By Rich Gaston, Heateflex
Patented technology driven by a proprietary algorithm is one of the reasons manufacturers worldwide that require ultra-pure, precisely heated, deionized water systems do business with Heateflex Corp., Arcadia, Calif.
Heateflex’s Power-to-Flow algorithm enables the company’s temperature-control technology to deliver water held to extremely tight temperature tolerances, even with highly variable flow rates. Manufacturers in semiconductor, data storage media, optical, solar cell and medical industries are typical users of the technology. Rinsing chemical reactants used in chip etching is an example of a process in which precise water temperature control might be critical. In this instance, chemical activity during the rinsing process could accelerate or decelerate depending on water temperature.
Power-to-Flow Algorithm
“Conventional water heating approaches typically use proportional-integral-derivative (PID) schemes that sense and respond to only one parameter, as from a single thermocouple,” says Hector Castaneda, engineering manager, Heateflex. “The Power-to-Flow algorithm simultaneously accounts for both incoming and outgoing water temperatures, flow rate and heater voltage fluctuation.” Using these inputs, the alogrithm determines how much power to send to heaters. “Under conditions of widely varying flow rates, Power-to-Flow technology is capable of maintaining water temperature tolerances as much as five times tighter than conventional approaches (Figure 1),” adds Castaneda. “The technology is very efficient because it can avoid overshooting target temperatures—enabling faster delivery of correct-temperature water for improved process responsiveness.”
On Target
Figure 1: Power-to-Flow technology avoids overshooting target temperatures.
(Source: Heateflex)
For the past 18 years, Heateflex has offered Power-to-Flow technology in the Aquarius line of deionized water heating systems. The algorithm was programmed in assembly language into an embedded temperature controller—a custom-designed board running a 6809 microprocessor. Manufacturing of the controller had been contracted to a local PCB assembler for production in relatively limited numbers.
All the electronics were housed in a single box, and the user interface was a single line of display plus 12 programmed buttons. Operators entered water-heating recipes line-by-line, often calling for creative, almost cryptic, programming. Confirmation was displayed back line-by-line. LEDs lit up to indicate where the user was in the process, making programming time consuming and painstaking.
Drivers of Change
Since it first was developed, the Power-to-Flow algorithm has been improved steadily, requiring an ongoing effort to tweak the dedicated board. By 2006, our company was ready to introduce a major advance that would require an extensive controller re-work. At the same time, customers started to ask for networking capabilities and user-friendly HMI, as well as state-of-the-art utilities. We realized that its embedded board control scheme was limiting and that is was time for a new approach.
Heateflex had been relying on Automation Controls, Campbell, Calif., for the controls on our Fluidix line of steam-heated water heaters. Heateflex acquired the Fluidix line in 2002 to add a large-volume water heating system to our offerings. Automation Controls equipped the Fluidix machines with PLC controls, and we were impressed with the extremely consistent process temperatures delivered by the Fluidix PLC control system and, accordingly, talked with Automation Controls about converting Aquarius machines from the dedicated, embedded controls to controls using off-the-shelf PLCs.
“The embedded control board was boxing us in, recalls Hector Castaneda, engineering manager, Heateflex. “At first we considered a PC-based control solution, but we found that implementation tools for our specific requirements were more highly developed for PLC systems, making them the right choice to get to market faster. PLCs were right for our customers and for us.” A PLC control platform, adds Castaneda, would enable a more capable version of Power-to-Flow and provide for future growth while providing the new control features customers were asking for then.
“The issues that concerned us about moving to PLCs included being certain of the security of our intellectual property and knowing there would be sufficient safeguards to prevent the customer from altering the unit into an unsafe condition,” says Castaneda. Automation Controls demonstrated that a PLC-based control scheme could address these concerns.
Automation Controls recommended an Omron CJ1M PLC for its reliability, performance and ease of programming. It’s the same PLC used on the Fluidix system. The commonality made programming as pain-free as possible—an important consideration since translating the Power-to-Flow algorithm’s functionality into the ladder logic required by the PLC takes significant effort.
Tom Trinh, senior application engineer, Automation Controls, was the project manager. He designed the touchscreen interface and included Ethernet communications. Omron field application engineer Chris Hebert took the lead in translating the functionality of the Power-to-Flow algorithm to the PLC’s ladder logic, enabling both the temperature control functions and the touchscreen. Hebert also set up values to display system status and alarming. At Heateflex, Castaneda supervised PLC programming and integrated the hardware, including power, wiring and installation into cabinets, as well as linking the PLC to flow meters, other instrumentation, valves and pumps.
PLC Enables Multi-Zone Control
Applying the Power-to-Flow algorithm to multiple zones was a major advance made feasible by application of PLC control.
“Now, consider dividing the flow of water into a number of zones as it passes through the machine,” explains Castaneda. “Sensors in each zone essentially tell both the previous and subsequent zones what conditions they see, enabling incremental adjustments to optimize overall system performance. The result is better responsiveness to increases and decreases in flow, as well as changes to the temperatures called for by the customer’s process. Multi-zone technology provides a real competitive advantage for our customers.” (Figure 2)
In the Zone
Figure 2: Multi-zone sensors mean better responsiveness to flow and temperature changes.
(Source: Heateflex)
Expandable With High Connectivity and an Intuitive HMI
Beyond enabling the multi-zone version of Power-to-Flow, Heateflex believes the PLC solution also provides Aquarius machines with all the benefits that accrue to state-of-the-art control. “The PLC is flexible for adding modular plug-and-play I/O,” says Hebert. “For communications, it has integrated 100BaseTX Ethernet connectivity with DeviceNet and Profibus available. The original controller board had only two serial ports. Also, the PLC offers a very high scan rate of 4–5 msec, up to 10 times faster than the scan rate of the former solution, enabling implementation of a more sophisticated algorithm than would otherwise be possible.”
The touchscreen enabled display of and access to a lot more data than did the former controller, says Trinh about HMI design (Figure 3). “And, the HMI’s ability to deliver information in clear, easy-to-understand formats reduces training requirements,” he adds. “Also, we designed screens specific to safety and alarming. Alarm conditions, including over-temperature of DI water or heating elements, leaks, high pressure and no-liquid can be directed to personal email or cell phones. We also designed pages enabling fine-tuning of individual parameters. With the touchscreen, unlike with the embedded controller, you don’t have to scroll through parameter numbers, then look them up to reference how they relate to overall control. Before, you could only monitor one or two parameters at a time. Now, we can look at multiple things happening dynamically on one screen and view the process in real time via the Internet from anywhere in the world.” Our company doesn’t do remote customer monitoring yet, but now we’re ready for it.
More Information, Less Training
Figure 3: The easy-to-understand format of the touchscreen HMI reduces training requirements. (Source: Heateflex)
The PLC can be programmed from a handheld device or a laptop making programming for general maintenance or updates easier and more cost-effective compared to the board. The Power-to-Flow algorithm sits password-protected in the PLC. “Features built into the program prevent anyone without the password—even if they had CX programmer implementation software—to download, copy or even view the ladder logic,” says Hebert.
“There are two types of programming parameters: those that are customer-accessible and some critical, factory-set parameters that are accessible only through hidden screens deliberately not available to the user.”
Program reloading or updates simply require uploading a code into the password-protected system from either a compact flash or other downloadable media. Replacement hardware items are available off the shelf.
“The difference between an embedded controller and state- of-the-art PLC is the difference between troubleshooting online and having to send a tech out to physically punch in code, and taking a lot of time to do it,” summarizes Castaneda.
Looking forward, the PLC control regimen already has stimulated some Heateflex customers to consider interfacing the Aquarius system with their central facilities management software, enabling integration with their status and trending routines.
Rich Gaston is vice president, business development for Heateflex, Arcadia, Calif. Learn more about the company at heatelex.com.
Programmable Controllers Vs. Embedded Controllers
If you weigh the costs of developing embedded controls in-house against buying a PLC, there are some important advantages that accrue to the off-the-shelf solution. These include shortened time-to-market with your product and reducing the size of your captive technical support teams to service an installed base of controllers.
Continue Reading
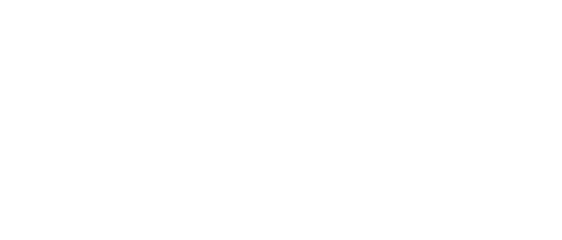
Leaders relevant to this article: