That in a nutshell, is how engineers from those companies summarized their experiences during an end-user panel at the April OMAC meeting held during the CMM (Converting Machinery & Materials) Show in Chicago.
Benefits Already Apparent
Although the OMAC packaging working group has had some success over the past two years in identifying common open architectures in packaging equipment, OMAC members would be the first to admit most of the hardest work still lies ahead.
Nevertheless, when asked during a panel discussion if they've profited over the past two years from their involvement with OMAC and the pursuit of open architecture controls, engineers from Hershey, M&M/Mars, and Procter & Gamble were bullish. "We're seeing quotes from our key suppliers now using motion controls and other components that are much more open," confirmed Gary Downey of Hershey Foods. "We are seeing lower cost and smaller footprints, too."
Bob Martell, motion control technology leader at P&G and chair of the OMAC packaging working group’s connectivity/architecture subcommittee, concurred. "In the past, if we wanted a standard the OEM didn't provide, it was quite an upcharge, because the OEM may not have had the resources [to accommodate the request]," explained Martell. "They had to develop that expertise, and we would end up with a machine that probably didn't run as well as with the proprietary controls offered by the vendor. So we ended up with a machine with higher cost, longer leadtime, and little support. Now with open architecture, P&G and its machinery builders are all saying the same thing, so it's reducing some of the other engineering we were paying for in the past."
P&G's OMAC involvement is expected to reduce integration costs globally. With manufacturing operations in more than 70 countries, P&G's global nature is also at the root of its involvement with OMAC, claimed Martell. "We buy machinery from OEMs all over the world, and we place them in plants all over the world. We want the assembly of packaging lines to happen in a seamless way. Open architecture is a way to do this. If we had to coordinate every OEM's design, that adds a lot of cost and time into our development schedules. The demands of our market are to be faster, to bring products to market more quickly at lower cost. Open architecture will help us."
Finally, the evolution of the components themselves is contributing to reduced costs, according to Steve Ford, controls engineer with M&M/Mars. "Control components have more functionality, so we don't have to buy as many individual components now. We're able to merge functions such as logic and motion control in the same control, and that reduces costs significantly."
OEMs Are More Collaborative
All three end-user panelists agreed that the open architecture dialogue created by OMAC has completely altered the dynamics of their relationships with machinery builders.
"One of the most revealing things for me and P&G is that there really are a lot of common needs among machine builders and end users," said Martell. "Before, the relationship between the two was often fraught with conflict. We had our preferred platforms and the vendors had theirs. Open architecture has allowed us to collaborate [using a common control platform]."
Hershey's Downey concurred. "In OMAC, we're discussing and sharing information with competitors, OEMs, and technology suppliers that, in the past, we might not have. We're doing that to try to make us all succeed. There's great potential here. The more people involved, the better."
The pursuit of a common, open architecture is yielding internal benefits at the panelists' companies. That's especially the case at Mars, well-known in engineering circles for its decentralized engineering operations. "Since each site has its own engineering department, it's difficult to maintain standards from site to site," said Steve Ford of M&M/Mars. "Open architecture helps promote standards within our own company."
Downey has noticed an attitude change regarding electronic versus mechanical controls. "Our packaging engineers used to say, 'Why do we need a servo?' Now they say 'Why doesn't it have servo? Why this big frame? How are we going to get in there and work on it?' "
P&G views its participation in OMAC as a competitive advantage. "I believe the directions we're setting are going to be the final outcomes for the industry," declared Martell. "As we decide OMAC's direction, we already have the inside track. It helps make our decisions a lot quicker. We know the direction of the technology months ahead of time versus waiting for an article in a publication to show up."
PackML Group Formed
The April meeting provided the forum for the formal kick-off of the PackML subcommittee. This group formed after members at the OMAC meeting in February realized that defining standard machine states is key to interoperability on a packaging line.
The PackML subcommittee is led by Fred Putnam, a consultant representing Markem Corp. Subcommittee members also include representatives from Hershey, Procter & Gamble, Unilever, Bosch Packaging, Elau, Indramat, and Rockwell Automation. The stated mission of the PackML group is to develop naming convention guidelines for packaging machinery data communications. The objectives are to collect—from users and suppliers—existing machine state naming conventions, tag name conventions, and machine state definitions. From that, the group hopes to arrive at a common set of OMAC-recognized naming conventions that can then be promoted to end users and machinery builders.
Finally, Fred Hayes of the Packaging Machinery & Manufacturers Institute (PMMI), representing the education subcommittee of the OMAC packaging working group, provided an update. Three online surveys were launched on PMMI's web site at the beginning of April: one for end users, one for OEMs, and one for technology providers. The goal is to try to determine the educational needs and formats for educating each constituency about open architecture controls.
Continue Reading
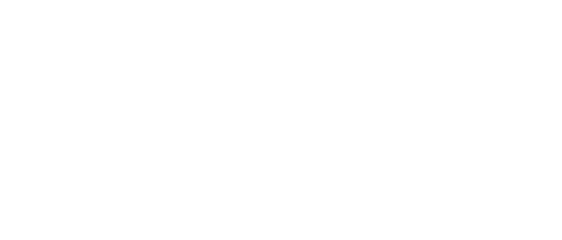
Leaders relevant to this article: