By Joe Feeley, Editor in Chief
Most technology users and providers agree that the pace of new technology rollouts is blisteringly fast. When that speed combines with many competing opinions about what products and systems work best with that new technology, the crystal ball becomes cloudy. It's hard to foretell with Kreskin-like accuracy what's really going to happen, or exactly when.
Despite the uncertainties, a number of new services and systems are clearly emerging as tools that will impact your thinking about control, if they haven't already. There also are some next-generation technologies that are being introduced in process plants or further up the enterprise chain and they may enter the industrial OEM market at any time.
First, the Market Report
Nearly all the emerging control technologies have common threads to the overall information technology marketplace. "The global controls market is tiny compared to the global IT market," reminds Jim Heaton, analyst, Advanced Manufacturing Research (AMR), Boston.
"Since the selling price of most electronic and software products is affected more by volume than design cost, complex general-purpose [high-volume] products can sell for a fraction of comparably complex, but low-volume controls products." These cost advantages will make it inevitable for the controls market to use general-purpose technology wherever possible. The rapid acceptance of open architecture as the predominant hardware and software design strategy reinforces this projection.
The Objects of Our Affections
The world of little objects is creating rapid growth for new companies that provide control solutions based on object-oriented technology. This program architecture is groups of self-contained blocks of code, with data and function built in. It has been likened to using Legos to build a structure, which, in this case, is a large, complex program. Each unit is a proven, reliable object that can be copied into the larger function. The industry makes the analogy of stringing together software objects in the same way as integrated circuits are strung together on a printed circuit board. "The implications are large. Imagine building your control system with Visio instead of a $5,000+ proprietary package," says Dan Miklovic, analyst, Gartner Group, Stamford, Conn.
Object technology was only a programming tool a few years ago, but commercialization now advances on two fronts. Microsoft's Object Linking and Embedding (OLE) begat the common object model (COM)-the object programming in Microsoft operating systems and applications. Today, this approach matures through OLE for Process Control (OPC).
Where there's OPC, you'll find Sun Microsystems' Java right across the street making similar promises. Java first emerged as object-oriented programming for network and Internet applications, but provides capabilities that make it popular for control. Java is platform blind-it will run on virtually every major operating system and browser.
The advantages of object technology are the growing availability of large libraries of objects; portability across networks and Internets; and easy, visual assembly. Some applications are showing 50% reductions in development time.
The biggest obstacles have been security across networks, familiarity, and the commitment to the learning curve, but 1998 should bring more practical opportunities.
Software Foundations
It really does come down to Windows-both NT and CE-as the software platform and Java as the alternative programming architecture that PC-based real-time control will be built around.
AMR predicts Windows NT will dominate the plant floor by 2001. "The NT operating system is better equipped to manage the market's changing software needs," says AMR president Bill Swanton. While this may not always be the best thing for your real-time control needs, the operating system on the plant floor will influence your end users' preference for the control system platform you build into your machines. Windows NT, with several third-party, hard real-time operating system extensions and Visual Basic for Applications (VBA) scripting language, provides the operating foundation that many third-party solution providers use for PC-based control.
The scripting language lets the solution provider build process-specific applications and still provides the end user further customizing capability with considerable ease. Windows CE has promise provided its beta version solves several embedded application problems, including functional shortcomings with flash disks. Miklovic is convinced, saying, "This can be the hottest thing [in factory automation] since the IBM PC." He believes it will have enough real-time control to be useful, and it integrates well with Windows-based tools and applications.
Java's great attribute is portability-it solves cross-platform problems-and that's attractive to program developers. Even Microsoft supports it, although Sun alleges that Microsoft is giving their version a bitter, MS-only flavor. Embedded Java appears well suited for low memory and storage applications. As much as Miklovic likes Windows CE, he says, "Since Microsoft can't squeeze even CE into a $5 chipset, expect Java to work itself into control at the device level and move on to the controller level."
My Kingdom for a Network Standard
As we move through the year, the march to connectivity will continue with much faster advances in the previously quiet motion-control sector. An industry-expert panel discussion at ISA Tech/97 concluded that DeviceNet and Sercos are motion control's buses of choice-Sercos if the application is motion-centric with some I/O, DeviceNet if the application is I/O-centric with some motion.
"DeviceNet in the U.S. and Profibus in Europe will emerge as clear leaders, although sensor-bus technology will not dominate," says Miklovic. The reason for that could be the emergence of Ethernet.
Faced with too many proprietary and standard control networks, some users are exploring Ethernet for control applications. Ethernet TCP/IP is omnipresent-it's sold in high volume all over the world. Ethernet PC boards sell for about $50 compared to $900 or more for a control or device-network PC board. "The growing acceptance of industry-standard information technology (IT) is improving Ethernet's chance of becoming the backbone of future high-speed control and device networks," says Rich Mullen, senior analyst, Automation Research Corp. (ARC), Dedham, Mass. "Many PCs today include an Ethernet interface and Windows NT has built-in Ethernet drivers." The movement is also fueled by user concerns that existing control networks may not provide enough bandwidth for current and future requirements.
Ethernet offers easy connectivity to the Internet-devices need only an IP address. "Many emerging Internet-based technologies are finding their way into the world of automation," says Mullen. "Java is being used in applications from Foxboro and Westinghouse. Since Ethernet is already the network of choice at the business level, its presence at the control level will make sensor-to-boardroom integration easier."
The limited number of control products supporting Ethernet is its biggest drawback today. While this picture is rapidly changing, a careful examination of the available products might disappoint any 1998 expectations.
Adapt Well and Prosper
A number of industrial equipment makers are beginning to look hard at alternatives to traditional PID-algorithm feedback-loop controllers.
Many engineers use PID loops for motor velocity and absolute position control. Some say that with rapidly changing conditions, derivative is the most useful. Just as many will tell you that derivative is awful for rapidly changing conditions. Sounds like an imperfect control solution for today's requirements.
The microelectronics industry is trying to improve methods of monitoring and controlling dimensional accuracy and precision of the sub-micron features formed on wafers during processing. Smart sensors and nonlinear adaptive control are gaining interest for plasma processing equipment.
Robotics and machine tools are looking at adaptive feedback loops to help provide real-time kinematic control in very close-tolerance arm movement and complex grinding tasks.
Some process industries have successfully applied adaptive control. Universal Dynamics, Vancouver, B.C., seems to have the only commercial predictive/adaptive controller for difficult processes. Users like the controller because it adapts to processes that are nonlinear, higher-order, dead-time varying, or have changing time constants and gains. It learns on the job, reducing long setup times and the detailed process knowledge required by advanced PID strategies. The approach, or one similar to it, should work well for applications needing precise motion control and positioning, in particular where some process control may also be involved.
Psychic Control Without a 900 Number
Predictive device monitoring is gaining credibility as a practical diagnostic tool for the near future. "There are too many costs involved with just waiting for equipment to die," says Dr. Carl Talbott, an active leader in MIMOSA, the Machinery Information Management Open Systems Alliance. He has been very instrumental in promoting device condition monitoring from the end users' perspective.
For the time being, IQ PreAlert from Rockwell Automation/Allen-Bradley, Cleveland, is the only hardware/software solution-this one is for motors. It uses device design criteria to analyze and respond to motor condition data collected by embedded sensors. An expert module uses specific algorithms that, with a big enough historical database, may accurately predict failures.
"But there's another big payoff," says Hale Hillhouse, Kingsport, Tenn.-based Eastman Chemical's manager of reliability technology. His plant has been the beta site for a number of predictive, condition-monitoring trials. "This technology can turn devices like motors into sensors. In combination with established process controls, an intelligent motor may be able to identify pump cavitation trends, verify flow and pressure readouts, and be a valuable complement to control technology."
"Today, we control setpoints by responding to actual variation in a process. PID loops, adaptive loops, and similar technologies are reactionary," says Talbott. "Condition monitoring technology is preemptive." As Hillhouse's view of the motor as a sensor and diagnostic tool becomes real, Talbott sees, "a control system that takes preemptive action even before the process variable appears to start changing. This would be a huge step-change in control technology." This may not be next year's off-the-shelf technology, but advances in smart sensor miniaturization and predictive algorithms are bringing the day closer.
Thin-Clients-Not a Modeling Agency
A network PC display is very different from the scaled-down, remote-access, dumb terminals of mainframe days gone by, or UNIX X-terminals of 10 years ago.
These units-the difference between thin-client and network PC is semantics-have internal logic, but the function of the internal processor is restricted and may require little more than a 286-level processor and 640 KB of RAM. They have modems and browsers, but very little storage. The applications stay with and are processed at the server, while display processing is done at the client. The client retains the multitasking operator-interface capability available with intranets today.
Cost savings are the obvious reason for interest in this technology. A thin-client is estimated to cost 50-60% less than the PC that currently occupies that space. Life-cycle costs should accordingly be superior.
Zona Research, Redwood City, Calif., a market research group emphasizing Internet technologies, projects the commercial market will grow from today's 1.7 million network computers to 6.7 million by 2000, evolving primarily as a replacement strategy for companies that refresh their technology level.
Concerns about using thin-client are similar to misgivings about networks. Bandwidth may be insufficient for data capture, and many potential users don't view intranets and Internets as reliable or secure enough.
1998 might provide some initial success stories-maybe even the first account of an OEM dialing up mission-critical control applications from the end user's server.
Wireless Connections
It's a stretch to think your customers will be telling you to interface your machine with its wireless network in 1998, but the technology may be emerging, although it may take time to gain noticeable, standardized, application strength. Business Week, for one, called wireless data communications one of the most over-hyped technologies of the '90s.
The promise of faster application comes from last year's ratification of 802.11, the new standard for wireless medium-access control and physical layer specifications, by the Institute of Electrical and Electronics Engineers (IEEE). The standard is designed to be a broad-based wireless network protocol to replace wired networks like those based on Ethernet.
Sematech, the Austin, Texas-based non-profit consortium of integrated circuit manufacturers, has begun to develop a sensor-bus wireless network. While the elimination of wiring is an important contaminant-minimization step, the cost savings and space implications are considerable in any industrial application.
Wireless systems have been available for remote inventory reporting and bar code reader applications, but recently a few companies have begun to promote wireless process monitoring and control applications for remote devices using the Internet over cellular communications systems. Motorola and Microsoft formed an alliance in January-albeit initially at the consumer level-to use wireless technology with Windows CE. This should give application development a jump start.
Ain't Got Skills
The future of control can look quite positive given this list of new toys. But a number of industry players are concerned that sufficient levels of skilled manpower won't be there to meet the demand for technology competence, particularly in high-growth markets.
The U.S. Dept. of Commerce reports that American universities are annually turning out about 25,000 graduates with higher-level computer skills against a demand of 100,000. Two industry perspectives are sharp, a bit cynical, but probably accurate. "An OEM can make a great, open machine," says Richard Hoss, vice president of Hoffman Estates, Ill.-based Rexroth-Indramat. "But then he ships it to a developing, high-growth market where untrained personnel can't deal with [the controls]."
The OEM will have to support the market he ships to, or not sell there. At the moment this is the only solution and it may complicate the level of detail that an OEM must include about the design of his control system. Even within Western markets, there is concern that user skill levels aren't keeping up. "The customer base doesn't have the desire to learn how to use the stuff," said Jay Greyson, vice president, Cleveland Motion Controls, at a recent gathering of motion control experts. "They don't want the responsibility. They know how to replace a gear, but don't care if they ever learn how to drag and click an icon."
Continue Reading
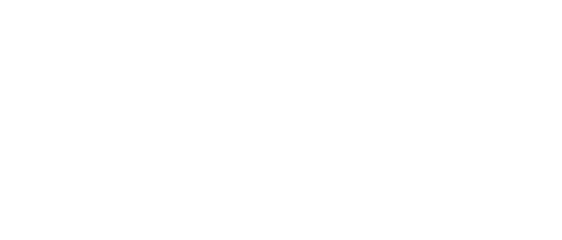
Leaders relevant to this article: