There was a time when many industrial machine builders had nearly everything they needed to build machines in house: designers, mechanical engineers, electrical engineers, programmers, technicians, and production facilities for precision machining, mechanical fabrication, making wiring harnesses and control panels, and assembling and testing complete machines.
These industrial OEMs also often were capable of installing new machines all by themselves at the customer plants, integrating them into the customer's assembly line or manufacturing system.
Very little was ever farmed out to external suppliers. Production of castings and printed circuit boards probably were sent out, and machine builders bought standard limit switches, components, and CNC controls off the shelf, but they designed and built just about everything else.
Then came today's troubled times and new machine performance criteria. Modern times came with layoffs, pullbacks, reorganizations, acquisitions, mergers, and all the other gut-wrenching realignments of the 1990s. By the mid-1990s, outsourcing had reared high its ugly head.
As you'll see, the outsourcing phenomenon bears watching. This article will bring you up to speed on the depth and breadth of what's happening throughout manufacturing in the U.S. Its impact on the machine building community is inevitable, the only question is degree and timing.
It has begun
"Outsourcing in the machine tool industry no longer covers the mere purchase of parts by OEMs," Woodruff Imberman, president of efficiency consultants Imberman and Deforest, said back in 1998. "It includes the purchase of design and product assemblies, product testing, inspection, and sometimes even sales and customer service. OEMs ask suppliers to provide logistics and materials supply, services covering technology, material requirements planning, procurement, inventory monitoring, accumulation, and replenishment." And so it began.
We turned the corner into the 21st Century, and many industrial OEMs left behind the old way of building machines. Some laid off key personnel and divested themselves of expertise and capabilities that were outside their core business of making machines.
Simultaneously, control systems changed. Over the past few years, they've gone from being an industrial machine builder's simple, custom-made dedicated controller, to name-brand CNCs and PLCs, and now to open architecture, PC-based controls, and industrial networks. Just as machine builders were losing some of their in-house control expertise, the entire control scene got more complicated.
"During downsizing, many companies began looking to outsource their control systems expertise," explains Herb Johanson, marketing manager at system integrator Concept Systems. "They cannot afford to staff a group with the same knowledge base that you can get from a good integration company."
So now, instead of being self-sufficient, some machine builders are starting to become dependent on outsourcing and collaboration with suppliers in similar fashion to other industries, it appears. Market researcher IDC says 20% of the electronics manufacturing market now goes to contract manufacturers. It expects that share to reach 27% by 2006, according Kevin Kane, program manager for IDC's Contract Manufacturing Services.
The 2003 AMR Research/National Manufacturing Week trade show survey of global manufacturing trends shows that 17% of design work and 17% of maintenance currently are being outsourced. "It's still a do-it-yourself market," says the study. "Third-party and automation vendors need to convince companies outsourcing is worth it."
From what we've been hearing, fewer and fewer companies need much convincing any more.
Outsourcing everything
All kinds of companies are outsourcing everything from aftermarket maintenance to information technology (IT). Gary Blankenmeyer, vice president of Bosch Rexroth, says maintenance is the second most-effective business function to outsource, led only by transportation.
"We see a small but growing number of plants using machinery built by our OEM customers outsourcing maintenance extensively," says Blankenmeyer. "Manufacturers in the automotive, machine tool, and semiconductor industries would rather focus on their own core competencies and outsource other activities." With such transactions firmly in place, how much of this after-sales support comes back to the industrial OEM as added revenue streams or added cost is the question. Right now, it's a mixed bag of answers.
"We frequently use outsourcing in combination with our inhouse staff in the development phase of our projects," says Don Kinley, chief engineer at Eaton Leonard, a manufacturer of tube forming automation in Vista, Calif. "Under these circumstances, the required system behavior, performance requirements and development guidelines can be defined and documented to the outsource firm up front. The outsourced deliverables can then be measured against these requirements and there are fewer surprises during the integration and test phases of the project."
"Outsourcing is no longer relegated to just non-core functions," says John Borden, leader of First Tuesday Atlanta, a business organization in Atlanta that sponsored an outsourcing roundtable in April. "Organizations are rapidly outsourcing mission-critical and core operations, such as research and development, customer care, and manufacturing."
One significant trend in the AMR/NMW study is the large number of companies that are building or acquiring manufacturing plants in China and Mexico. China now accounts for nearly 5% of world exports, says The Economist.
"Unless you have traveled to China in the past six months, the image you have is probably out of date," says Jim Hennessy, Asia Pacific regional director for ExxonMobil Lubricants & Specialties. "The country is modernizing its industrial capacity across the entire geography."
Foxboro demonstrated this recently when it unveiled a series of replacement I/O and control system printed circuit boards, which it said were being made by a supplier in China. Close visual inspection of the boards and components showed excellent quality.
Why?
Why are companies outsourcing? "Cost reduction continues to matter and to be a key goal of outsourcing," says Michael Corbett, president of outsourcing facilitator Michael F. Corbett & Associates. "In other cases, outsourcing is a way to take an existing fixed-cost structure and turn it into a variable cost, in which expenses can move up or down as the business climate dictates."
Imberman says outsourcing helps companies keep costs down. "If you made all the parts yourself, you'd have to pressure your employees to find ways to make everything at less cost," he says. "With outsourcing, you just pressure your suppliers instead."
The Outsourcing Institute's Fifth Annual Outsourcing Index says cost is secondary. The number one reason is to improve company focus. "Clearly, outsourcing is no longer just about saving money," says the institute's web site. "It's now about doing things quicker, more efficiently, getting to market faster than your competitors, having maximum flexibility with your workforce, and gaining access to high-quality employees you otherwise could not afford."
Take that for what it's worth. It's what you might expect an organization that promotes outsourcing to say. The impact outsourcing has on employees probably is the least of its worries.
In some ways, the survey results suggest a survivalist mentality. The idea that outsourcing has a positive influence on growing the business rates but a whisper in one of the surveys, and no mention at all in the other.
Outsourcing vs. inside jobs
The hardest-hit higher-tech employees may be the poor devils in Information Technology, who are facing outsourcing in record numbers. "On average, 60% of IT spending now goes to external companies, while 40% goes to staff," says Bart Perkins, managing partner at Leverage Partners, Louisville, Ky.
We ought to be concerned about our IT colleagues. IT inside a company once required extremely skilled and educated people who understood the technical details of complicated processes. Now, such talents are a dime a dozen in India, Mexico, Brazil, and China. "Eight cents on the dollar for IT labor in India is too compelling," says Marty Chuck, CIO at Agilent Technologies, as he explains why Agilent is outsourcing.
CAD/CAM is closer to the hearts of control system designers, and outsourcing is afoot there, too. Ford Motor is shipping its CAD/CAM and application development tasks to a subsidiary in Chennai, India. This effort is expected to save the automaker $30-60 million per year, because labor costs are a fraction of those in the U.S.
Like IT and CAD/CAM, control system design requires extremely skilled, highly educated engineers who understand the technical details of complicated processes. As you explore the possibility of outsourcing various parts of your control systems, keep in mind that control system design engineers in India and other countries make a fraction of what you do. Don't outsource yourself out of a job.
Some manufacturers might even try outsourcing after-sales support and maintenance, but this is difficult for a machine builder, says Kinley.
"There are two after-sales support jobs involved-,field service and maintenance-,and neither one can be outsourced easily," he says. "Field service requires a highly trained individual who can identify that a problem exists in the electronics, hydraulics, pneumatics or servo motors, and then repair it. Maintenance of a machine's control system requires someone who understands the program code and knows how to update it in the field."
Both jobs require so much training it is nearly impossible to find anyone who can do it, says Kinley. "If we do outsourcing of control systems, it's just in the development stage. We don't rely on an outsider to service our systems in the field."
Control system design
It seems strange, even in a magazine called CONTROL DESIGN, that we have to consider the possibility of outsourcing control systems.
"The sheer number of options available for automating traditionally localized machine controls, and the desire to interconnect these to information systems, have placed a real burden on OEMs," says Matt Bothe, senior automation engineer at CRB Consulting Engineers. Not only must they control the machine, they have to deal with many non-control issues as well, he says. "OEMs, machine designers, and specifiers must be able to handle the multi-party collaboration required to meet the needs of end users."
Bothe deals mostly with controls for process equipment and machinery, but the issues are similar in all machine-builder segments. "End users want to make clean-in-place (CIP) equipment design a highly collaborative effort with mainstream process controls. Coordination between OEM equipment, particularly those with regulatory significance, and central control is necessary. Even building automation is finding its way into the mix."
Another big issue facing machine builders is the unrelenting trend toward open (PC-based) controls. Open architectures are not just for HMIs anymore: They are also working their way into motion control, logic sequencing, and embedded systems. Moreover, machine controls are being asked to interface to higher level information technology software (such as ERP and MES), and to permit access via web browsers for remote maintenance.
Such a vast sea change in responsibility and need for specialized knowledge about PC functions is driving machine builders to outsourcing. Beckhoff Automation is an example of a control system outsourcing supplier. This isn't about building specialized or custom products for industrial OEMs. It's about providing hardware or software equivalents that machine builders formerly did themselves.
Ed Schultz, Beckhoff's western sales manager, names some machine builders his firm has helped. CBW Automation is a robot manufacturer and supplier of automation systems for plastic injection molding in Ft. Collins, Colo. Beckhoff developed motion control code and logic, eliminating the need for CBW to buy PLCs, motion control boards, and an HMI interface from different suppliers. Amada America is a sheet metal fabrication equipment manufacturer in Buena Park, Calif. Beckhoff developed a system to acquire data from Amada machines in the field via the Internet. Eaton Leonard is a manufacturer of tube-forming automation in Vista, Calif., for which Beckhoff provided motion control programming support and training.
In all cases, Beckhoff used its own software to accomplish the projects. Therein may lie the rub when asking equipment manufacturers for outsourcing support: you have to use their products. This can be good or bad.
Terry Sladky, senior applications engineer at Amada, found himself caught in the middle of two different outsourcing suppliers. "We wanted to upgrade old machines, such as press brakes, as well as our new machines with web diagnostic and data acquisition capability," explains Sladky. "But all the machine controls came from Japan, and we can't reprogram them. We do research and development here, not final assembly. So we interfaced Beckhoff devices to our existing controls."
Sladky developed a good working relationship with Beckhoff. "I do the design concepts, engineering, and check out the result, while Beckhoff develops the actual interface to the Amada system and writes the programs," he says. "When it all works, we send the system to Japan to be built into new machines, while we do field installations here on older machines."
Technical support
As machine control designers think about next-generation systems, an entire world of high technology is available for the taking. Well, for the licensing, anyway--from places such as NASA and universities. You may very well find an advanced sensor that would be ideal for your latest machine. Let's say that you license a limit switch from NASA that can see around corners, but you run into problems making the technology work. If so, it may be time to find some outsourcing support.
Generics makes its living by understanding advanced sensor technologies, and it helped both Invensys and Brooks Instruments develop new products.
Invensys Metering Systems could not get its absolute encoder register to work in new automatic meter reading system applications. So Generics developed a new, non-contact magnetic inductive approach, designed a new encoder register, and set up a high-production manufacturing operation in Malaysia.
Brooks Instruments, a subsidiary of Emerson Process Management, makes a thermal mass flowmeter, but it needed a software model that could predict the meter's response under various operating conditions. Generics developed the software model and verified that it worked.
In both cases, companies with solid reputations and long experience in their core businesses turned to expert outsourcing to solve highly technical problems.
Send out your networking
Speaking of highly technical problems, adding networking and Internet access to machines is becoming a major headache for many machine builders, and they are turning to outsourcing to find support. "Support starts in the project concept phase, where machine builders need advice on the different design considerations for a network that will operate on the factory floor," says Larry Komarek, product manager of automation systems at Phoenix Contact. "OEMs need help in identifying the key issues involved with fieldbus, remote I/O, and Ethernet systems."
Johanson says Concept Systems is also keeping busy converting existing machines from hardwired systems to modular, networked devices. "We do primarily Ethernet and EtherNet/IP," says Johanson. "Profibus is strong if machines are sold outside the U.S. We do DeviceNet only if it's specified, because it's difficult and we don't see it outside the U.S."
Working with an outsourcing supplier who really knows a particular technology could keep you from going down the wrong path, or it might prove to be the cheapest way to solve a problem. ProSoft Technology, for example, solves difficult interfacing problems for machine builders. "We do a great deal of custom development for customers who can't find an off-the-shelf interface solution," says Danetta Bramhall, application engineer. Products wound up in ProSoft's product catalog that include a Bosch communication module that interfaces between Bosch packaging machinery and A-B Flex I/O.
Outsourcing issues
Outsourcing is often used to supplement the capabilities of a company, but it can cause problems. "One example of this was a manufacturing line where the machines are designed in the U.S., manufactured in Poland, and installed in the U.S.," explains Komarek. "Reliability problems came up with the control system, but the distances involved meant the machine builder could not solve the problems easily." So the machine builder used one outsourcing vendor to solve problems with another outsourcing vendor.
"They switched to Phoenix for reliability, but needed design and startup support to redesign the control system and yet not slip the delivery dates to their customer," says Komarek. "In this case, we went the extra mile and provided programming support for another vendor's PLC."
Sometimes outsourcing can be used as a threat. This can be good or bad. "As our company grows, 'time to market' has become a new, sometimes primary, objective," says Mike Fahrion, director of business development at B&B Electronics Mfg.. "With this increased pressure on my product management group, we've sometimes found that internal departments aren't always able to meet the time-to-market objectives in their first estimate. Since failing to meet our primary objective just won't fly with our product managers, we'll turn to outside contractors to bid various components of a job."
Sounds typical. But, there's more. "An amazing side effect of these outside bids is that our internal departments quickly find a way to increase efficiency or modify processes to meet objectives once they see some outside competition," adds Fahrion. "While we have outsourced a couple of projects, more often our internal resources have responded and found an innovative way to get things done once there is some competitive pressure from outside contractors."
It can backfire on you. "I was very worried about reaction from our internal people," says a system integrator who decided not to use software programming supplied from overseas. "I could not afford to lose our top guys if they thought their jobs were being farmed out. Also, it is much harder to manage outside resources. It takes administrative as well as technical skills, and few engineers can pull it off."
Amada's Sladky says outsourcing isn't that tough to manage. "It's a lot easier to manage than some inside projects," he says. "Beckhoff just sends an engineer to work here for a couple of weeks at a time on each project."
When in Rome
Imberman warns that you may not want to get too dependent on outsourcing, because you can be put at the mercy of wars, dock strikes, and labor problems. "Johnson Controls, for example, was struck by the UAW a few years ago," he recalls. "Within two hours of the UAW going out, Johnson Controls received phone calls from Ford, GM, and Chrysler telling them to settle it."
Presumably, if you don't have the purchasing power of a Ford, GM, or Chrysler, you'll just have make do without parts until your supplier can settle its strike.
If you outsource, Imberman advises that you should keep a just-in-case inventory on hand at all times to carry you through such problems.
Even so, outsourcing may be one way you can stay alive. "With the margins of most businesses, outsourcing may be the only edge they have left," says Johanson. "Aligning with integration companies that bring many highly educated people to the table is essential and the most cost-effective way to do business."
It would appear that outsourcing is a much bigger issue than just finding a shop to build I/O and control boards. Your company's operating philosophy might be put to the test, too.
Outsourcing to India
Why has outsourcing to India become so popular with U.S. companies? "The availability of skilled manpower is a big factor," says Ramesh Pillai, general manager of European operations for Pentafour Software Ltd., based in Chennai, India. "At the last count, in the state of Tamil Nadu in India, there were 110 engineering colleges, each churning out, on average, 300 engineers every year. Also, there are at least two or three CAD/CAE training institutes in every town and city in the state. Extrapolate this to a total of 25 states and union territories, and you have a vast number of available and qualified personnel."
Don't underestimate the competition from India. Pentafour's capabilities are considerable, including design process reengineering, parametric 3-D design, finite element analysis, mold design, flow analysis, bearing technology, rapid prototyping, tooling design, product data management, industrial design, and reverse engineering. Clients of Pentafour include Ford Motor Co., Siemens, GE, Alstom, Ingersoll, Rand, Roush Industries, Visteon, MXS International, and Eaton Corp., among others.
At the moment, control system design appears to be relatively safe. "India rates are low, but we decided not to use them," said one system integrator, who briefly considered using a programming shop in India. He said rates in India were half to one-third less, but labor costs only make up 20% of a project cost, and the overhead and risks were too great.
"In the time it would take us to get the Indians up to speed on our project, we could finish most of the panel design, electrical install drawings, and so on," he believes. "After the design work was done, all that was left was the programming. In our jobs, the lead programmer always starts up the control system in the field. This was obviously a huge problem from logistics, visa, and customer interface points of view."
China: Going Inside the Wall Can Be Risky
Once upon a time, "Made in China" meant a product was made in Taiwan. Today, it means that it was made on the mainland. According to Jim Hennessy, Asia Pacific regional director for ExxonMobil Lubricants & Specialties, China is expanding 10% per year, foreign investment is up 14.9% over last year, and direct foreign investment was $50 billion in 2002. It is expanding its infrastructure by building roads, railroads, seaports, and hydroelectric plants.
Large and small companies from the U.S. are outsourcing manufacturing capabilities to China. Even tiny Yeoman & Co., an agriculture, lawn, and garden tool maker in Monticello, Iowa, has its products built in China. Tom Yeoman, president, says his company has an office and a representative in China to keep track of suppliers. "Just about every company you can think of is either in China or is making arrangements to have some of their products built there," he says. Yeoman himself travels to China three or four times a year.
China already dominates in at least one segment of industrial automation: valves. "I believe you will find China to be the dominant country in manufacture of commodity-type valves," says Don Caffee, senior principal of Valpers Performance Partners, a management consultant to the fluid power industry. "Almost all the major U.S. manufacturers have transferred their commodity valve manufacturing to China. At one point they tried to conceal it, but since Chinese quality has improved this is no longer an issue."
He says specialty valves are still made in the U.S. because the quantity is low and the Chinese don't want the problems associated with that type of production.
"We also know of major valve manufacturers who have transferred their engineering functions to India, and we suspect China will not be far behind India to compete for that business," Caffee says.
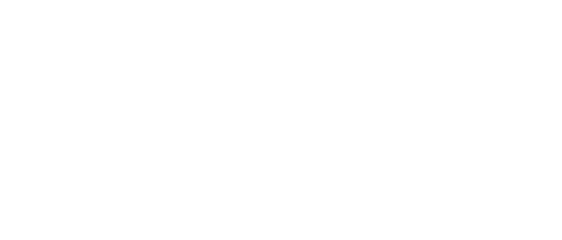
Leaders relevant to this article: