By Joe Feeley, Editor in Chief
Packaging solutions in almost every market segment are comprised of several pieces of equipment. Sometimes the individual machines are installed at different stages of the company's growth by one machine builder. Sometimes the customer buys from more than one builder. This could be the result of price or a customer's historical preferences for one brand of case erector while using another brand of packer or case sealer.
Whatever the reason, the wise machine builder recognizes these possibilities and naturally aims to supply as many of the machines as possible, preferably all of them. One way to do this is to make the required integration of these machines easier to do when needed, or to offer an already integrated solution up front.
That's the approach taken by Elliott Manufacturing (www.elliott-mfg.com) in Fresno, Calif. The company incorporated its case packing machinery, case erector and sealer expertise into its new Case Packing System. The modularity of the design allows packagers to run a pick-and-place module today and switch it out for a drop-pack module tomorrow, or even to break the line apart and redeploy the erector and possibly the top sealer to another location in the factory. Customers can purchase the complete line or, to build their systems a piece at a time, in a building-block concept (Figure 1).
The case-packing module can range from an economical drop-load system to a mid-range gantry pick and place or the more sophisticated robotic pick-and-place option that also could palletize the output of the case-packing system.
Constant Progress
Elliott Manufacturing was incorporated in September 1929, and has been operating continuously for 81 years. Thomas Henry Elliott owned and operated Selma Fruit, processing raisins. "He was an entrepreneur, inventor and self-taught engineer of sorts, and liked machinery more than the processing business," says Richard Allbritton, the company's president and CEO. "Raisins were packed in bulk corrugated boxes, sealed using a paint brush and cold glue, and then placed under a weight for compression until the glue set up. Elliott felt there must be a better way and designed a case sealer to do that job. He abandoned the raisin processing business and started Elliott Manufacturing, making the Type ‘A' case sealer. As his business grew, he looked for opportunities to expand his machinery manufacturing business and expanded into making food processing equipment."
Over the years, the company matured into a readily recognizable company, and Elliott wanted complete control of his products. He started the third leg of Elliott Manufacturing, a fabrication shop for custom machine work. "He realized that by making his own parts, the company could maintain control of the quality of the machinery manufactured," Allbritton explains.
Necessity and Reinvention
In 2007, Elliott Manufacturing embarked on the process of reinventing itself in the redevelopment of its present line of packaging machinery. "In the past we delivered a case-packing solution in a couple of different ways," Allbritton explains. "We can provide individual machines. A case erector forms the case. Next, feed the case into a packer that loads the case. The case finally ends up in a top sealer that seals the top of the loaded case. This solution involves a lot of conveyor work, floor space, and sometimes complicated handshaking between the machines."
"Part of the logic behind this approach is to allow the end user to either install a full system with one controls package or install the machines in stages as the company or product line grows."
Allbritton says the new Modular Case Packing Systems take these two solutions and apply the benefits of both while removing the downfalls. The systems take the three machines from the first solution and connect them together, giving users a form of the second solution. "It gives the end user a system without extra conveyor work to move product and cases around, an integrated controls system that allows all of the machines to communicate with each other, and the flexibility of changing product handling and loading simply by using different modules that can be integrated into the system easily."
Rethink the I/O
The current Case Packing System uses a Rockwell Automation controls platform with PLC, touchscreen, and servo drives and motors. The system meets Category 3 safety standards using safety switches, safety relays and safety functions integrated in the servo drives. This integrated controls platform allows Elliott to integrate its controls more easily and share information between them.
"In previous systems, a major encumbrance was the use of digital I/O that required us to wire each field component individually back into the main control cabinet," Allbritton says. "We decided to switch to remote I/O for field components such as photo eyes, proximity switches and other inputs. This allowed us to save valuable time by reducing wiring. The remote I/O gives us added flexibility because we can add new I/O without the worry of running out of digital inputs or adding new I/O cards to the PLC. That requires precious cabinet space and additional wiring."
Modular Automation
Elliott engineers selected a B&R Industrial Automation solution that provides remote I/O systems for the modules, so the cabling doesn't change whether the company uses a B&R control system or one from another automation supplier. The machine modules are wired the same whether they're used standalone or integrated as a case-packing system. Each removable, quick-connect case-packing head is therefore self-contained with plug-in communications and 24 Vdc power connections.
[pullquote]"B&R's Ethernet Remote I/O system was a great fit," Allbritton states. "It lets us standardize on one I/O system and integrate it into any of the controls systems that we might want or have to use. We do everything we can to meet our customers' specifications, and sometimes that means using a specific controls package. In this case, we were able to hook up and configure the B&R I/O in just a few minutes without writing any PLC code to tie the two together. The I/O also gives us the flexibility to add or reconfigure the I/O to accept a new module without adding new hardware to the control cabinet and reconfiguring the PLC's digital I/O structure."
Sold Separately Too
Each of the modules is one of Elliott's standard standalone machines. Each can be controlled by its own PLC and HMI, or use a common controls system. "Part of the logic behind this approach is to allow the end user to either install a full system with one controls package or install the machines in stages as the company or product line grows," Allbritton says. "If the machines are installed in stages, they all could have their own controls system or be integrated into one system as the pieces are added."
The Next Next Generation
Allbritton says the company is at work to add the cartoning side of its equipment line to the same modular principles that it used to develop the new case-packing lines. "When finished, we will have a complete system that could take a product from individual product, to carton, to case packing, and finally to a palette all in one integrated system," Allbritton explains.
The case erector section, based on the Elliott EV 350, can handle cases at up to 42 cpm with continuous control of the case. Size changeover requires less than 5 minutes with automatic changeover available. "Servo technology is incorporated into the control system, giving the end user fast and repeatable size changes every time," says Elliott Manufacturing President and CEO Richard Allbritton. "This feature minimizes line and production downtime for size changeover. A broad case-size range and small footprint combine with an open design for ease of access and scheduled maintenance. The magazine is ergonomically designed for operators and handles a wide range of corrugated quality. It is easily convertible to automatic loading of knocked-down cases. The use of new materials makes the frame of the EV 350 light, durable and very portable."
The TL 350 gantry pick-and-place module handles a wide variety of products at case speeds up to 65 cpm, depending on product and pack patterns. "The servo lane divider makes product transfers from a single lane to multiple lanes smooth and trouble-free," Allbritton says. "The product size, shape and material being conveyed make every case-packing project unique, and could require special product handling. The programmed product infeed conveying system allows Elliott to speed up/slow down different sections of the infeed conveyor to minimize product-to-product interaction and to control back pressure to the product load station."
Pick head size and product lane changes are simple and easily made in less than 5 minutes by the operator, Allbritton says. The application might call for single pick heads, or quad pick heads with vacuum pick gripper picks, or a special-design pick head for a unique product. The weight of the product might dictate the number of heads or the actual case-packing speeds achievable.
The Elliott SV 350 top sealer feeds filled cases into the sealer for the trailing minor flap tucker as the leading minor flap is plowed down, hot melt adhesive is applied to the minor flaps as plows close the major flaps and move the filled and closed case into the compression step.
Latest from Vertical Industries
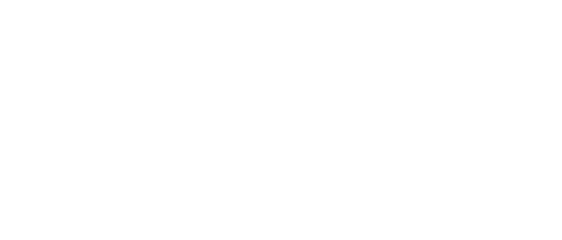
Leaders relevant to this article: