Decentralized, modular systems allow machines to multitask
Eder Matias is an electrical engineer and MBA. He joined SEW-EURODRIVE in 2001, and in his current role serves as national sales manager—drives and motion control. Matias has more than 20 years’ experience in industrial automation focused in drives, servo motors and motion-control solutions.
Rainge Dockter’s passion for motorcycles growing up led him to his mechanical-engineering studies. He subsequently joined SEW-EURODRIVE as an application engineer to assist the company’s vision in “Driving the World” through SEW EURODRIVE’s industrial gearing and automated-guided-vehicle (AGV) product offerings.
Mike DeMeo is a business development manager, drives and automation, for SEW-EURODRIVE’s U.S. headquarters in Lyman, South Carolina. He earned a bachelor of science degree in electrical engineering (BSEE) from Wright State University in 1992 and began his career as an electrical engineer, specializing in industrial machine automation and various programmable logic controllers (PLCs) and industrial-control components.
In 1998, DeMeo joined the SEW team as an application engineer and began to work with machine builders in a wide variety of applications and industries. DeMeo helped customers advance their machine motion-control capabilities by combining mechanical drive products with the expanding SEW electronic controls portfolio. He was able to grow and develop his machine and plant automation knowledge as the SEW electronics product line grew. In 2005, he became a motion product controls engineer where his experience led to the customer-based advanced engineering of mechanical and electronics products used in machine automation. DeMeo’s experience with machine automation spans many industries, including automotive, material handling, food processing, pharmaceutical, plastics and entertainment. In 2016, he became business development manager, drives and automation. His 30 years of experience in real-world industrial automation and his SEW product knowledge base allow him to help customers succeed in their potential automation needs and requirements.
Increasing customer and market demands are changing the layout of factories, resulting in more modules, more flexibility, more automation and fewer rigid structures. The need for machines to multitask over their life cycles requires more automation flexibility. Modular systems including decentralized products allow them to simplify this type of interchange. Whether a manufacturing operation is implementing simple or complex motion-control applications, SEW-EURODRIVE’s MOVI-C modular automation system is designed to provide an end-to-end solution from one manufacturer.
Both single-axis and multi-axis applications can be individually combined depending on requirements: from planning, startup, operation and diagnostics software to electronic control and monitoring devices and on to the mechanical drive itself.
Q: How do modular automation systems lend themselves to decentralized installations?
Thanks to our many years of experience in the field, we have in-depth knowledge of a wide variety of industrial sectors around the world.
• One inverter family for all motors: synchronous and asynchronous AC motors with/without an encoder; asynchronous motors with LSPM technology; synchronous and asynchronous linear motors.
• The application inverters can also be used to operate explosion-proof motors.
• Extremely easy startup using the electronic nameplate or the electronic catalog.
• Simple startup of unknown motors using the calibration function.
As with our other modular systems, everything in our new MOVI-C modular automation system fits seamlessly together: The engineering software matches the controller and inverter technology, which in turn both fit with the drive technology. Decentralized takes this modular concept to a new level allowing even more combinations to create the perfect flexible automation system.
Upgrading additional components such as motor cables without any differences in terms of project planning, handling or performance, an essential part of the new modular platform is the digital motor integration. This supports automatic drivetrain startup and also ensures that various sensor signals can be transmitted from the motor to the electronics without requiring any additional installation work.
The decentralized modular automation platform lends itself to just-in-time automotive production; the precise control and finely stepped torques needed to ensure accurate positioning and gentle handling of transported materials; and beverage companies’ needs to adjust their systems to new processes, batches and production programs based on changing seasons and markets.
The MOVI-C modular automation system gives customers the option to implement their applications both with inverters in a control cabinet and with drive electronics that are either located close to the motor or integrated into it.
Q: How does a decentralized portfolio of motion components lend itself to more flexible motion configurations?
Mike DeMeo: For economical decentralized installations SEW-EURODRIVE offers components such as MOVIMOT Advance, MOVIMOT Performance and MOVIGEAR for power, quality and sturdy design combined in one standard product and controller. SEW-EURODRIVE decentralized controllers allow for multiple type motors including synchronous and asynchronous AC motors with/without an encoder. Match these gearmotors with integrated frequency inverter or a field distributor for installation close to the motor: our decentralized drive solutions provide you with flexibility in terms of your application, while saving energy and reducing costs.
One of the challenges is to reduce the complexity and startup times of installations. A single supplier “shaft to plug” design concept allows this. Additional higher-level functions and applications embedded in the decentralized controllers offer all the necessary functions such as positioning control with simple parameterization MOVIKIT modules. Torque and load speed monitoring increases protection before failure of critical plant machines. This condition monitoring assists in increasing plant operations by reducing mechanical failures. Additional technology such as MOVITRANS inductive contactless power transfer system can be integrated with modular technology creating even more automation motion capabilities. Also, flexible motion systems should have a wide range of product power requirements, requiring a portfolio consisting of products from 40 W power rollers to 10 hp AC induction motors, all with decentralized components.
Decentralized drive technology couldn't be more intelligent, lean, efficient and cost-effective than this. The MOVIGEAR performance drive unit combines servo motor, gear unit and inverter in a single housing. What's more, the decentralized inverter from the MOVI-C modular automation system means the drive unit can be used in all standard Ethernet-based infrastructures. The SEW-EURODRIVE decentralized products allow for IE4/IE5 type motor systems. With MOVIGEAR, you can achieve energy savings of up to 50% for your system. This is made possible by the seamless interplay between the IE4 efficiency class motor, efficient gear unit and integrated electronics.
Based on the MOVI-C modular automation system, MOVIGEAR performance complements existing products in terms of functionality and consistency and extends the range of possible applications for our decentralized drive technology, which has been proving its worth for decades.
The MOVIGEAR performance drive unit consists of a decentralized inverter, a permanent-field synchronous motor and a gear unit. These three core components are located in a single compact aluminum die-cast housing.
Thanks to its integrated digital interface, no additional installation is required for transfer of the electronic nameplate and various sensor signals between motor and inverter. Communication takes place via fieldbus interfaces and also via integrated, digital inputs and outputs.
Q: As more equipment looks to decrease its footprint while increasing its energy efficiency, what role does the motor-inverter combination play, and how scalable is that?
SEW-EURODRIVE offers optimized drive systems from a single source, which includes high-efficiency gearbox, motor and integrated frequency drives capable of achieving the highest system efficiency class IES2.
Our motor-mounted frequency inverters MOVIMOT Advanced and MOVIGEAR Performance are delivered with a precise motor-inverter combination, high overload capability and no motor tuning required, making them simple and unique drive solutions. MOVIMOT Advanced in particular covers applications from 0.5 hp up to 10 hp, has remote I/O capability and communicates with Ethernet/IP, Profinet, EtherCAT and Powerlink. Besides that, the optional safety options such as CIP Safety, FSoE and ProfiSAFE make MOVIMOT Advanced an ideal solution for customers looking for scalability and flexibility with the highest system-class efficiency.
Q: What do you recommend for connection of the motion-control system to higher-level systems in terms of cabling and communications protocols?
Eder Matias: Each OEM, plant manager or system integrator will have its own preferences when it comes to cabling and communication protocols. Taking all passions aside, it feels like EtherCAT-based communication protocols are becoming predominant when sophisticated motion control is required. EtherNet/IP and Profinet protocols seem to be the preference for systems with a high number of nodes or when shorter cycle times aren’t required.
SEW-EURODRIVE frequency inverters are communication-agnostic and can talk to most modern communication protocols. Customers can decide what is the best protocol without changing the drive-system supplier.
With labor and material shortages, connectivity needs to be considered, too. Panel-mounted drives and motion controllers such as the MOVIDRIVE Modular and MOVI-C Controller use the common industrial RJ45-style connector, which is abundantly available.
MOVIMOT Flexible decentralized solution from SEW-EURODRIVE can combine 460 V power, 24 V and communication all in a single pre-assembled cable (PAC). This mitigates all the connectivity mistakes in the field and reduces the cabling planning to a minimum.
Q: Automated guided vehicles (AGVs) have become integral to warehousing and factory operations. What are some of the most recent innovations that are differentiating AGVs from previous generations?
On the hardware side, this takes the form of offering bundled system functions. For example, the drivetrain, navigation, inductive charging, energy storage and safety concepts are all being developed into modular, bundled solutions that can be reused between a wide variety of vehicles.
On the software side, the vehicles are communicating via non-proprietary solutions. The AGVs communicate using message queuing telemetry transport (MQTT), according to the VDA 5050 standard. This allows huge flexibility for end users and integrators to work with the AGVs and seamlessly integrate the vehicles with other plant assets. This also means that while the SEW Maxolution team has a fleet-management solution available for users who need it, the vehicles are capable of integrating with third-party fleet-management solutions that communicate to these standards.
Q: Can you talk more about Maxolution and how bundled functions figure into the flexibility needed in material-handling operations?
Rainge Dockter: As industry increasingly transitions to more mobile systems, it is no surprise that SEW-EURODRIVE’s Maxolution division is taking the same modular approach to the market for the AGV offerings. Since many of the vital functions an AGV needs to perform, such as navigation, the drive system, energy storage and communication, are similar, it simply makes sense to turn these into predefined, modular solutions. This enables SEW’s Maxolution engineers to reuse these modular solutions between a variety of vehicles.
For example, during the planning phase of a project, the bundles offer streamlined solutions to many of the common material-handling operations. The engineers can then focus on the application-specific challenges, such as the interface points between the vehicles and the automation or people working with them. The end result is a customized, yet expedited planning process that does not compromise quality for the material-handling operations.
After the vehicles are commissioned, the bundles help support the longevity of the product by simplifying the spare-parts requirements and simplifying the repair process, should it be necessary.
For more information, visit www.seweurodrive.com.
Sponsored Recommendations
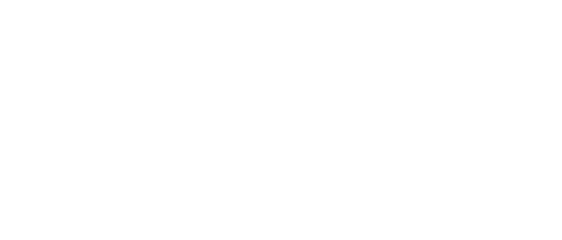
Leaders relevant to this article: