A Control Design reader writes: What are the minimum standard features and any regulations for a variable frequency drive (VFD) that needs tight speed and torque control? And what is the best fieldbus protocol for applications using motor control—speed and torque dynamically—via variable frequency drive (VFD)?
ANSWERS
From low speed to high performance
For tight speed and torque control on a VFD, there are several options, with each having different strengths depending on the type of speed and torque control needed for the end-use application.
- For low-speed, high starting torque applications, we recommend drives that employ Sensorless Flux Vector Control (SVC). SVC uses a high-speed DSP microcontroller to maintain a mathematical model of the rotating magnetic flux within an induction motor and thus can determine the motor’s speed and position. From this, it can calculate the optimal timing of the voltage pulses to deliver to the stator windings in order to maintain the proper speed and torque. SVC can provide optimum speed and torque control, but it cannot deliver full torque at near zero speed. If the application calls for this (i.e., extruding and metering), then closed-loop control, with an encoder to give positive motor speed and position feedback, is required.
- For high-performance applications, like elevators, cranes and hoists, which require holding a load and not moving, drives that employ Closed Loop Vector (CLV) are a reliable option. CLV uses a vector algorithm to determine output voltage and the critical difference for this option is that it incorporates an encoder. Encoder feedback paired with the vector control method allows for 200% motor starting torque at 0 rpm. This feature is a selling point for applications.
- When simplicity is the priority, we suggest drives that employ Volts-per Hertz, commonly called V/f. This method is often preferred due to its plug-n-play simplicity that requires very little motor data is needed by the drive. Tuning the VFD to the connected motor is not needed (but still recommended), and no motor encoder is required.
As usual with engineering, it’s not so much that there is a single best protocol for every situation, but rather several options depending on the application:
- Modbus Remote Terminal Unit (RTU) protocol is a good choice if simplicity is desired. It is straightforward to support and as a result, is one of the most widely used for industrial automation applications.
- EtherCat, a less common option, is an excellent fieldbus if the VFD is being controlled from a remote PLC. It is inherently self-healing and uses standard RJ-45 to create a network, so no switch is required. Ethercat runs at Layer 2 (Data Link) on top of bare Ethernet frames, with payload substitution happening at each device. Thus, there is no network layer overhead, which allows for maximum raw speed; on the other hand, it is not routable – the devices must be on the same physical Ethernet. It can attain cycle times of 100 microseconds.
- Profinet Isochronous Real-Time (IRT) is also a solid choice for a fieldbus. It is a superset of Profinet that uses PTP (Precision Time Protocol – IEEE 1588) to maintain device synchronization. It can attain cycle times of 250 microseconds. Both Ethercat and Profinet allow standard Ethernet frames to be delivered during the slack time between real-time frames.
ALLEN BENNETT AND JOHN CLEMENT / field application engineers / Allied Electronics & Automation
Figure 2: Vector control is the bare minimum method used to tightly control speed and torque. (Source: ABB)
Scalar, vector and direct torque control
Great question, and for us to answer it, we need to discuss the various methods for variable frequency drives control of ac induction motors. There are three methods in the industry:
- Scalar Control (also referred to as V/Hz or V/f): varies both the voltage and frequency of power supplied to the motor in order to maintain a fixed ratio between the two. With this technique, sometimes known as scalar control, field orientation of the motor is not used. Instead, frequency and voltage are the main control variables and are applied to the stator windings. The status of the rotor is ignored, meaning that no speed or position signal is fed back. Therefore, torque cannot be controlled with any degree of accuracy. Furthermore, the technique uses a modulator, which basically slows down communication between the incoming voltage and frequency signals and the need for the motor to respond to this changing signal.
- Vector Control (also referred to as field oriented control, or FOC): controls the magnetizing and the torque-producing components of the stator current independently to control both motor speed and torque. To achieve a high level of torque response and speed accuracy, a feedback device is required (an encoder for example). This can be costly and adds complexity to the traditional simple ac induction motor. Also, a modulator is used, which slows down communication between the incoming voltage and frequency signals and the need for the motor to respond to this changing signal. Although the motor is mechanically simple, the drive is electrically complex.
- Direct Torque Control (DTC) technology was developed by ABB. Field orientation is achieved without feedback using advanced motor theory to calculate the motor torque directly and without using modulation. The controlling variables are motor magnetizing flux and motor torque. With DTC there is no modulator and no requirement for a tachometer or position encoder to feed back the speed or position of the motor shaft. DTC uses the fastest digital signal processing hardware available and a more advanced mathematical understanding of how a motor works. The result is a drive with a torque response that is typically 10 times faster than any ac or dc drive. The dynamic speed accuracy of DTC drives will be eight times better than any open-loop ac drives and comparable to a dc drive that is using feedback. DTC produces the first “universal” drive with the capability to perform like either an ac or dc drive.
So, to answer the question, vector control is the bare minimum method used to tightly control speed and torque. The main drawback of VC is the need for a feedback device such as an encoder. This adds complexity and costs to the control system. DTC is recommended over VC due to its accuracy, simplicity, and lower total cost of ownership.
On the fieldbus question, it is irrelevant to tightly controlling speed or torque since the motor control algorithms are embedded in the control module of the VFD. The VFD is controlling the motor directly without any fieldbus interaction. With that said the most common industrial fieldbuses are Modbus/TCP, Ethernet/IP, ProfiNET, EtherCAT and Ethernet Powerlink.
RALPH CONTRERAS / OEM business development manager, food and beverage segment / ABB Motion Division - Drives Products
Easier selection and set up
Easy selector tools and apps are available to help select the proper drive for your application.
Standard drive control (SDC) is ideal for pumps, fans, compressors, mixers, kneaders, agitators or horizontal conveyors of all types.
Dynamic drive control (DDC) is ideal for vertical conveying, gantry cranes, lift tables, escalators, elevators or closed loop extruder control, just to name a few.
Using dynamic drive control could include braking resistors. Feedback for close loop control can be from SSI encoders, incremental and/or absolute position measuring systems. This will allow precise control.
Easy to use graphical parameterizing software is available to setup base parameters and fine tune the VFD to your application. VFDs are being used more these days, and the price for the drives are to the point where it makes sense to use them for both energy efficiency and control benefits. Commissioning, monitoring and controlling VFDs can be simplified utilizing common industrial communication protocols like Profibus and Profinet.
WERNER LAMBERGER / technical support engineer / Automation24
VFDs vs. servo drives
Users can achieve different levels of velocity control with the various solutions available from automation suppliers. The differentiation between servo drives and VFDs has shrunk significantly. Historically, servos were preferentially used for applications requiring positioning and dynamic operation, where tight control of speed and torque were essential (closed-loop operation). VFDs were more cost effective in applications with generous operating windows for speed (and often operated in open loop). Today’s servos and VFDs offer open-loop (V/Hz) and sensorless vector control functionality. The addition of a feedback card for closed-loop operation will achieve the highest speed regulation and accuracy. Torque control requires a closed-loop system.
With regard to functional safety, variable frequency drives typically offer only safe torque off (STO) and motor free-wheeling must be taken into consideration.
Servo drives use motor encoders for velocity and position feedback and therefore can offer STO and many other safe motion functions.
In industrial manufacturing today, Ethernet-based communication protocols are the most prevalent. Fieldbus protocols such as EtherNet/IP, Modbus TCP, ROFINET are typically used with VFDs. Increasingly, VFD devices also offer real-time synchronous protocols, such as Sercos automation bus and EtherCAT to operate on the same network as the servo drives and IOs. These protocols support multiple control modes. A few vendors offer an interface card capable of multiple potocols. This will be an advantage for machine builders who integrate different control platforms based on end customer preference.
MIKE MUELLER / product support manager / Bosch Rexroth
How fast does the VFD need to respond?
Minimum standards and features for VFDs are often hard to differentiate, as different products not only have different performance ratings, they also use different terms and slogans. To further muddy the waters, applications require different performance levels.
These can be defined as the goals of the entire system or may be defined by a specific industry standard or customer specification.
Ultimately, it boils down to the entire application and how the VFD fits within the system. Utilizing VFD application specialists, reference stories and other experiences can help someone define their required performance levels. Questions such as feedback device requirements (encoders or resolvers) and understanding system response times can help to identify how well the VFD can perform in certain situations. Looking into speed and torque accuracy values, with or without feedback devices, will allow you to compare products and their performance. As in most things, the higher the performance level, the more investment that will be required. You may even discover newer technologies that can meet your performance requirements and not require a feedback device, which will ultimately lead to savings.
Fieldbus protocols and performance will also vary from product to product. The protocols are individually defined; however, some will have different communication rates as well as different VFDs have different capabilities in how fast they can process the information and deliver results. Further, one must also consider the controller they are using and its preferred network. Depending on your application needs you may or may not require fast fieldbus communication.
Another impact to the fieldbus discussion is how will it integrate into existing infrastructure and what knowledge base may already exist to make the transition easier. Often in industry, Ethernet is used as it pairs well with existing IT infrastructure and resources. However, in building automation (such as HVAC) BACnet is typically preferred as it is understood by most technicians in the field.
For both fieldbus and VFD selection, it is important to determine how fast you need to respond before beginning the selection process. From there you can examine how fast controllers can process, the length of time the information takes to travel over the network and then how long from when the signal is received at the VFD to when it generates a response to know whether it meets system needs. This will prevent one from not getting what they require, or possibly overpaying for something they do not need. Further, keep in mind as technology advances, VFDs are becoming more intelligent controllers, often eliminating the need for smaller PLCs, or allowing users to program fast sequences in the VFD that outpace some external controllers.
Overall, to state a minimum standard is extremely difficult. Rather, it may be better to ask what the application really requires, and who can partner with you to find a proper and affordable solution. Often, the best performance can be found in the right partner who will walk alongside you through installation, startup and the entire lifecycle of your VFD.
JONATHAN MOSTERD / manager/ Danfoss Drives, Center of Excellence, NAM
Basic, advanced and closed-loop
VFDs are typically grouped into three performance categories: basic, advanced and closed-loop. Basic VFDs are meant for simple variable speed applications, do not provide speed control at 0 rpm nor do they provide any torque control. Advanced drives (often called open-loop vector drives) provide improved speed control, near 0 rpm control and some torque control (mostly used to guard against over-torqueing the mechanics). Closed-loop drives (vector drives) require a shaft feedback device and provide full speed and torque control over the whole range of operation. For non-lifting/hoist applications, there is a sensorless closed-loop (SCL) technology that uses advanced technologies to replace the shaft feedback with a software model. SCL has been shown to provide as good as closed-loop speed and torque performance. The limitation is at 0 rpm – depending on the motor (servo or induction) you may only have between 50% and 100% of rated torque available. Most applications can benefit from this latest technology.
Fieldbus technologies have thankfully narrowed to a few popular platforms. Most have moved to TCP/IP hardware platforms (one exception being CAN over serial wires, which is still used extensively). One platform that has gained high adoption from many different control manufacturers is EtherCAT. EtherCAT was designed from the ground up to support synchronized communications for coordinated motion, yet have simplified node-to-node or star wiring without the need for managed switches or protocol “upgrades” common with non-deterministic fieldbus solutions. It is also very fast: low end controllers typically run at 4 to 8 ms communication update rates, while high end controllers run under 500 us update rates with 50+ drives. This means machine builders can standardize on EtherCAT and support easy and difficult applications out of the box.
SCOTT CUNNINGHAM / product and application manager, controls and automation / KEB America
Product speed, torque and communication requirements
In addressing this question, first we must define the application and plant standards for communication. We must investigate the packaged control to make sure we meet the needs of the application and plant system. As always, there are many product choices that work as a system to perform the requirements of the application, as well as to satisfy the communication needs of the drive, control and plant requirements (Figure 3).
Figure 3: There are many product choices that work as a system to perform the requirements of the application, as well as to satisfy the communication needs of the drive, control and plant requirements. (Source: Motion Industries)
The application defines the product speed, torque and communication requirements, and the components are chosen to operate together to satisfy those requirements. Normally, you will be defining the precision requirements of speed or torque control – not necessarily in combination. Many VFDs can add modules and provide exceptional speed and torque response (open/closed-loop), along with communication protocols of choice. As expected, this is not a quick rule-of-thumb answer because every application defines the needs.
Coming to the best solution will involve answering questions relative to load, acceleration, deceleration, position and dynamic movements, environment, cabling and control options. There are additional limitations that must be addressed relative to speed/torque demands on the VFD and motor, thermally and mechanically, along with other criteria that envelope a “Packaged Drive System.” With today’s sophisticated drives and fast processors, we can achieve very good performance open loop with standard Voltage Vector AC Drives. For very tight speed/torque regulation, we would consider a Flux Vector Current Control Drives with Feedback (Either resolver or encoder). For very dynamic moves or high accuracy position, we would look toward servo performance drives and controllers. The VFD package is still only a small part, as the power transmission, machine dynamics and specifications will also play an important role.
Typical performance specifications of various drive manufacturers:
*These are typical performance results for many manufacturers’ motor control techniques.
Fieldbus: This subject can get lengthy, as it is very specific to application, plant standards and product availability. Normally an experienced plant engineer will determine the required communication platform to be used. CANopen for many years worked well and is still in the industry. Ethernet/IP has been becoming the plant standardization for many years and works very well in demanding motion control applications, especially well-suited for VFD applications. EtherCAT’s ability to handle bandwidth and information transfer has made it a leader in the servo motion control arena.
Communication with the plant engineer and manufacturer(s), as well as early involvement in the design, will ensure the proper needs are addressed and the correct package solution will perform to expectations.
JACK KORZYP, business development manager / Motion Industries
Tight speed or torque control
There is a wide range of applications out there: from basic “shaft spinners” to complex multi-axis automation applications with varying degrees of requirements to the control system.
A first step is to understand different fundamental VFD control methods commonly used. Each provides varying degrees of speed and torque control. A few are listed below for reference.
V/F
- speed regulation: +/- 2.3% of max frequency
- speed control range: 1:40
Open-loop Vector (Sensorless Vector)
- speed regulation: +/- 0.3% of max frequency
- speed control range: 1:200
Closed-loop Vector (Flux Control)
- speed regulation: +/- 0.01% of max frequency
- speed control range: 1:2000 … 1:5000
Generally, applications require either tight speed control or tight torque control with some form of speed limitation. Open-loop control offers a good overall value and is capable of providing reasonable speed control without external feedback. However, using external feedback greatly increases the speed and torque capability. On the downside, it increases the price and adds additional points of failure to a system.
Here are some basic criteria that should guide the selection process: The controls concept determines the selection of a VFD: from controlling via discrete I/Os all the way to fieldbus operation of the drives. VFD types can range from centralized single or multi-axis control cabinet mounted drives, to motor-mounted or even remote-mounted VFDs – all with different “standard features.”
Safety demands of the application are another aspect: from Safe-Torque-Off (STO) all the way to fully drive-integrated safety functions such as safe limited speed (SLS), safe limited position (SLP), safe brake control (SBC) and many others. Depending on the control method, open-loop VFDs do not need integrated encoder feedback, but many multi-axis VFDs offer integrated encoder feedback to allow closed-loop operation as a standard. Also, the number of I/Os that can be directly tied into the VFD is another differentiator in the market and might be relevant when selecting the VFD.
The choice of a fieldbus protocol depends on a variety of factors: the application’s requirements, the machine and factory periphery/environment, preferences of the machine builder as well as the end user.
Analog speed and torque control remain an industry standard as it offers a familiar, proven and cost effective solution.
The best choice depends on the application dynamic requirements and if the system requires deterministic control. Most modern fieldbus solutions are capable of providing speed and torque information at a rate suitable for common applications.
Higher dynamic systems may benefit from the use of Ethernet or EtherCAT based systems, which are standard in industrial control solutions, provide very high throughput, and are supported by the majority of machine control systems. When collecting data from the drives for predictive maintenance and IoT functionalities, Ethernet or EtherCAT based fieldbuses are a good choice for transmitting this data via fieldbus.
By shifting control logic from the upper-level PLC into a motion controller or directly into the VFD, the choice of the main fieldbus becomes less critical. The use of pre-programmed and parametrizable software modules facilitate fieldbus-independent motion control. This for example allows for the creation of motion control systems running on EtherCAT that can be easily tied into any upper-level PLC or fieldbus that is Profibus-based.
ARNE VALENTIN / technology manager machine automation / SEW-Eurodrive
Closed-loop control with encoder feedback
VFDs should provide closed-loop control with encoder feedback, if the precise control of the speed and torque is required in the application. This feature is commonly available in most of the VFDs available on the market today. Users can select the VFD that is ideally suited to their application requirements.
There aren’t any regulatory or minimum requirements for VFD speed and torque control. However, users are encouraged to select the VFD that has an Efficiency Class of at least IE2 according to IEC 61800-9-2 (EN 50598-2), and is UL 61800-5-1 listed for UL applications.
The fieldbus protocol for motor control using a VFD include ProfiNet, EtherNet/IP, EtherCAT, Modbus TCP/IP, Modbus RTU, BACnet IP, BACnet MSTP, USS, PROFIBUS, etc. There isn’t a single protocol that can be claimed as the best since the selection of fieldbus type for VFDs is generally specified by the customer and/or application requirements, and the type of industry. ProfiNet, EtherNet/IP and Profibus are examples of the most popular fieldbus protocols globally.
NIKUNJ SHAH / product manager, Digital Industries — motion control business / Siemens Industry
ALSO READ: Variable-frequency drives and electromagnetic interference
The importance of encoder feedback
When it comes to selecting a variable frequency drive for an application that needs tight speed and torque control, you want to look at a VFD that is capable of the following:
- Encoder feedback. When it comes to knowing what the speed of the motor is, there is no substitute to having an encoder mounted directly on the motor and providing true speed feedback. Whatever the type of encoder you have on mounted on your motor, differential is most common, make sure the VFD that you select has an option that can accept the encoder signals.
- Closed-loop vector motor control. Vector motor control is a tried and true motor control algorithm that can accurately regulate the flux and torque in the motor. Being able to provide an accurate speed of the motor, hence the importance of having encoder feedback, to the algorithm will help make the regulation of torque in the motor more precise.
VFDs have come a long way since they were first introduced, which has led to their speed response and torque accuracy improving dramatically over that time. Even with those improvements, you may want to still be cognizant of a VFDs speed response and torque accuracy, e.g. 50 Hz speed response and +/- 5% torque accuracy. What you’ll find is that a lot of VFD manufacturers will have response and accuracies that are very close to each other.
When it comes to choosing a fieldbus for the application, there’s no clear cut answer. However, if you plan on building your control system around the network that you choose, then pick one that is Ethernet based. Good ones to start with are EtherNet/IP, ProfiNet, and EtherCAT. Each of these protocols are considered real-time and capable of high-speed messaging.
An alternate way of choosing which protocol to use for your system is to see what your controller of choice supports. The implementation of the VFD will go more smoothly for you if you’re working in an environment that’s familiar to you. If the controller supports multiple fieldbus networks, narrow it down to the Ethernet based protocols and go from there.
Another thing that you may want to consider is what else you want to achieve with a VFD that’s networked. If you and your company have plans to monitor and record various data points from your VFD and use it on a larger scale, predictive maintenance for example, then choose a VFD that provides access to a large assortment of monitors that it has available. This will give you the flexibility to set up your system how you want to at that moment and also provide you the flexibility to expand if the need arises.
EDWARD TOM / product manager, drives / Yaskawa America
High speed and torque performance
Any application that requires high speed and torque performance should use a VFD with Flux Vector motor control that is derived from Field Oriented Control (FOC). This means the torque producing component of the stator flux can be controlled independently. Couple that precise control with some type of motor feedback, such as an encoder, and high bandwidth control of the motor can be achieved. There are many technical papers written about this method of motor control.
For fieldbus protocol, industry communications have been migrating to EtherNet/IP in recent years. EtherNet/IP is an open fieldbus standard managed by ODVA that provides reliable, high speed communications. Most drive manufacturers have several communication options available that can be used with the VFD.
JEFF THEISEN, STEVE WIRTZ and MIKE HARRIS / commercial project engineer, commercial project engineer and senior project commercial engineer / Rockwell Automation
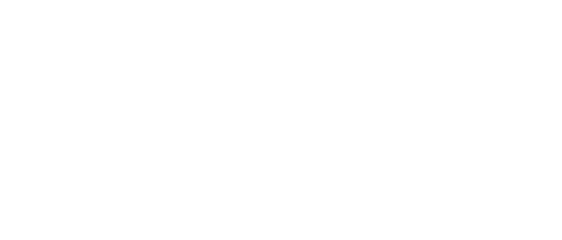
Leaders relevant to this article: