By by Mike Bacidore, Managing Editor
A Harley-Davidson motorcycle epitomizes untethered freedom.
So, it made perfect sense when Dana Fluet, maintenance reliability engineer at the H-D machining center for motorcycle power trains in Milwaukee, decided to make the plant’s vibration measurements wireless.
The facility, which cuts engine- and transmission-related parts, has been using walk-around vibration analyzers in the past, but that technology can create production obstacles. “We have a walk-around vibration program,” says Fluet. “But we have to take a machine out of production, run it at a fixed speed and take measurements. Plus, we’re not running the spindle under load. Conditions will vary under load versus under no load. Those were the two obstacles we had to overcome—not interrupt production and collect data while the spindle was cutting or under load.”
With more than 1,400 assets under one roof, Fluet has a lot of machines and processes to monitor via walk-around. He’d like to implement wireless monitoring throughout the H-D plant, but you have to walk before you can ride.
Emerson Process Management’s CSI data collectors are used to collect data around the plant from a variety of brands of vibration sensors. “Right now, the third phase of a Techkor wireless solution supplements these,” says Fluet.
Critical Mass
The power-train plant has multi-axis machine tools or CNCs, some with as many as six axes. “We can’t hardwire the existing machines,” explains Fluet. “I was looking for a wireless technology that we could attach to a spindle inside the machine and continue to run the machine while monitoring the condition of the spindle bearings. It’s difficult to get data out of the nose with wires hanging out (Figure 1). It’s difficult to support cables in these.”
The important feature Fluet wanted was vibration monitoring. “I need to identify the bearing fault and plan replacement,” he says. “We have 60 tools, and each tool runs at a different speed. When we set a schedule, we don’t know which speed it’s running at.”
Ultimately it was the solution’s nature and the bottom line that prompted Fluet to look for sensors that were completely wireless. “These sensors are mounted on each machine and subjected to direct coolant spray during machine operation,” says Bob Kirker, sales manager, Techkor Instrumentation, of the harsh environment. “And Fluet’s putting these sensors in metal enclosures. From a wireless perspective, that’s a difficult environment.”
In most cases, each machine has one sensor, explains Fluet. “Our R&D project is using one sensor per machine, too,” he says. “One machine has six sensors because it has six spindles. Two Cisco repeaters with a 250-ft range are interfaced with Techkor network access points, which are also good to 250 ft from the sensors, giving a total package of 500 ft. In the end, when you add in the cost of routing cable and connection, it’s more cost-effective to install wireless.” Many wireless sensor solutions are actually tethered, with an accelerometer connected to a junction box, says Kirker.
Cost savings already have paid dividends for Fluet. During Phase II, the wireless sensors captured data when a machine started to lose a spindle bearing. “We were able to replace the spindle without losing production,” he says. That financial impact enabled him to fund the addition of more sensors.
“My dream is to have these deployed on many, many machine tools so we can monitor everything,” says Fluet. “We have around 350 A-critical machines.” If an A-critical machine is down for more than four hours, it impacts the assembly line and consequently the H-D facilities in York, Pa., and Kansas City, Mo., where completed power trains are delivered. “I want all 350 of those A-critical machines wirelessly monitored,” he says.
Back to School
Pivotal to Fluet’s aspirations is the Center for Intelligent Maintenance Systems, directed by professors from University of Cincinnati, University of Michigan and Missouri University of Science and Technology. The Center for IMS is an NSF industry/university cooperative research center that works on projects with more than 50 member companies to transform the traditional fail-and-fix maintenance practice to a predict-and-prevent methodology. As a member company, H-D has access to IMS university graduate students who can help with R&D, as well as IMS’s Watchdog Agent prognostic tools. Dr. Jay Lee is the director of the Center for IMS.
“We’ve been working with Dr. Lee at the University of Cincinnati,” explains Fluet. “He’s got a handful of master’s and Ph.D. candidates in mechanical engineering. I’ve been using one of their students to integrate the Techkor wireless system on our machine tools using Watchdog Agent, the integration device from the University of Cincinnati.”
Ultimately, the goal is to integrate sensor data with the control system on the machine, so it could shut down the machine when an anomaly occurs. “The Watchdog Agent will provide that capability,” says Fluet. “It will interface with a Siemens or Fanuc controller, which are the primary ones we use on our machine tools.”
Getting There Is Half the Fun
While Fluet began his wireless trip with a destination in mind, he wasn’t quite sure how to get there until he found Techkor. “He had the concept in mind,” explains Kirker. “He took our existing system, which got him to 80% of where he wanted to go and deployed it across his factory for about a year and figured out the capabilities. Then he came back to us and asked if we could help him with polling. He was looking for more consistent data to trend with. He hooked us up with the Center for IMS, which has the PLC interface that we don’t have. That opens a lot more opportunities on the control side of things.”
H-D is now entering the third phase of the wireless-sensor implementation.
In the first phase, the wireless system was put in place and Fluet began experimenting with it to work on the plant’s wireless network and looking at how Techkor’s Maintenance Watchdog system could be integrated to trigger when an anomaly occurred on a machine. “We had the student for a couple weeks during Phase I,” says Fluet. “He set up some software for some trend capabilities. In Phase II, the student developed a system to let us get data at a fixed speed and under load. He developed a protocol, so now we can actually trigger the sensor to collect data when we want it. If we know a 4-in. pin mill is coming into the spindle, we have inrush current on the motors. When the tool starts cutting, it will collect data then.”
Initially, Fluet was monitoring 22 machines with the wireless sensors. But that number has dropped because of the reliability issues being addresses during Phase III, in which the new system with polling capabilities will be loaded and the student will return for consultation. “We’re using a time-based system and migrating to a poll-based system,” explains Fluet.
“In the earlier generation of Maintenance Watchdog, it was not listening,” says Kirker. “The sensors only woke up on a time schedule. The new sensors wake up every three seconds and see if you’re trying to talk to them.”
Morning Comes
While Fluet’s dream of fully wireless monitoring of all critical tools and integrated machine control is yet to reach the REM stage, significant accomplishments have spurred on future plans.
Data integrity, for example, is a non-issue for the system. “The sensors provide a digitized acceleration wave report,” explains Kirker. “From the sensors to our access point, we use a proprietary protocol.”
The sensor data uses TCP packets to ensure it keeps sending until the complete data is received.
“The data resides on my computer, and I have a vibe analyst on staff who looks at it, too,” says Fluet. “Now, we’re going to a more self-contained system where we can access the data through a Web browser, which simplifies the installation process. In the old system you had to install an SQL database. In the new system, you know the IP address of the data.”
Where the Wires Are?
Does wireless sensing make sense for your operations? What’s holding you back? Or if you’ve already begun an implementation of a wireless monitoring system, where are you in evolutionary iterations? Share your stories or concerns at ControlDesign.com/wirelesssensors.Wireless Monitoring Will Shift to Standard Networks
Proprietary wireless protocols are being used on the largest share of 2007 shipments of products for on-site industrial monitoring and control, according to “RF/Microwave Industrial Wireless Monitoring and Control Products: For Discrete and Process Manufacturing, Global Market Analysis,” a market study from Venture Development.
Proprietary wireless protocols accounted for more than 55% of the applications, and wireless products with proprietary protocols operating in the 800 and 900 MHz band accounted for the largest share of these products, followed by those with proprietary protocols operating in the 400 MHz band. Proprietary networks operating in the 400, 800 and 900 MHz ranges have been preferred in industrial applications that require longer distances. Compared to higher-frequency networks, these also provide better propagation, especially through walls and other obstructions, and require lower transmission power. Many of these are applications for which high data rates are not required, such as data transmissions for simple on/off controls or alarms, and remote monitoring of variable signals, but without high data transmission rate requirements. Many users believe proprietary networks are more secure and more reliable than standard networks.
Dramatic shifts in preference are expected over the next four years, with a trend toward standard wireless networks. The advantages of standard networks include lower costs, interchangeable products and established best practices, including security and interference protection.
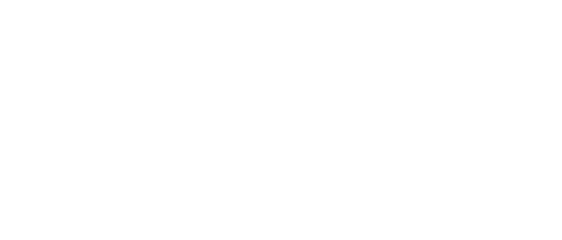
Leaders relevant to this article: