I |
T'S A PRETTY SIMPLE PREMISE: Without dependable and accurate lines of data transmission, a system cannot be properly controlled. Signal conditioners often are necessary to ensure the accuracy of analog control and process signals, improve transmission accuracy and reduce the effects of EMI/RFI (electro-magnetic/radio frequency interference) that can plague voltage signals and their high-input resistances.
A signal conditioner’s main purpose is to provide isolation and signal transformation. Over the years, technology has moved from transformer isolation to solid-state isolation. This has allowed the cost of the product to be reduced dramatically without sacrificing functionality.
That’s Harsh
Welding Services (www.weldingservices.com), Atlanta, is in the pipe welding and weld metal overlay business, and the company designs, builds and operates the remote, semi-automated welding equipment used to support its business. (See Figure 1)
“There are more choices today for signal conditioning and signal processing solutions for sensor network data transmission and collection,” says Donald Lupo, director of marketing & sales, process products, for Acromag (www.acromag.com). “Key differences are being made in space and cost saving designs with multi-channel instruments and universal power supply options for global applications.”In most cases, the smaller the size of the I/O, the higher the value for the customer. Basically, more information is packed into less space. This should translate into cost savings for customers and the ability to make better use of their plant floor.Signal conditioners have evolved from resistor-based designs that were housed in octal socket housings, to analog precision resistor designs in industrial housings, and now on to highly integrated microprocessor designs that fit in 6 mm-wide housings. “The industry is moving towards decentralized control of process signals and highly efficient compact and space-saving solutions. Peripheral devices, such as signal conditioners, should follow this trend and allow users to install remote control systems in remote locations,” says Mathews.Belcher needs a few specific features. “The devices we use are DIN-rail mounted, and allow us to replace the unit simply by unplugging connectors, he says. “We prefer to retain the factory calibration for the module, and do any calibrations required in software. This allows us to field replace modules without much adjustment.”Lupo says device performance has increased in accuracy, calibration, and stability with the use of microprocessors and 16-bit sigma-delta A/D converters and D/A converters. The 16-bit sigma-delta A/Ds for analog contribute to higher accuracies and stable measurements. “The trend for data-acquisition is certainly moving away from 12-bit A/Ds, even though many sensor measurements or applications may not need this kind of accuracy,” says Lupo.As isolation technology continues to develop and become more cost-effective, isolation is going to be transitioned into receiving devices such as PLCs or data acquisition systems,” says Fairfield. “The purpose of the signal will then trend towards a conditioning device and away from an isolation device.”When Does It Matter?
There are simple tests to determine if isolation is required, such as measuring voltage on the ground circuit or measuring voltage on the shielding of a cable.Typically, areas with high electrical noise devices, as Belcher described, require signal conditioning more than other areas. For existing systemsand that would generally mean analog signal requirementsusers will know right away if their data is not accurate or stable enough to meet requirements.Some of these interfering devices include drives, motors, lighting circuits, etc. “Even in very clean environments, electrical isolation may be required,” says Fairfield. “One of the most problematic areas in a plant is running wire close to a fluorescent lighting fixture.”Welding Services also uses signal conditioners to directly measure environmentally harsh, non-isolated feedback signals. “This prevents the noise generated from ground loops and protects the controller electrically as well,” states Belcher. “We use Dataforth (www.dataforth.com) when we need to monitor the harshest signals, since they have the largest absolute maximum ratings. The modules are configured for only one input and output range, with span and offset being adjustable.” (See Figure 2)FIGURE 2: ALWAYS USE PROTECTION
Belcher also uses Phoenix Contact devices for most of his prototype and custom applications. “We use the Phoenix MCR line for prototypes because of the short lead times associated with Phoenix and the option to configure both the input and output signal,” he says. “Phoenix's configurability also allows us to stock one part number, which we can use in a wide variety of applications, and are great for short-notice custom designs. When a design is completed, and the system has been thoroughly tested, we tend to use Dataforth since it doesn't need to be configured prior to commissioning.”Signal conditioning both in analog, digital and serial data applications will improve signal integrity when used in applications where harsh environments are prevalent and accuracy/integrity of the signals from interference and ground loops are common, adds Mathews. “The effect of using a conditioner is immediate improvement and correction of incorrect signals,” he states. “In theory, using a signal conditioner is the easiest and least expensivein terms of total maintained costmethod of ensuring signal accuracy, but there are a few stumbling blocks that must be avoided to prevent mismatches in the control system.”Experts all agree that if you choose the wrong isolator, your loop simply will not function. “The mismatches occur because power supplies can be incorporated in many different places in an instrumentation loop,” explains Mathews. “They can be located either at the transmitter, the receiver, or in the loop. Since many isolators are specified only after a system is operational, it is necessary to know how the devices are powered before ordering an isolator.”Ultimately, the user needs to solve his signal conditioning problem in the most cost-effective way. Signal conditioners are typically used with PLC systems. There are several applications for which a signal conditioner can be cost-effective, says Fairfield. “If a customer has only one signal that requires isolation, purchasing a single signal conditioner may be more cost-effective than upgrading to a fully isolated analog input card,” he states. “But if a customer is wiring in a thermocouple, RTD or similar sensor, it may be more cost-effective to convert the sensor signal to a mA or V signal and use an existing PLC input, versus purchasing a new thermocouple/RTD input card.”Lupo has additional advice. “For new systems with analog signals from thermocouples, RTDs, 4-20 mA loops, and voltage loops, users should study the grounding and locations for the sensors, transmitter/amplifiers, I/O cards, and the control/monitoring system,” advises Lupo. “As a rule of thumb, analog signals being monitored or retransmitted should be equipped with isolation.”An isolator needs a source of power to operate, but it can not interfere with the power needed by the transmitter or receiver. Isolators can get their power from one of three different sources: an independent power supply, the input loop, or the output loop.I/O devices equipped with isolation help eliminate the effects of multiple grounds in a system and reduce/eliminate electrical noise generated by devices such as variable-speed drives or other high-voltage equipment. “Moreover, if users perform monitoring and control functions over a properly selected digital serial network for their application, such as Hart, Profibus, Ethernet, etc., they should gain better overall system performance and control over time and temperature due to the digital two-way communications versus one-way analog 4-20 mA signals,” says Lupo.For isolation and differential inputs, Lupo recommends device I/O should include three-way, 1,500 V isolation between I/O, power, and network. “Moreover, analog inputs offer differential measurements to further break up ground loops, protect the system, and eliminate the need for isolators,” says Lupo.TED IS HERE The approval of the IEEE 1451.4 standard in June of this year has paved the way for signal conditioning devices capable of reading the Transducer Electronic DataSheet (TEDS) information--an electronic copy of the sensor's datasheetmaking sensors, in effect, plug-and-play. “This dramatically reduces the amount of time required to set-up a sensor measurement and also greatly increased the accuracy of sensor measurements,” says Ryan Wynn, Data Acquisition Systems Product Manager, National Instruments (www.ni.com). "As a result of sensor parameters now being stored electronically on each individual transducer, sensor vendors can now precisely characterize each individual sensorboth their output curves and calibration parameters.”
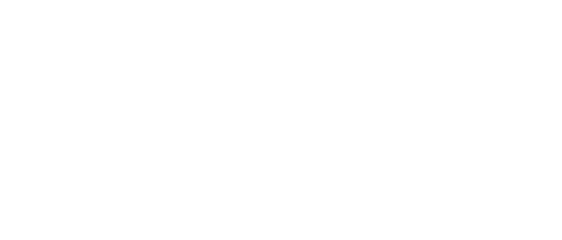
Leaders relevant to this article: