At Braun Sondermaschinen, we recognized automation, Industry 4.0 and big data as trends early on and utilize them for developing fully automated production lines, especially in the automotive and electromobility sectors, in order to increase productivity for customers and to achieve potential savings (Figure 1).
Building specialized machinery requires individual concepts and flexible solutions. This is why we have developed, for example, the modular automation concept (MAK), a set that includes both software and hardware. Smart components are also used to make the processes within the systems even safer and more efficient. These components also include AG24 positioning drives from Siko, a manufacturer of sensors and positioning systems. They enable an automated size changeover for more precise adjustments when changing products and faster refitting times, as well.
Also read: Digital twin aids in virtual commissioning
The automated production lines that we implement are developed according to specific and individual customer requirements, usually as a prototype and then as an adapted replica of the prototype. No two systems are alike; there are always special requirements. To ensure a certain level of standardization remains, we offer a modular automation concept: The MAK system consists of an aluminum traverse and a protective housing. Depending on customer requirements, the individual processes are modularly linked in, and a software package is fitted over the entire system. Even after years, processes in this design can be replaced and modified, without having to redesign the entire line from scratch.
Automated size changes using the positioning drive
Another aspect that is taken into account in system planning is the increased number of variants that machines must be able to handle even with the smallest batch sizes. Compact positioning drives enable automated and fast size changeovers without major intervention in PLC programs. Braun Sondermaschinen always uses the AG24 positioning drives when manual workstations requiring automation need precise size changes. Examples of this are balancing systems—assembly and balancing machines—for the production of cooling fans for the automotive supplier industry. Up to now, balancing has been a manual process in which the special machine manufacturer had already used Siko’s mechanical position indicators for manual size changeover. With the AG24 positioning drive, this module can quickly and precisely be converted to manage the increasing number of model variants. Existing manual workstations can also be retrofitted with a drive, thanks to easy assembly via the hollow shaft.
High power reserve for demanding applications
The AG24 actuator was selected partially for its high torque and the associated power reserves. This power range is not always necessary for systems, but the reserve option plays a major role—for example, if components become more difficult to move due to dirt and stress—and the drive can then provide more power. Maintenance intervals can also be extended if the drive is not constantly running at the load limit.
Servo motors are an alternative to positioning drives and are justified in most processes, but less so when compactness and manual operations are important. With the AG24, all essential functions, such as the brushless dc motor, position encoder or power and control electronics are already integrated into the device. It can be connected directly to the machine control and is compact; unlike a servo motor, which requires additional components such as variable-frequency drives or inverters, it does not require any wiring. The positioning drive also has an integrated absolute encoder that records the position at all times, even when the power is off, and does not require any referencing.
This also demonstrates the advantages for a special machine manufacturer like Braun. “Every project is accompanied by a new set of specifications, with additional possible variants, which in turn involve special requirements,” says Jürgen Schuh, business unit manager of changeover solutions at Siko. “With the AG24, Braun Sondermaschinen has a device up its sleeve that, thanks to the functional reserve, can serve a wide range of applications for size changeover and can thus be a standard tool."
The drive also includes an additional safety function, thanks to the optional spring brake. Even when the power is off, the brake keeps the axis in its specified position—a function that is interesting, for example, for vertically positioned spindles of a certain weight. In the event of a power failure, the weight could press downward, but the drive would no longer be able to counteract it without a power supply. In this case, the braking force is activated and the brake automatically closes when it is switched off, thus holding the spindle in place.
Manual settings made directly on the device
The ability to not only control the drive via the fieldbus and the PLC, but also being able to use the option for changing manual settings directly on the device display via control buttons is also very valuable. In some applications, it makes the most sense to change the settings and positioning manually in advance via teach-in—in other words to gradually travel to the appropriate dimension with the positioning drive and then save these positions as target values in the machine control system. In this way, the finely adjusted positions can be traveled to directly during commissioning. The AG24 positioning drive combines both aspects—the manual fine adjustment and the automated, efficient process.
From an electrical design standpoint, the integration of the actuator is also very straightforward, including integration into the machine control system. While we usually use EtherNet or EtherCAT, Siko also has numerous other interface standards in the real-time Ethernet area, as well as the corresponding software tools.
Predictive maintenance, thanks to diagnostic data
Another aspect that will become more important for his customers in the future is the collection and evaluation of data on the production lines, which is supported by the smart functionality of the AG24 positioning drive. Besides determining the position, the drive can also show additional diagnostic data, such as current consumption or temperature, both on the display and via the interface. Conclusions can be drawn from this data in terms of predictive maintenance, allowing maintenance intervals to be planned in advance. The drive thus also supports requirements related to Industry 4.0 and data evaluation via artificial intelligence (AI).
Full automation is becoming the standard
There’s great future potential in the diagnostic capability because the ideal automation line is a system in a dark hall, in which production can run 24 hours, seven days a week, 365 days a year without human intervention. This vision is not far away; human judgment is still mandatory for certain processes, but the greater the number of unnecessary, tedious or error-prone process steps that can be automated, the more efficiently production can be carried out.
One thing is clear: Not only is full automation increasing steadily, it is becoming the standard in industrial production. Intelligent peripheral components such as positioning drives play an increasingly important role.
Manuel S. Gander, M. Sc., is head of supply chain management and material management at Braun Sondermaschinen in Germany. Contact him at [email protected].
Sponsored Recommendations
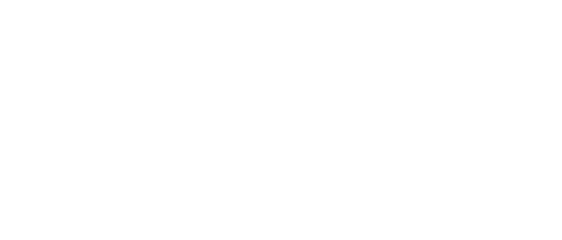
Leaders relevant to this article: