Chris Knorr, vice president, business development, North America, at Eclipse Automation, which is part of Accenture, will present “Automated Manufacturing Scale Up: Planning for Success " during A3's Automate Show in Chicago's McCormick Place on May 7 at 10:15 am. For more than 30 years, Knorr has helped companies in the transportation, life-science and consumer-product industries to develop strategy and optimize manufacturing operations through automation. Contact him at [email protected].
Many manufacturers launching new products are challenged with how to scale their manufacturing operations, with capital equipment, data infrastructure and staffing being major considerations. Adding to the challenge are often new processes which haven’t been automated before. Greenfield and brownfield facility planning add risks that need to be considered well in advance of start of production. The old saying “failing to plan is planning to fail’ holds very true as it relates to launching new products and ramping up production. Several considerations must be made when creating a manufacturing scale-up plan.
Although early product launch forecasts can often be uncertain, when possible, a phased manufacturing ramp-up can provide several benefits.
In particular with new automation processes, by getting one line through integration rather than multiple simultaneously, the staggered timing can allow time for learnings to be realized and solutions implemented prior to replication. Typically, issues seen when a system has only seen moderate run time will be amplified when running 24/7 or at higher rates.
Another benefit of having multiple lower-throughput machines vs. one higher-throughput machine for the initial automation launch is the benefit of redundancy. By having multiple systems, you have a redundant path in case of unplanned downtime.
An early risk-mitigation activity that can happen while still at the very early pilot level is the proof of principle of new and challenging processes. By doing this early testing you are able to address these risks in a low-cost way, saving potentially significant cost, schedule or quality issues requiring rework later in the project.
There are some key considerations when developing the automation concept.
A key element is choosing the right level of automation relative to needs. Most often, manufacturers are looking to automate a process to save labor costs. By looking at the number and burdened cost of operators, factories can save per shift vs. the cost of the capital over time during the payback period.
Another consideration for automation can be quality. If there are processes that cannot be done consistently by an operator, causing cost scrap and rework, a payback case can be made.
Operator safety is another potential reason for automation. Where there are particularly dangerous tasks that have caused costly lost-time accidents, automation of these processes can often be a solution.
When developing an automation concept, one of the first things we look at is balancing cycle time relative to overall target throughput. By first breaking down the manufacturing steps, grouping them to be within the required overall cycle time, factories and plants are able to determine how many automated cells are needed. For operations that take longer than the target cycle, having multiple cells or processing multiple parts simultaneously can help to achieve target.
It’s important to consider overall equipment efficiency (OEE) in the design to ensure a system is capable of meeting production needs.
The element of availability can be addressed by ensuring the process is reliable. This might mean selecting a certain process over another based on required service intervals.
Automating and simplifying part change over time can be another method to optimize availability.
Machine performance can be enhanced by ensuring proper balancing of operation cycle times to realize a more optimized process flow.
Quality is the third element and can be addressed by doing upfront testing on processes to optimize first-pass yield.
When trying to estimate OEE, consider the number of processes and the challenge level of the processes; and, remember, the effects per station are cumulative.
When in the conceptual and design phases, the use of simulation and digital-twin technologies can also provide some real-world benefits and picking the right simulation tool for needs is the first step.
For simply ensuring accurate prediction of robotic processes a simple robot simulation is often all that’s needed. Similarly, understanding overall line throughput, potential bottlenecks and optimal buffer placement can often be done with relatively simple line simulation software tools.
On the higher end of the technology spectrum, there is an increasing trend toward realizing the benefits of full kinematic digital twins. Although there is increased cost with these technologies, some of the benefits that can be realized come in the form of reduced integration time, which can compress an overall project schedule, reduced physical rework and the ability to test future cause-and-effect scenarios for retrofits.
Increasingly as manufacturers seek to save labor cost and address labor shortages and improve product traceability, autonomous operation is another key consideration.
Similar to examining payback for automation of the manufacturing process, calculations need to be made around the cost and availability of labor vs. the capital cost of adding automated material handling in and out of the line.
Phase implementation is often recommended to ensure there is adequate time to focus on the automated assembly process first, but at the same time, planning in advance can save future costs.
Consider physical routings that allow adequate space for automated guided vehicles (AGVs) or autonomous mobile robots (AMRs) in addition to any other foot or material-handling traffic when laying out a manufacturing space.
It’s also important to examine the types of parts that will need to be handled and the incoming format compatibility with automated material handling. While utilizing trays or other formats that allow easy material transfer can facilitate automation, they come at their own cost of handling and maintenance.
Planning around the other infrastructure for AGVs and AMRS can also save cost in the long run. Consider the transfer of parts from the AGV or AMR to the automation in advance by implementing docking features; this can save future cost of retrofit. Similarly, plan for incoming parts scanning to allow for traceability.
Placement of charging docks and planning for maintenance and spare vehicles can also ensure meeting required uptime.
A very important and sometimes overlooked element of automated manufacturing planning is the planning of data architectures. Traceability of product is an increasingly important consideration as manufacturers seek to provide further product security, reduce the severity and scope of product recalls and provide further customer transparency around product sourcing.
The other important benefit that can be realized through implementing data collection can be in gaining detailed understanding of machine performance. By implementing machine-performance data collection and reporting early in the integration and production phases, more valuable insights can be gained allowing faster correction of issues.
While the implementation of product traceability and machine performance is nothing new, there is an increasing trend toward more seamless integration of data across the entire data stack, often referred to as the convergence of information technology (IT) and operational technology (OT). By having more seamlessly integrated bidirectional data, many benefits, such as real-time visibility of manufacturing output, work in progress, quality checks and inventory levels, can be realized. This can also allow reduction in quarantine time, getting product to market faster.
Early consideration of the requirements to have a successful transfer of equipment from manufacturing engineering to operations is also key to a successful manufacturing ramp-up.
Considering standardization of programmable devices such as robots, programmable logic controllers (PLCs) and human-machine interfaces (HMIs) and implementing programming standards can reduce training needs for a manufacturer’s maintenance staff. Similarly, by reducing the number of similar products from different vendors, a plant or factory can reduce the need for stocking of spare parts.
In a world of supply-chain volatility, it is also important to consider ordering spare parts well in advance of site acceptance testing to ensure parts are available in case of a breakdown from the first day of operation. There can also be cost benefits for the early order of spare machined parts, as, in some cases, ordering multiples at one time can save additional setup costs.
Early training of maintenance in advance of machine commissioning is also beneficial to ensure a smooth transition.
Planning for remote-support options with an automation partner can also prove beneficial in reducing unplanned downtime. Technologies such as augmented reality (AR) can help to facilitate improved visualization of issues, sharing of information in real time and ultimately reduced downtime.
There a many moving parts and considerations when planning an automated manufacturing ramp-up, but, by creating a well-thought-out plan, mitigating risks early and choosing the right partners for success, manufacturers can optimize capital expenditures (CapEx) and deliver on production requirements.
Sponsored Recommendations
Latest from Financials
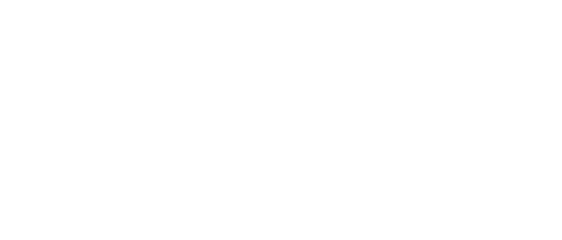
Leaders relevant to this article: