By Loren ShaumLONG BEFORE the current world of sophisticated mechatronic solutions for machine automation emerged, many industrial OEMS embraced pneumatic solutions. In certain machine segments, designers had few cost-effective mechatronic solutions, and were more comfortable with the simplicity of pneumatic valves, cylinders, actuators, motors, etc., and the plumbing associated with their operation. They incorporated them into every design they could.
But as machine performance requirements evolved, builders had to adopt alternative solutions to be competitive. For more sophisticated applications, the move to mechatronic solutions became necessary. Today, for more complex and flexible machines, mechatronics dominate, especially where quick changeover to another part/assembly production, higher precision, and more speed are essential.
However, even on these more precise, higher-speed machines, many pneumatic components are incorporated into the design—creating a hybrid solution of sorts. For automating machines with fixed or limited variability in output or product, pneumatic components often dominate.
Large segments of manufacturing operations today have a huge installed base of pneumatically operated equipment. According to several companies that sell mechatronic and fluid-power solutions, the legacy installed base is so large that pneumatic component sales for maintenance purposes far exceed mechatronic equipment sales in many parts of the country. About the only segment of pneumatic control that’s become virtually extinct is pneumatic logic control. Even so, pneumatic logic still is used in some explosion-proof applications.
An argument against hybrid machine solutions might come from designers who prefer centralizing their pneumatic power source (pumps and compressors). Non-fluid-power solutions most often require power sources integrated at or nearby the point of machine action. However, with the advent of multiple interfacing capabilities integrated into pneumatic components and equipment, such as the various fieldbus interfaces, the ability to centralize controls for pneumatic equipment becomes significantly easier.
Advances in Pneumatic Control
The introduction of servo-pneumatic systems has meant new applications for pneumatics that were, not too long ago, reserved strictly for electric servos driving optimized mechanisms. One noteworthy application is controlling press rolls on a lumber mill machine (See Figure 1 below), in this case, built by Pacific Fluid Systems, Portland, Ore.
The controller positions the press rolls that hold logs, cants, or pre-cuts as they transfer through the saw in a mill. Controlling the press rolls means holding the logs tightly without damaging them, based on a previously defined profile.
The sensor-controller-actuator combination positions press rolls that hold logs, cants, or pre-cuts as they transfer through a lumber mill saw. The control of the press rolls has to hold the logs tightly without damaging them, based on a previously defined profile.
Figure 2 below diagrams a press-roll station configuration designed and built by Pacific. These configurations typically are used on planers, edgers, and band mills. Lineal wood-feed speeds can be as fast as 2,000 board-ft/min. The press rolls have to sustain a force of 1,200-1,800 lbs, depending on log type and speed, to keep the logs from moving as they pass though the saw. Cylinders are usually 6-in. bore.
“Pre-programming desired cylinder position and forces are critical to this application,” says Tom Wells, Pacific’s engineering manager. “It allows us to operate in a higher-bandwidth, proportional-control mode to get the cylinder to the position where it can decelerate to the final position. Once there, the controller moves to a controlled stop, then switches to a force mode to sustain the proper pressure. This reduces our setup to hours, rather than weeks.”
A typical application is a machine called an edger. For this machine, there is one station of dual press rolls at the input to the saw and another at the output. This application demonstrates the advantage of auto-tuning of the active damping algorithms.
“With these advances, it’s common to reduce the time required to tune a system by an order of magnitude,” claims Steve Nylund, CEO of Delta Computer Systems, Vancouver, Wash., a provider of electro-pneumatic motion control solutions. “For the machine builder and customer, reduced time to machine commissioning is highly important. The use of various standard communication interfaces that allow the machine control designer to implement a best-in-class solution also is a big plus.”
Another advantage of pneumatics for this application is the inherent compliance. Where surfaces are continually changing, adaptation to the deviations is quicker and more resilient than with other technology.
“New servo-pneumatic systems are capable of much smoother and more precise motion compared to old ‘bang-bang’ valves,” argues Nylund. “These electronically controlled, proportional servo valves provide a better choice in applications where the wear in pneumatic systems is less likely to directly affect motion accuracy.”
Another growing innovation is fluid-power-enabled motion control. These controllers perform closed-loop control using position and pressure feedback. This dual-feedback control capability allows the controller to compensate for classic pneumatic nuances such as air compression/expansion and valve nonlinearities. An active-damping approach provides more stability for higher performance than previous electro-pneumatic solutions. Controllers now can handle one to eight axes simultaneously.
Delta’s system includes a tuning wizard in its controllers that enable graphical tuning (See Figure 3 below).
Tuning Wizards in software make it easier to optimize servo-pneumatic motion, and include the advantage of auto-tuning of the active damping algorithms.
“Any application needing fast, short strokes of motion involving many actuators is a good pneumatics candidate,” says Frank Latino, product manager, Festo USA. “Other suitable applications are where high force is needed in a small area, and point-to-point actuation, whether linear or rotary.” Latino adds that users naturally think of the possibilities of pneumatics for spark-free applications, and adds that pneumatics can be very cost effective where the precision of an electric actuator isn’t required.
Hybrid Control Optimizes Ice Handling System
Robots and Automated Equipment Services Co. (RAESCO), in Syracuse, N.Y., builds ice-handling equipment, and offers other machines and services. RAESCO’s machines palletize ice at 40 bags per minute. In developing the control system for its machines, RAESCO engaged Applied Automation Controls Inc. (AACI), also in Syracuse, as a control solution consultant. AACI offers machine solutions that use mechatronic and pneumatic technologies.
“We worked together to complete a design based on RAESCO’s concept,” says Tom Swenton, AACI’s president. AACI provided the control components to optimize the machine design.
“The design went through a few changes from prototype to production,” says Swenton. “The present design implements three axes of electric servo control—two from conveyors and another from a gantry mechanism. These axes required higher speed and positioning accuracy than a pneumatic solution could provide. However, there are four motions to align and rotate the ice bags as they’re presented to the collation station from the in-feed conveyor. Moreover, there are various clamps and lockouts implemented with pneumatic solutions. These were legitimate choices for these motions because they provided more than adequate controls and were more cost-effective.”
Rich Huchanski, RAESCO’s president, adds, “A pneumatic solution provides us with an adaptive capability because the ice bag shapes vary so much from bag-to-bag as they enter the collation station. Using air pressure to sense when vacuum cups come in contact with the bags allows the cups to adapt to the bag shape. Using this compliant adaptation, we can align bags uniformly before delivering them to the pallet.” The machine is capable of lifting as much as 150 lbs, but generally palletizes 7-lb. bags in pallet loads of 300.
This application indicates that a hybrid solution not only can optimize the capabilities of many machines, but also can be the most cost-effective solution.
“For many machines, pneumatics solutions still are preferred because of cost,” says Steve Whyte, business unit manager for controls distributor BW Rogers Co., Macedonia, Ohio. He cites a project in which ITW-Akron Standard uses an all-pneumatic solution on an inspection machine. “Electromechanical solutions drive the cost much higher than the customer can justify,” says Whyte.
So, even though the cost of compressed air continues to increase, pneumatic solutions still are preferred by many machine builders.
Improved Connectivity
“Ethernet technologies have given a tremendous boost to efficiencies of pneumatics in factory automation, especially if there is a very high density of actuators,” says Festo’s Latino. “Consider an installation with more than 2,000 actuators. Valve manifolds can be loaded with up to 128 valves, and sometimes more. This reduces the overall quantity of valve manifolds, but there still are 30-40 manifolds. Ethernet brings the bandwidth to reach all of these valves in the shortest time possible.”
Other fieldbus systems would have required multiple channels or networks, increasing costs in hardware, commissioning, and maintenance, according to Latino. In addition to the huge leap of bandwidth, IT services like web server, file transfer, and e-mail can provide unparalleled diagnostics, especially with COTS diagnostic tools and media.
Integrated control in valve manifolds makes pneumatic power/control a better alternative these days, says Latino. “Sensors and diagnostics embedded into valve manifolds, system diagnostic algorithms for diagnosing a total pneumatic system, and using Ethernet and open standard technologies such as OPC or industrial Ethernet protocols tie all these together, and improve a control system, he adds.
What’s Next
Where there are high forces and an application requiring compliance to changing load variables, like the press roll and ice bag applications, pneumatic solutions seem to be preferred. And there’s no evidence suggesting this is going to change in the near future. Several companies focus on making pneumatic solutions more responsive, while mechatronic solutions sometimes must be detuned to behave similarly to a pneumatic solution. This is especially true for motion control applications that move to surfaces that aren’t exactly defined.
The Other Fluid Power
MACHINES WITH large force or thrust requirements represent a segment in which neither pneumatic nor mechatronic solutions are practical—from price and/or performance standpoints. This machine genre includes presses, benders, formers, crushers, etc. These machines use hydraulics to achieve the force levels necessary to complete required work.
“Hydraulics in machine design is another matter, since only a few machine designers have any idea of what’s available, and even less understanding of how to apply the right component to a given situation,” says Bud Trinkel, president of Hydra-Pneu Consulting, Newburgh, Ind. “Ninety-eight percent of my work is in hydraulic circuits.”
This might suggest that pneumatic solutions now are such a known commodity that many machine designers can include pneumatic components in their machines without hesitation.
About the Author |
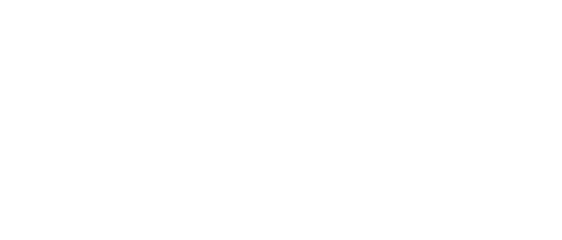
Leaders relevant to this article: