs. planned and unplanned downtime. Unplanned downtime due to faults and planned downtime due to equipping and setup affect machine availability. Idling and short standstills along with reduction in speeds affect productivity. Scrapped and reworked parts affect overall part quality. Customers are looking to more accurately capture and identify these loss makers. Transparency of these loss makers is key to improving productivity and saving costs. Having the CNC provide this information in greater detail than can be manually collected by operators provides customers with what they are looking for to improve their operations.”
This is an advantage of Siemens’ CNC control, he contends. Every cycle is tracked with complete part and machine performance data. It can upload the data through a secure network to an intermediate zone controller, host server or remote monitoring station.
“At big plants where machines run unattended, this shortens the response time for troubleshooters, provides all machine/part/tooling data for subsequent analysis and predictive, not just preventive, maintenance,” he says. “Plus it feeds into the OEE protocol.”
Jim Romeo is a freelance writer specializing in the technical trade media.
IN THIS CORNERCNCs are the undisputed heavyweight champions of machining-center control, but other architectures are entering the ring and sizing up the application. Are you backing the champ or looking at other options? Square off at www.ControlDesign.com/cnc.
The Lexicon of Control ArchitectureProgrammable Logic Controllers (PLCs) make real time mathematical calculations in response to onboard conditions of machine mechanical functions. “A PLC is a dedicated computerized system that controls an electronic circuit by using ladder logic,” says Bill Zalot, president of Tek Supply. Simple motion can be controlled and devices can be actuated from a single control station, explains Jon Cruthers, business development manager for Siemens. “PLCs are still the norm for most production machines, including packaging, printing, textile, papermaking and metal forming machines such as stamping presses, where motion is quite basic and repeatable,” he says. Programmable Automation Controllers (PACs) are multi-disciplined controllers capable of providing real-time logic, motion and process control, in addition to HMI and other functions, on a single platform, according to ARC Advisory Group, the organization largely credited with coining the phrase. A PAC offers one programming and engineering tool, as well as one programming language and a single tag database for the complete system. It combines a PLC with PC-based functionality. “This enables programming of a cycle or sequence of events to a greater degree,” explains Cruthers. “PACs and PLCs perform approximately the same job,” says Robert Page, an engineer with Milltronics, a machine builder in Waconia, Minn. “While a PAC is a PC-based device, a PLC is not,” he adds. “Both run a high-speed loop, examining inputs and setting outputs according to control program logic. Generally these devices run an automated process and are programmed using ladder logic. They do not have an operator interface.” Computerized Numerical Controls (CNCs) are unique to the machine tool world. “A CNC is used to run a machine that performs a repetitive task such as drilling holes in sheet metal,” explains Zalot. CNCs control by reading the particular G code and M code languages needed for the highly complex machine-operation variables such as distance, rotary motion, tool positions and angle of incidence. PC-Based Controls are similar to PLCs, except that they use a regular PC or laptop computer to enter and run the programs as opposed to a CPU or processor module in a PLC system, explains Zalot. “They also do not run a continuous loop program like a PLC does when using a PC to run the program,” he says. “And they tend to not be as robust in harsh factory environments as a PLC is.” |
Continue Reading
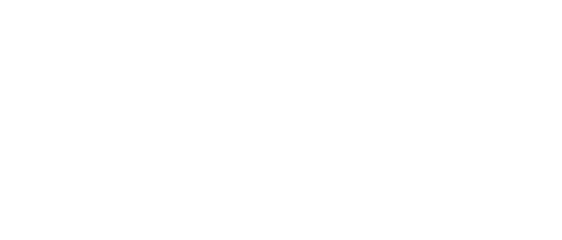
Leaders relevant to this article: